Paul Harvell, Product Director E3.series, Zuken USA Inc.
In today’s economic climate, with a scarcity of skilled workers, component shortages, and supply chain issues, design-to-manufacturing companies are looking at ways to improve their bottom line without sacrificing quality and throughput. For most design-to-manufacturing companies, multiple cultures exist to sell and deliver products. These islands have traditionally been isolated and rely upon manual methods of communication, often requiring data recreation or reentry. A reasonable next step toward improving the bottom line is to adopt a holistic approach, bridging and automating the business, design, and manufacturing islands.
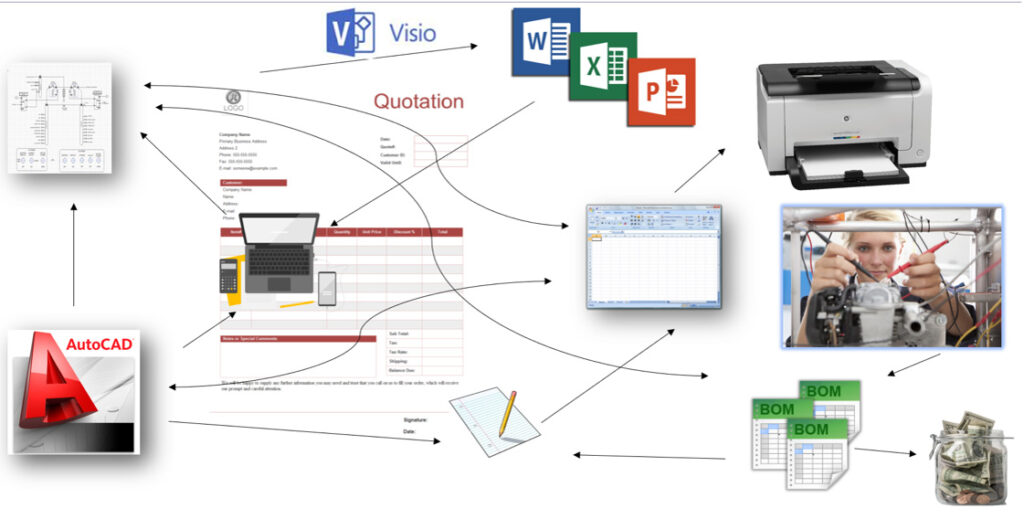
This article will explore some solutions and suggest a running thread that connects the operations of creating and manufacturing wire harnesses. As multiple new and exciting technologies exist, from the initial job estimation to the finished product delivery, companies have jumped on the automation bandwagon. These technologies are often islands without bridges.
The Automation Bandwagon
The entire world has been on the automation bandwagon for decades. Automation fuels our breakneck pace of development and is even responsible for the introduction of sliced bread! However, the goals of a company’s single automation project are usually not defined by considering the end-to-end business process and requirements. The reasons are quite understandable; engineering likely isn’t too concerned about the new quote generation system used by sales and accounting. Similarly, the sales team isn’t worried about the design tool used by engineering or the label machines used by manufacturing. The company must come together and exchange information at a more granular level to improve the overall process.
To tackle the automation projects and bridge the gaps in the automation bandwagon, we must answer a few questions and take a closer look at some popular automation initiatives:
- Are we getting the most out of our automation initiatives?
- Are there tools that have automation options already built in?
- Are we missing a trick or two?
- Quotation and initial order configuration initiative
- Automating using a PDM or ERP system
- Generating estimates from the design platform
- Standard design creation initiative
- Standardizing CAD tools or even Excel
- Removing bottlenecks from manual processes
- Reusing existing design data
- Quality control initiative
- Driving Harness testing and verification directly from captured design
- Improving consistency
- Next-gen manufacturing initiative
- Modularizing designs (pre-built kits)
- Automating Work instructions
- Improving cable/connector build with details such as labels, tooling, etc.
- Assembly process initiative
- Augmenting assembly aids
- Driving inventory and procurement
There is no one-size-fits-all answer. It differs based on the company’s current level of automation, focus, individual teams, and goals. Harness Builder for E3.series was developed specifically to address these automation initiatives.
The Quotation
Many smaller manufacturing companies will live or die on the accuracy of the initial quotation. Too expensive of an estimate could put off the customer/prospect, and too little may cost your company to produce the harness at a loss. It is imperative to pay attention to the following:
- Turn-around speed
- Accuracy of the Quotation
- Flagged for long lead time items
- Automated inventory check (In the stores/stock room or on the floor)
- Include Labor/Assembly time
- Consider Inspection Time
- Correct labor rate
- Include Testing time
- Factor in the cost of tooling
- Use an existing design/quotation to keep the same/similar number
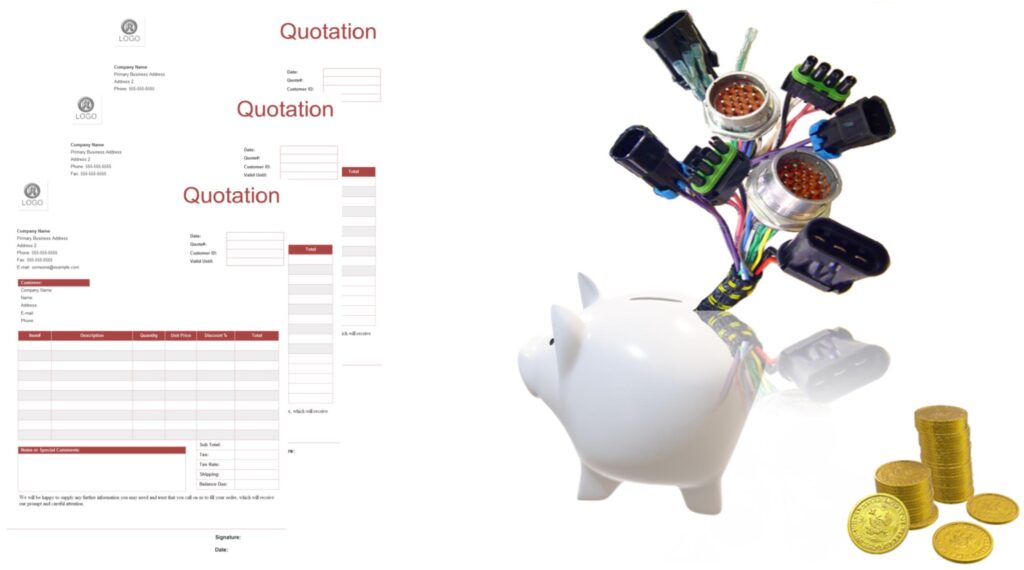
Figure 2: An accurate quote is like money in the bank
You can create this quotation within an ERP system. However, using an application that allows you to quickly generate a harness design for cost estimation would streamline the overall task and provide a more accurate quote. Adopting a multi-purpose process and using Harness Builder for E3.series Cost Estimator Figure 3) would accomplish this. For example, using Harness Builder for E3.series, you could:
- Import an Excel spreadsheet to/from list (Figure 4) into a Harness Builder project
- Import a CAD drawing of PDF file into the project to use as a template (Figure 5)
- Create harness design by overlaying on the template, placing parts from the parts-ready database offered in Zuken’s Harness Builder for E3.series, and routing the conductors
- Generate a materials list
- Run the Harness Builder for E3.series Cost Estimator
Using this simple process, a harness design is created with sufficient detail and accuracy for a cost estimate and becomes the starting point for the final harness design.
By using the parts-ready database, dependent part associations and additional parts, along with their cost parameters, are automatically included in the design. By generating a materials list, lengths and quantities are automatically calculated. Using the Cost Estimator, labor, material costs, and lead times are calculated and presented.
The Design Tool
After accepting the estimate, the same data is available to reuse for the detailed design. Harness Builder for E3.series offers even more automation to speed up and accurately detail the design:
- Automatically calculate the cable protection based on the design. This automation will search the database to find the applicable cable protection and place it directly on the design and include it in BOM. The automation can even be restricted to control a percentage fill.
- Creation of on-sheet BOM and Wiring List reports. The BOM is dynamically synched with the detailed Wiring List, so if a part or wire is added or changed, the reports will instantly update to reflect the change. The BOM will contain all design elements, including associated and additional parts required for the build.
- Online design rule checking will catch and prevent problems long before building the harness: incorrect wire placement in the wrong connector terminals, signal mismatching, and physical design impossibilities.
- Automatically generate helpful documentation showing splice information and wire colors while creating the design.
- Attach the harness revision so changes between new builds can give a delta list of what has been added and removed.
- The overall harness weight is known, so visual feedback helps with design restrictions and constraints.
- 1:1 Formboard prints for formboard overlay.
- Labeling exports directly to industry-leading labeling machines.
- A formboard co-pilot is available to ensure accurate length on long runs, folding the cable around fixings to fit on a single board.
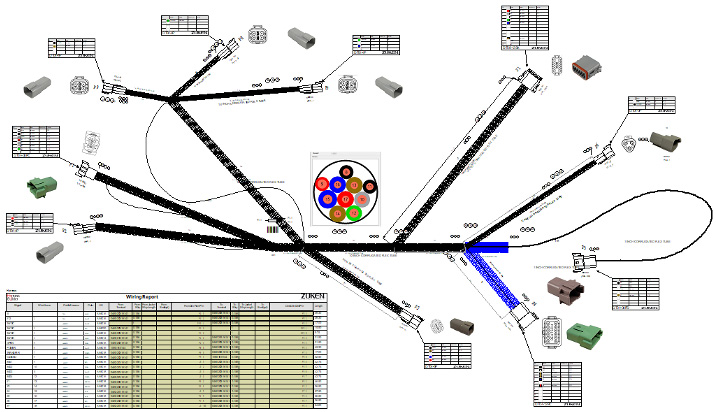
Figure 3: Harness Builder for E3.series harness drawing
Building the Formboard
Legacy processes might include printing from a CAD drawing onto large format paper and attaching it to a physical board. A technician would use this board to manually cut and route the wires through fixings and connect them to their respective termination components. These manual tasks often require some form of step-by-step instructions, likely also printed on paper and referred to as a Work Instruction package. Once completed, the board is stored for reuse, requiring a tremendous physical space in the building or manufacturing factory.
Harness Builder for E3.series can aid in creating Work Instructions directly from the original design in either printed form or displayed on a handheld tablet. Each instruction can be checked off once completed to monitor progress and the remaining effort to complete the build.
Augmented Work Instructions
To improve the process of building and assembling wire harnesses, Harness Builder for E3.series creates a new electronic formboard file (EFB). This file effectively bridges the work instructions with the manufacturing island. Industry-leading solutions such as HarnessWorks and Laselec consume the file and convert the data into mixed reality step-by-step work instructions projected or highlighted directly onto the formboard.
Export to Wire Machines
Another island to bridge is from the design directly into a cut, mark, and strip machine. Harness Builder for E3.series exports machine-readable formats, eliminating the need to take an existing drawing and program the machine manually. Harness Builder for E3.series supports multiple machine manufacturers and in some cases, multiple machine formats for a given manufacturer. These include Komax, Schleuniger, Artos, Spectrum Technologies, Laselec Modena, Z and F / Weidmuller, and Laserwire.
Wire Harness Test Machines
Test equipment requires programs to drive the machines, and these programs are often created manually. Harness Builder for E3.series generates the programs for many of the most commonly used test machines from within the application. It then exports the programs for loading directly into the associated machine. This bridge eliminates errors and effort often associated with manual program creation. Harness Builder for E3.series currently supports DIT-MCO, CAMI Research, Nexeya, Cirris, Cablescan, C.K. Technologies, and Dynalab test machines and consistently adds new test machine bridges with each release.
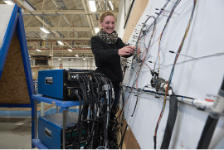
Figure 4: Technician Testing a Harness
ERP System Data Exchange
Using its robust controls, Harness Builder for E3.series enables direct data exchange between PDM, PLM, and ERP systems. For example, engineers can exchange BOMs and revision-specific wiring information between Harness Builder and the CETEC ERP system. The revision classification of the designs and builds is stored in the cloud for easy access throughout the company and makes this a powerful bridge to yet another island.
Summary
Harness Builder for E3.series provides a flexible workflow and robust capabilities to bridge islands of processes from quotation to final build:
- Capture requirements at the sales stage.
- Manage options and variations on existing harness builds or completely new designs.
- Connect the islands of quotation to final build using one data model throughout the system.
- Improve the bottom line without sacrificing quality or quantity.
- Track data through sales, design, and delivery gates while focusing on the accuracy and quality of the final product.
Visit the Zuken team EWPTE for a demonstration of this technology.
Author Bio:
Paul Harvell is the Product Director for E3.series, leading an application development team within Zuken USA. His team defines the Harness Builder for E3.series product along with other Zuken design automation solutions to connect engineering and manufacturing. Paul plays a pivotal role in refining the electrical design-to-manufacturing process to help customers successfully realize digital transformation.
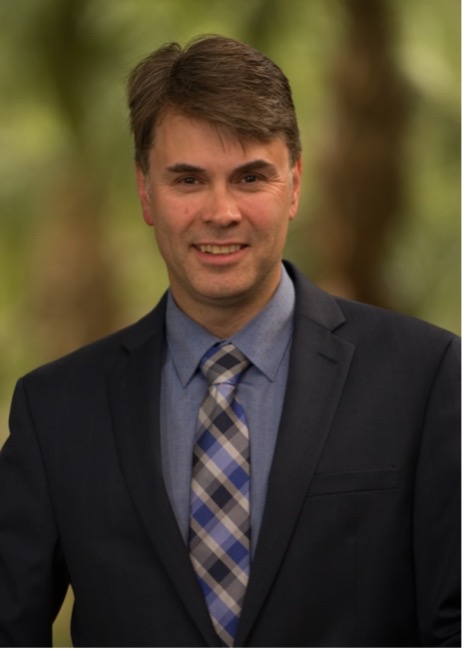
Paul Harvell, Product Director E3.series, Zuken USA Inc.
[A1]I have heard about waste reduction. Not sure if it could be added here.