Quality standards in crimping technology are becoming ever more stringent. Particularly for connections that are integrated into systems that directly serve the protection and safety of people, like ABS anti-lock braking system, airbags, emergency call systems, medical equipment, etc., quality requirements are constantly being increased.
For a harness maker to be approved as a supplier, these high standards need to be met. This concerns the processing equipment, skills of the operators and, of course, the applied testing methods for the crimp connections.
The days when crimps were made with “flat nose pliers” or “hammer and chisel” are long gone. Today, even during the prototyping phase, care is taken to ensure that samples are produced with the processing equipment that will later be used in production.
Still, we read about recalls in the automotive industry because of flaws in the electrical system or houses on fire due to short circuits. A control cabinet who’s wiring is not manufactured to standard may cause downtime on a machine or entire production line.
Yes, quality control in production costs money. But it’s absolutely necessary, because the consequential costs in case of a failure, e.g. in a crimped connection, may be many times higher. Certification is key in every modern, competitive company and quality monitoring is a must for businesses looking to grow.
In addition to high-quality processing equipment, cost-effective quality management is essential. A good quality monitoring system not only shows prospective customers that a company is committed to quality, but also demonstrates its expertise and can help generate new business.
Talking about crimping technology, these are general testing methods:
1. visual inspection
2. measurement of crimp dimensions
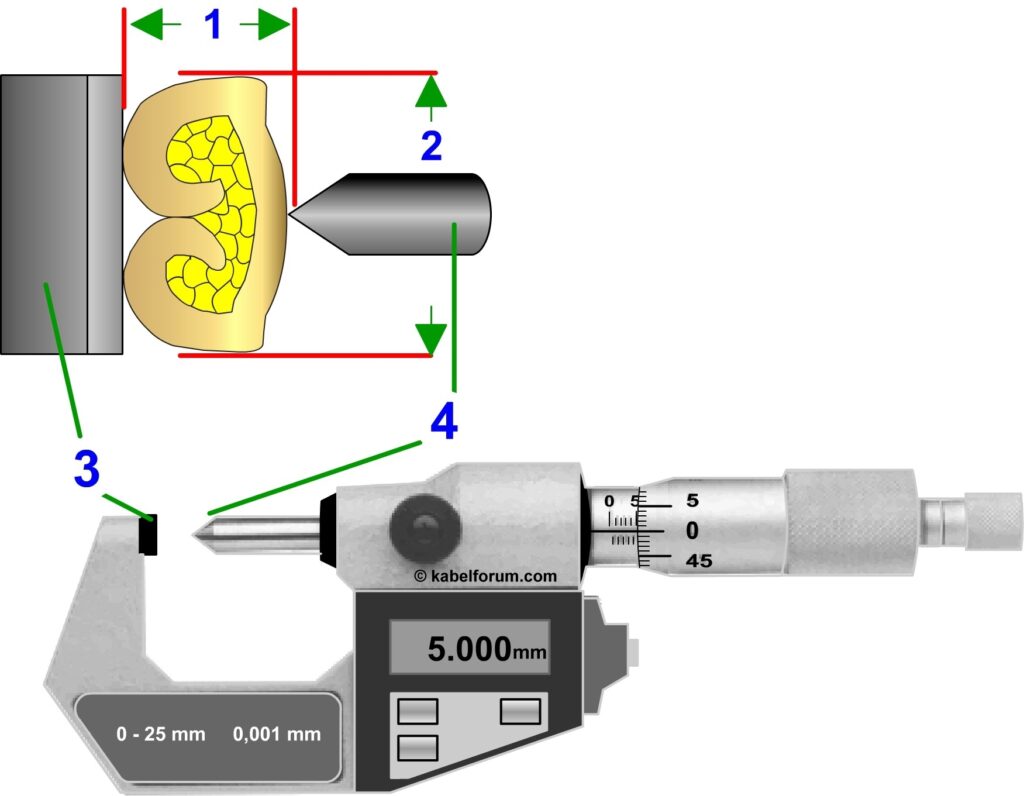
3. pull-out test
4. micrograph + micrograph evaluation
The above-mentioned test methods are the backbone of quality assurance in crimping technology today. But beware, this does not mean that one can just “pick something” from the list. Each test method on its own is to be considered as not sufficient! Only a combination of these measures will enable consistently high and reproducible quality of crimp connections.
In the fully automatic crimping machine segment, once a crimping machine or tool has been set up and is producing good crimp quality, there is a wide variety of other inspection systems that can accompany production. In addition to sensor technology, optical recognition is also used in these systems to monitor the quality of the respective work steps. Detected errors are sorted out directly via the programming. This means that production will no longer be interrupted.
Possible control parameters of such monitoring systems are:
- Crimp force monitoring
- Cutting depth of the stripping blades
- Stripping length
- Insulation caught in the crimp area
- Missing wire strands
- Damaged insulation
- Position of the seal (if present)
Many parameters in crimping technology can be monitored and controlled using modern measuring and testing methods.
However, since cable processing involves working with flexible parts (dimensionally unstable materials), there are limits to the technology. Unlike a turned part made of steel, a fine-stranded wire cannot be fixed with too much tensile force. A flexible wire simply could not withstand that.
Despite sophisticated optical monitoring units and the measuring and testing methods already mentioned, the human eye and the experience of the operator play a very important role in the production of high-quality crimp connections.
Visual inspection is one of the most important verification tools in wire processing and crimping technology.
There are simple but effective visual checks that are neither expensive nor time consuming.
A simple real-world example: Let’s say, wires are stripped and crimped in one work cycle via a stripper-crimper. If the machine operator takes a look into the collection container for the stripping residues several times an hour, he can very quickly determine whether individual wire strands are cut off during the stripping process. (This is also true for all other stripping production equipment).
This is a test that quickly and at almost no cost ensures process reliability and thus quality, and makes it possible to detect changes in machine settings or conductor quality. The alternative would be to create a micrograph, which is relatively expensive, and to count the individual wire strands on the micrograph.
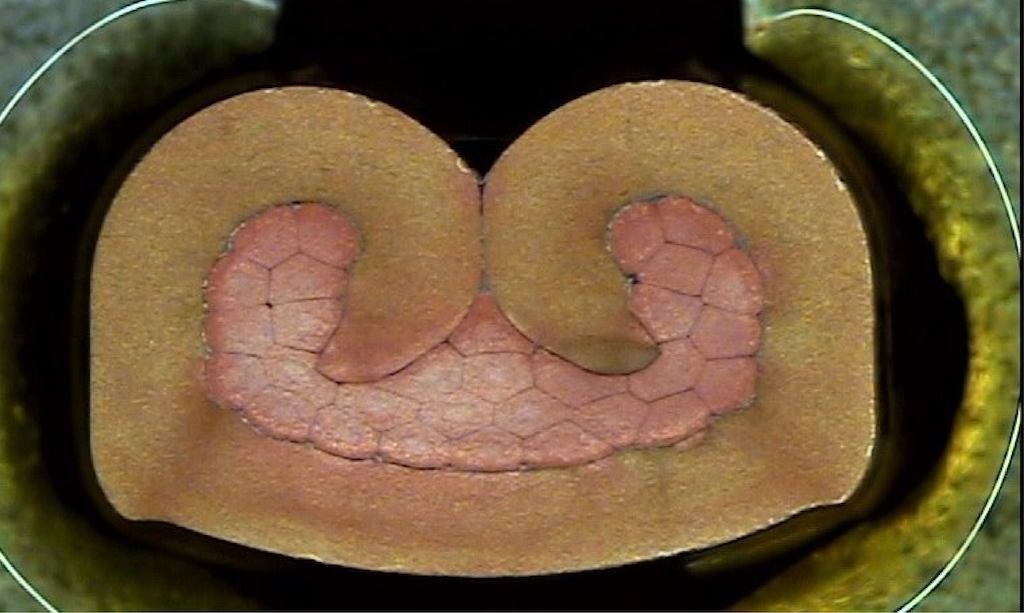
Certainly, a 100% visual inspection of crimp connections is maybe not the most feasible option, since the human eye tires very quickly and defects can be overlooked as a result. When setting up machines, as well as during inspections in ongoing production and also during incoming goods inspection, the visual inspection is probably the most important verification tool we know in crimping technology.
A condition for this is of course: You have to know what to look for. And: You have to do it!
Continuous training and employee education not only increase quality awareness, but also convey a feeling for problems and sources of error in addition to knowledge – not only in crimping technology. Or in short: If the operator knows what and why he is doing something, he will also recognize the errors!
Which test can detect which errors?
For quality assurance in the production of crimp connections with the open crimp barrel, corresponding test methods are used for different possible errors. Table 1 shows different defects and the test methods that can be used to detect them.
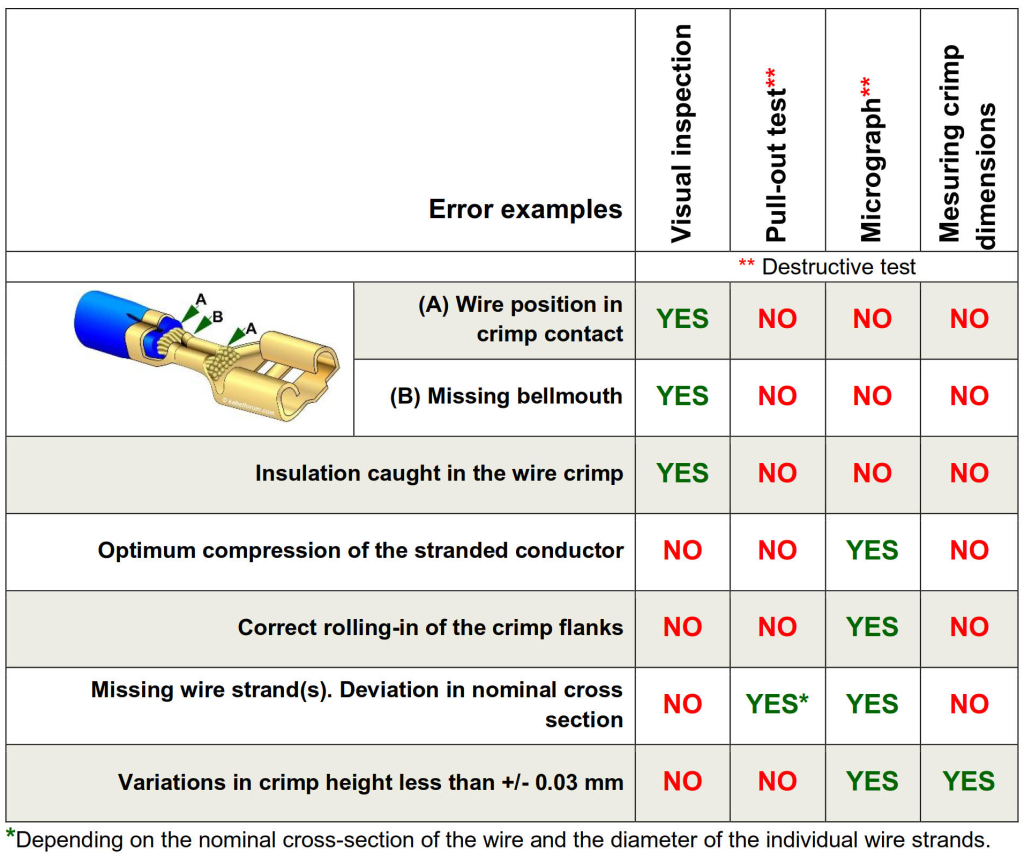
“This article was written by Volker Kratt, Founder of the German internet platform “KabelForum”, edited and translated by Andrea Weyh of Crimp Academy (www.crimp-academy.com), a source for training materials for the cable processing industry.”