Flat cable has been around for a long time, but its use has increased in recent years. The increased need to reduce space and weight and the boon in automation and robotics has led to an increased need for conductors that flex and move. The electrification of almost everything with wheels (or even propellers) has created new applications for flat cable. Some of these varieties are available across multiple manufacturers, but for the purpose of this discussion, we will be dealing with the 3M product line.
The concept of flat cables has evolved with market needs over time. 3M has played a significant role in developing and popularizing flat cable technology. WHN spoke with Gregg Couture, Senior Account Executive at 3M’s Electronics Materials Solutions Division to bring us up to speed on flat cable offerings and applications.
Gregg began with some basics saying flat cable was developed using Insulation Displacement Connection (IDC) as a cost-effective way to terminate a number of connectors at once. “It was revolutionary technology in that you didn’t have to crimp a separate contact to many different conductors. You could do it in one stamping action and that was a real game changer,” he detailed.
He talked about the termination process in detail. “For standard unshielded/unjacketed flat ribbon, there isn’t much prep involved other than just cutting it to the correct length. There’s no need to strip insulation or perform any wire prep, that’s part of the appeal of using ribbon cables. There’s very little labor involved in terminating to the IDC connectors.”
He described the process in detail, noting that the connector has two parts, the strain relief and the connector itself. The connector has a row of teeth which, when compressed, shear through the insulation of the ribbon cable, and make contact with the wire cores (fig. 1).
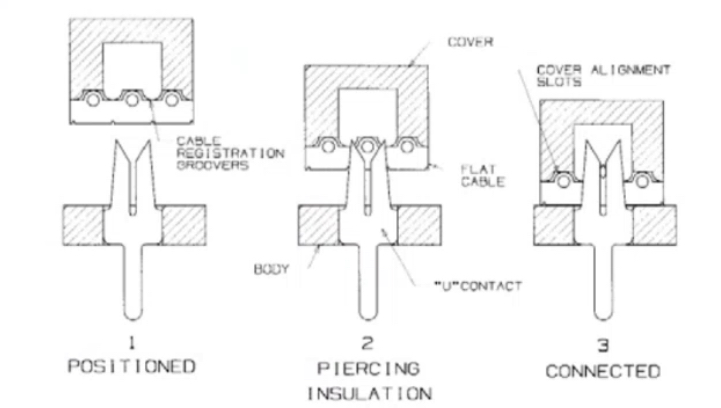
Figure 1. IDC in detail. (photo courtesy of 3M)
The connector is then folded back on itself and the strain relief is attached to the wire onto the connector, facing the opposite way to the final orientation. “The process can be done with some fixturing and a simple press. You can use an arbor press or something like that. We actually make a press, but you don’t have to use ours.” There are also automated options available from other manufacturers (see New Semi Auto Machine For FFC/FPC Processing in the Sept/Oct issue of WHN).
Because of its low profile, flat cable is a great selection in enclosures or other areas where weight and airflow are important. “You don’t have a big nest of round jacket cables obstructing the airflow. Fans run more efficiently, components stay cooler with lower energy costs and with a significant weight and space savings,” he advised.
As far as offerings, Gregg began with the basic grey PVC flat cable we have all seen, but noted it is also available with TPE, FEP, LSHF and Halogen Free insulation (fig. 2 left). “From there you move into flat flexible cable or ribbon cable, popular in places where you have a moving assembly.” Standard flat cable offerings are rated for one million flex cycles while flat flexible cables work best where you have a moving assembly and are rated for up to ten million flex cycles (fig. 2 right).
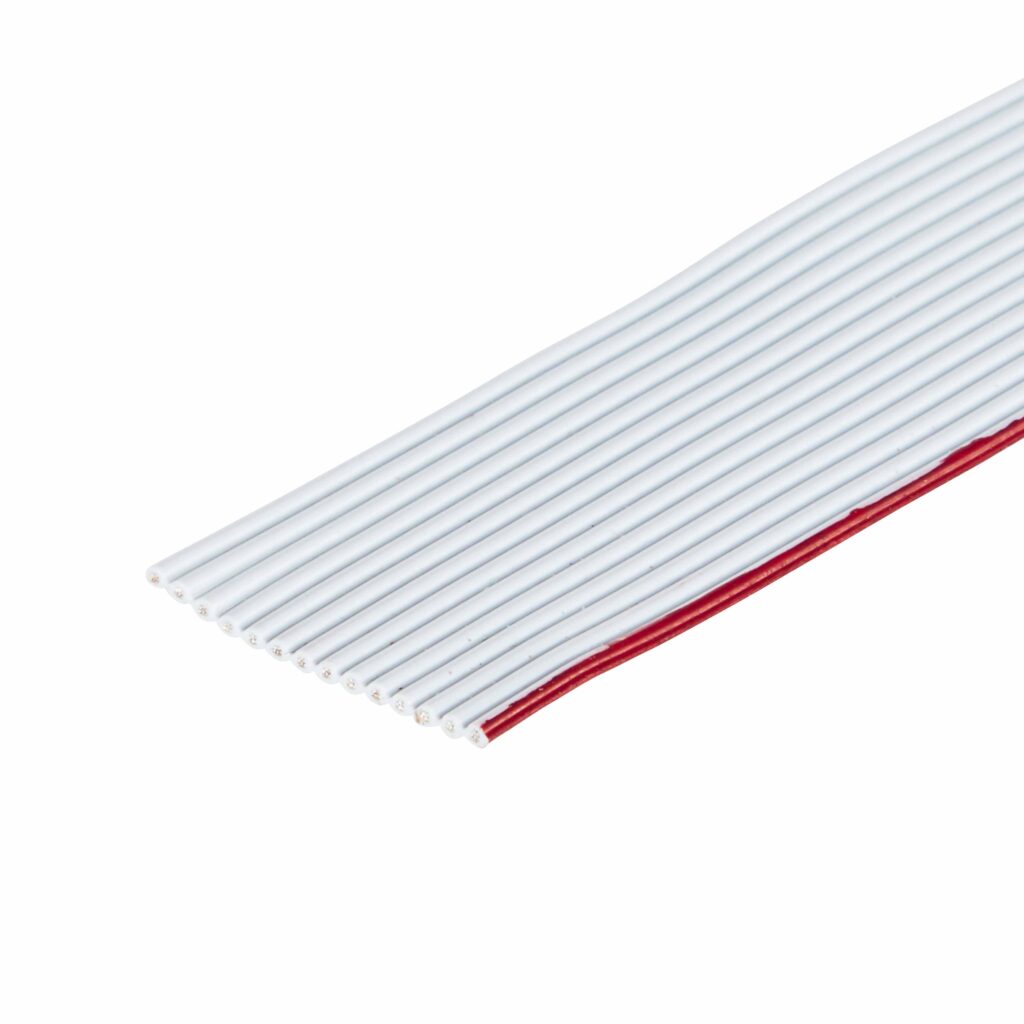
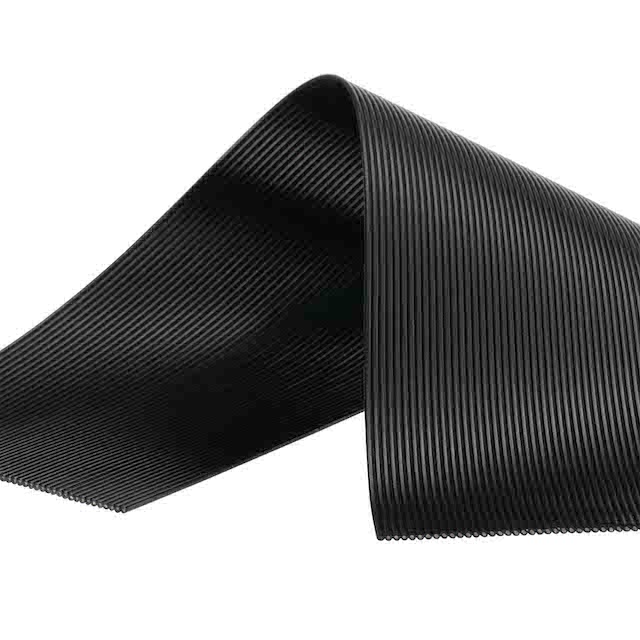
Figure 2. Standard PVC Flat Cable (left) and Flat Flexible Cable. (photo courtesy of 3M)
Another standard offering in the marketplace Gregg noted is color coded flat cable (fig. 3 left). It is often specified where the customer requires color coding for second-end terminations. All of the options mentioned thus far are available in a zippable configuration for branching or discrete termination.
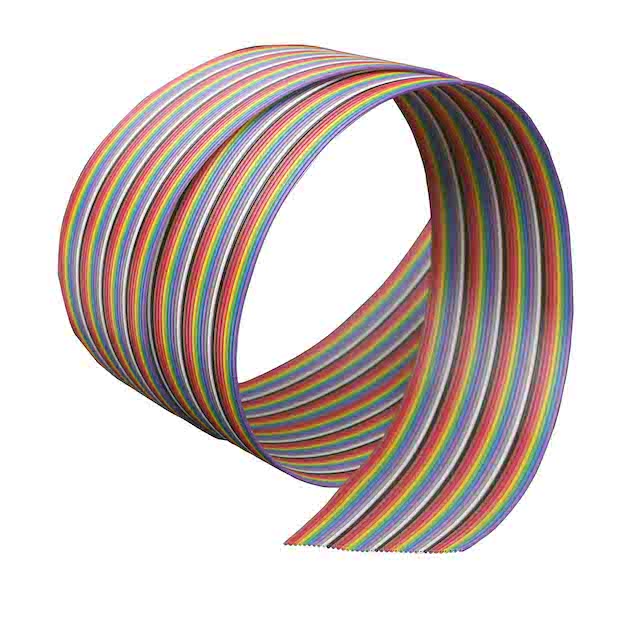
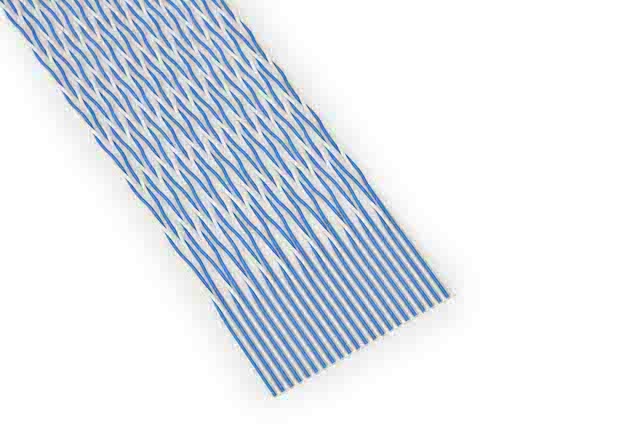
Figure 3. Color Coded Flat Cable (left) and Twisted Pair. (photo courtesy of 3M)
Gregg noted that for enhanced signal transmission, twisted pair flat cable is often specified (fig. 3 right). He explained that twisted pair wires offer better signal transference due to their design, which helps reduce electromagnetic interference (EMI) and crosstalk. The twisting pattern minimizes the impact of external electromagnetic fields by canceling out their effects on each wire. “It’s a more balanced application if you need to run some differential signaling.”
The subject of signal transference brought up shielding, and 3M has two main categories of offerings for many sensitive applications. “We have jacketing materials that offer protection where you may want to run something externally or for otherwise harsh environments. We also offer copper braided, pleated copper foil and expandable copper or aluminum foil for EMI protection (fig.4).
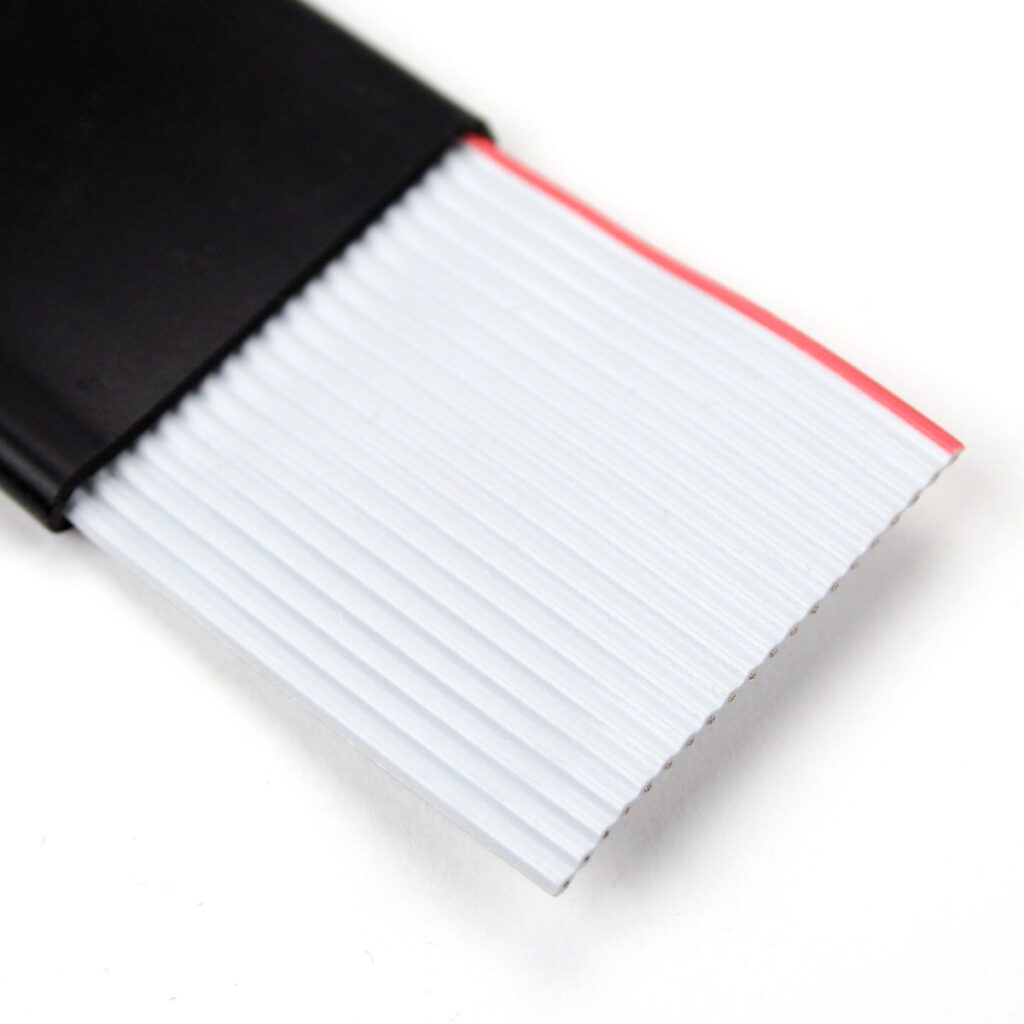
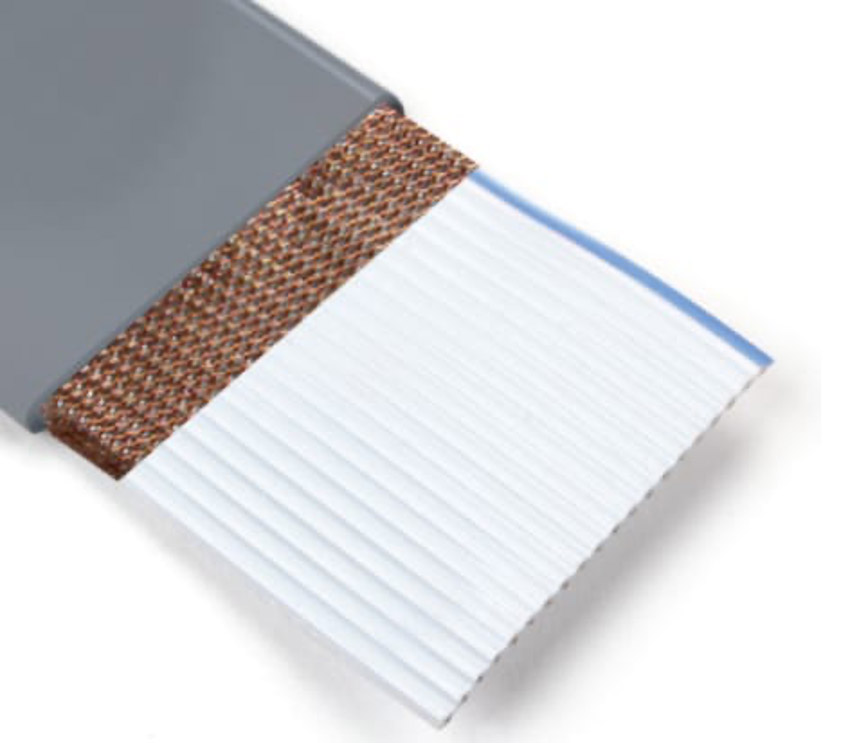
Figure 4. Jacketed Cable (left) and Shielded Cable. (photo courtesy of 3M)
Once you move into jacketed, or shielded ribbon cables, Gregg noted some preparation is required. “You’ll need to cut back some of the insulation to expose the bare ribbon cable for connector termination, and the shielding will also need to be cut and sometimes attached to the metal shell of the connector to properly ground the termination if a shielded connector system is being used. Otherwise, it can just remain hidden under the jacket if just attaching to a standard IDC connector.”
One very interesting option that takes the concept one step further is round jacketed flat cable. “Some customers want a rounded cable but still want the mass termination benefits of IDC, so we offer cables where you can actually split the conductors in certain spots and then bundle them up into a nice round construction (fig. 5),” Gregg instructed. “We have some connectors that you would use specifically in this type of environment where you can still use mass termination. It could be a D-Sub or different type of I/O connector.”
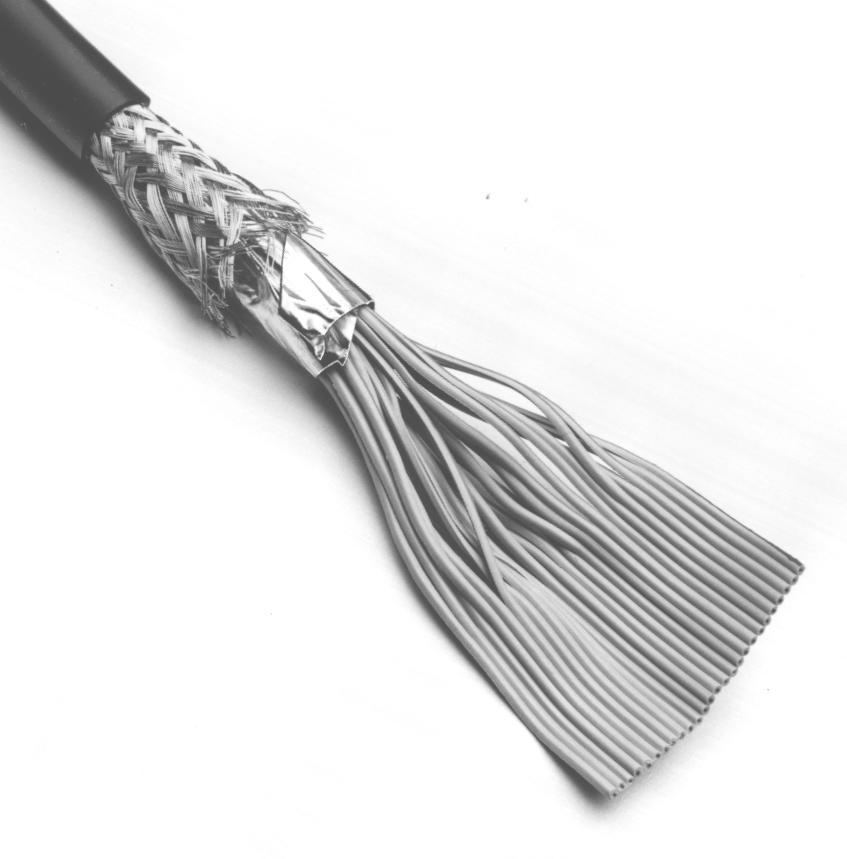
Figure 5. Rounded IDC Cables (photo courtesy of 3M)
3M also has a series called MDR (Mini Delta Ribbon), and Gregg elaborated on its virtues. “It’s a high speed, shielded connector used for higher speed, rugged environments.” He mentioned its popularity in machine vision, low-voltage differential signaling (LVDS), medical, and imaging system applications. “Most of the market uses soldering for these applications; but here you can use IDC. You can then tie the metal shield to the shielding of the cable. If you’re using a 50 position D-Sub, that would be 50 individual solder terminations versus one stamp of a press, so that’s one area where the technology helps with labor cost.” And the result, he insisted, is a secure, reliable and repeatable connection with no pin stubbing.
Moving up the scale of durability, 3M offers their Molded-On Assemblies. “These are actually intrinsic to 3M,” Gregg revealed. “We mold the cable into the connector at a factory level (fig. 6).
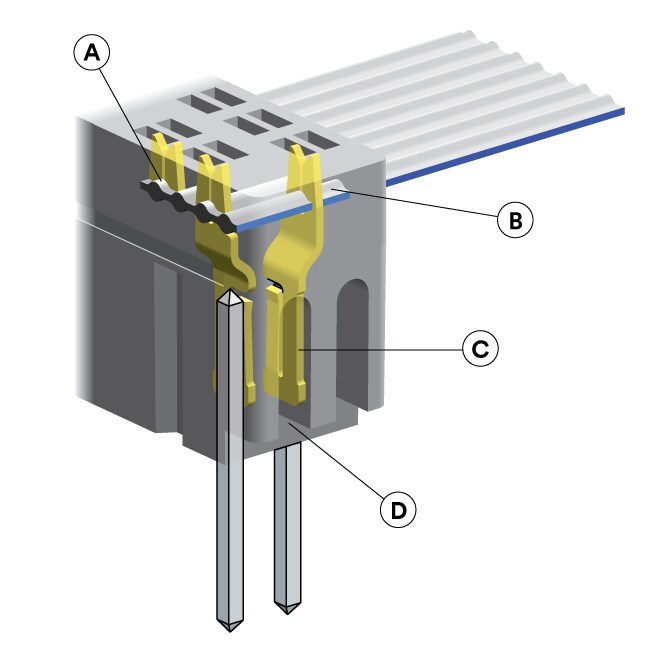
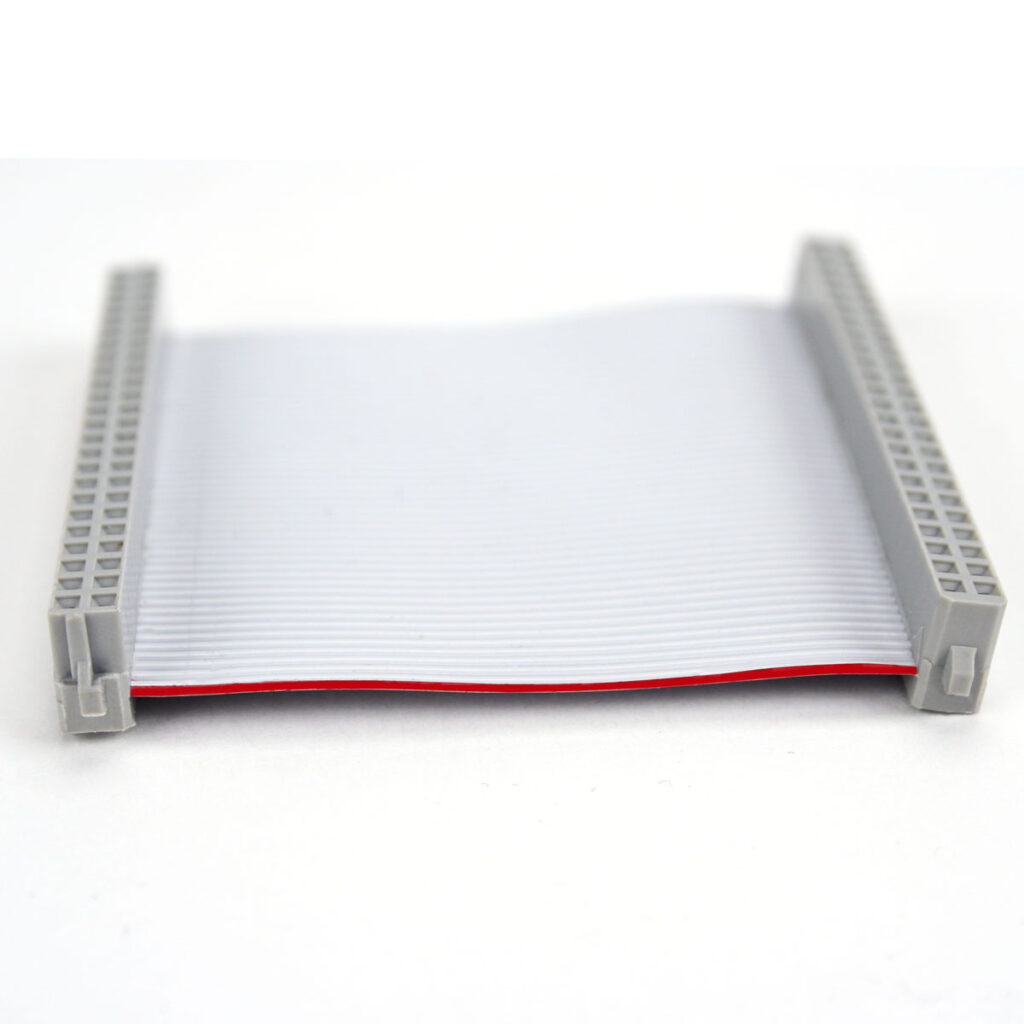
Figure 6. Molded-On Assemblies. (photo courtesy of 3M)
It encapsulates the cable inside the connector and offers the most rugged and robust ribbon assembly available today.” He cautioned that standard assemblies can be damaged in applications where the connector may need to periodically mated and unmated. “Sometimes, if you try to pull the connector off your board, especially when you have no latch eject system, you can pop the cover and ruin your assembly,” he detailed. Although these cables are not Ingress Protection rated, they offer better environmental protection and are a good choice for many of their customers in outdoor equipment markets.
Gregg rounded out the discussion with their Series 451/452 for applications where signal control is needed but space is at a premium. “We offer one of the world’s smallest ribbon cable connectors. Applications are getting smaller and smaller and this series of connectors and cables is literally half the size with a pitch of 0.050.” He explained it’s still the same type of termination as their standard product offering and has a lower profile connector design version their competitors lack. “Their connector design is larger and that defeats the whole idea of going smaller to save space.” He mentioned that a molded-on version of the miniature series should be on the market by Q2 of 2024.
Many thanks to Gregg Couture and his marketing team at 3M for taking the time to compile this article. Special thanks to the folks at TTI, specifically, Cathy Walensky, Bobbie Warner, John Sandy and Emily King, who put us in touch with Gregg. All of these products are available at TTI.com.