Introduction
In the ever-evolving world of industrial electrical connections, innovation is the key to staying ahead. This article describes a new groundbreaking advancement that promises to open new avenues in the industry. In collaboration between Telsonic and the renowned KERN-LIEBERS Group, this cutting-edge solution provides a robust method for securing silver-plated aluminum busbars using screws, setting new standards for reliability and conductivity.
Today, there are up to two dozen busbars in a battery pack, and that number will rise as battery packs get larger and/or more powerful, while the space inside them remains incredibly tight. Ultrasonic welding is a preferred joining process for busbars in EV applications. But, because these more powerful batteries are only as good as their ability to charge quickly, we will soon see more busbar innovation outside the battery pack as well, routing high power from charging inlets to batteries and out to other high-power motors and devices, drivig the need to innovate ultrasonic welding applications.
Benefits to using busbars:
- Reduced facility costs and faster installation
- Ability to add, remove or relocate power easily and quickly without any downtime
- Future-ready and highly flexible as some plug-in units can be disconnected and reconnected without de-energizing
- Require no routine maintenance
- Faster and less costly for expansion or remodeling
- More environmentally friendly as it often requires fewer installation materials and plug-in outlets are reusable and easy to relocate
- Flat conductor takes up less space, 70% shorter in height
- Can support up to 15% more power than a cable with the same cross-sectional area
- Less weight and packaging space, with much better flexibility. E.g., 160 mm² Flexible Flat Aluminum (FF-Al) cable is an innovative and alternative solution to 200 mm² round Al cable
- Use bolts for fastening which is the most reliable process today and less costly.
- Efficient heat dissipation – More effective than stranded cables
- Multiple Constructions – Cu & Al, rigid or flexible, laminated.
- No EMC required for inside battery
- Facilitates automation which improves safety and quality
Overcoming the Challenge: Securing Silver-Plated Aluminum Busbars
The KERN-LIEBERS Group, a leader in precision stamped parts, has pioneered an inline technique for coating aluminum busbars with silver, significantly enhancing their conductivity. However, this advancement brought with it a unique challenge. Aluminum’s natural relaxation properties made it difficult to secure these busbars with screws without compromising the connection over time.
To tackle this, the experts at KERN-LIEBERS and Telsonic embarked on a mission to find a solution that would maintain the integrity of the silver coating while ensuring a secure, durable connection. The result was an innovative approach involving the integration of a copper sleeve into the busbar, which provides both the necessary durability and excellent electrical conductivity for screw fixation.
The Innovative Solution: Integrating Copper Sleeves with Ultrasonic Welding
This revolutionary solution involves the precise placement of a copper sleeve into a pre-punched hole in the silver-plated aluminum busbar. The copper sleeve, designed with an oversized collar, facilitates the effective transmission of torsional ultrasonic vibrations through a sonotrode. This process welds the copper sleeve to the silver layer, ensuring a robust bond that preserves the silver coating’s integrity (figure 1).
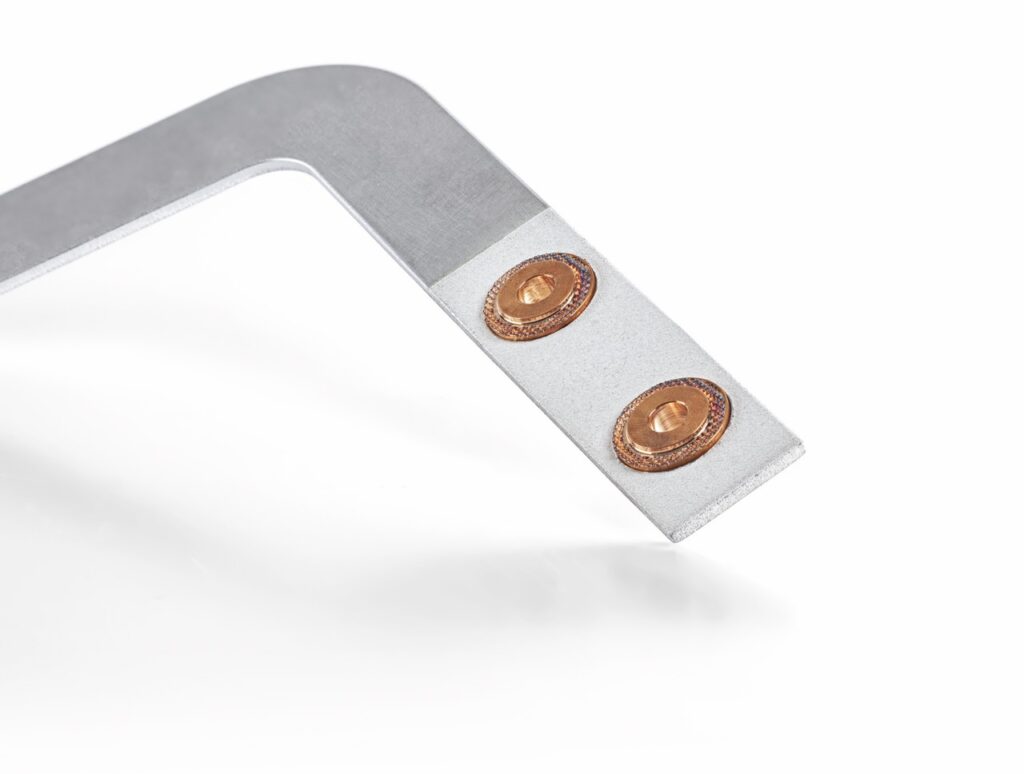
Material Properties and Advanced Welding
At the heart of this solution are the remarkable material properties and the sophisticated welding process:
- Silver Coating: Enhances electrical conductivity and compatibility with various aluminum alloys.
- Aluminum Base: Offers a lightweight, cost-effective foundation for busbars.
- Copper Sleeve: Ensures a strong, conductive connection point for screws.
Ultrasonic welding, especially Telsonic’s torsional SONIQTWIST® technology, excels in joining dissimilar metals with minimal electrical resistance. By generating localized heat through high-frequency vibrations, the materials fuse without melting, maintaining the essential properties of the silver coating and ensuring a stable, enduring bond.
Advantages of Ultrasonic Welding Over Other Techniques
Ultrasonic welding offers numerous advantages over traditional welding and joining methods, making it particularly well-suited for this application:
- Precision and Control: Ultrasonic welding provides high precision and control, essential for delicate materials and complex geometries.
- No Need for Additional Materials: Unlike traditional welding, ultrasonic welding does not require solder, flux, or adhesives, reducing material costs and contamination risks.
- Energy Efficiency: The process is highly energy-efficient, using significantly less power than conventional welding methods.
- Minimal Thermal Distortion: Ultrasonic welding generates much less heat, minimizing thermal distortion and preserving the properties of the materials being joined.
- Speed and Efficiency: The process is rapid, allowing for high production rates and reducing manufacturing time.
Configuration Advantages
The inclusion of a silver coating expands the range of aluminum alloys suitable for ultrasonic welding, significantly broadening industrial application possibilities. The configuration boasts numerous advantages:
- Reliability: Ultrasonic welding delivers a dependable, long-term stable connection between dissimilar metals.
- Efficiency: Producing busbars with pre-punched holes is cost-effective, and integrating the silver coating into the production process eliminates extra transport costs for external coating.
- Enhanced Performance: The combination of materials ensures minimal electrical resistance, boosting overall conductivity and performance.
Successful Implementation: Torsional SONIQTWIST® Technology
The successful implementation of this groundbreaking solution was made possible by Telsonic’s exclusive torsional SONIQTWIST® technology, specifically the TSP3000 torsional welding system (figure 2)
. This system has proven its ability to meet the stringent demands of industrial applications, providing a reliable and conductive connection for silver-plated aluminum busbars.
The torsional SONIQTWIST® technology uses torsional vibrations, which are particularly effective for welding complex geometries and delicate materials. This method ensures a homogeneous bond across the interface, crucial for maintaining both electrical and mechanical integrity.
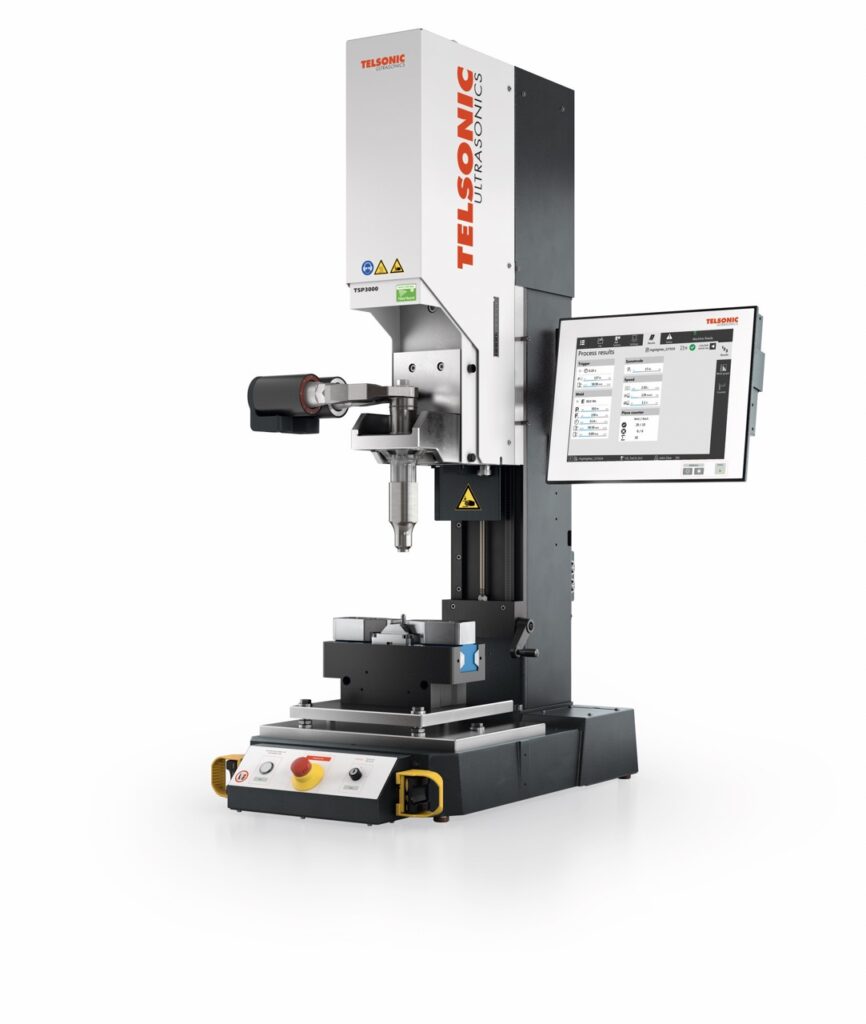
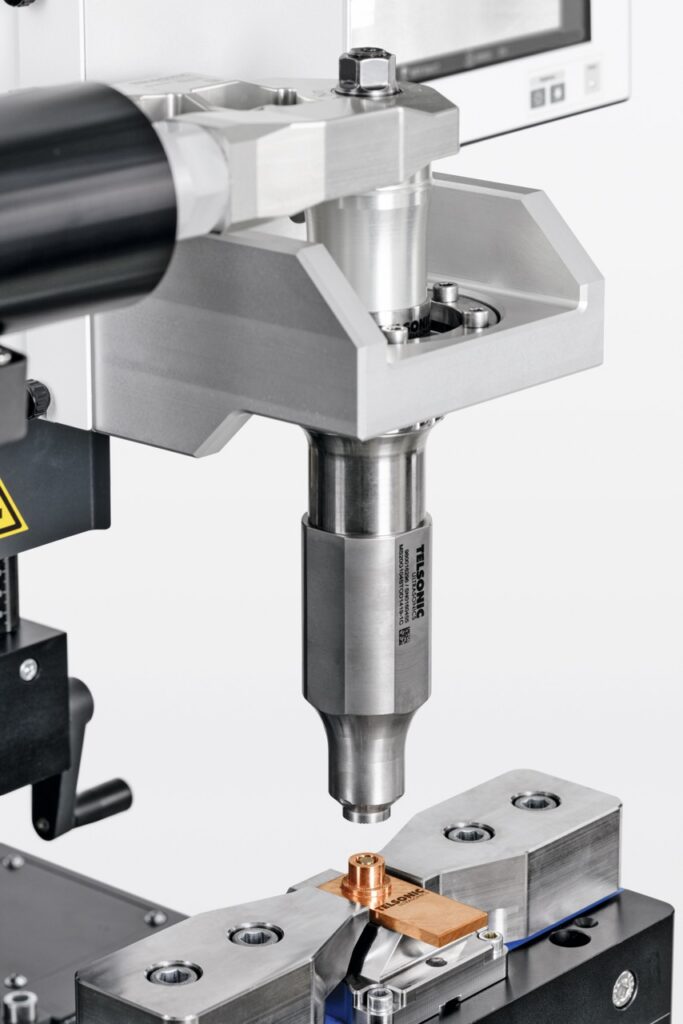
Figure 2. Telsonic TSP3000
Conclusion
As industrial demands continue to evolve, pioneering solutions like this will be essential in setting new benchmarks for reliability and conductivity in electrical engineering. We are excited to see the impact this innovation will have on the industry and look forward to continued advancements that drive progress and excellence in industrial electrical connections.
Additional Information: The Future of Ultrasonic Welding
Looking ahead, the potential applications of ultrasonic welding are vast and varied. This technology is not only limited to electrical connections but also extends to the automotive, aerospace, and medical device industries. Its ability to create strong, reliable bonds without the need for additional materials or excessive heat makes it an attractive option for a wide range of manufacturing processes.
Moreover, ongoing research and development in ultrasonic welding are likely to yield even more sophisticated techniques and equipment, further enhancing its capabilities and efficiency. As industries continue to seek ways to improve performance and reduce costs, ultrasonic welding is poised to play a critical role in the next generation of manufacturing technologies.
By Dirk Schnur and Saeed Mogadam