The fast pace of technological advancements has brought a heightened demand for reliable and efficient electrical insulating sleeving. Varflex, a leading manufacturer for OEM wire harness solutions, has risen to the challenge by offering custom solutions that cater to engineers’ specific needs. With the increasing complexity of electrical systems in various industries, engineers have continued to partner with Varflex for their ninety-nine years of expertise providing OEM wire harness solutions.
One of Varflex’s strengths is the ability to deliver custom products and solutions fast within tight schedules. Varflex offers flexible electrical insulating sleevings to designers struggling with dimension reduction and increase need for flexible wire harnesses. Varflex’s team of experts works closely with customers to understand their requirements and wire harness designs with the ability to customize colors, coatings and wall thicknesses. The result is a product that is not only high quality, but also meets the customer’s specific needs and demands.
Varflex’s solutions are critical in industries from medical, HVAC and lighting applications to the defense industry, automotive and electrical vehicles where precision and reliability are paramount. By offering custom wire harness solutions, Varflex provides the necessary infrastructure that supports technological advancements in various equipment.
Value Added Protection with PVC Coated Nylon
PVC Hi-Temp Coated Nylon is a highly specialized material that is designed to function in extreme environments. It is made from high temperature resistant PVC polymer with a high tenacity nylon core for added strength. PVC Hi-Temp Coated Nylon is ISO 9000 accredited. Varflex’s PVC Hi-Temp Coated Nylon is used to braid a protective cover over standard harness wiring systems that are particularly popular in the commercial, off-road, and emergency vehicle industries, as well as in outdoor goods and sporting equipment. It is also frequently used in marine, aerospace, space exploration, and military applications.
The use of PVC Hi-Temp Coated Nylon is important in harsh environments where high temperatures, chemicals, and other factors can cause damage to wiring systems. PVC Hi-Temp Coated Nylon is particularly well-suited for use in hydraulic lines and motors. This material is designed to withstand high temperatures, abrasions, and other forms of wear and tear. Additionally, it is resistant to water, oil, and other chemicals, which helps to protect the wiring systems it covers from corrosion and other forms of damage. One of the key benefits of Varflex’s PVC Hi-Temp Coated Nylon is its durability and ability to provide a protective barrier between high-pressure fluids and the operator or equipment itself, limiting risk of injury and damage to the equipment. The high durability can withstand extreme temperatures and pressures without degrading or breaking down over time.
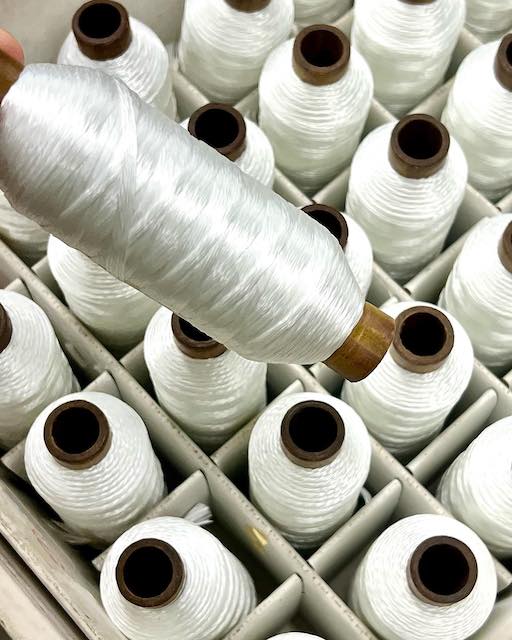
PVC Coated Nylon is a popular choice for hydraulic lines, motors and industries with prerequisites for a lightweight, flexible product resistant to abrasion and chemicals. Varflex’s PVC Coated Nylon is flame retardant meeting MVSS302, SAE J369, UL 94 and VO burn. The UV resistant coating passes UL 1581 and SAE J2527 requirements. It is an excellent choice for applications where durability and resilience are essential.
Another advantage of PVC Hi-Temp Coated Nylon is its flexibility. This material can be easily braided over wiring systems, which makes it easy to install and remove as needed. It is also available in a range of colors. The use of color-coding in electrical engineering is an essential practice to ensure safety and efficiency in the identification of wires and cables. Different colors signify different levels of voltage, which is crucial to prevent accidental electrocution or damage to electrical components. For instance, red, orange, and yellow indicated high voltage where blue cables indicate low voltage. Green and yellow stripes may appear on a wire to indicate that it is grounded. Additionally, black and white cables are often used for neutral wires and current-carrying wires, respectively. Color-coding not only helps engineers to identify cables, but it also aids in the maintenance and repair of electrical systems. Overall, the use of color-coding in electrical engineering is a simple yet effective practice that helps to maintain a safe and efficient electrical system.
PVC Hi-Temp Coated Nylon is an excellent choice for those in need of a reliable, high-quality material for use in wiring harness systems. Its high temperature resistance and strength make it ideal for use in extreme environments, and its protective cover can help to ensure the long-term reliability of a vehicle’s electrical system.
A Revolutionary Product Known as Viton® 231
The collaboration between engineers and Varflex has resulted in a powerful innovation that has revolutionized the world of motorcycles. Varglas Viton® 231 was specially designed to encapsulate alternator wires in motorcycles adding excellent protection against high temperatures, abrasion, fuels and oils. Varglas Viton® 231 is extremely durable and long lasting, making it a top choice in motorcycles, DC generators and motors to reduce arcing problems. Varglas Viton® 231 is particularly well-suited for application where a silicone-free environment is critical. Its excellent resistance to flames and abrasion make it an ideal choice for insulating leads and connections of critical electrical components, withstanding continuous operating temperatures as high as 220°C (428°F).
In addition to its use in motorcycles, Varglas Viton® 231 is widely used in transformers, electronic coils, motors, aircraft manufacturing and many other electrical apparatus applications, where resistance to high impingement velocity oils is required. Overall, the collaboration between engineers and Varflex has resulted in a highly effective and versatile material that continues to be an important innovation in the world of electrical engineering.
Customization Under the Hood
Varflex’s Varspan Expandable Sleeving is often used for wire protection and customization in and around motors. One of the main attractions to Varspan is the endless option of colors and patterns making it a popular choice for racing teams who want to add a touch of team colors and customization to their cars, snowmobiles or dirt bikes. Varspan is used to protect wires around the motor where temperatures are often cooler and subject to abrasion. The expandable design of Varspan sleeving makes it easy to install and remove, making it versatile to fit over wires, hoses and tubes of different sizes.
Engineered Defined, Varflex Implemented
For ninety-nine years, engineers have turned to Varflex to design and configure custom protection over wires and cables. Custom overbraiding is a technique that uses various design configurations with materials provided by either the customer or Varflex. This method is used to create a protective outer layer over wires, cables, hoses, tubes and other products. The overbraiding technique is commonly used in aerospace, space exploration, automotive and military industries where durability and protection are of the utmost importance.
Varflex offers a wide range of options when it comes to custom overbraiding. We work with a variety of materials such as Fiberglass, Wire Shielding, Nickle Plated Copper, Kevlar, Varspan and many other materials to create a protective layer that can withstand harsh environments. Varflex can also provide assistance with the design process to ensure the final product is both functional and aesthetically pleasing. Overall, custom overbraiding is an excellent and cost-effective choice for industries that require a protective layer over their products. With the help of Varflex, customers can create a braided layer that is both durable and functional.
Another 100 years of Varflex
The demand for reliable and efficient electrical insulating sleeving has never been higher. As a leading manufacturer for OEM wire harness solutions, Varflex continues to provide custom solutions that cater to engineers’ specific needs. Varflex’s products are well suited in many industries and applications from the defense sector, automotives and aircrafts to motors, alternators, transformers, HVAC, lighting and generators being just a few applications that utilize Varflex electrical insulating sleeving. Varflex offers a wide range of insulating sleeving solutions, including braided fiberglass, twisted and plied yarns as well as custom over braiding. The company’s commitment to providing custom solutions is evident in its ability to offer tailored products that fit the unique specifications of each project. Varflex’s electrical insulating sleeving solutions are designed to withstand high temperatures, resist abrasion and provide excellent electrical insulation, ensuring the safety and reliability of electrical systems and wire harnesses. With over ninety-nine years of experience in the industry, Varflex has established itself as a trusted manufacturer of high-quality OEM wire harness solutions. The company’s dedication to innovation and customer satisfaction has earned its reputation as a reliable partner for engineers seeking custom insulating sleeving solutions. By providing tailored products that meet the specific needs of each project, Varflex is helping engineers to achieve their goals and deliver high quality products to their customers in a timely manner.
Varflex Corporation was the first United States company to braid fiberglass and has manufactured electrical insulating sleeving since its founding in 1924. Along with electrical insulating sleeving, Varflex specializes in twisting and plying yarns including but not limited to Fiberglass, Kevlar, Spectra, Basalt, Polyester and other fibers. With almost 100 years of experience, Varflex offers a century worth of manufacturing knowledge and techniques across a wide range of industries from medical, lighting and HVAC equipment to aerospace, automotive, military and defense applications. www.varflex.com