The eMobility sector is creating many opportunities for the harness industry. OEMs rely heavily on contract manufacturers to guide them in choosing wire with the proper performance capabilities. Increasingly, this includes not only an understanding of wire and cable conductors, but also knowledge of the polymers that surround and mate to them. These can be connectors, grommets, strain reliefs or anything that makes up the completed assembly. This article deals with materials used in eMobility, and more specifically, charging cables and BASF’s Elastollanâ TPU material.
WHN spoke with Christopher Bradlee, Market Segment Manager at BASF about how their Elastollan brand of thermoplastic elastomers (TPUs) is meeting the challenges of the eMobility sector. Elastollan is a premium jacketing material engineered through years of experience. It offers superior flame retardant properties while still having a physical performance of a TPU.
This TPU has a wide range of uses across many markets and products. Its properties are particularly useful in eMobility, and more specifically charging stations. “A big part of the global requirement for charging cable outer jacket material is low conductivity,” Chris mentioned. “You’ve got high voltage running through these cables, so you don’t want them to conduct electricity.” Another crucial requirement met by Elastollan for EV charging cables is hydrolysis resistance. As these cables are subjected to prolonged exposure to the elements, it’s crucial that the chemical bonds in the material do not break down with water over time.
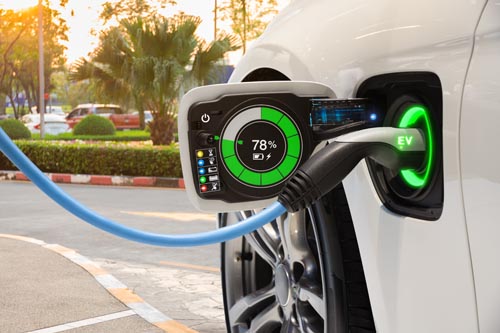
Charging station cables must also have good abrasion properties, along with good temperature flexibility. “These materials have to be resistant to cold, heat, sun and rain, but they must also have good abrasion resistance. They are dragged along the ground continuously and would easily wear if they didn’t have good abrasion toughness,” Chris informed. Excellent resistance to tears, cuts, oil and grease along with good tensile properties are also charging station cable essentials. Elastollan has all of these bases covered. He also mentioned that the material meets the challenge of coiling as well. It holds the coil and does not harden or break along the bend radii.
It’s also important that these jacketing materials do not bloom. “Blooming is when the functional additives inside the product bloom, or come up to the surface,” Chris explained. “Polymers often times have additives that enhance their processability, impact resistance or other performance benchmarks. But it doesn’t do you any good if your UV resistance additive blooms to the surface over time.”
Chris was then asked about any challenges with sealing Elastollan. “It really depends on the compatibility of the polymers, but overall, it seals quite well. TPUs generally have good compatibility with many polymers, but poor compatibility with a polyester, so if you’re putting a TPU and polyester together, you may need an adhesive,” he clarified.
Elastollan TPU does have good compatibility with most overmold materials. “These materials are generally TPUs or other elastomers, and their improved adhesion to Elastollan is due to its low filler content. High filler content can greatly affect adhesion,” he revealed. “This is one of the big value propositions of Elastollan, that it has good grommet adhesion.”
As far as processability, Chris mentioned that Elastollan TPU is pretty standard. It’s similar to other materials that harness manufacturers would be using, with no special handling or stripping requirements. One thing it does have is excellent colorability, with a wide spectrum of colors available. This can be very important to OEMs when they design cables. Another important aspect about the material is that it is globally available.
As you may have surmised, BASF does not actually make the cables. They supply bags of pellets to the cable manufacturers who extrude the material over various conductors to make different types of wire and cable. But sourcing cable with Elastollan is pretty simple. “They can contact me, and I will point them to a supplier,” Chris suggested. In fact, with any questions regarding the suitability of a cable to an application, Chris encouraged reaching out to him. “We have a whole team of experts who know the standards for charging cables and connectors, and we also have a whole product regulatory support group who know the regulations globally.” He stressed that regulations vary from country to country. These regulations extend to things like cable specifications and to important restrictions that may also exist. “Not only do we have the product development experts who know the chemistries and how to develop solutions, but we also have the regulatory and stewardship experts who can help navigate product development.”
Chris wanted to stress the fact that BASF covers a wide range of offerings to the wire harness industry. “We already covered the cable jacket material, but readers should know we have the Engineering Plastics group who do all the fire resistant PBTs for the connector industry.” Fire resistant PBTs are an emerging trend within the wire harness industry, and BASF has the same level of product and regulatory experts to handle PBTs that they do with the TPUs. Both materials can be used to produce high-strength cable management components like wire ties, holders and mountings.
In closing the discussion, Chris wanted to mention that BASF is a leading expert in sustainability. “I think as your readers go forward and learn more about us, they’ll see that we put a tremendous amount of effort into recycling, circular economy, and bio-based materials. I like to say that we create chemistry for a sustainable future at every level.”
You can contact Chris at +1 (734) 512-3527, or at [email protected]. Jump on the BASF website at wireandcable.basf.us for a plethora of information useful to our industry.
Special thanks to Patti Presswood, MARCOM at BASF, for organizing the interview and keeping us on track.
*