By Greg Ruscak – Telsonic
Ultrasonic welding has become a cornerstone in wire harness and battery manufacturing, offering a host of advantages that are increasingly essential in today’s fast-paced production environments. This technique provides high-strength connections, short weld times, and eliminates the need for additional materials like adhesives or fluxes. The process consists of two parts being rubbed together under high pressure and frequency. The resultant heat leads to the softening of the materials at the interface which causes short-distance diffusion and recovery to occur. This bond occurs in the solid state and can typically be completed within 0.3 – 3.0 seconds with little to no change in the material composition. The high-speed movement can also displace small levels of contamination to clear the boundary layers enhance the reaction. This technology is similar to traditional friction welding and is classified as a cold pressure welding process according to DIN 1910. These welded connections can yield close to the strength of the surface material in some applications, and they boast low electrical resistance, close to the electrical resistance of the metals themselves. These are crucial qualities in industries like data transmission, power electronics, and automotive.
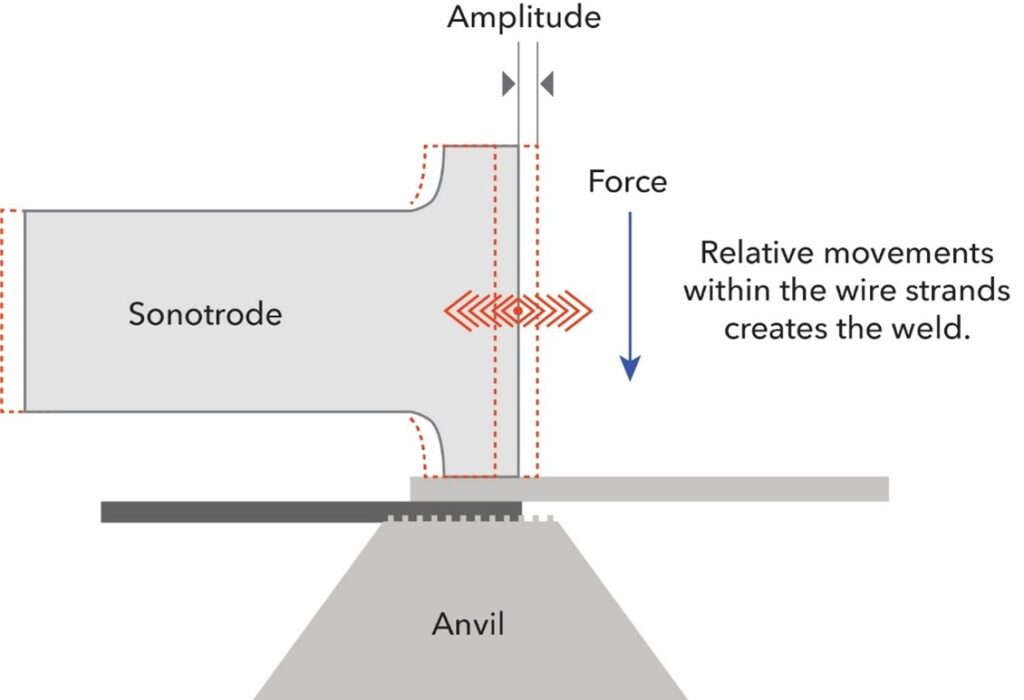
Ultrasonic welding systems are also highly adaptable to high-volume applications, whether they are used for single operations or fully automated production lines. Compared to traditional joining methods, ultrasonic welding offers substantial advantages in reducing scrap and minimizing downtime.
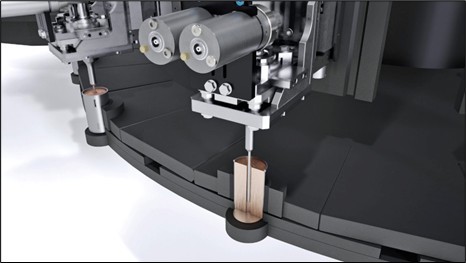
This makes it an attractive solution for manufacturers looking to maximize efficiency and reduce costs while maintaining high-quality production standards. Though ultrasonic welding is already robust and reliable technology, engineers in manufacturing are always striving to improve quality, reduce waste, and increase production throughput. Many wire joining techniques in modern manufacturing include some form of quality measuring system, which helps identify flaws in the process. However, one of the major challenges faced by production teams is the degradation of a process over time. At the beginning of a production run, the welding process might operate flawlessly, but over several days, months, or years, issues can arise, causing inconsistencies in the final product.
Ultrasonic welding has a significant advantage over many other wire joining techniques in this regard because it allows for real-time monitoring during the welding operation. This enables manufacturers to address issues as they occur and prevent bad quality parts from progressing through the production line. By continuously tracking performance during each welding cycle, operators can eliminate errors early in the process, preventing costly downstream defects and ensuring a smoother, more consistent operation.
In addition to the advantage of real-time monitoring, the sensitivity of the process can be adjusted to detect small defects. Every input into the system must be analyzed, as even a small change to the application can affect the outcome of the weld. To ensure consistent, high-quality production, it is critical to treat each application as unique, even when the same general method is used. Engineers must recognize that minor modifications such as switching material suppliers, altering specifications, or changing the terminal plating can drastically affect the results.
Even seemingly insignificant factors like changes in wire insulation or the color of the insulation can impact the process in unexpected ways. Therefore, whenever the specifications of the materials or application change, they must be revalidated. These adjustments may seem minor, but they have the potential to disrupt the welding process and introduce defective parts. To maintain consistency and avoid defective parts, it is essential that materials be stored properly, free of oils, oxides, or foreign contaminants. By managing these factors effectively, manufacturers can avoid introducing variables that might otherwise compromise the welding process.
A critical aspect of ultrasonic welding is ensuring that the materials going into the process are of the same high quality as the final product expected. The process itself is highly repeatable, so whatever is fed into the system will have a direct effect on the final world. This means that the quality and consistency of materials entering the machine are just as important as the settings of the ultrasonic tools themselves. By establishing proper material quality checks and adhering to stringent preparation procedures, manufacturers can maintain the integrity of their production process and avoid defective parts.
To set up an ultrasonic welding process, a thorough understanding of the specific application is required. This includes a range of specifications, such as the wire and terminal materials, wire size, terminal dimensions, and assembly requirements. Without this information, it is nearly impossible to establish an effective ultrasonic welding process. When the application is well defined, it allows the manufacturer to select the correct tools and parameters from the outset, ultimately setting up the process for success.
Ultrasonic welding achieves optimal results when product-specific tooling is designed to meet the precise requirements of the customer. Tooling ensures that the welded parts adhere to the necessary tolerances and specifications. The primary tools used in ultrasonic welding are sonotrode, anvil, nest, and gather blocks. Each of these components serves a vital role in achieving the perfect weld.
- The sonotrode is the tool that transmits ultrasonic vibrations into the workpieces. It is typically made from hard, durable material like steel or titanium and is designed to ensure precise energy transfer to the weld interface.
- The anvil provides support for the terminal, ensuring it remains in place during the welding process. Typically, the anvil is knurled to grip the terminal securely and prevent any movement.
- The nest or mask positions the terminal in the exact location relative to the sonotrode, ensuring accurate alignment during welding.
- The gathering blocks help to clamp the terminal in place, defining the width of the weld nugget and ensuring uniform pressure distribution during the welding process.
Together, these tools are essential for achieving strong, reliable bonds and meeting customer specifications. When selecting ultrasonic tools for a specific application, it is vital to ensure that the proper tools are used to optimize tool life and minimize downtime during changeovers. By using the right tooling, manufacturers can reduce the need for frequent replacements and maintain production efficiency.
Once the application and tooling are properly defined, the next critical step is determining the appropriate process parameters. The most important parameters for ultrasonic welding are energy, pressure, and amplitude. These inputs play distinct yet interconnected roles in achieving a strong and reliable bond.
- Energy refers to the amount of ultrasonic motion delivered to the materials. By setting a specific energy level, the system can compensate for minor variations in material properties. However, if the variation is too significant, the system may be faulty and stop the weld from occurring, ensuring that only quality parts pass through the system.
- Pressure is essential for achieving a good bond. Without proper pressure, the materials cannot be properly fused, as the ultrasonic energy alone is insufficient. Pressure helps deliver the energy in a controlled manner, ensuring a uniform, weld quality.
- Amplitude controls the degree of expansion and contraction of sonotrode. It regulates the intensity of the ultrasonic vibrations, and, in turn, the amount of heat generated at the welding interface. Amplitude is particularly important for different materials that require varying degrees of excitation to achieve optimal bonding.
Defining the appropriate settings for the inputs can be overwhelming, especially when starting with a new application. The best approach to optimization is by a parameter optimization process and design of experiment. This method allows manufacturers to systematically explore different parameter combinations and identify the optimal settings for each unique application.
Using design of experiments (DOE), engineers can eliminate guesswork by optimizing these critical inputs based on experimental data. By establishing ranges for these parameters and verifying the results, manufacturers can create a reliable and repeatable process that reduces the risk of defects and improves overall throughput.
Training in ultrasonic welding processes is highly recommended for operators to ensure they are equipped to fine-tune the system effectively. By understanding the relationship between the parameters and the outcomes, operators can confidently make adjustments to optimize the process. Given that manufacturing environments are dynamic, it’s important to recognize that changes in factors like tool wear, material variability, and personnel changes can affect reliability. Therefore, real-time monitoring of outputs is crucial for identifying deviations from optimal conditions and making necessary corrections.
Once the process parameters are established, it’s vital to continuously monitor the system to detect any changes or potential issues that could affect the quality of the welds. Real-time monitoring systems provide valuable feedback on the welding process, allowing manufacturers to identify tool wear, material variations, and deviations from the defined parameters.
In addition to monitoring critical process variables, ultrasonic welding systems can incorporate advanced measurement devices to assess weld quality. For instance, integrated load cells can detect if the weld is being subjected to the correct amount of force. Distance measurement devices can precisely measure the displacement of the weld to ensure that the desired compaction has been achieved.
Tensile tests can also be performed to measure the strength of the ultrasonic weld. However, these tests are typically performed on sample parts, which may not always reflect the consistency of the entire production run. Additionally, destructive testing of production materials is often impractical due to time and cost constraints. This is where real-time measurement systems offer a distinct advantage, as they enable continuous quality assessment without the need for destructive tests. Some of the key metrics that are critical for monitoring the quality of ultrasonic welds are the amount of power delivered to the workpieces during welding which can be monitored to ensure that the welding process is operating within the defined parameters. The duration of the ultrasonic pulse can be measured to verify that the weld is completed within the optimal time range. The amount of force applied to the workpieces during welding is crucial for achieving a strong bond. Accurate displacement measurement ensures that the desired compaction has been achieved, contributing to a strong, uniform weld. These metrics, when analyzed together, form the foundation of statistical process control. By defining quality control limits based on these parameters, manufacturers can detect defective parts early in the production process, ensuring that only high-quality welds progress to the next stage.
Tool wear is an inevitable part of any manufacturing process, and ultrasonic welding is no exception. As the ultrasonic sonotrode, anvil, and gathering blocks undergo repeated use, they gradually lose effectiveness, which can impact the quality of the welds. Detecting tool wear in ultrasonic welding can be a challenge, particularly in high-volume production settings. Some systems feature basic built-in tools that allow operators to input expected tool lifecycles and receive alerts when the tools are nearing the end of their usable life. These alerts provide valuable warnings that help reduce downtime and keep production running smoothly. However, for some systems, tool wear is not easily detected without more advanced monitoring tools.
With the increasing integration of digital technologies in manufacturing, it is becoming possible to monitor the health of welding tools more effectively. Digital sensors can track changes in tool performance by alerting operators of wear before it becomes a significant issue. This data can also be used for predictive maintenance schedules, allowing manufacturers to replace tools proactively before they fail, reducing unplanned downtime. Digitalization is transforming the way ultrasonic welding systems are monitored and controlled. Advanced software solutions now offer adaptive data monitoring that enables production teams to closely track performance in real time. This technology is particularly beneficial for remote troubleshooting, as supplier support teams can also access production data and offer faster, more accurate assistance when needed.
Moreover, digital systems like Manufacturing Execution Systems (MES) are integrated with ultrasonic welding systems to track production data, including quality metrics, tool wear, and part traceability. By combining real-time data with MES, manufacturers can optimize their processes even further, improving both the quality and efficiency of production.
Ultrasonic welding has evolved from a niche, specialized technology into a widely adopted solution for high-speed, high-quality production. As manufacturing demands continue to increase, the advantages of ultrasonic welding particularly in speed, reliability, and precision become even more apparent. By incorporating advanced measurement systems, real-time monitoring, and digital technologies, manufacturers can further enhance the performance and efficiency of their ultrasonic welding operations.
With continued innovation, ultrasonic welding will remain at the forefront of manufacturing, providing versatile and scalable solutions to meet the growing challenges of industries like automotive, electronics, and beyond. By embracing these technological advancements, manufacturers can improve their production processes, maintain high-quality standards