The increased use of flat flexible cable (FFC) and flat printed cable (FPC) especially in EV battery production, has highlighted the need for automation in processing these materials. (for more information on FFC and FPC, see the companion article, Use of FFCs and FPCs in Electrical Systems in this issue).
One company that seems to be at the forefront in this endeavor is TE Connectivity (TE). TE has had an FFC bench-top machine for processing FFC, the Mark II semi-automatic machine, for crimping reel-fed terminals for some time. They recently released the next generation machine in FFC/FPC processing, the FFC/FPC semi auto termination machine. The new equipment represents a leap forward in technology with a greatly enhanced crimp monitoring system. TE’s Ying Yin (Sandy), Manager of Product Engineering for Application Tooling & eMobility Crimping, was kind enough to make herself available to Wiring Harness News to discuss the new machine and the enhanced crimp analysis it offers.
As Sandy indicated, the bench-top unit provided an excellent template for the new machine with its precision crimping for FFC and FPC. But TE had some customers in the automotive realm who required more automation and enhanced monitoring. “The new machine does a vision alignment before the crimp. Specifically, the machine will take a picture of the FPC/FFC to catch the 1st crimp position center line. It then moves the FFC/FPC to correct position before crimping. It performs crimp force and crimp height monitoring along with a visual inspection after each crimp.” Sandy advised. “The system takes a picture and determines where the crimp location should be. During the crimp there is crimp force monitoring, and after the crimp, the crimp height is measured.”
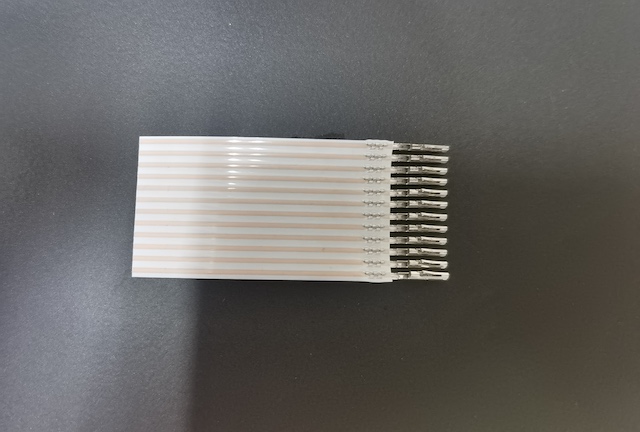
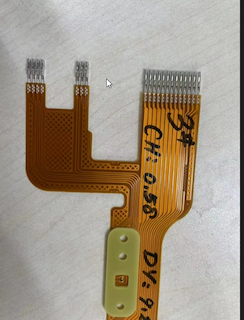
The machine can accommodate FPC foil up to 100 mm and can do three crimps per second. The new crimping process enables the position and posture of the terminal to be better controlled during the crimping process to avoid asymmetry. It also has a re-crimping function, so if a batch of foil is missing one crimp, the machine compensates and does a re-crimp on that terminal. This feature greatly reduces waste.
Sandy explained that operators can change out the tooling kit to accommodate different terminals. “It would take about 30 minutes. It’s not difficult, but the operator will need some training to understand which parts would need to be changed.” She added that most of their current case customers are using the machine for high-run applications, and really don’t have the need to change terminals often.
Asked about the challenges they encountered developing the tool, Sandy indicated there was a lot of experimentation with the optics to be able to perform the intricate monitoring steps.
Sandy thinks this is the opportune time to release the FFC/FPC Semi Auto machine. “We see a lot of applications in automotive, specifically for EV batteries. At the same time, we are seeing that there is a trend towards FFC/FPC cables as a replacement for traditional round cables in wire harnesses.” She indicated that efforts in weight savings also play a significant role in the FFC/FPC trend.
Beyond automotive, Sandy and her team see applications in commercial transportation, aerospace & defense, marine and data communications industries. She mentioned that TE will stay out front, expanding the FFC/FPC product line as market forecasts and industry trends develop.
For more information on the FFC/FPC product line, click go to www.TE.com.