I recently had the opportunity to sit down with Paavo Niskala, Vice President at TactoTek, to discuss In-Mold Structural Electronics (IMSE®) and its impact on the automotive industry and beyond. If you’re not familiar with IMSE, think of it as the next big leap in electronics manufacturing—integrating printed circuitry and electronic components directly into molded plastic structures. It’s a radical departure from traditional circuit boards and a game-changer for industries where weight, space, durability, and sustainability matter.
Paavo, who’s been with TactoTek since its early days, explained how the company spun out of VTT Technical Research Centre of Finland, where early experiments with printed electronics paved the way for what would eventually become IMSE technology. Originally, their work focused on infrared LEDs for touch sensors, but when prospective customers asked if they could do the same with visible LEDs, the company pivoted. That shift led them toward embedding entire electronic systems into molded plastic, and now, over a decade later, they hold nearly 300 patents in the space.
The advantage of IMSE, according to Paavo, is that it can be manufactured using existing equipment used in film insert molding—an already widespread process in industries like automotive, consumer electronics, and medical devices. It’s a process where a printed or decorated film is placed inside a mold before plastic is injected, allowing the design to become permanently embedded into the molded part. “Rather than building our own manufacturing capacity,” he said, “we chose to license the technology. It’s a scalable business model, and our investors see that scalability as key to our success.”
That licensing model is already proving its worth. TactoTek now has 26 licensees, most of them Tier 1 automotive suppliers, and the technology is beginning to find its way into mass-produced automotive components. “We’ve spent the last ten years working through the rigorous validation processes that the automotive industry demands,” Paavo told me. “And now we’re finally seeing real adoption.”
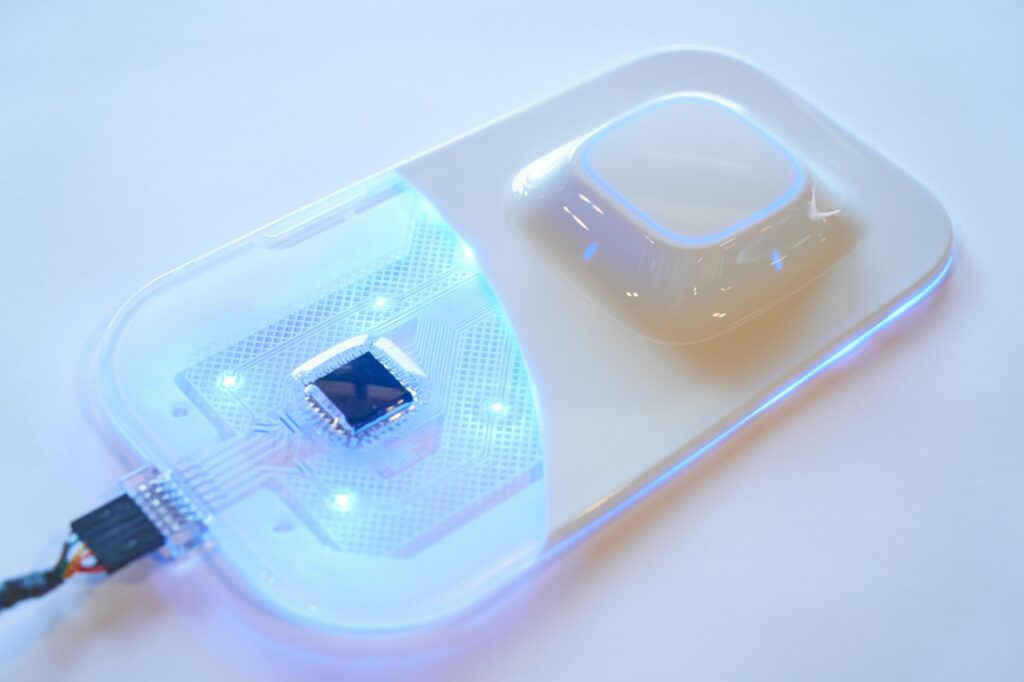
One of the biggest hurdles for IMSE’s acceptance has been proving its durability. Automotive applications require components to endure extreme conditions—temperature cycles from -40 to 105 degrees Celsius, rapid temperature changes, and mechanical stress. TactoTek’s IMSE technology has met these challenges, and the company is now focused on expanding into other industries. “Once something is validated for automotive,” Paavo noted, “it tends to spread elsewhere.”
We also talked about the core manufacturing process behind IMSE. The system starts typically with screen printing conductive traces onto a polymer substrate, a technique with roots in ancient China but now used in modern printed electronics. “The process is robust,” Paavo explained. “Once the traces are printed, we add surface-mounted electronic components using standard techniques—just like conventional circuit boards, but with adhesives instead of solder, because traditional reflow soldering temperatures would damage the plastic substrate.”
The next step is high-pressure thermoforming, a process widely used in plastics manufacturing. This step transforms the flat printed circuit into a three-dimensional shape. Unlike copper, which would crack under this kind of stress, the silver-based conductive traces in IMSE technology stretch and deform without breaking. After that, the formed substrate is overmolded with transparent resin, which serves both as a light guide and as a structural element, eliminating the need for separate housings and light guides.
Paavo showed me an example—a sleek, illuminated center console component (figure 1). “This,” he said, “used to be a complex electromechanical assembly made up of twenty separate parts—PCBs, light guides, screws, and other components. Now, it’s a single molded piece, with all electronics embedded inside.” The result? A 90% reduction in thickness, fewer assembly steps, and increased durability.
IMSE technology isn’t just about making things smaller and lighter. It also simplifies the supply chain. “Traditional electronic assemblies require you to ship multiple parts between suppliers before the final assembly,” Paavo said. “With IMSE, you manufacture everything in one step, reducing transportation and logistics costs.”
One of the most intriguing aspects of our conversation was IMSE’s potential beyond automotive. “Smart homes, consumer electronics, and even aviation could benefit from this technology,” Paavo said. “In aircraft, every gram matters, and our technology significantly reduces weight.” He shared an example from Finland’s national airline, which recently removed in-flight magazines to save weight. “If they’re making changes that small to improve efficiency, imagine the impact of reducing the weight of every electronic component.”
Paavo also highlighted the sustainability benefits of IMSE. “Because it’s an additive process, we only use the material we need,” he said. “Traditional PCB manufacturing involves etching away excess copper, which creates waste. With IMSE, we print only what’s necessary.” Lifecycle analyses have shown that IMSE components have a lower carbon footprint than conventional electronics, thanks to reduced material use and streamlined production processes.
Of course, I had to ask about end-of-life concerns—what happens when an IMSE component reaches the end of its use? Paavo acknowledged that this is still a challenge but one they’re actively working on. “Right now, the standard “recycling” process involves incineration of plastics into energy and recovering the metals such as silver,” he said. “But we’re collaborating with research centers to investigate novel recycling methods, so that both plastics and electronics can be efficiently recycled. Additionally, in Horizon Europe project UNICORN we are collaborating together with partners on developing materials to discriminate plastics and electronics prior recycling”
In addition to energy recovery, TactoTek is working on new recycling methods to further enhance sustainability. “We are investigating ways to break down the plastic components and repurpose them into new products rather than just incinerating them,” Paavo explained. “The goal is to create a circular lifecycle where IMSE components are not just disposed of, but truly reused in a meaningful way.”
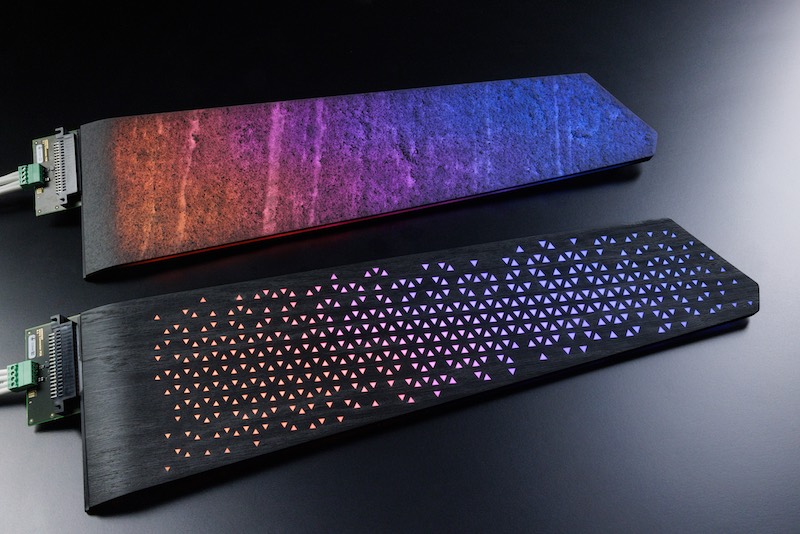
He also noted that IMSE technology’s integration into automotive manufacturing aligns with the sustainability goals of many major OEMs. “Automakers are under increasing pressure to meet strict environmental regulations,” he said. “Our technology helps reduce material waste, energy consumption, and even emissions associated with transportation and assembly.”
As our conversation wrapped up, we touched on how IMSE could change the way manufacturers and suppliers think about their businesses. “Right now, harness manufacturers see themselves as suppliers of wires,” I suggested. “But really, they should be thinking about themselves as manufacturers of systems that deliver power and signal—whether through wires or through something like IMSE.” Paavo expressed agreement. “Exactly,” he said. “This isn’t just about a new product; it’s about a shift in how we think about electronics integration.”
For now, automotive remains the key focus for TactoTek, but with IMSE proving its worth in that rigorous industry, it’s only a matter of time before it spreads to other sectors. Whether it’s in your next car, home appliance, or even the airplane seat in front of you, chances are you’ll be seeing more of this technology soon.