Written by Saeed Mogadam, Former President at Telsonic Solutions, and Catherine Dela Cruz, Global Strategic Partnerships and Marketing Leader at ProMark Electronics
The dynamic development of new electric vehicles and batteries present ongoing challenges. For the connector designer, cable manufacturer, joining and assembly processes, these challenges demand due diligence, hard work, and collaboration by all involved. New ideas, new designs, cost reductions, higher voltage products, are all customer demands that are no longer unexpected but the norm for all involved.
Exciting and at times challenging, it is fun to see how innovation is developing in such high speed in this industry. The necessity of everyone’s expertise has created an environment where suppliers and customers are working together as a collaborative team to achieve OEM requirements. The ultimate but common goals for the team are reaching objectives for a smooth manufacturing process, building a 100% reliable quality process, and manufacturing a functional product with another breakthrough.
Ultimately, the results and action plans always encourage this collaborative team’s spirit development. We share each other’s challenges, obstacles, and difficulties by cooperation, dedication, and best technical practices to get the job done. A relationship is developed that will go on for the years to come as this exponential growth in the battery electric vehicles market evolves.
Tasks
In the wire harness industry, any new HV connection with a welding application needs to be developed at an early stage. In order to successfully accomplish a new welded HV connection, the functional requirements are as follows:
- Connector’s design for functionality, material, plating, and ultrasonic welding feasibility.
- Cable size, material, purity, and construction of the cable.
- Welding requirements, meeting the specifications such as SAE/USCAR-38, volume, production rate.
- Connector’s prototyping, welding evaluation, and assembly.
- Equipment selection and the tooling design for the welding application
- Engineering validation of the equipment, application, and process
Although welding in the cable assembly may be a small part of the big picture, without a good joint, the entire assembly would fail.
None of the functions above can be done without the involvement of both the manufacturer and welding experts. It is the close cooperation in the team that always allows a smoother release of the equipment, from the start of production and a long-term production with minimal stumbling issues. The design details of the connector and selection of the cables are and must be established at the early stage upon which the welding feasibility can be verified and confirmed. At this stage, the project starts moving forward towards the ultimate final step which is the release to production. But the process must be proven to be statistically capable. The statistical Process Control is the study that determines the best parameters for the highest standard quality requirements and monitors a consistent process of the quality of the welds.
Validation of application
It is both parties’ intention to ensure a smooth transition from installation to full production. Consequently, substantial effort is required by both sides in the pre-validation of the application in terms of tooling and the process. The idea is to find the range of welding parameters where we can have a statistically capable process. From the perspective of a welding machine supplier, the process capability is evaluated by tensile strength and visual attributes. Telsonic will conduct the following studies to pre-determine the range so that the customer can achieve good results within CPK parameters in the long run.
Although the study results may not fully match the validation at the plant due to variety of influencing factors, this makes the startup less challenging with much less effort by both the customer and the equipment supplier. Although during the development phase, it is costly to conduct this study, the results are worth the investment as opposed to when production starts.
Procedure:
- Determination of the limits that can be used for the main parameters, namely Pressure, Amplitude, and Energy. It will take about 200 test samples to determine the minimum, nominal, and maximum values of each parameter.
- DOE – Having the range of the acceptable parameters would allow us to perform a Design of Experiment to determine how much each parameter affect the tensile strength and visual attributes.
- A capability study of 50 to 100 samples, ensures that a normal distribution of data is collected before the final validation step.
- A study is then conducted for Minimum, Nominal, and Maximum settings of all three parameters. Normally one should use 100, 30, and 100 for min, nominal, and max settings. Sometimes the results may indicate that the range needs to be shifted. In such case, we must shift the range slightly based on the DOE conducted prior to the study. The shift in the range may change in the plant during the validation per USCAR specs. However, if the adjustments are made within the limits determined by the DOE, the tensile strength and visual effects would be within the acceptable range.
All these prior efforts result in a much smoother release of the equipment. Although at times costly, it is imperative that the testing of material be prepared in advance. The testing described above allows time for resolutions on any issue that might otherwise arise during production.
Ultrasonic welding is the method of choice for battery cable assemblies. These days, with the new designs and customer requirements, Telsonic is encountering more fun and creative applications which bring new challenges.
Increasingly, there are more varieties of connectors with different geometrical shapes and sizes: cables’ constructions, material and size must be suitable for the specific connector for the best quality weld. The current ultrasonic welding technology is capable of handling the growing welding sizes due to the increase in demand of larger High- Voltage cables. Currently, 120 mm² cable is the maximum size used for welding in the battery cable assemblies. However, the Telsonic PowerWheel® machine can manage cable sizes up to 200 mm² – the connector shape and size and orientation of the connection have influence in the results.
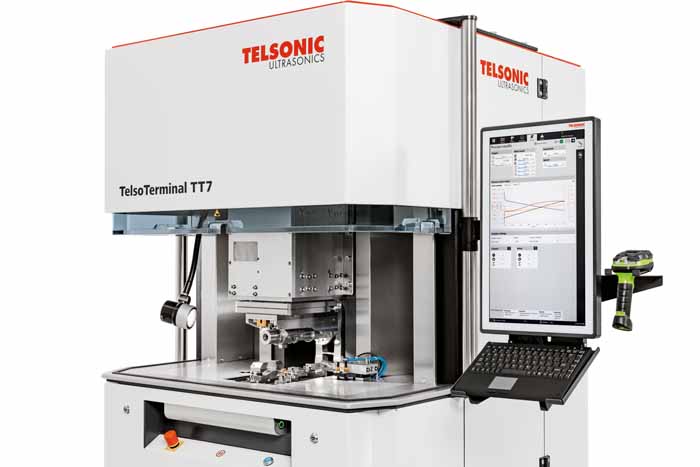
Telsonic PowerWheel® TT7
Sometimes when a welding application just seems impossible, the engineers must go back to the drawing board. But due to this close cooperation among the parties involved, the impossible becomes a solution. We can say a new team is born because our collaboration will continue for many more applications and the way we work together becomes the most efficient way for successful results. Telsonic and Promark have been working together as a collaborative team with excellent experience in providing solutions for different battery cable assemblies in 2021. The relationship between the two companies opens the path for all new product development that are in early stage with quick turn prototypes, design, and engineering support. Once production begins, Promark and Telsonic are there to fully support at scale with OEMs, to ensure they can continue to grow at the pace required. This business structure and cooperation provides a true convenience for the OEM.
About ProEV™ by Promark Electronics and Telsonic Solutions
Promark Electronics, a division of Electrical Components International, is a global manufacturer of interconnect solutions with 35 manufacturing facilities and a growing team of 24,000 employees worldwide. ProEV™ was established in response to the transportation industry’s growing need for electric vehicle high-voltage cable and custom wire assemblies. Driven by Promark’s 35 years of experience in creating mission-critical electronic components for OEMs, ProEV™ is made by manufacturers, for manufacturers. ProEV™ focuses on the electrification of industrial, commercial, agricultural, and recreational vehicles. They provide OEMs with access to ultra-fast delivery of locally stocked high-voltage cable in a wide range of sizes, and wire harness assemblies with a wide selection of connector options, including crimp and ultrasonic terminations.
The Swiss Telsonic Group has been offering its industrial ultrasonic solutions through representation in Europe, America and Asia since 1966. Constant innovations help to ensure that, in many applications, Telsonic has established a lead over competitors that offers added value to customers. With over 250 highly qualified staff, the owner-managed company specializes in plastic and metal welding as well as ultrasonic cleaning and sieving. All over the world, customers in fields such as automotive, packaging, and medical technology value the company’s comprehensive services and broad range of ultrasonic components for system construction as well as its complete welding systems.
Recent application development by ProEVTM and Telsonic:
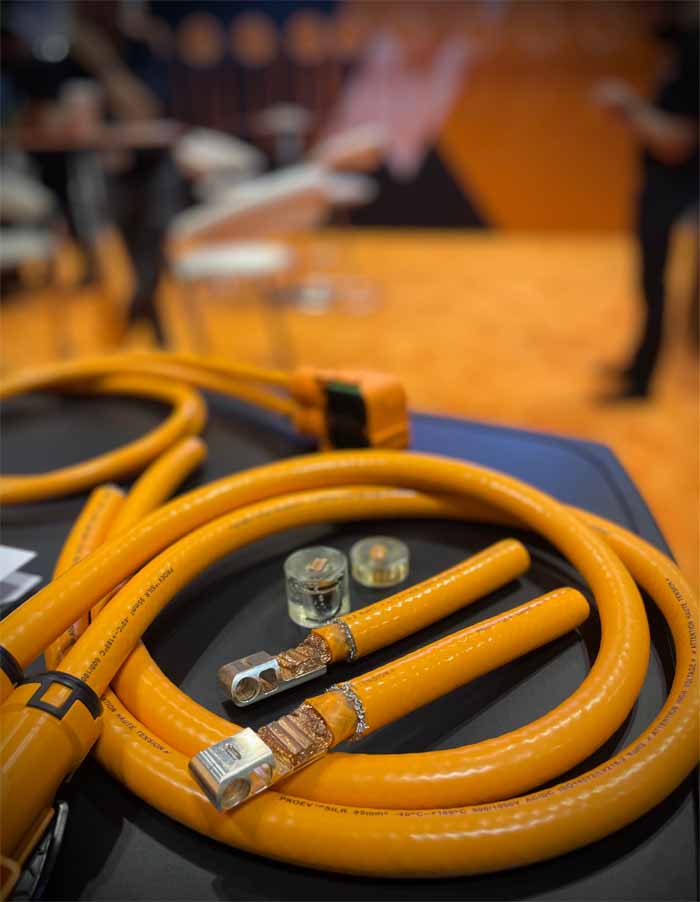
The ProEVTM 95 mm2 cable with 3,000 flexible fine strands of 0.2 mm diameter is used to terminate the Stäubli terminal with limited space for required weld width of 22 mm. ProEVTM cable was used in this application for its high flexibility. The available weld width of 18 mm as opposed to 22 mm presented challenges of providing a welding solution on a smaller space where the required weld compaction can be achieved without damages to the finer strands in the weld transition area.
The Torsional PowerWheel® welding system was utilized to achieve an excellent quality weld between ProEVTM 95 mm2 flexible cable and the PerforMore connector with 18 mm width. Tooling design and configuration had to be arranged so that we could allow sufficient welding energy to achieve a quality weld without affecting the finer strands in the transitional area.
The PowerWheel® system allows higher clamping force for the Stäubli terminal which is an advantage when welding a large cable in a smaller area. The weld nugget height in such case is higher than in a normal scenario. Since the Torsional welding amplitude is at its peak at the center of the weld nugget, one can apply more required energy for the thicker height with minimal chance of affecting the strands in the weld transition area. This ideal feature of Torsional welding allows an acceptable weld quality with minimum efforts. The quality control variables such as final weld height, welding time, and power are monitored and controlled for every weld while production data is recorded for traceability.
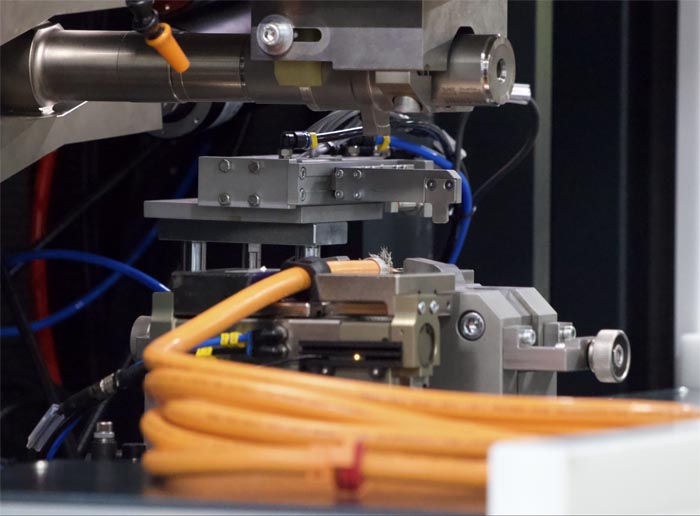
The whole is greater than the sum of its parts
In sum, as we progress in this electrification revolution, it has become imperative for the supply chain to become a global collaborative environment. Telsonic and ProEVTM’s strong cooperation have led us to quickly accelerate from design to production during this demanding and fast-paced era. Together they have solved multiple challenges through deep innovation which lets customers deliver and achieve their goals. Telsonic and ProEVTM continue to succeed and to collaboratively advance technology in the wire harness industry.