By: Sanu Warrier – Zuken
Wire Harness Manufacturing Automation
The move towards electrification across the machinery and transportation sector is increasing the demand for wire harnesses. Simultaneously, the booming industry is battling the overall labor market shortages. The wire harness production process has been predominantly labor-intensive. The most commonly sighted reason is the lack of viable wire harness manufacturing automation options. That may have been true a decade ago, but not today. Several options are available today for automating the wire harness manufacturing process.
Even so, without the right tools, wire harness design teams struggle to gather the information required to adopt an automated manufacturing process. A detailed, intelligent design and layout accelerates the documentation process and sets the stage to drive automated assembly and production machines.
Let’s look at the leading automation options with significant advantages over traditional manual processes.
Automated Wire Processing Machines
The process of cutting, stripping, and preparing wires for the harness is often labor-intensive and time-consuming. The next step of completing the wire terminations is error-prone as well. Furthermore, any errors in picking and finishing the wire terminations will significantly impact the project. Indeed, automated wire processing machines have the potential to save more than 50% of labor costs and deliver additional time savings.
Automated wire processing machines eliminate a large portion of the wiring challenges. The latest machines cut, strip, and mark the wires and have options for adding the wire terminations. For instance, machines like the Komax Zeta have advanced bundling capabilities to group processed wires to supercharge the assembly process. Using the right design tools can help generate the required data in a suitable format to drive machines from major vendors like Schleuniger, Argus, and Komax.
Automated Wire Harness Testing
Testing a wire harness to ensure connectivity and continuity is vital for quality control. The automated wire harness testing machines provide various test options like connectivity, impedance, signal integrity, and more. However, setting up test routines or manually conducting tests has overheads that design teams tend to avoid. Automated wire testing machines deliver significant time savings, but more importantly, have the potential to cut the error rate by half.
Leading automated testing machine OEMs like DeltaSigma, Cirris, DIT-MCO, Dynalabs, CamiResearch, Nexeya, CKT technologies, and others can drive testing from intelligent connectivity data. Using purpose-built wire harness design tools like Harness Builder for E3.series, designers can automatically capture and produce data required to set up the test routines.
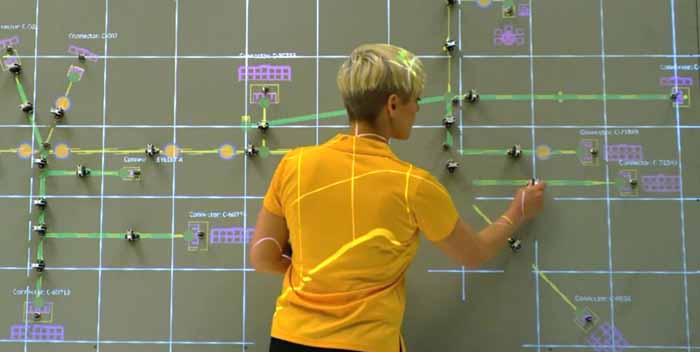
The harness assembly process on physical formboards or nailboards demands a great deal of set-up, maintenance, and storage overhead. The next step in the evolutionary process is to reimagine wire harness assembly fundamentals. Augmented or mixed reality has significant benefits over the traditional visualization process with 70% potential time savings. Augmented reality solutions are perfect for resolving complex assembly challenges across many domains. A game-changer is the on-demand digital delivery of dynamic and accurate assembly and manufacturing data.
Augmented reality systems like ProjectionWorks from DeltaSigma are leading the way in transforming wire harness assembly from a paper-based formboard into a digital formboard process. Digital formboard solutions reduce wire harness manufacturing overheads by:
- Reducing set-up time and improving the reuse of formboards
- Removing the need to store every legacy formboard
- Lowering the impact of experience and knowledge gap between new and seasoned employees
- Simplifying the training and ramp process to bring on new employees
- Producing step-by-step instructions directly from design tools like E3.series
Automated Wire Harness Assembly
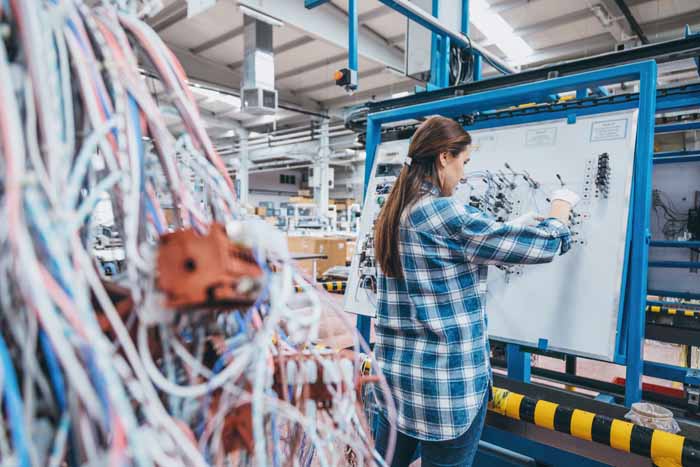
Imagine providing the interconnect details of a harness to a machine on the shop floor and receiving a complete wire harness. Although not possible yet, technological advancements bring automation options previously available in mechanical manufacturing practices to the wire harness industry. Unsurprisingly, parts of the wire harness assembly process will be manual for the foreseeable future. As a result, the possibilities for automatically assembling harnesses have been very limited in the past. Furthermore, the variations in connector sizing, wire application, and terminations also significantly impact the automation process.
Thankfully, many manufacturers are taking up the task of overcoming the challenges. Notably, the latest automated assembly machines deliver complete wire harnesses with connectors and wire terminations. For instance, the Komax Zeta series delivers wires plugged into connectors to automate a significant part of the wire harness assembly process. Automated assembly options are ready to reduce labor costs and improve quality and consistency.
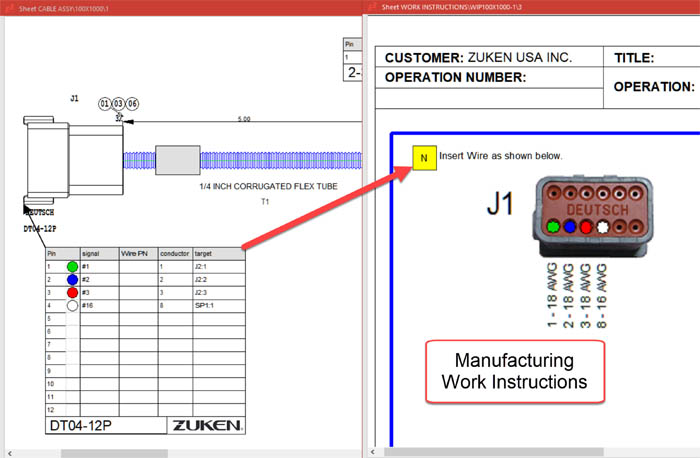
Automating Manufacturing Work Instructions
Although not a production option, clear work instructions lead to higher productivity in the manufacturing process. Design teams are often left picking between two bad options. They are either manually creating work instructions or skipping them and leaving it up to manufacturing. The first option increases the design cycle and cost. The second option is worse, skipping manufacturing instructions to save time upfront only to spend time fixing issues and going back and forth between engineering and manufacturing. Either way, the dreaded engineering change order rears its head, and the overhead around managing the ECOs adds to the pain.
Intelligent tools like Harness Builder for E3.series help design teams simplify and expedite the manufacturing work instruction creation. The balanced mix of automated and semi-automated templates caters to different requirements across projects.
Automate Printing and Labeling
Label printing for projects is an umbrella term covering markings for components, locations, wires, and other visible data. The partial automation of label printing has been around for many years with popular printers from suppliers like Brady, Brother, Hewlett Packard, and many more. The design tool has a significant influence on the printing process.
The labels play an essential role in increasing productivity and improving the overall quality of production and services. Assembly and service teams need clear indicators for components, locations, wire identifiers, and critical equipment data. Using solutions like E3.series, design teams can automate multiple printing requirements. The data captured during the design process is readily available in multiple formats to drive the labeling machines.
Conclusion
Automated manufacturing, testing, and assembly options have a huge potential to positively impact every aspect of the design to manufacturing journey. Considering labor shortages and price pressures, companies willing to act early stand to gain a significant advantage. However, the most critical step in the manufacturing automation journey is to produce accurate data capable of driving the automation. Above all, an intelligent design tool is a prerequisite for adopting efficient automated processes. The E3.series design suite offers unmatched capabilities to augment the assembly and manufacturing process quickly while reducing errors and design overheads.
Many thanks to Sanu and his team at Zuken for compiling this article. You can check out more automation solutions on Zukin website, or visit them at the E W P T Expo at booth 618.