By Maria Schierscher, Phoenix Contact USA
Introduction
The purpose of this article is to help readers understand ferrules:
1. What is a ferrule?
2. Why are there different colors?
3. Why use ferrules?
4. How do I choose a high-quality ferrule?
5. How do I properly apply a ferrule to the end of a conductor?
6. How does UL Listing work for ferrules?
Many applications require the uses of ferrules, such as for CE certification in Europe. Control cabinet and rail assembly engineers may specify the use of ferrules in the build simply due to the high quality, durability, and security of the connections.
What is a ferrule?
A ferrule is a copper tube that is tin-plated with or without a colored polypropylene insulation. It is applied to the end of a conductor where the insulation of the wire has been stripped off. Ferrules come in many sizes, ranging from 250 MCM to 28 AWG, and in many styles: insulated, un-insulated, single, twin, loose, in strips, and reeled. Insulated refers to the colored polypropylene attached to the tin-plated barrel. Uninsulated ferrules are just the tin-plated barrel. Single ferrules are for use with one wire, and twin ferrules are for use when simultaneously combining two wires.
Ferrules are produced loose or individually, meaning just one ferrule, or in strips and reeled, where each ferrule is attached to the next via the polypropylene insulation. Strips of ferrules
are for use with specific hand tools, and reeled ferrules are generally used with semi-automatic or fully automatic devices.
Why are there different colors?
Ferrules come in many sizes and colors. The size required for the application depends on the AWG of the wire. The color used can be the user’s choice unless specified in the panel
build design; typically, however, blue is used for 14 AWG, black for 16 AWG, and red for 18 AWG. Special sized collars on insulated ferrules are available to accommodate thicker insulated wires, where the colored collar, or insulation, has a larger diameter. (Figure 1)
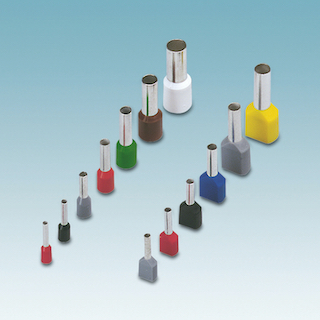
Why use ferrules?
Ferrules provide many benefits. They ensure a solid and air-tight connection versus a bare, stripped wire. When wires are stripped of their insulation, the individual strands are compromised. The strands become loose or frayed, and depending on the quality of the strip process, they can be severed. Using a ferrule strengthens stranded wire bundles,
eliminating stray strands and providing a durable and safe connection ensuring long-term electrical performance.
Ferrules also safeguard the connection from corrosion and vibration, avoiding high temperatures, short circuits, and, in some cases, arc flashes. The use of ferrules allows for easy installation and retention of the shape and integrity of the wire end when removed and reinserted into the application. In many cases, when building a control panel or a rail assembly, wires can be landed incorrectly and must be removed and reinserted into the correct location. This action can cause wear and tear on the fine strands; however, dressing the wire end in a ferrule can eliminate the damage to the fine strands.
How do I choose a high-quality ferrule?
Different ferrule manufacturers use different methods of producing ferrules, but one very important step in manufacturing a quality ferrule is called annealing. It is when the metal is heated and then allowed to slowly cool. This process alters the physical and chemical process to increase its flexibility and toughen the material. There are three stages of the annealing process: recovery, recrystallization, and grain growth. Skipping the annealing step results in a weaker ferrule that might crack when crimped onto a wire, or in the future, when the wire is moved or touched in the cabinet.
Annealing is an additional step in the production of ferrules. As in all cases, additional steps mean additional costs and ultimately, higher prices to the end user. Many lower-cost manufacturers skip the annealing step, so the ferrules are too hard and stand the chance of cracking.
How do I apply a ferrule?
When applying a ferrule, the conductor must first be cut flush. Using a sharp, proper cutting device will prevent a jagged edge on the cut insulation. The next step is to remove the insulation. This is a very important step, as caution should be taken to prevent damaging the individual strands. In addition, it is necessary to remove only the length of insulation required.
Removing too much will result in an extra step of cutting off the excess once the ferrule is applied. Removing too little will affect the air-tight, corrosion resistance of the connection. The strands should completely fill the ferrule’s barrel and protrude no more than .02 inches (0.5 millimeter) from the end of the barrel. (Figure 2)
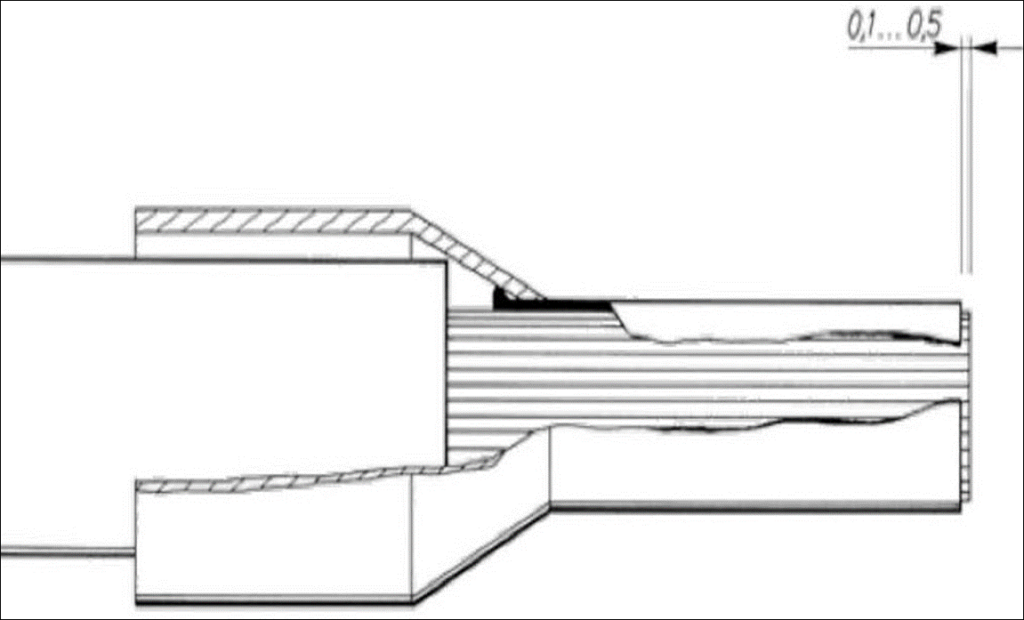
Locate a suitable wire stripper that offers strip length adjustments. The strip length should, at minimum, equal the barrel length of the ferrule. Set the strip length guide accordingly and strip the insulation off the conductor. Insert the stripped conductor into the plastic collar of the ferrule and then into the proper ferrule crimping tool to fasten. Which crimp tool and crimp profile to use is a separate subject.
The ferrule should pass a pull force test. This is a test that determines the amount of force required to pull the ferrule off the wire once crimped. There are different pull force requirements depending on the American Wire Gauge of the wire.
How does UL Listing work for ferrules?
There is often confusion about Underwriters Laboratory (UL) Listing and approval as it relates to ferrules. The simplest explanation is this: Ferrules are not UL Listed. The UL Listing applies to the combination of ferrule plus crimper. UL tests a manufacturer’s ferrules with the same manufacturer’s crimpers, and either passes or fails them. If passed, the combination is then UL Listed. Because of the testing requirements and process, mixing manufacturers is not permitted. Ferrules from Manufacturer A cannot be crimped by Manufacturer B’s crimpers, regardless of whether both manufacturers carry UL. (Figure 3)
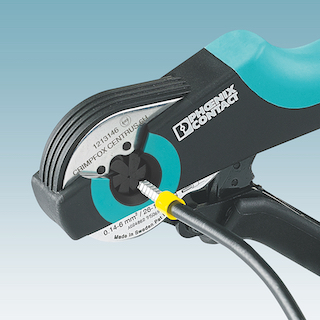
Conclusion
In conclusion, this article gave an overview of ferrules, including the purpose of the various colors, why they are used, the quality variance in the manufacturing, how to properly apply
a ferrule to the end of a conductor, and an explanation of UL Listing as it applies to ferrules.
Captions
Figure 1: In many cases, the designer can select ferrule color based on preference, but generally, blue ferrules are used for 14 AWG, black for 16 AWG, and red for 18 AWG.
Figure 2: When applying the ferrule, the strands should completely fill the ferrule’s barrel and protrude no more than .02 inches (0.5 millimeter) from the end of the barrel.
Figure 3: For UL Listing to apply, ferrules must be used with the approved crimper from the same manufacturer.
By Maria Schierscher, Lead Product Marketing Specialist, Industrial Cabinet Solutions
Phoenix Contact USA