Wire Terminal WT fully automated wire assembly machine
(para español)
If you are a frequent reader of WHN, you notice that we do a fair number of articles that deal with enclosures. Through surveying, we have discovered about 70% of our readers do some type of box, panel, or switchgear build. Rittal has been an excellent source of information for us, so when they recently informed us of the release of their new WT (Wire Terminal) automated wire processing machine, we jumped at the chance to get on the phone with Mike Herzog, Manager, Rittal Automation Systems & Technical Service.
Mike described the path to automation development at Rittal. “In 1961 we started building standardized enclosures to get our customers away from building everything from scratch, and we have been quite successful doing that ever since,” he began. Rittal owns EPLAN, one of the world’s leading design software packages for machine, plant and panel builders. The company’s owner had the vision of using this as a springboard to automate the panel component building process. “We had EPLAN on the front end, so you could do all the control panel layouts, motor starters, terminal blocks, din rails and everything you need,” he described. So, they had the enclosures and the detailed build instructions. What was missing was a way to automate the panel build. And that’s where the company’s path to automation began.
Their first step was the Perforex MT series which is basically an automated milling, drilling and tapping machine to modify enclosures.
Considering the time required to build a control panel, the fabrication of the point-to-point wiring is the most time-consuming effort. The WT machine was the next logical solution in their automation efforts. With it, assemblies can all be produced in a fully automated process without manual intervention. It pulls wire from a box, cuts it to length, prints a label onto the wire, crimps a ferrule, and deposits the completed assembly into a magazine. “So that’s it in a nutshell,” Mike said. “It’s a simple process, but there’s a lot of engineering behind it. Throw away the hand strippers and crimpers, and take those folks who were doing all that stuff manually and put them in value added areas where you are not yet able to automate.”
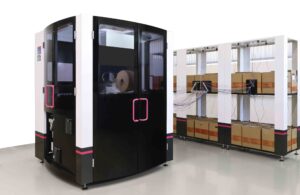
It makes sense that the equipment integrates flawlessly through EPLAN since it exists under their corporate umbrella, but Mike insisted there is a fairly straightforward integration process with other engineering software. “There is a specific template that the machine would like to see because it needs all of its dimensional data in order to create a completed assembly. But those things can be formatted and uploaded back into the WT machine through a spreadsheet.”
“The advantage of EPLAN is that you’re programming from start to finish in one language and one program,” Mike explained. “But the key for this machine to work is the data, and with that I now know three dimensionally what the wire looks like.” He pointed out that with a simple schematic, an assembler has no specific data information on wire lengths, stripping parameters, ferrule selection, or any of the other data pertinent for the build. Without automation, the panel builder must manually measure the length of wire directly on the control panel and then cut the wire to length. By processing the wire with WT machine, the exact length is ensured, and it will reduce the amount of wire that goes into the trash.
The WT machine accommodates up to 36 different wire sizes with cross-sections ranging from 0.5 mm² to 6 mm². The minimum assembly length is 230 mm (about 9 inches) and it can go up to 10,000 mm (almost 33 feet). Ferrules can be fed from a reel or by an available gravity fed hopper.
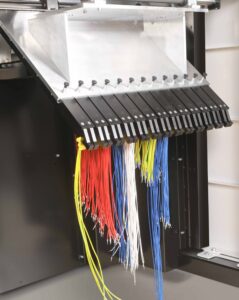
Because of their background in the panel build and switchgear production market, the equipment is limited to crimping ferrules at this time. As ferrules become more popular across industries, however, market applications for the WT machine are expected to expand. “The machine doesn’t care where the wire is going,” Mike joked.
Mike wanted to stress that a key to the machine to work is that it uses box wire. “That’s important because when you buy box wire, the wire is laid in the box, not wound around a reel. Once you wind it around a reel you create memory in that wire, and you get a pigtail. The box wire doesn’t have those properties,” he explained. Box wire is much more popular in Germany than other parts of the world, so Mike let us know that they are working with distributors in the United States that now provide box wire for their customers.
Although the WT machine represents the pinnacle of automation design for wire processing at Rittal, Mike wanted to mention another product they also have available for companies who may not be able to justify the capital investment. It’s the Wiring Work Station WS 540, and you can see a full description in the News Plugs section of this issue. “It’s basically set up as a mobile desk/workspace that you can pull wire from. We can fit it with wire cutting and ferrule crimping machines. So, we can take the same data out of EPLAN, feed the wire, cut it to the whatever length, print a label and then put a ferrule on it.” Mike reiterated that it’s a good step towards automation for people who aren’t ready for the bigger machine.
As if that weren’t enough, Mike also mentioned a second EPLAN software package called Smart Wiring that can be used with a PC or mobile device. It takes an assembler point to point in the wiring instructions without the need for a schematic. It’s a visual modeling system that prompts the user to select the correct part number, shows where it starts, the exact path it follows, and where it lands. He noted quite a bit of interest for these products at the recent IMTS show and is looking forward to exhibiting them at the Rockwell Automation Fair this November 16 – 17 in Chicago, IL.
Special thanks to Jill Jozwik, Senior Marketing Manager at Rittal for putting us in touch with Mike. Jill is always quick to supply valuable subject matter material for Wiring Harness News.