STRUNK Connect has more than 50 years of expertise and innovation in resistance welding of non-ferrous metals and was founded in 1972 by Mr. Helmut Strunk. The company started as dealer and distributor of welding accessories and tools in Germany’s welding technology cluster approx. 100 km by car northwest of Frankfurt/M. As of 1980 the product range expanded to own controllers and monitoring systems for resistance welding technology. In 1986 the first own welding machine was developed and delivered to the wire harness industry. The first project as supplier of an automated system was successfully acquired and executed 1992. Since then the company evolved and in the 2012 the first project as system integrator for an e-traction application was executed for an automotive OEM.
Over the years STRUNK Connect has grown to a renowned partner for companies in the automotive, electronics and solar industries, medical technology and the white goods and defence sectors, with approx. 80 employees.
In addition to our German headquarters, we maintain since 2010 a subsidiary in Florence (SC) and work with partners for sales and service in China, Morocco, and Poland. The next countries we want to cover are India and South Korea.
Megatrend electrification and its impact on STRUNK connection technologies
The ongoing megatrend of electrification throughout all industrial and private consumer segments in conjunction with energy saving requirements and increased safety requirements calls for highly reliable and efficient power distribution and signal transmission. This is typically achieved via copper and/or aluminium conductors: stranded wires, braided wires, bus bars, etc.
Here are a few examples where STRUNK resistance welding solutions are applied:
- Power distribution with all connections used for:
- copper and aluminium bus bar systems
- flexible bus bar systems with braided wires and foil layers
- HV wire harness with HV connectors
- Inverter systems
- Storage / Battery
- E-traction with hairpin and magnet wire applications for stators and rotors
- AC/DC charging in vehicle and stationary applications
- Sensor signal transmission in safety environment or automotive applications
- Energy transmission in household appliances, e.g. inductive ovens, washing machines, etc.
The special STRUNK resistance welding process under braze or without delivers extremely tensile strength in addition with highest reliability and full traceability.
Features and benefits of STRUNK resistance welding
The technology ensures a real weld in the melting phase of the joining partners for only milliseconds with minimal heat impact on the components. With newest technology of three phases DC machines joining areas of more than 1000 mm2 in one shot can be achieved. No additional water needs to be applied on top of the joining partners for chilling purposes. This avoids oxidation and prevents later high resistance. Depending on the material combination and cross section STRUNK applies by full automatic and totally monitored feeding systems braze foil in between of the joining partners to ensure reliable weld under braze. The process is controlled in that way that the joining partners will come to an inter-metal connection so that mentioned tensile strength in pull and peel forces can be achieved. The monitoring and control of the full process delivers diverse parameters and arguments for traceability (MES) to ensure this high reliability.
The connection itself shows no aging or corrosion over lifetime paired with nearly no resistance and high conductivity. Problems in derating and automotive tests are things of the past.
STRUNK resistance welding in the production environment
The STRUNK resistance welding process itself is a versatile process and robust process:
– Unlike than other connection technologies, STRUNK resistance welding is resilient to surface contamination of joining partners: dirt, oil, oxidation, etc.
– Low temperature input on joining partners
– Welding of tin-coated products and other coatings is possible
– Welding of Aluminium and Copper either as welding of Aluminium stranded wires into copper sleeves or via butt-welding of busbars made of Aluminium and Copper.
STRUNK Connect’s portfolio of solutions
With over 50 years of activities in resistance welding, STRUNK Connect is a renowned manufacturer of customized machines and solutions in:
- Benchtop,
- semi-automatic,
- full automatic,
- and system integrated design out of one hand.
Following application processes are covered:
- Hot Crimping
Welding of stranded magnet wire into standard copper sleeves or cable lugs with unlimited cross -sections without prior stripping.
- Welding Under Braze
Overlap and butt-welding of connection areas up to 1000mm² with automatic braze feeding in manual automated STRUNK lines.
- Terminal Welding
Connection in the low voltage wire harness to terminals. Direct welding without prior compacting of strands via a special tool. - Wire Compacting
Stranded or braided wires up to 1000 mm² area in one shot optional with inline stamping and calibration processes to achieve surface quality and tightness like copper busbars. Subsequent processes with the compacted ends are possible.
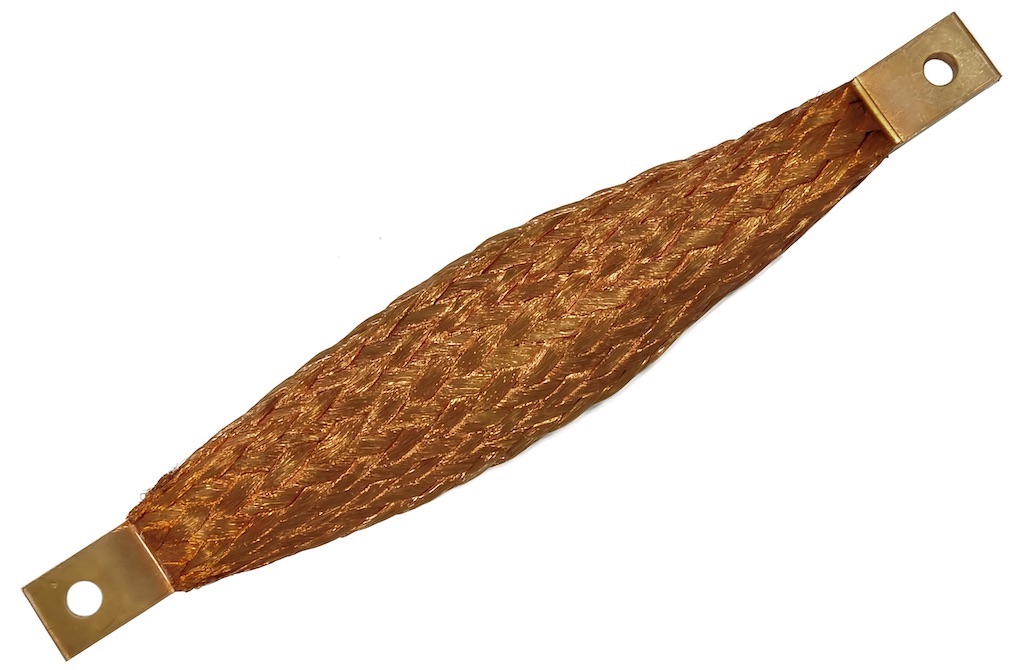
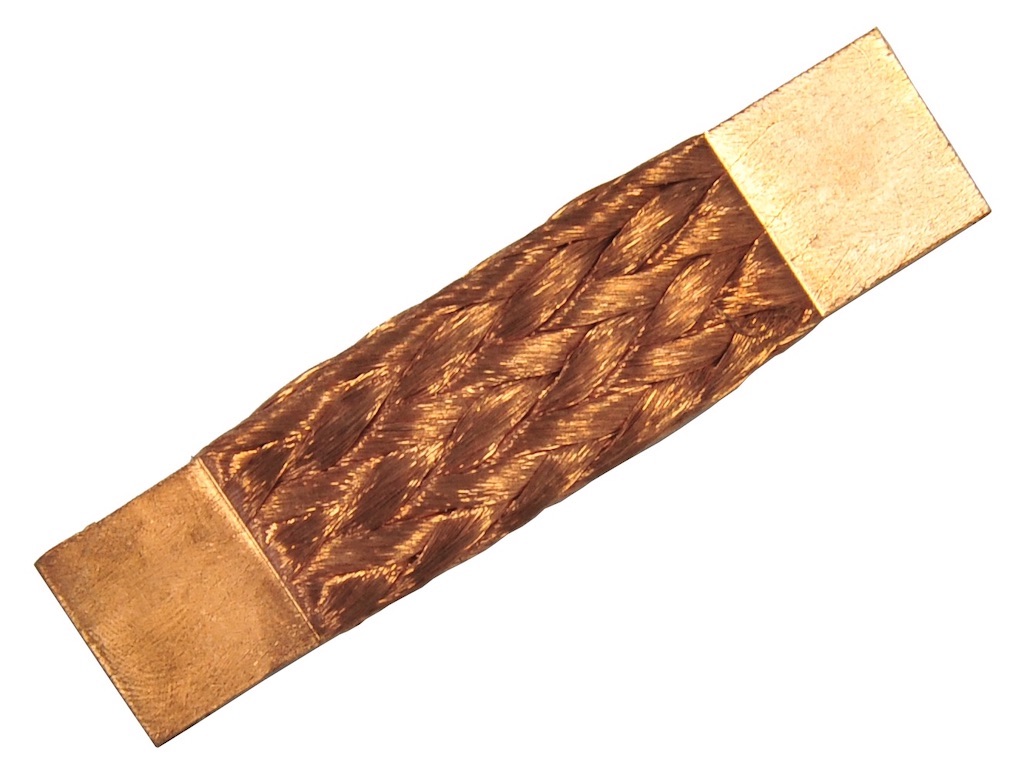
- Splicing
Very thin wires (medical applications) up to 400mm² can be handled. Welding of tin coated wires, copper cables or other alloys.
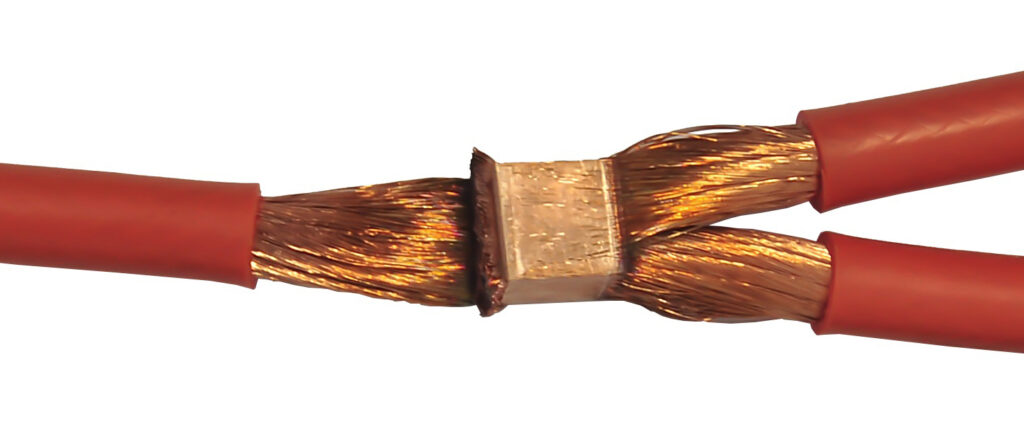
- Micro-Welding:
Small structures with minimized heat impact. - Diffusion Welding of copper foils with STRUNK three phases DC Resistance Welding
Fast joining of multiple thin copper layers (e.g. 80 x 0.2mm) with minimum heat impact. Suitable for bonding areas up to 1000mm² in one shot and without additional water application.
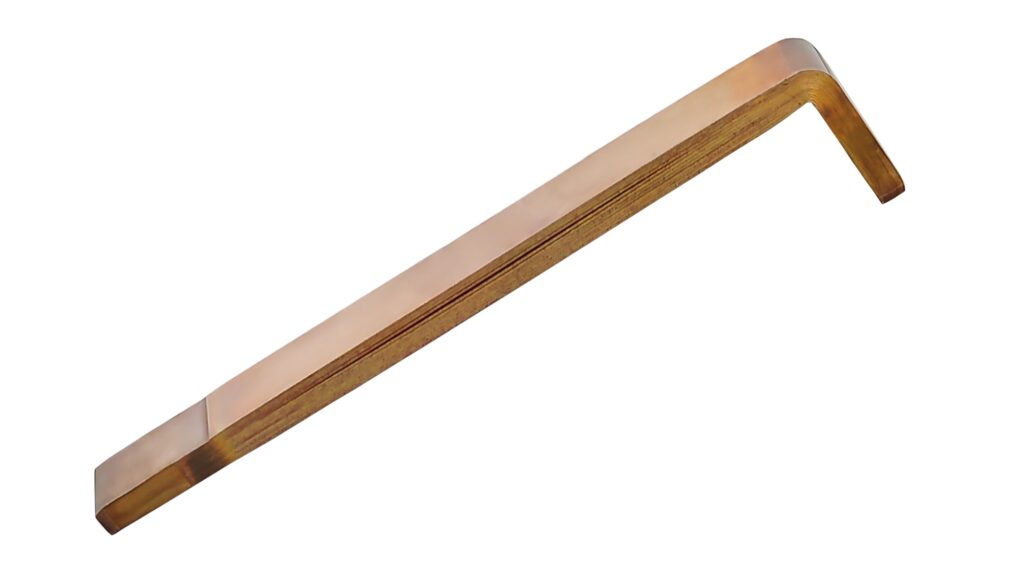
- NEW: Copper and aluminium connections.
- Butt-welding of aluminium and copper busbars and of copper wires to aluminium busbars without inter-metallic phases.
- Welding of aluminium stranded wires into standard copper sleeves or cable lugs.
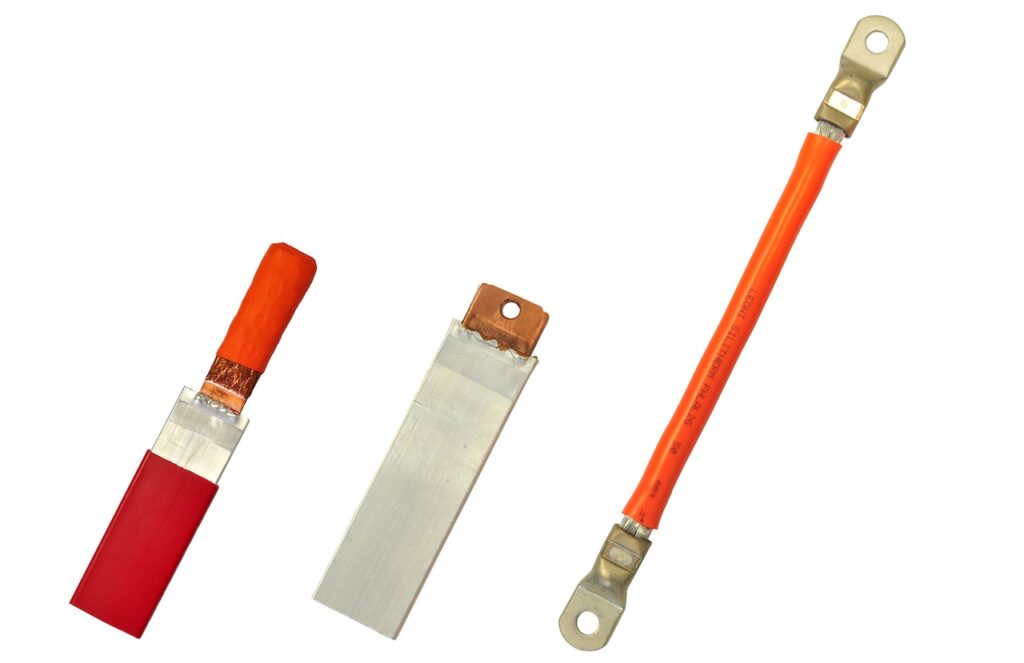
STRUNK resistance welding – The experts in connection
Our approach is to supply the right solution for highly reliable and high performing connections of non-ferrous metals. We assess the feasibility of the process for the requested application in our laboratory. For the industrial production requirements, we consider production quantities, number of variants, traceability and provide a suitable and even scalable machine solution.
We are here to support your ambitious connection challenges.