GOING SMALL TO SEE BIG IMPROVEMENTS
As wire harnesses become more complex, advanced design and testing techniques are required to ensure their safety and reliability.
In the automotive industry, for example, modern vehicles require complex wiring harnesses able to handle high-speed data transmission, control multiple systems, and support various sensors and devices.
Similarly, in aerospace and defense industries, wire harnesses must be able to handle extreme temperatures, high vibration levels, and harsh environments while carrying critical data and power signals to different parts of the aircraft or spacecraft.
This increased complexity requires more wires, connectors, and components to be incorporated into the harnesses, making them more intricate and challenging to design, manufacture, and test.
A need for improved testing during wire harness manufacture
The increasing complexity of wire harnesses, combined with the critical role they play in modern electronic systems for vehicles both on land and in the sky requires more advanced testing methods to ensure their safety and reliability.
There is a significant need for better electrical testing techniques to ensure wire harnesses in modern electronic systems are safe and reliable. Improved electrical testing during wire harness manufacture can help prevent system failures, reduce maintenance costs, and improve overall product quality and safety.
Widening the testing bottleneck
We know that testing creates a bottleneck in the manufacturing process. Even with automated systems, testing can often be time-consuming and labor-intensive. The high variability of harness design and components can also make it difficult to standardize testing procedures and equipment. Increased complexity of harnesses can also be a factor, with multiple test types required. Management of the test equipment itself also contributes to the bottleneck, with cable management being an evergreen headache.
Harness shops can help to overcome these challenges by employing strategies such as automating test processes, standardizing testing procedures and equipment, and using modular testing systems that can be easily scaled up or down as needed. By reducing the time, labor, and complexity of testing, manufacturers can improve the throughput of the testing process and avoid bottlenecks in the manufacturing process.
How a modular system can help harness shops
MK Test System’s RTS system addresses several of these contributing factors to the testing bottleneck.
RTS stands for Real Time Scanning. It is a modular, high speed, rapid deployment automatic electrical test system. It takes the principle of high speed ‘pass/fail’ testing from the automotive sector but with vastly improved measurement accuracy for more complex harnesses.
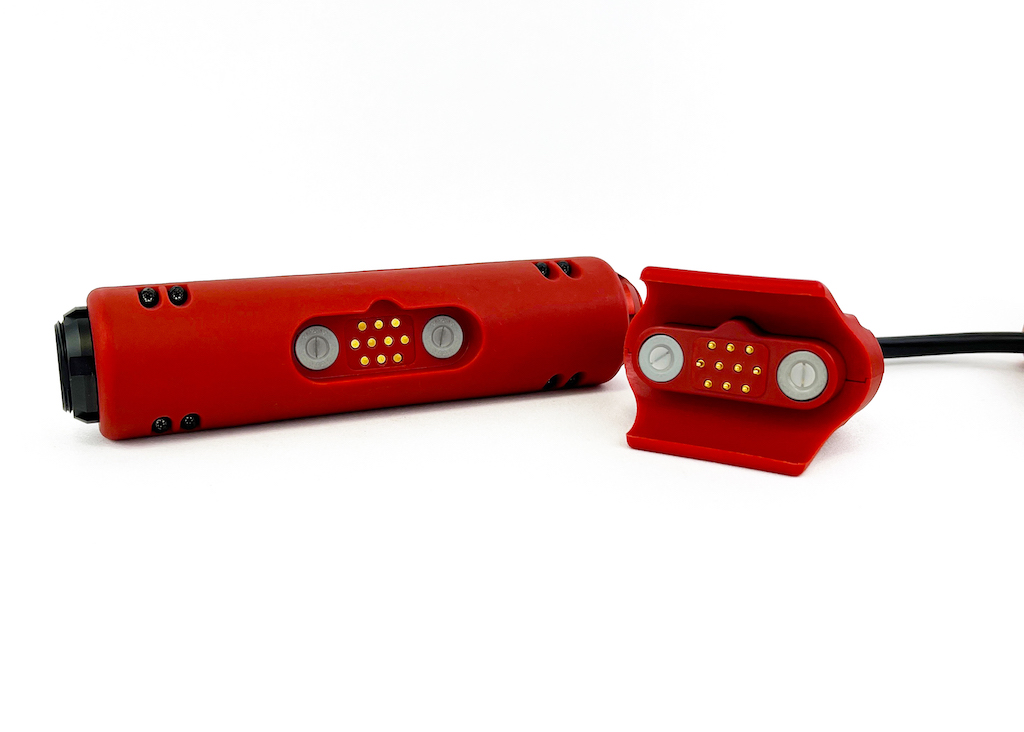
Benefits of RTS for wire harness manufacturers include:
- Reduced interface cables – The RTS system uses miniaturized components to take the test points directly to the harness under test using small umbilical cables, rather than requiring dozens of interface cables trailing back to the test system rack.
- Flexibility – A range of satellite modules are available from 32 test points up to 360 test points. This enables a customizable system which can be configured to suit the demands of a wide variety of wire harnesses and harness shop set-ups. More satellites can easily be added to expand the system.
- Faster hook-up – Hook-up is quicker with a modular solution compared to a traditional rack-based system. Uniquely to RTS (at the time of writing) are the magnetic connectors, which save even more time.
- Test during build – The other major time saver with RTS is that the low current and low voltage measurement signal means that system is safe to be running live, taking measurements during the harness build. This enables assemblers see in real time where the failure is and to fix it immediately, rather than waiting until the harness is built before carrying out a full test and reviewing the results before being able to fix faults.
- Random hook-up – the Active xRef feature enables random hook-up, identifying UUT test points no matter where on the system they’re connected.
- Operator aids – features to help operators include built-in guidance or instructions. RTS has several additional features to aid operators and harness assemblers. For example:
- All satellites have LED pass/fail indicators which provide instant visual results within seconds of hook-up.
- The probe feature is built in to every satellite, allowing easy access to a 4mm banana socket for fault location and diagnosis.
- For test engineers and programmers, Automatic Program Generation is included as standard.
- The RTS software also supports translation of alternative test programs to provide a smooth transition from existing test systems.
Harnessing the benefits of a modular test system
Whilst not an exhaustive list of benefits, this article should have demonstrated that a modular wire harness test system – such as RTS – can provide wire harness shops with a flexible, accurate, and efficient testing solution.
Modular test systems can undoubtedly help improve the quality and reliability of wire harnesses while reducing costs and improving productivity. For end customers, this will result in higher quality wire harnesses and improved customer satisfaction.
MK Test Systems will be demonstrating the RTS system and other automated test solutions at the 2023 EWPTE show in May. Come visit us at booth 620 for more information and a demo.
–END–
Notes:
- MK Test Systems was established in 1992 and are a world-leading manufacturer of automatic electrical testing systems.
- The systems are widely used within the aerospace, rail, defence, subsea, power & control industries worldwide to ensure high performance electrical systems are correctly wired and undamaged.
- With the main headquarters in Wellington, Somerset, the company has satellite offices in the US and Hong Kong, as well as a network of partners and distributors offering sales, service, and support around the world.