By Joe Tito
Way back in 2017, at the annual WHMA Conference (now WHMA Leadership Summit) Paul Evans, Director of the Manufacturing and Robotics Technologies Department at Southwest Research Institute made a prediction. He was talking about the history of stationary and mobile robots and discussed their future implications for harness assembly. He said to be on the lookout for a major wave of automation in our industry. Once reserved for high-volume/low mix manufacturing, automation would be more accessible through the proliferation of sensor technology. Machines would be able to recognize, grab and process a wider variety of parts, and the glass ceiling of automation would be shattered in the relative short term.
It appears as though Paul was right. Indeed, developments in optical and pressure sensor technology have made automation possible for the high-mix/low-volume harness producers. We need look no further than the Komax’s automated wire processors, Techsonic’s Closed Loop Control ultrasonic welders, or TE’s newer FFC/FPC processing equipment to realize that Paul’s prognostications were right on the money. And these are just a smattering of the automated equipment available from these and other companies.
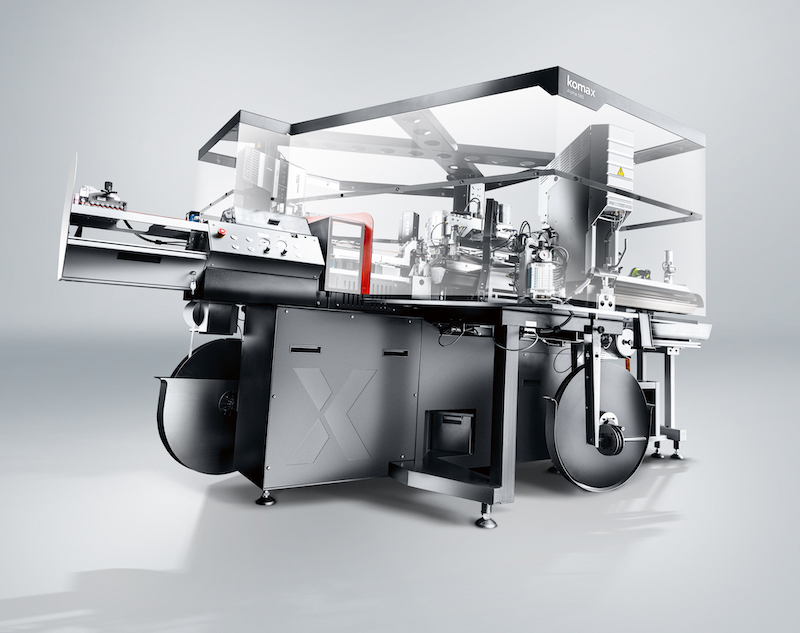
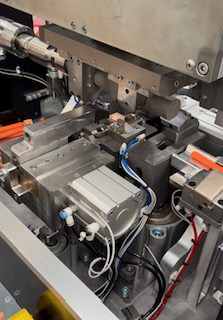
With this in mind, I jumped at the opportunity to interview Erin Byrne, CTO/VP Engineering, Sensors Business Unit at TE. Erin started by talking about her division and how key it is in TE’s new product and application development. “Sensors have been an area that we have been investing in for the better part of the last decade,” she began. “We’ve built up quite a large business there, mostly by acquisition. It started with a smaller sensor business that was targeted to the automotive space, but today we target three different verticals: medical, industrial and transportation, and we have developed harsh environment packaging for all three. We have also spent a great deal of time developing the digital interfaces the customers may need to create value with these products.”
Erin confirmed that Paul’s prediction had come to fruition, and that smaller scale automation is indeed an important market for them. Smaller scale viability, she mentioned, generally means that overall systems costs have come down, and that cost driving components have become less expensive. She confirmed sensors are a big part of that for harness production automation and other industries. “Harness production is very labor intensive. In order to automate, you have to replicate the very specialized labor of joining wires, and holding them in a certain position while cutting, stripping, crimping, or other joining technologies.”
Individual operations are all quite complicated, and Erin pointed to ways better and cheaper image sensing is key. “Multiple cameras can now be placed to be the eyes of the operator. It will give placement accuracy in real time. Newer cameras are speeding up in terms of their frame rates, so you’re getting bigger pictures and they are cheaper per pixel. I would say this is the biggest trend contributing to automation.”
Force sensor improvement and proliferation is also a major contributor to the automation boon. “If you think about when a human picks up a very fine piece of wire, you have a great deal of precision involved. The force sensors we provide are much more capable and much more accurate at low force exertion. They provide exactly the right force to pick something up and put it in range. You need more precise force sensors to do this and that’s something we are continuing to improve, making robotic handling more accessible for more applications.”
Erin further explained that it’s not just the low range gram force that is important in wire processing, but also precise control and monitoring of that force throughout an action sequence. This makes crimp monitoring more exact, enabling quicker identification of crimp force variance. She also mentioned that heat sensing is another way the tools can become more precise to predict imperfections in processes. Abnormal heat buildup can identify a myriad of problems.
Another aspect of the deployment sensors that Pete pointed towards back in 2017 and confirmed by Erin is with the use of cobots. Cobots, or collaborative robots are robots designed to work in conjunction with humans in a shared space. “This is a big area of interest for our business,” Erin said. “There is the safety aspect of making sure that when the cobot touches a surface it shouldn’t, there is a safety stop.” The cobots do this through a combination of force/torque, vision and proximity sensors.
So, what has changed to bring about these advancements? Erin answered, saying, “When we talk about image sensors, that’s related to advancements in semiconductors. With cameras, it’s more of a volume and productivity play. We don’t make our own image sensors, we package them. They are produced by our supplier partners who bring the cost down. When you talk about heat sensors, those are strictly volume plays. There’s nothing new technically that’s driving the cost of those down.”
Another major factor allowing Erin and her team to better integrate these sensors into a more economically deliverable automation tool is the availability of powerful, off-the-shelf microcontroller units (MCUs). “Sensor output is usually analog,” she advised. “We wouldn’t design our own analog controller for a small customer, so we have the solutions with off-the-shelf microcontroller units that are digitizing the output and may be providing some edge processing and local computing, while providing the signal in a way that is more standardized in terms of the communication protocol that the customers will use.”
TE is always monitoring the environment where their tools are operating and designing tools and sensor packaging to address each application. “We can’t cover all of the requirements generically, so we often say we design products for a particular industry or customer, and therefore the requirements to go along with that. Machines may need to withstand ten years in a debris filled environment or they may need to be resistant to acid or other substances. It may or may not involve an industry standard, but it gives us some validation testing requirements.”
In conclusion, Erin stressed TE’s continuing support of automation through the integration of sensor technology. “I think you will agree the world is becoming smaller and smaller and that just means there is a need for more and more sensors. We aim to be a leader in intelligent sensing, and I think if we do our jobs right and build the scale we need, we will continue to bring the glass ceiling of automation down.”