By David Norquist
Schunk Sonosystems provides a range of standard and customized ultrasonic equipment tailored to our customer’s specific manufacturing needs. Our range of industries touches automotive, battery, refrigeration, power electronics and other industries where ultrasonic metal welding has been adopted and is the preferred technique.
Inside the technology, ultrasonic metal welding is a solid-state joining process that utilizes high frequency ultrasonic vibrations to create a strong bond between metal components. Unlike traditional welding techniques such as soldering or resistance welding, ultrasonic metal welding does not require the melting of base materials. Instead it relies on the application of pressure and oscillatory motion to forge a metallurgical bond between the materials. The material can be same or dissimilar for example joining copper to aluminum.
The process typically involves the following:
- Preparation: The materials are cut and stripped to the proper lengths and clean
- Clamping: The two material pieces are clamped together using tooling designed for the application.
- Ultrasonic vibration: A transducer generates high frequency vibrations, Schunk uses 20 Khz and 35 Khz. The vibrations are transmitted to the metal components where they create heat and friction.
- Bonding: As the pieces of material heats up due to friction the metal atoms diffuse across the boundary layer, forming what is called a true metallurgical bond.
Some of the advantages of ultrasonic metal welding are:
- No melting: Since the ultrasonic process does not involve melting, there is minimal material distortion.
- High speed: The welding is a rapid process which makes it suitable for high-speed production and weld are achieved in most cases in under one second
- Clean and environmentally friendly: With no fumes, sparks or consumables involved, the process is environmentally friendly.
At Sonosystems we are involved in many industries where this ultrasonic process lends itself to be the best option for metal welding. Nothing is truer than our automotive wire harness application. We specialize in two major applications in this industry 1) wire to wire welding and 2) wire to terminal welding.
Wire to wire welding is just that, where we can join two or more wires. Sonosystems has the capability to join wire as small as .26mm2 up to 300mm2 with our portfolio of welding machines. Each one of our splice welding machines have been designed and refined to ensure welding is consistent, strong and passes quality standards that the customer sets.
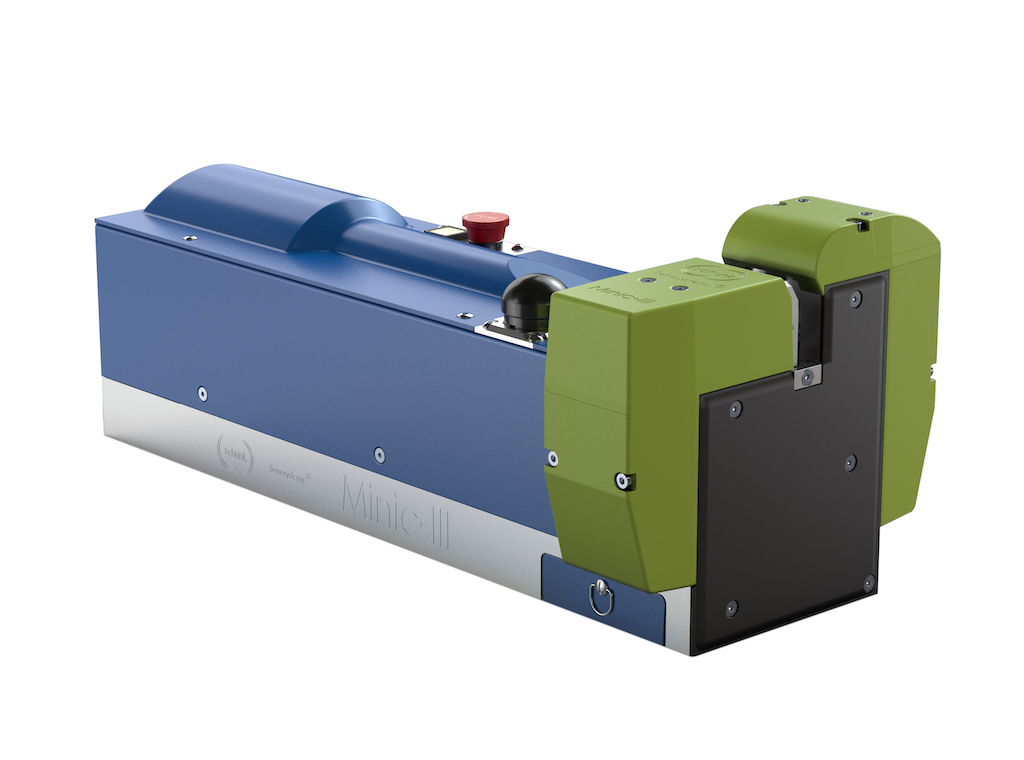
The Minic-III splicing system we offer the is most modern, fastest, most user-friendly and low-maintenance ultrasonic welding machine on the world market today. The machine covers the range of cross-section sizes that include 99% of your welding jobs. A benchmark for the worldwide leading wire-harness manufacturers, this machine has delivered the best welding results with respect to strength, Cmk / Cpk as well as the visual appearance of the splices produced, in all applications.
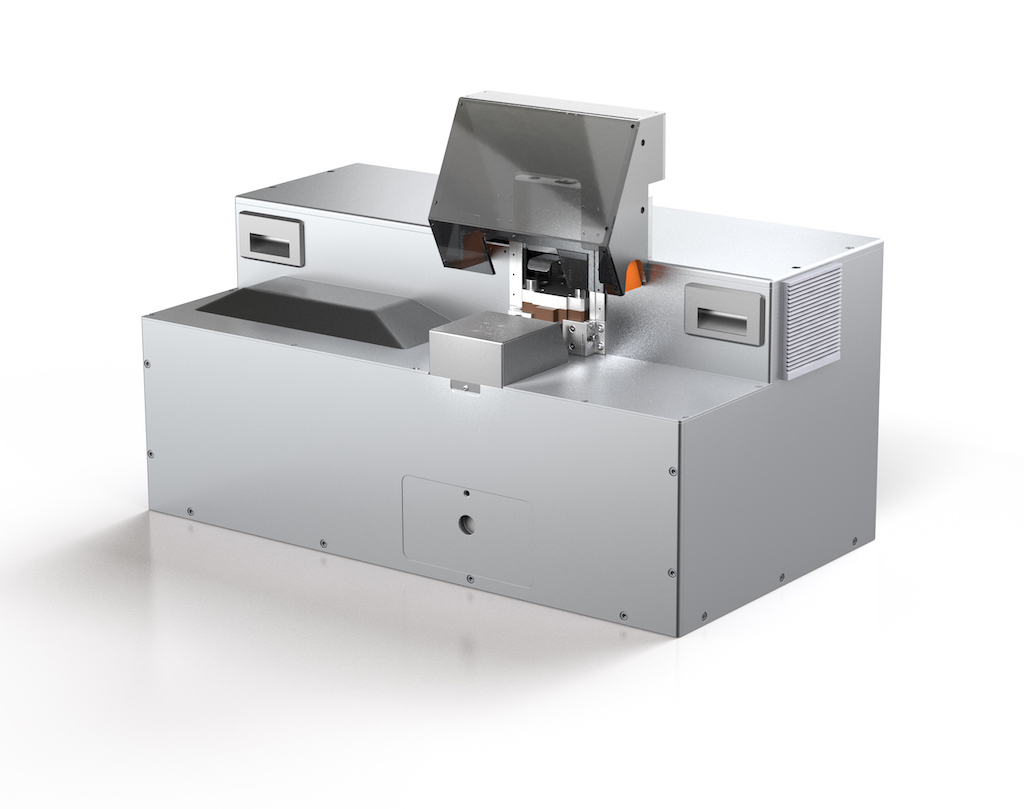
The L-Splice is designed for welding splices in the upper cross-section range of up to 100 mm² or 200 mm². The L-Splice is well suited for both manual operation and integration into a fully-automated production system. There are two different design variations available for optimal ergonomic operation. Regardless of which model you choose, machines of the L-Splice series are built to withstand high thermal and mechanical stress.
Wire to terminal applications are bit more involved due to the unique geometric shapes of the terminals. Our experienced engineers get involved from the beginning to create the proper tooling to be able hold the terminal in the correct position and firmly, without damaging it, during the weld process. These applications can range in size to use wire as small as .35mm2 to the high end of 120mm2. Sonosystems products can provide customers with the correct machine for the range of their application needs.
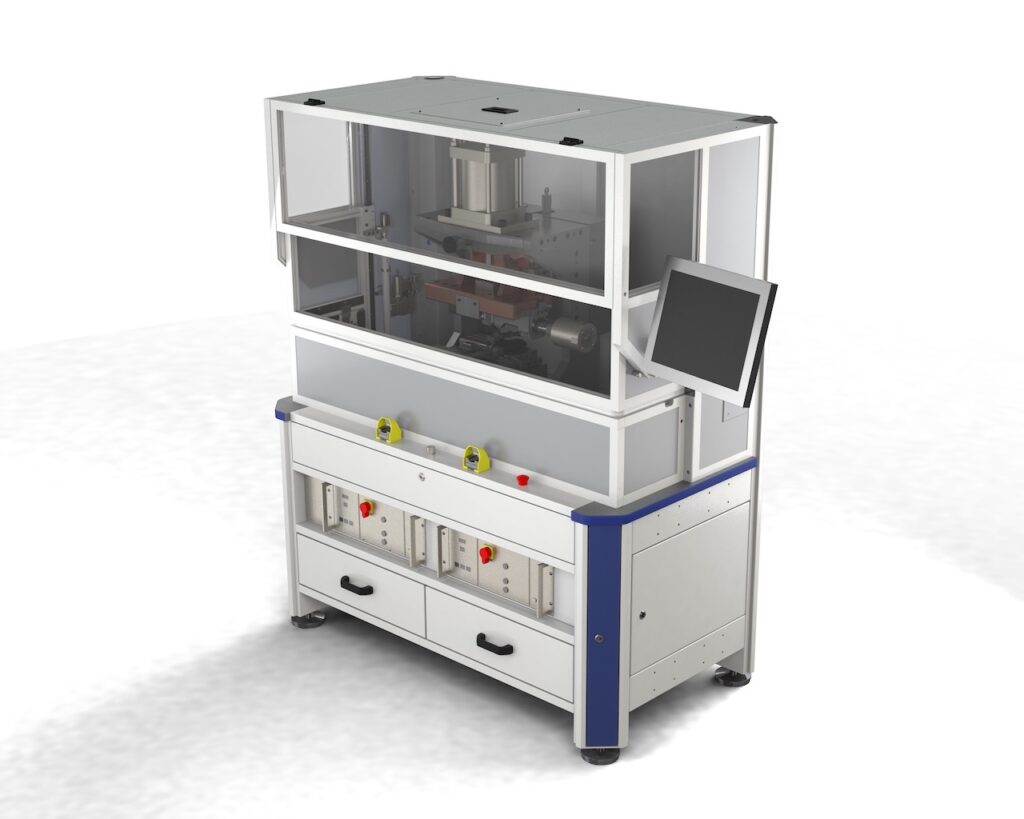
The LS-C is Schunks latest wire to terminal or busbar welding machine. This unit has a cross section range from 6mm2 to 200mm2. The LS-C is suitable for numerous terminal applications such as tubular cable lugs or busbars. Welding of Copper and aluminum wires to terminals. Can be used on for insulation crimps and a reject management cutting device. This unit can be integrated into automation for the end user.
Both applications used the same ultrasonic principles however, when wire sizes increase, the power and the pressure needs to be increase accordingly. Sonosystems has developed a family of systems to be able to step up power and pressure as the applications grow in size.
From an operator point of view the equipment and the software has been refined over the years such that the screens are intuitive even for the first time operator. We have spent year developing operator aids so that the process is repeatable and have built in failsafe to ensure no bad product can move forward in the production process. Examples of these aids are:
Alarms for various nonconformance conditions.
Cutting systems to segregate good and bad welded pieces.
Vision systems, to recognize correct terminal and terminal placement.
In the case of end and inline splices, the length of the overlap of the strands and the distance between the welding area and the insulation of the cables are often specified. Both are influenced by the manual insertion of the strands.
With the Cable Fit-In module, Sonosystems has developed an external insertion aid that ensures absolutely reproducible welding results and exact adherence to the specified dimensions. The cables are optimally placed in the welding area by means of two clips. The distances can be preset and configured according to the application, specifications and cross-section range.
All systems include SQC reporting to check batch consistency.
These are only a few of the aids offered to benefit the operator and the process such that both can be as efficient as possible.
The systems are manufactured at one of our three sites worldwide to a common standard to ensure the products made in Europe would be the same as it made in USA as well as Asia. With ISO 9001 certification our customers can be certain that the quality and attention to detail meets our high standards.
We cannot ignore the effort we put into our world class global service and support group. Over the years we have put a tremendous amount of effort into developing internal systems to increase the speed and efficiency in which our service team can respond to customer. It does not matter where in the world our customers are, a factory trained service engineer can be contacted and send out spare parts from one of our locations. For example, a project may start in the USA but be transferred to Asia. Once this happens the global network of Sonosystems starts and provides local support and spare parts.
Our company’s success is predicated on our customers success. The Sonosystems guiding principles are to take care and partner with our customers. By being “the dependable supplier”, this allows our customers to have confidence when accepting contracts to be able to produce parts of high quality and on time. Working closely with our key users also gives us insight into the next generation of products and or problem they face. Working collaboratively, this information allows us innovate real world solutions which affords us to stay number one in the industry.