Which is better for wire harness manufacturing on flexible cable: The hexagonal crimp or B-crimp? Tom Grant and Gary Conn, OEM Sales Managers for Ask Power get asked this question routinely by wire harness manufacturers dealing with the challenges of flexible cable wiring systems.
Faced with customer concerns about vibration, greater ampacity, temperature ratings, and heat exposure, wire harness manufacturers are constantly seeking additional information that can help them adjust to these greater demands.
What happens in a crimped connection and rigid cable case:
In a crimped connection, Electricity travels from strand to strand and creates a charge path from cable to terminal. Each transfer from one strand to another contributes to overall electrical resistance.
In the case of a rigid cable, there are a limited number of large strands. After crimping, as the number of strands to cross is limited, poor contact between strands only has a limited effect on the overall contact resistance. Consequently, a hexagonal shape is widely used and suited for such applications, with a limited risk of overheating.
Most applications require the use of flexible cable:
The higher technology found in hybrid and electrical vehicles, railway, aerospace, and most of the modern OEM designs requires flexible cable to be able to accomplish. Flexible cables offer a small bending radius and are easy to bend which makes them the first choice for application in narrow spaces.
Most wire harness manufacturers for automotive, aircraft, and train are used to using a flexible cable, but it is difficult to work with because the strands expand after stripping and can occupy more space than rigid cables. Insertion of flexible cable can typically lead to using a larger barrel and associated larger crimping tool. Such a combination can lead to poor strand contact in the connection and the presence of many voids between strands.

Figure 1: hexagonal crimp on rigid versus flexible cable
Hexagonal crimping dies used on rigid and flexible cables are compared in Figure 1. Poor contact between strands leads to high crimping resistance and risk of temperature elevation.
Performance requirement of a good, crimped connection:
Typical tests to qualify a connection include a current cycling test where the current is applied to force the cable temperature to 120 degrees centigrade. The temperature on the terminal must always remain below cable temperature to ensure the connection is not the limiting point of the current path.
Examples of industrial standards specifying means for qualifying a connection include UL486A/B; ANSI 119.4; and IEC 61238-1-3.
To ensure such a requirement, crimping quality is essential. In the example of Figure 1 above, experiments in the lab they demonstrated that when cable temperature is set to 120°C, hexagonal crimp leads to a temperature of 110 degrees in combination with rigid cable versus 170 degrees centigrade in combination with flexible cable.
Hexagonal crimps lead to poor performance with flexible cable and risk of overheating. Behind the high temperature exhibited when a high current is applied, such a combination also leads to poor aging performance. Tin-coated connection exposed to temperatures over 150 degrees centigrade age fast and leads to the creation of intermetallic alloy (Cu/Sn combination). Intermetallic alloys are highly resistive materials and limit current flow, leading to potential installation failure.
Compaction ratio analysis and performance optimization.
Only good crimping will ensure the temperature on lugs remains below critical temperature. During the crimping process, the cable is compacted and will reduce in section. The compaction ratio (in%) is used as a development metric.
Crimping analysis equipment including sawing, molding, and polishing machines is used in the laboratory to analyze the inherent compaction ratio and to determine the overall compression effectiveness of the crimping process.
B Crimp for flexible cable:
The B crimp is preferred over the hexagonal crimp when working with flexible cable. The B crimp is developed to optimize the contact between strands, leading to a low crimping resistance, and a lower temperature elevation. It is a preferred solution for most OEM wire harness applications using a flexible cable.
B-crimp thermal performance on flexible cable: Hexagonal crimps perform very well on rigid cable as the smaller number of contacts are making solid connectivity within the terminal. However, with flexible cable, the hexagonal crimp has lower connectivity, and the temperature of the terminal is elevated above the cable.
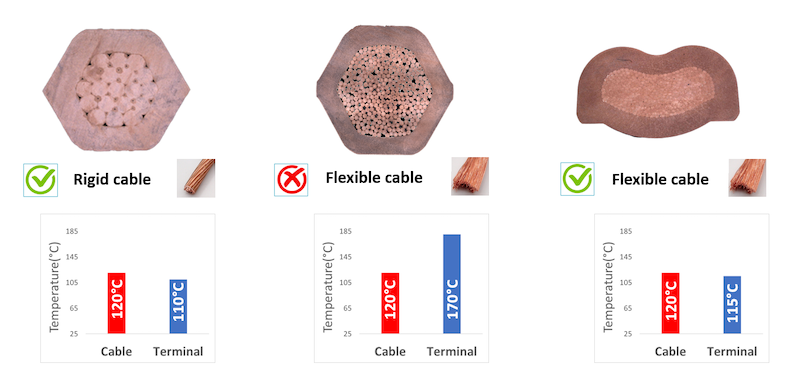
The B crimp provides lower temperatures for the terminal and offers optimal performance with flexible cable.
Qualification of electrical connection: Optimized crimp is verified by lab testing including electrical performance testing (crimping resistance and ampacity), mechanical performance testing (traction and vibration testing), aging tests (Thermal chocks, current cycling, and salt mist test), and thermal performance tests (Derating and overloading).
Summary: In today’s modern technology including electric vehicles, railway, aerospace, and many OEM applications, most of the wire harnesses are produced with flexible wire. In addition, a lot of wire harness requirements need to produce less temperature and handle vibrations.
Eric Gery, Head of OEM Project Management and Technologies says “MTR, works to deliver a laboratory-tested crimping solution that can handle the unique pressures of today’s challenging new technologies. We believe the B-crimp makes the most sense for flexible cable.”
Ask Power and Mecatraction will help anyone facing crimping difficulties and share our experience, expertise, and testing laboratories to help you find the exact method for your needs. Let us know what we can do to help.
History of ASK Power: In 1986, Steve Kase purchased a company that had been in operation since the end of World War II. The company, which is now called Ask Power, was previously involved in the production of lighting components and connectors for military vehicles.
In 2016, the SICAME Group made a significant move by acquiring ASK Power. Founded in 1955 by Basile Lachaud in Pompadour France, SICAME grew internally and through acquisitions that gradually gave it an international dimension. The Group is composed of more than 50 companies, and this international organization is in 24 countries and selling products in 170 countries with more than 3600 employees.
The SICAME Group is a recognized worldwide leader specializing in products and services linked to the transport and distribution of electricity as well as systems, safety equipment, and associated tools. The Group’s products and markets are focused on several fields of activity: energy transmission networks, overhead distribution networks, Renewables, Electro-mobility, Commercial and industrial, Services and OEM.
SICAME North America and Ask Power are in Naperville, Illinois. ASK Power specializes in designing, developing, and manufacturing complete lines of terminal junction sleeves and grounding solutions for power grids, renewable energies, telecommunications, military, marine, and utilities. Sicame Group has further expanded its North American presence by acquiring Kortick Manufacturing in Pittsburg, California in 2020, Hydel Incorporated in Vaughan, Ontario, and Power Line Sentry in Wellington, Colorado in 2023.
SICAME Group has US-based Ask Power and MTR located in France to handle the metric-type connectors used by wire harness manufacturers. MTR designs develop and produce a complete range of components for industrial electrical connections. Sicame adds an extensive range of crimping tools and accessories.
Ask Power and MTR have combined resources to bring expertise to the wire harness manufacturing companies based on their long experience and innovative technology-driven performance.