The automotive industry thrives on its ability to embrace innovation as it continues to evolve to meet the combined demands of the consumer and increasingly rigorous environmental and sustainability targets. Innovation is making a positive impact across all areas of the sector, from the materials being used, the introduction of new, more flexible manufacturing methods and of course the processes used in the production of individual component parts, sub- assemblies and at the final assembly stage.
Innovation is also at the heart of the ultrasonic welding systems being used to facilitate the manufacture of the complex wire harness systems used to connect the numerous sensors, actuators, and energy storage devices required for Electric Vehicles (EV’s). Of course, these ultrasonic systems need to be based upon reliable and robust technology, however with an increasing drive towards smart manufacturing, it is also imperative that these ultrasonic welding systems leverage the benefits of digitalization if they are to meet today’s standards for efficiency, flexibility, and sustainability.
Combining the benefits of the Ultrasonic Welding process, with the latest cutting-edge developments in digital technology, delivers a production solution which is not only capable of meeting the needs of today, but which also future proofs the capital investment through the inherent flexibility of the technology to accommodate future developments within the sector.
Taking A Field Proven Process To New Levels
The digitalization of ultrasonic welding technology builds upon what is already recognized as a robust process which uses mature, field proven technology. Digitalization however, takes the ultrasonic welding process to new levels, facilitating a smart process capable of meeting the diverse requirements of a constantly evolving manufacturing environment. These all- important features, which allow a welding system to provide intuitive operation, process stability, enhanced productivity, and ease of integration with automation, is exemplified in Telsonic’s Telso®Terminal TT7.
Telso®Terminal TT7 delivers significant customer benefits including outstanding levels of digital process control through Telso®Flex software, high levels of productivity, the ability to weld large cross-sections, plus ease of integration within production lines.
The Telso®Terminal TT7 platform
Innovative Digital Control Technology
The latest Telso®Terminal TT7 system leverages the power of Telso®Flex control software, which is already well established, and field proven within both ultrasonic welding systems and automation lines.
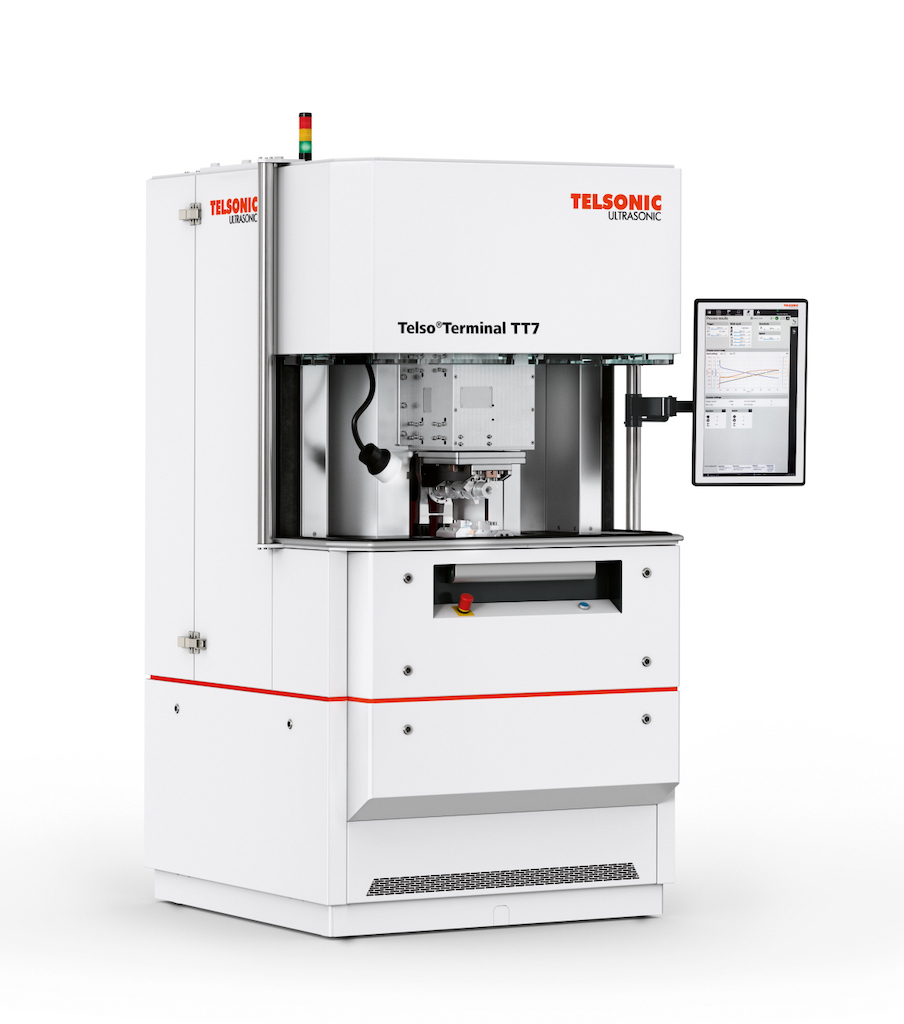
Adopting this innovative and intuitive control technology allows users to become productive more quickly. Packed with useful features, Telso®Flex provides operators with intuitive instructions and a step-by-step guide during application set up or product changeover. This includes the display of images and information about each of the components to be processed, including color, dimensions, and part number. User and rights management means that only authorized personnel can make changes to the system.
One of the key features of Telso®Flex is its ability to automatically configure the system, based upon information contained in a unique Parameter Setting Sheet (PSS) supplied with converters, torsion transducers, boosters and sonotrodes. A QR code attached to the PSS contains the article number, serial number, and relevant production data. Once scanned into the system, the digital platform is automatically configured with the production data contained in the QR code, avoiding errors which can sometimes occur when data is entered manually. Each sonotrode is assigned its own unique digital signature and all tool changes are recorded, with the system performing automatic self-test routines to ensure compliance with the anticipated configuration.
The benefits of Telso®Flex, extend far beyond the set-up stage as when in production, the current application is displayed along with a description and images. Welding results and their limits are shown as values and as different colored bars designating status as either within the limits, close to the limits, or outside of the pre-set limits. Four weld graphs and the limit settings for efficient process analysis are displayed, with the flexibility to focus on parts of the weld cycle or the whole actuator cycle.
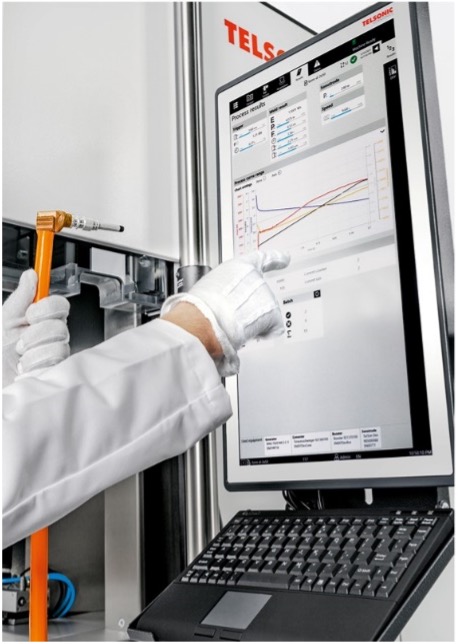
There are also a series of valuable features which provide a comprehensive level of process information during welding. An integrated load cell measures the actual force being applied to the weld, regardless of any potential friction losses in the actuator. Aiding the intuitive operation of the system, real values are used for parametrization and results. Force is shown in newtons [N], with amplitude displayed in microns [µm] helping to easily compare results and prevent failures. Also displayed are the total number of parts which have already been produced, identified as good and defective parts, together with the piece part count for the current production run.
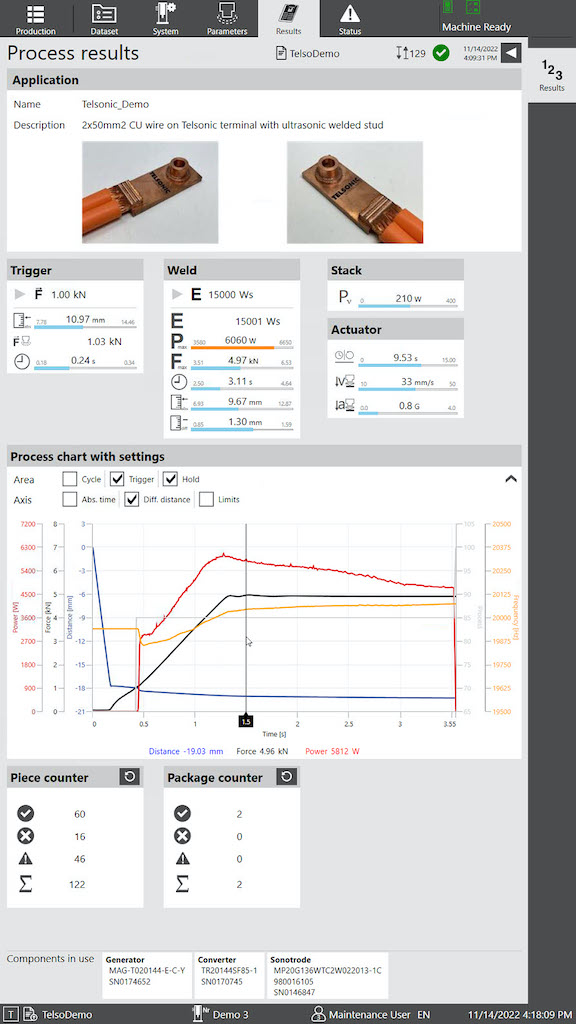
Users are provided with comprehensive levels of information on the welding process
The temperature of both the sonotrode and the component clamping jaws can be controlled by water cooling or heating as required for weld quality consistency, with the desired temperature configurable in software and readable in a data log file. Should the temperature exceed the pre-set threshold, production will be inhibited, protecting both the sonotrode and clamp tooling. A number of other options are available including: the ability to measure and monitor the converter temperature, protecting it from overheating. Other options make it possible to measure the cable diameter to identify if the wrong cable has been loaded, or if the cable is in the wrong position. It is also possible to measure terminal height to detect incorrect terminal height and misplacement.
Additional features include a material database for cables and terminals, additional sensors for enhanced quality monitoring, maintenance support functions plus remote access for in-house support.
Although Telsonic’s Telso®Terminal TT7 is available as a standalone and complete production system, for those who may wish to integrate ultrasonic welding technology as part of a more comprehensive production line, the same TT7 components, including Telso®Flex and the all-important ditalization features are available. Telsonic provides the ultrasonic press(s), control, integration support and tailored application solutions.
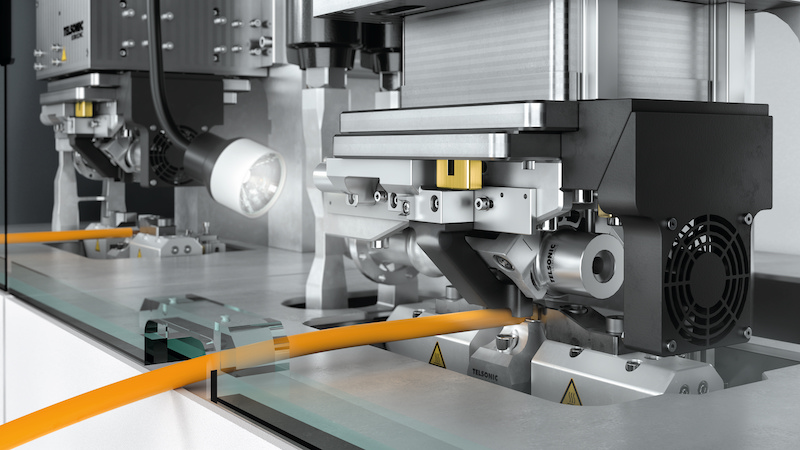
The key components of Telsonic’s TT7 can be easily integrated within an automated production line if required.
The use of cutting-edge technologies, such as the combination of Telsonic’s MES Connector and Telso®Flex software, help revolutionize the control and optimization of manufacturing processes. MES (Manufacturing Execution System) Connector is a groundbreaking development that simplifies the integration of ultrasonic systems within a customer’s existing manufacturing system. As JAVA open-source software, the MES Connector makes it possible for system operators to customize and optimize their systems independently, without the need for external support. With pre-built functions for event response, order capture, and data querying, the MES Connector offers a flexible and efficient solution for controlling manufacturing processes.
Looking to the future, automation in its many forms will continue to positively influence production processes, making them faster, more capable, and more flexible. Ultrasonic welding technology, especially with the benefits which digitalization brings, will continue to be seamlessly integrated within automated production lines, further increasing productivity and quality.
About Telsonic
The Telsonic Group, headquartered in Bronschhofen (Switzerland), has been providing ultrasonic technology solutions in Europe, America, and Asia since 1966. Continuous innovation helps to ensure that, in many applications, the company maintains a lead over competitors, offering added value to users. With more than 300 highly qualified staff, the owner-managed family company specialises in plastic and metal welding, together with ultrasonic cleaning, screening, and cutting. Current trends mean that these skills are in strong demand, e.g., for lightweight construction, electromobility, battery production, the packaging industry, medical technology, and 3D printing.
There are no fees or royalties for use; please send reader inquiries directly to Telsonic