The automotive and commercial vehicle industries are renowned for their intricate processes, extensive supply chains, and complex manufacturing operations. However, this complexity often leads to inefficiencies, increased expenses, and diminished customer satisfaction. Recognizing these challenges, automotive and commercial vehicle companies are now embracing simplification to bolster their competitiveness and foster sustainable growth.
Wire harnesses are crucial components in connecting electrical systems within vehicles, ensuring the reliable operation of various elements such as lights, sensors, and control modules. However, the complexity associated with designing, manufacturing, and installing wire harnesses presents significant challenges for automotive manufacturers. Siemens, a supplier of advanced wire harness manufacturing engineering solutions, estimates that a typical wire harness comprises approximately 10,000 individual part numbers. 2Complexity reduction initiatives aim to streamline these processes, resulting in cost savings, improved efficiency, and higher-quality products.
tesa offers an assortment of solutions to reduce the complexity of the coverings, improve the manufacturing process time, and reduce weight and outside diameter. These solutions can reduce the number of covering types used on the harness by more than half. Our experts will collaborate with you to find the best solution for achieving the optimal outcome.
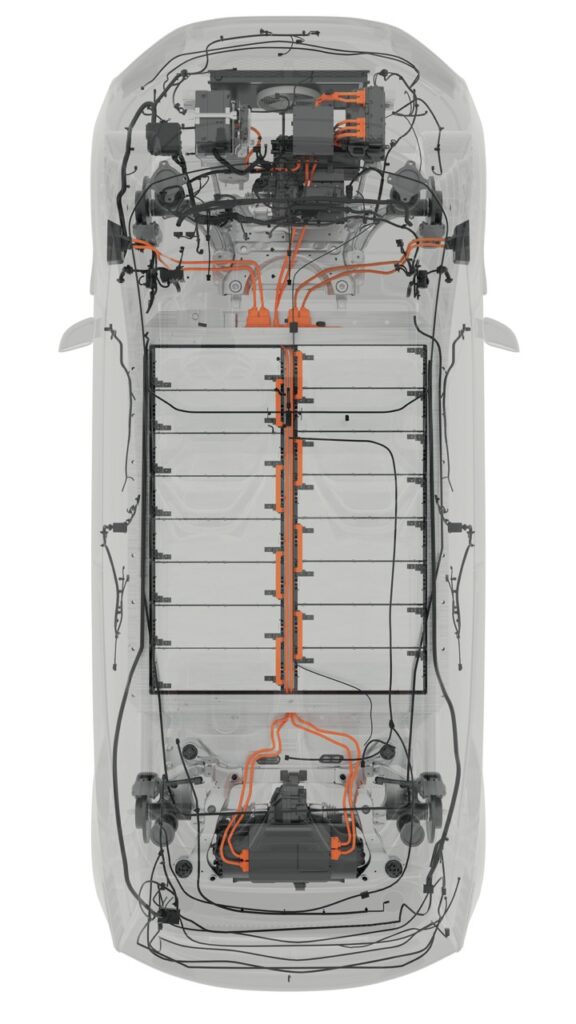
The Benefits of Complexity Reduction
Complexity Reduction Strategy
According to strategy management advisor Oliver Wyman1, reducing complexity within the automotive and commercial vehicle sectors can yield substantial cost savings throughout the value chain. By streamlining suppliers, companies can potentially save between 10 to 18% in personnel and material costs over five years. Additionally, optimizing production processes, including setup costs, planning, assembly time consistency, and quality control, can result n savings ranging from 10 to 30% over the same time frame. Furthermore, a reduction of 5 to 8% in logistics costs is feasible over five years.
This complexity reduction strategy also benefits tier manu- facturers within the automotive and commercial vehicle sup- ply chain. By simplifying processes, these manufacturers can enjoy a range of ad-vantages beyond immediate cost savings, including increased resilience, competitiveness, and innovation within the industry.
Cost Savings
Complexity reduction in wire harness manufacturing leads to significant cost savings throughout the production process. By simplifying designs, standardizing components, and
optimizing assembly processes, manufacturers can reduce material waste, labor expenses, and overhead costs. Studies suggest that complexity reduction initiatives can result in cost savings ranging from 10 to 30%, contributing to improved profitability and competitiveness.
Improved Efficiency
Simplifying wire harness designs and assembly processes enhances production efficiency, resulting in shorter lead times and increased throughput. By minimizing the number of components, reducing assembly steps, and leveraging automation technologies, manufacturers can achieve higher productivity levels and lower production costs. Improved efficiency also enables manufacturers to better meet customer demand and delivery schedules, enhancing overall operational performance.
Enhanced Quality and Reliability
Complexity in wire harnesses increases the risk of defects, wiring errors, and reliability issues, which can lead to costly rework, warranty claims, and customer dissatisfaction. Complexity reduction initiatives focus on standardizing designs, implementing robust quality control measures, and ensuring consistency in manufacturing processes. By simplifying designs and minimizing variations, manufacturers can improve product quality, reliability, and durability, thereby enhancing customer satisfaction and brand reputa- tion. Several components of automotive and commercial vehicle wire harnesses have undergone complexity reduction efforts to streamline manufacturing processes, improve efficiency, and reduce costs.
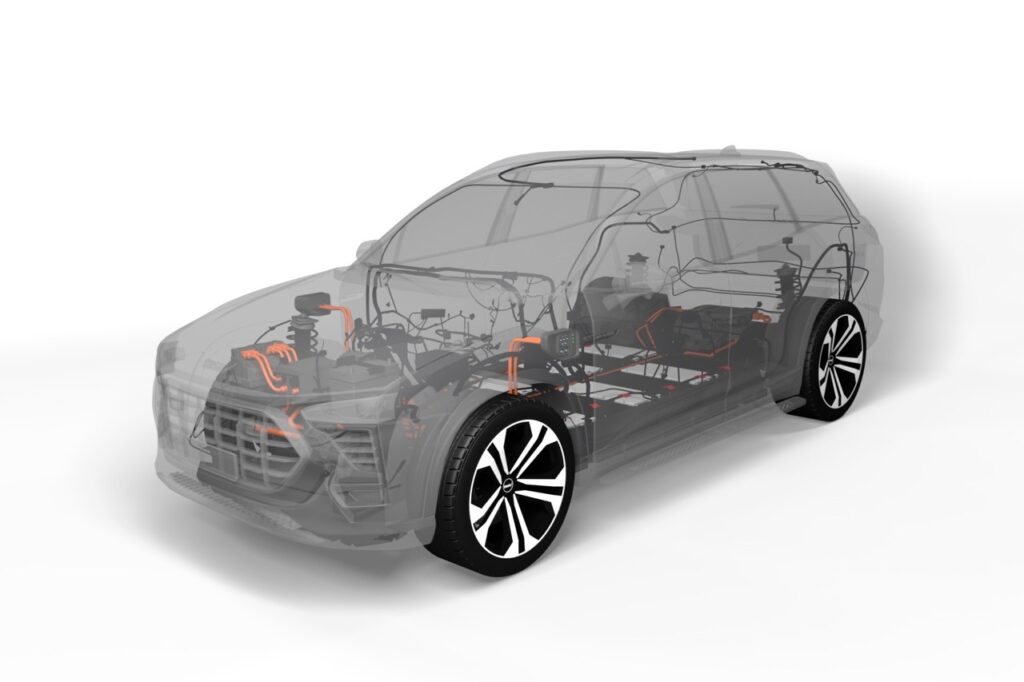
The Role of Ultrasonic Wire Splicing
& Protective Coverings
Connectors and Terminals
Splices
In the realm of electromobility, ultrasonic wire splicing stands out as a vital technology for the automotive industry. Its continuous development has made it the preferred method for joining wires due to its reliability and versatility. Ultrason- ic welding is renowned for its ability to create robust connec- tions, particularly in splicing and terminating wires to connectors. This technology offers various benefits, including low electrical resistance, cost-effectiveness, and excellent corrosion protection, essential for the longevity of vehicles subjected to harsh environmental conditions.
Protective Covering and Sleeving
The material and design of protective covering and sleeving can significantly impact complexity. Consequently, several factors determine the most effective and least complex solution to prevent damage to the harness. When designing coverings for a harness, OEMs typically stick to a standard set of criteria to define the performance need of the covering being applied. These criteria include temperature (ambient operating class temperature), abrasion (protection against vibration and dynamic movement against rough surfaces), sound damping (noise generated from harness rattling after installation), flexibility (the ease of the harness installation process based on design layout), and color (indicating special functions or safety features). Reviews are run for each performance aspect corresponding to the respective OEM specification.
Once the testing is complete, each criteria is assigned a rating corresponding to a performance classification table developed for each of the five aforementioned areas.
OEMs then combine these alphanumeric ratings for each criteria to generate a code that becomes the overall performance requirement for a covering used in a specific application area. This performance code is then cataloged in an engineering selection guide that design engineers can reference when choosing coverings for their harnesses. Approved products that match the desired application performance codes are deemed usable for these same application areas and will be available for selection in the database.
Traditional products for covering vehicle wire harnesses include a variety of materials and designs, each offering specific protective qualities suited to the automotive environment. Here are some of the most used traditional coverings:
• PVC (Polyvinyl Chloride) Sleeves • Braided/woven Sleeving
• Vinyl Tapes
• Split Loom Tubing
• Convoluted Tubing
• Heat Shrink Tubing
• Rubber Grommets and Bushings
• Adhesive Laminated PE or PUR Foams • Non-Woven Tapes
• Fabric Tapes
Conventional wire harness coverings use these products in combination with two or more products to provide different characteristics to the wire harness, such as abrasion resistance, noise reduction, temperature resistance, and flexibility.
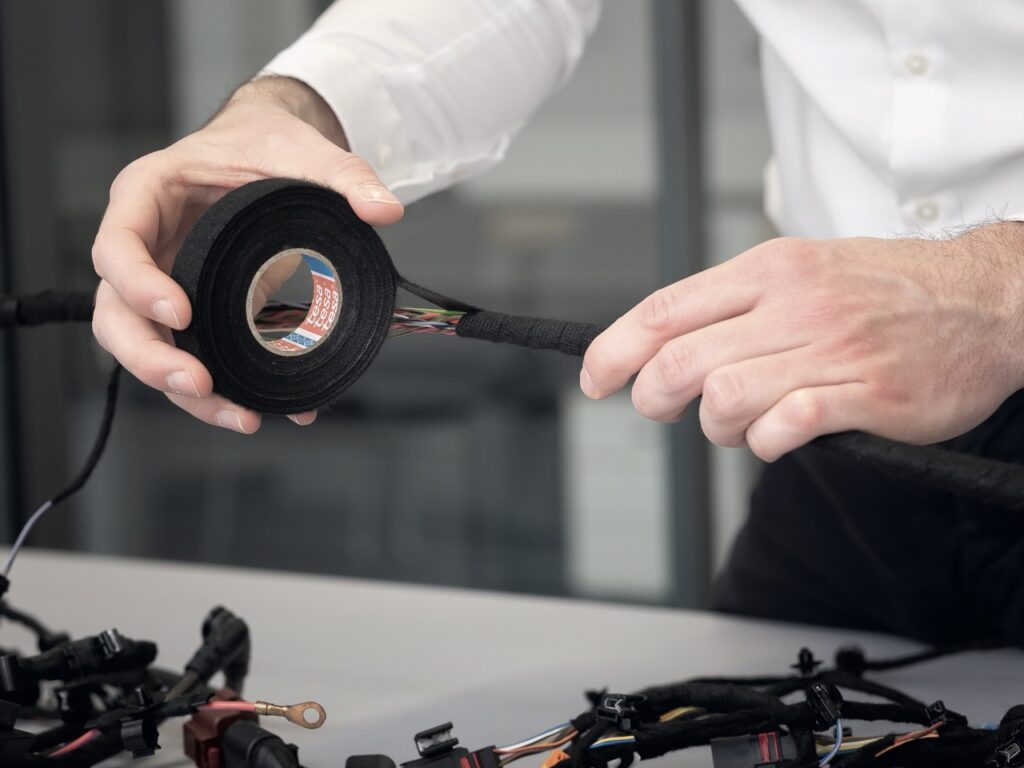
tesa® Sleeve 51036PV76: high abrasion resistance and high noise damping due to layers of both PET cloth and fleece.
tesa® Sleeve 51036PV78: Flexible covering solution with high abrasion resistance and medium noise damping due to layers of both PET cloth and fleece.
tesa® Sleeve 51036PV9: Flexible basic abrasion protection and bundling due to one layer of PET cloth.
tesa® Sleeve 51608PV6: Flexible high noise damping solution due to double layer of fleece PET fibers.
tesa® 51036 PET cloth tape: High abrasion and temperature resistance.
tesa® 51638 Thin non-woven fleece tape: Basic noise and abrasion tape.
tesa® 51616 Thick non-woven fleece tape: High noise and abrasion resistance tape.
And many more!
Reach out to tesa’s adhesive experts so we can help you identify the right solution for your unique needs. We will work to help you reduce your complexity and improve the covering performance.