Doom and gloom predictions for wiring harness suppliers about the shattering of the market by a trend to design vehicles more predominantly featuring software-delivered functionality are over-dramatic. But the trend is real, it does have consequences for harness manufacturing and companies should plan and prepare for the future as it will have impact.
SDV Basics
Don’t be confused; descriptions of what constitutes a Software Defined Vehicle are many and varied. Diverse ways of explaining a vehicle defined by its software are influenced by the role or interests of the person or group representing a company. These stakeholders are usually seeking to provide goods or services into a very competitive market, just like you do, in the middle of a highly active business trend, in a complex technical field.
And just like a baker may address every challenge they face like the problem of how to bake the perfect loaf – a vendor of an AutoSAR software stack or a vendor of over-the-air software update infrastructure for example, will stress the importance of solving the issues their offerings address. Expect their descriptions to advocate for specific standards and extol their services for customizing and integrating the software on board the vehicle.
The totality of software and services players for SDV are in what is referred to frequently as an “ecosystem” of suppliers. Well, a jungle is an ecosystem, impenetrable and hostile to human beings unprepared for it. Some arcane definitions of SDV are off-putting and skewed towards the detail of technical realization of software components for vehicles. That can be hard to decode even for someone who has worked in software business for more than 30 years.
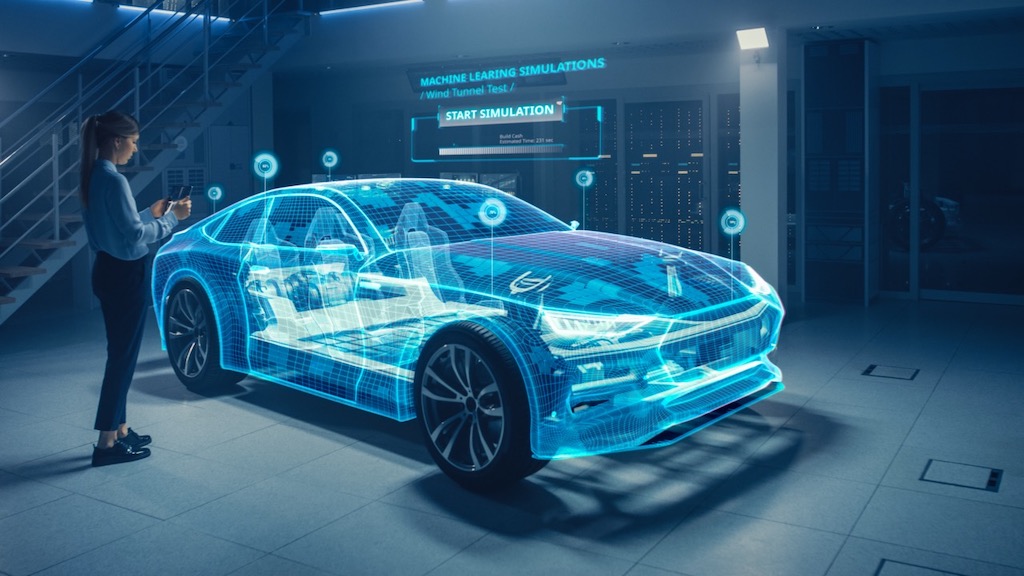
Figure 1: An example of SDV iconography – apparently the future is very likely blueish with glowing usually white aspects.
But fear not, because wiring harness suppliers are not going to compete for business producing software. However, they are down-wind, and will be living with the consequences of this shift in the way vehicles are designed.
Commonsense definition
A simple working definition of SDV should focus on what characterizes a vehicle and what imbues it with the personality the vehicle has. What defines it (“D” in SDV). In some of the present and upcoming vehicles being designed, OEMs will deliver the features and behaviors their customers want via increased deployment of software. Where previously electronics, and earlier electrical/mechanical or simply mechanical features were present, software is now substantially replacing it. Features in the vehicle get enabled and are governed because of software components. Circuit breaking accomplished by software rather than mechanical means (so-called “smart fusing”) is a good example.
Software components in vehicles vary in type. Often vehicle OEMs refer to different layers or levels of software. From operating systems to applications with user interfaces, some layers would be recognizable to almost everyone who has owned/operated a computer or a smart phone. However this analogy doesn’t fit perfectly once you realize extra critical software components in vehicles are not present in a phone or PC. Specialized software in vehicles is needed for example to meet rigorous safety and security standards mandated by regulators, and for particular fault diagnostic and monitoring purposes. More layers of software interacting with each other. More complexity.
The increasing importance, the primacy, and the sheer volume of software in vehicles means OEMs have to not just emulate, they must be actual software producers themselves. In addition, they must manage external suppliers of software which goes into their product too. It is very difficult to go it alone and produce every piece of software in a vehicle.
In short, to qualify as a software defined vehicle substantial you would expect delivery of major functions through software compared to the previous generation. Think of the essence, the characteristics of a vehicle as you get to use it becomes familiar to you. In an SDV that machine ‘personality’ is a product mostly of software.
Better product quality at lower cost for vehicle makers.
Quality and cost are top level goals/consequences of adopting methodologies of Software Defined Vehicles (SDV) and are familiar ones for vehicle OEMs.
Design engineers are tasked to develop electronic and electrical architectures for next generation products which are scalable, flexible and deliver customers’ desired functional richness. This is a common goal irrespective of what the propulsion system is – gas, battery, or hydrogen or hybrid. Agricultural machines and mining equipment, as much if not more than trucks, buses and cars, have been moving in the direction of software-based delivery of functions for more than a decade. Fly-by-wire has been ‘fly by software’ for ages for many years, so SDV although a new acronym to automotive engineers is recognizable as containing old concepts.
Wiring content reduction is, in effect, a benefit of architectural design using fewer electronic control units (ECUs) and centralized computing. Fewer nodes to route to – like fewer stops on a delivery route – means less distance travelled. Increased availability of technology for high-speed networks means signals from sensors are carried in fewer and smaller wires. Material and part number reductions can promise over-delivery to companies’ cost and sustainability goals.
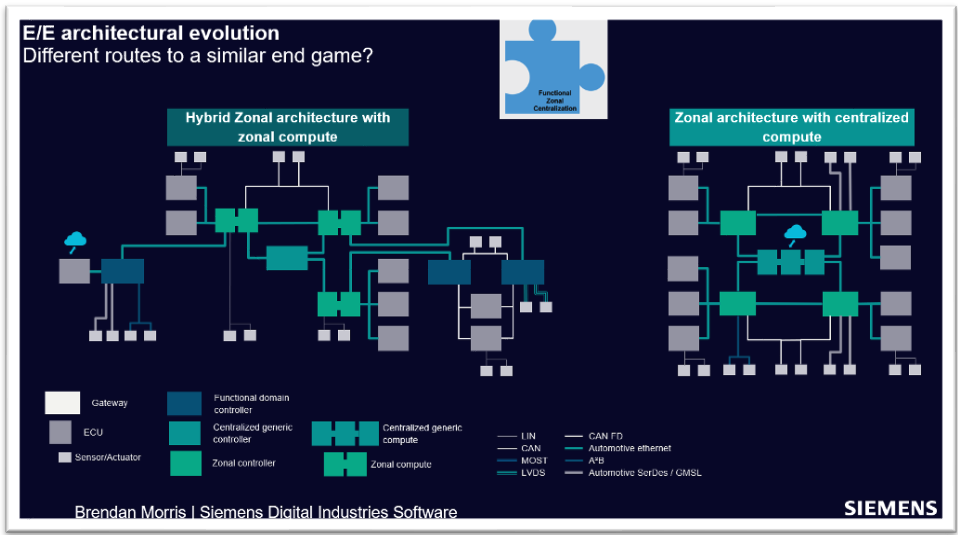
Figure 2: Aspirational and now reality – reduced electronic control unit numbers in vehicle architectures.
Wiring reduced by how much? Publicized and private studies 2019/20 in Europe and the USA found the potential of E/E architectures linked to the shift to SDV would vastly reduce wiring content. An in-theory reduction of around 50% of wiring was described for long-established car companies in research into E/E architectures. Tesla has made public pronouncements for the last seven years about imminent massive reduction in wire harness content in their upcoming designs. In the 2023 Cybertruck via a 48V system and using flat-flexible cable (FFC) routing and automotive ethernet cabling, many of these promises eventually came true.
But what about the “traditional” car companies who have not gone to 48 volt systems or other Tesla techniques? There have been some OEMs who have implemented zonal controllers, centralized computing and high-speed networks architectures in their vehicles adopting the principles of those pilot studies 5/6 years ago. They are experiencing in contemporary production vehicles around 15% less wire harness material. That is a large, practical and beneficial gain for them.
OEMs love the potential of SDV for another very seductive reason
SDV Architectures save development costs and even more in the piece cost of manufactured harnesses. However, there is apparently an even more compelling reason to go down this route if you want to be profitable making and selling vehicles. It is the motivation to exploit and enable digital services.
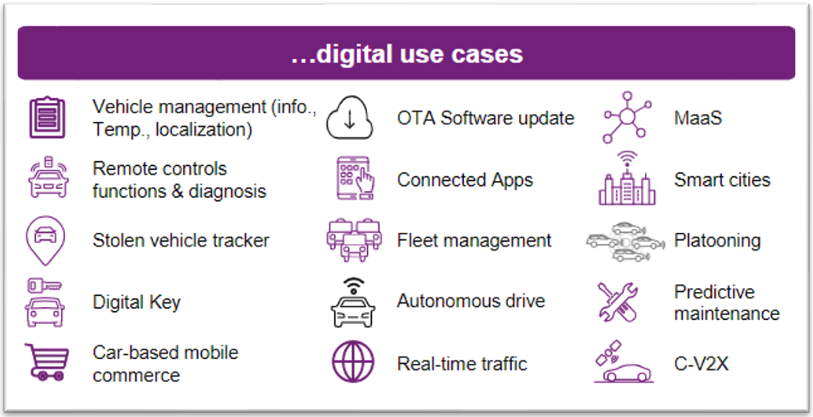
Figure 3: Example categories of vehicle digital services (Siemens DISW)
The market opportunities and attendant revenue streams are forecast to be massive. If your vehicle packed with software functionality, is updated over the air (OTA), then it could perform better older than new! Moreover, if the vehicle should “talk” to other vehicles, communicate with traffic lights, tollway systems, insurance companies and so on, offering an infinitely personalized experience tailored to the individual user is close. OEMs are betting huge sums of money in setting up ways to monetize this through subscription payments.
Recurring transactions for digital services are lucrative. The OEM makes a certain amount of money from selling a new car. If the owner pays the OEM about $20 a month for software and keeps the vehicle for 8 years – that’s another $2,000-ish in total. If one of only 10,000 customers riding that payment conveyor belt for 8 years, then the revenue to the vehicle maker is an extra $20 million. That’s new money – the kind shareholders like best.
Digital services revenue predictions describe a rapid expansion in this way of paying for transportation. It is so startling that a “fear of missing out” exists. Not following the trend looks risky to many vehicle makers. Executives respond to competitors moving to these emergent revenue streams with big counterinvestment moves. It’s in the billions of dollars.
Production efficiencies for designing electrical distributions system [EDS] and harness piece cost savings are worthwhile benefits of SDV. However, it is these potentially massive new revenue streams from digital services that are turbo-charging the trend. If you don’t have a software defined vehicle you can’t claim the value and secure these revenue streams.
If it was that simple it would be finished by now…
Bringing vehicles designed as software defined vehicles to market is difficult. There are seemingly herculean challenges for companies of all sizes to overcome.
Development cycles for vehicles, especially first attempt, may fail to meet targets. The more aggressive the compression of the design cycle, the more difficulties. Younger EV companies, and longer-established giants of automotive innovation, e.g. Tesla, GM, have over the last decade publicized plans only to then quietly modify and lengthen product release projects.
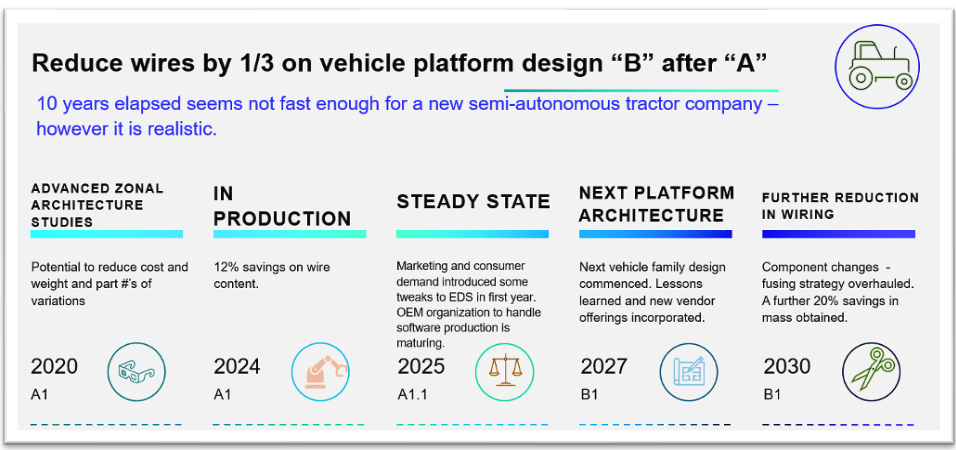
Figure 4: Even agile startup companies need time to evolve their product designs into production.
Re-engineering product designs to include substantial software content means a vehicle maker becomes a software house. The vehicle maker may choose the path to insource lots of software creation responsibility and learn quickly how to make many different layers of software. One should not underestimate how hard it is to overcome software development talent scarcity and scale-up. If you can you find the people, that’s great. But now you have to train them, bring them together as a well-functioning interlacing of teams in the various software production disciplines – likely geographically dispersed. Also plan to retain them, because their skills will be in high demand.
Outsourcing involves handing over responsibility and sharing sovereignty over the essence of your brand to companies clustered in the jungle-ecosystem already mentioned. Demand is high and supply is pinched, so that will be expensive.
Design carryover makes it harder to achieve a reduction in wire harness content. If you start off from a blank canvas, so to speak, you can choose from the whole of the palette. If the picture is already 95% painted, the constraints mean you are not going to make a significant difference. Failing to accomplish a zone controller architecture which would remove the need for 500 wires – instead implementing something partly distributed and partly zonal, your wiring design will clearly fall short of that 500 wire saving. Perhaps by a lot.
Development cycles for vehicles have very little slack time, and compromise decisions have to be made if new technology devices are late to market or don’t test out to show the desired reliability, e.g. under noise, including EMI/EMC (electromagnetic interference/compatibility), vibration and harshness tests. Or there could be a chip shortage after a pandemic or other disruption to global markets and logistics. It does happen.
Not having advanced IT tools and skilled systems electrical engineering people to design from architecture to wiring harnesses introduces great risk. OEMs need to maintain continuity of the data through the process of managing an inevitable multiplicity of changes. When desired cost and quality of wiring interconnect is compromised, a fix very close to manufacturing release takes excessive resources, time, and money.
The final challenge for vehicle OEMs whose design teams have successfully reduced wiring by following SDV methodologies is temptation. If you have removed wires from a design, then adding new wires for new features (marketing wants it!) cancels out some or all the gains.
Keep your friends close, your enemies closer, and customers closest
The SDV trend is taking hold and accelerating – but definitely not across the board. The inhibiting factors described above are strong for some companies. It is too simplistic to say that older companies are less agile and new companies are more flexible, Each vehicle OEM is unique and has unique challenges.
Harness manufacturers should understand the trends and formulate their strategy and tactics for the new conditions and seek out business opportunities to diversify and adapt. Going along with customers where they are venturing is fundamental to your future. Helping customers get to their successful future is the key to your prosperity as a service business.