Choosing the right heat shrink for terminals can be challenging, as no singular type of heat shrink tubing will work for all terminal applications. With a limitless combination of application requirements combined with a wide selection of terminal designs of varying complexities, many factors must be considered in each scenario; these factors include: the geometry of the application, viscosity of the heat shrink adhesive, operating temperature, shrink ratio, application equipment, and more. This article will review at a high level DSG-Canusa’s recommendations for selecting the right heat shrink tubing for your terminal applications.
Adhesive Viscosity:
Adhesive flow must be controlled so that the adhesive does not overflow into a prohibited area of the application, such as a terminal eyelet. Adhesive bond strength must also be controlled so that the adhesion is strong enough for the application.
Low viscosity adhesives with high flowrates are suited for more complex geometries, due to its ability to flow into and seal locations where other adhesives may not be able to reach. These are commonly used for splices and easy claw cable lugs due to the prohibited areas of these applications being located a substantial distance away from the heat shrink installation.
Medium viscosity, medium-flow adhesives are suited for complex geometries where overflow needs to be limited. Medium viscosity adhesives can generally be selected for flat terminals connected to large cross-sections or terminals with semi-complex geometries and eyelets that are located near the splice area.
High viscosity, low-flow adhesives are recommended for applications requiring strong adhesion on smooth, even surfaces. High viscosity adhesives can be used for tubular cable lug applications.
Size Selection and Shrink Ratio:
Selecting the correct size and shrink-ratio is critical in designing a well-sealed product. When selecting the size of heat shrink for complex geometries, there are generally two dimensions on the application area where the heat shrink will be installed that are critical: the largest effective diameter and smallest effective diameter. For the highest effective diameter, it is important that the heat shrink jacket shrinks a bare minimum, so that the jacket compresses and creates a seal. Likewise for the smallest effective diameter, it is important that the jacket does not shrink too little resulting in a lack of compression and hurting the seal of the application.
The following formulations can be used as guidelines for heat shrink sizing selection:
(Heat Shrink Non-Recovered ID – Recovered ID) * 20% + Recovered ID > Application’s Smallest Effective Diameter
(Heat Shrink Non-Recovered ID – Recovered ID) * 80% + Recovered ID < Application’s Largest Effective Diameter
Product Recommendations:
Below is a reference list of the properties mentioned above for some of the most popular DSG-Canusa adhesive-lined heat shrink tubing products used in terminal applications:
Product | Adhesive Viscosity | Shrink Ratio | Operating Temperature |
DERAY®-Splicemelt | Low | 4:1 | -40°C to 125°C |
DERAY®-RKS | Medium | 3:1 | -40°C to 125°C |
DERAY®-ACT | Medium | 3:1 to 5:1 | -40°C to 125°C |
CPA-300 | High | 3:1 | -55°C to 125°C |
DERAY®-T-Melt 150 | Low | 4:1 | -40°C to 150°C |
DERAY®-UMS | Low | 4:1 | -40°C to 125°C |
DERAY®-IXKT | High | 4:1 | -40°C to 125°C |
Application Equipment:
To achieve consistent results for a challenging application, it is recommended to use dedicated application equipment. DSG-Canusa offers a variety of application equipment designed in-house to consistently deliver quality heat shrink tubing installations onto terminals in bulk quantities.
This section will cover general processing procedure at a high level for tubular cable lugs using the DERAY®-Shuttle 2.0. There are many factors and parameters that must be considered when designing the application protocol, including shrink temperature, shrink time, air flow during shrinkage, core temperature of the splice and terminal underneath the heat shrink tube during installation, adhesive flow behavior, and more. All of these must be considered on a case-by-case basis.
The terminal splice must be properly welded and be free of sharp edges to prevent puncturing of the heat shrink jacket and ensure the heat shrink adhesive can flow properly. In the example below of a tubular cable lug installation, the heat shrink tube should be positioned as shown in the photo, if possible, with a minimum of 1.5 mm of the tubing extending past the splice area onto the terminal lug and a minimum of 15mm extending past the splice area onto the wire insulation.
During shrinkage it is important to observe that the final product shows minimal air bubbles under the heat shrink jacket, a persistent sealing section around terminal lug, and a minimal liftoff of the heat shrink jacket. The DERAY®-Shuttle 2.0 has an approximate max shrinking temperature of up to 600 °C. This device can be pre-programmed with shrinking parameters for specific applications and utilizes trays which can hold multiple terminals for simultaneous and consistent heat shrink installation.
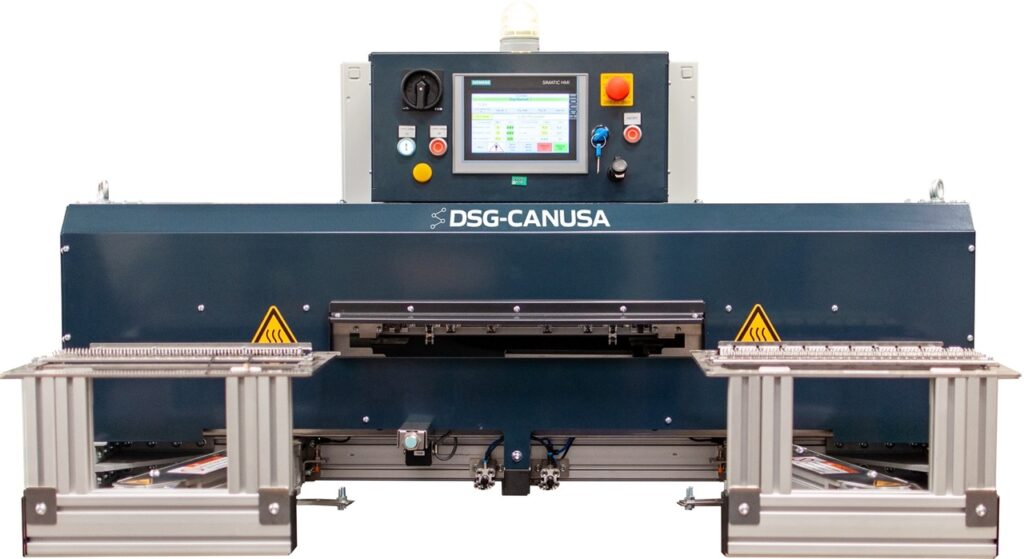
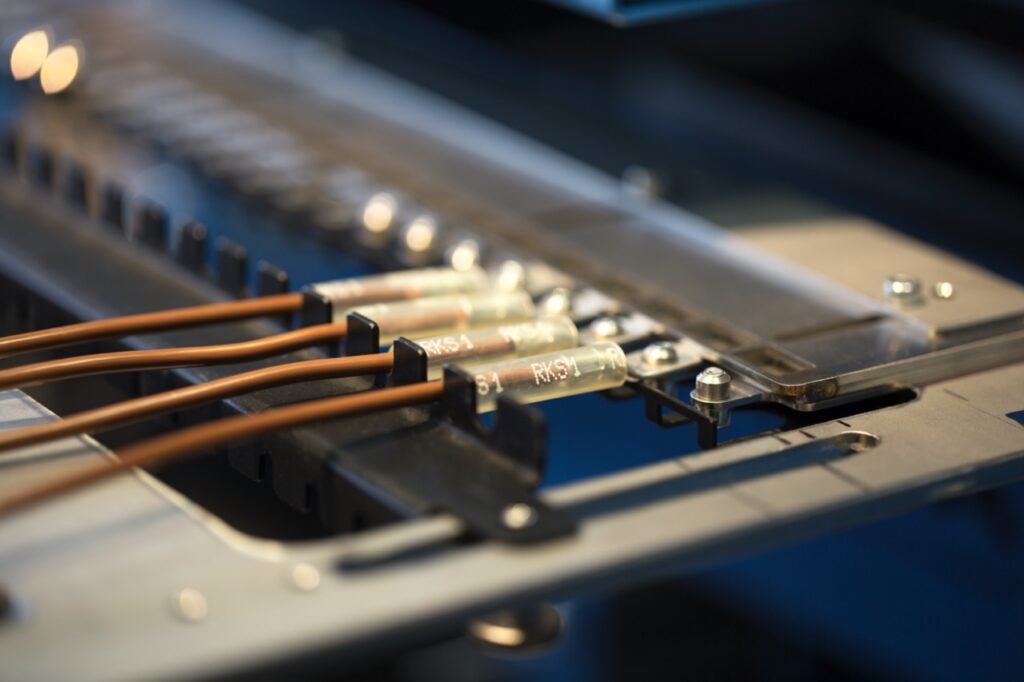
DSG-Canusa also offers Quality Assurance equipment to ensure a proper seal has been created around the application. The DERAY®-VaDi 2.0 vacuum-leakage tester is suited for applications that use thicker wire cross sections between 10 mm² and 80 mm². The VaDi 2.0 operates by creating a vacuum underneath the jacket of the cable and measuring for air pressure irregularities that would indicate air sourced from an insufficient seal. The VaDi 2.0 is capable of testing up to 5 samples at a time in a dry environment so that the terminals can then immediately be used in the next stage of the manufacturing process.
Conclusion: These guidelines serve as a general tool for selecting the correct heat shrink for your terminal applications. DSG-Canusa specializes in collaborating with manufacturers to select the best heat shrink tubing for an application and testing the solution to ensure consistent desired results. Should you encounter challenges with your current terminal applications or have any other heat shrink related questions, please do not hesitate to reach out to our team to discuss any of your heat shrink nee