Creative Motorsport Solutions
Improving Quality of Testing Motor Racing Cables and Harnesses
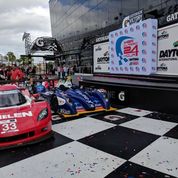
Founded in 2003, and located in Daytona Beach Florida, Creative Motorsport Solutions (CMS) has grown from being a data system re-seller to a company that now designs and builds its own complex embedded electronics systems for all types of racing vehicles in the motorsport market. CMS also offers services for wiring system design and manufacturing, and Wire Harness Testing. It is one of the few motorsport wiring houses in the US to utilize a CAD solution for wiring harness design. CMS customers include teams racing the Daytona 24 and Daytona 500.
Motorsport harneses are usually complex and mission-critical requiring the same level of quality of manufacturing as Aerospace parts. A few years ago, CMS set about finding a test system that would be accurate and flexible enough to handle the high mix, low volume testing. “At that time, we were looking to attach a “primary” connector to the tester with up to 79 pins and use the probe to identify correctness of the other pins. We did not want to build a mating interface for the many smaller connectors, but just have the system read out the name and pin number of the target”, explained Colin Harmer, Owner. “During our tester evaluation phase, we were drawn to the versatility of the CAMI Research CableEye® system, especially its invaluable AutoBuild™ guided assembly function which allows us to have a test lab that talks to us. When set up for 2nd-sided pinning, we probe each pin with the test probe, and the tester reads out the pin number while displaying the same information on the screen.
“The CableEye tester also allows us to rapidly identify the wiring of an unknown cable or harness using its Learn Cable function. This feature is especially useful when reverse engineering parts for customers who have lost their schematics (Fig. 2).
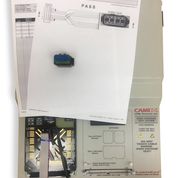
(Photo CMS)
“In this test (Fig. 3), the customer had an issue that pointed at the corner assemblies being “suspect”. These were not harnesses we built but because the CableEye test rig is so flexible we could quickly reverse engineer the harness, check it against the supplied drawings, perform a hipot test, and generate test reports showing the wiring in very little time.
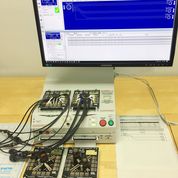
“In general, motorsport-type builds are typically low volume, which puts a premium on flexibility with fixtures and ease of use and is a true delineator of the CAMI testers. We now easily hipot test every product we produce which ensures that the client receives goods that are exactly to specification. By keeping records of all the tests, we can easily retest at a future point to ensure that there’s been no change in the harness, for example, in post-race, and post-crash diagnostics. We find it really easy to generate, store, and print all the test documentation we need within the CableEye system.
“Here’s an example of a device with switches (Fig. 4). This historic steering wheel was in need of repair. Using our CAMI CableEye hipot tester we can use the constant dwell option to function test each button before the wheel leaves the shop.
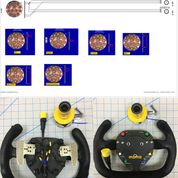
Front View (Bottom).
“Installing a CableEye test system has allowed CMS to test smartly and has contributed to our increase in productivity and growth. We purchased our CableEye tester December 2015, and moved a year later to larger premises to accommodate more efficient workspace and our continued growth. By mid-2016, we made the decision to hipot test everything before it goes out the door, and that’s now happening. There are no “off the shelf” test interface solutions for motorsport connectors, so these have to be made. We make ours in-house using blank CableEye test fixture boards from CAMI. Each board has a breakout of 64 test points. Boards are modular so you can mix and match to fit the harness you’re testing. We’ve built up a large library of these (Fig. 5) and are now often able to offer our services without need of creating further custom tooling.”
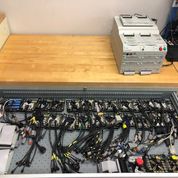
(Photo CMS)
CableEye testers have many benefits and can be used for the testing of all powertrain harnesses through prototyping and manufacture to post-crash diagnostics. These multiconductor testers easily link to custom test fixtures and harnesses and instantaneously check for faults, identify the type of faults, and pinpoint fault locations. Depending on the model, the testers detect and dynamically display continuity (opens, shorts, miswires, and intermittent defects), resistance, capacitance, diodes, dielectric breakdown, insulation resistance, and can check twisted pairs for correct orientation. Hipot tests (e.g. insulation resistance and dielectric breakdown) are necessary steps in qualifying insulation integrity. Testing for intermittent defects pre-screens the harnesses for the kinds of faults that can be stimulated by vibration.
As mentioned previously by Colin Harmer, motorsport harnesses are usually low-volume and often bespoke, and so require a tester with a high degree of flexibility to deal with unique test settings, connector types and combinations. Since these testers log the data, post-race and post-crash comparisons of harness integrities are a cinch. The former ensures there have been no changes giving the go-ahead for reinstallation, and the latter can be used for crash diagnostics and the results fed back for potential design improvement. These automation-ready testers provide for barcode tracking and detailed, wire-by-wire, colored wiring reports – even for hipot tests.