An Introduction & Overview of diagnosing Crimp Applicator Issues, Inspection Equipment and Preventive Maintenance
Crimp quality is a key aspect within the wire harness industry. Poorly crimped connections can lead to a variety of issues, such as an electrical short, an open circuit, or a weak connection. Poor quality crimps can cause corrosion, intermittent or poor performance of the connection, and even complete failure of the connection. There are several specifications of a terminated wire that must pass through a quality check. These are just the basic elements of a terminated wire that must be measured and must fall within a certain tolerance. Each crimped terminal will, to an extent, vary between samples but minimizing it maintains high quality and process reliability. This is especially critical for wire harnesses which carry power and data between larger assemblies.
Quality is Never an Accident
Per the IPC/WHMA-A-620 standard, users hold responsibility for identifying the Class to which the assembly is evaluated for.
Class 1: General
- Includes products suitable for applications where the major requirement is the function of the completed assembly
i.e., Everyday Consumer Appliances
Class 2: Dedicated Service
- Includes products where continued performance and extended life is required, and for which uninterrupted service is desired but not critical. Typically, the end-use environment would not cause failures.
i.e., Televisions, Game Systems, Home Computing and Telephones
Class 3: High Performance/Harsh Environment
- Includes products where continued performance or performance-on-demand is critical, equipment downtime cannot be tolerated, end-use environment may be uncommonly harsh, and the equipment must function when required, such as life support systems and other critical systems.
i.e., Medical Device, Military, and anywhere high performance is needed
Wire Harness Manufacturers demonstrate their commitment to providing the highest standards of service and value to their customers. This is important because it leads to operational efficiency, improved profitability, and lower costs. A company that prioritizes quality will create products and services that are better designed, require less rework, and fewer resources, and have higher reliability and durability. Customers who receive and trust the quality of a company’s solutions are more likely to remain faithful to the brand and recommend it to others.
Inspecting the crimp is important in ensuring its quality. When inspecting your crimps there are several specifications to look at. These specifications include Core Crimp Height, Terminal Bend, Cut-off Tab, Crimp Centrality, Burr, and Pull Force. Visual inspection, using a microscope or magnifying glass can be used to determine if the crimp is good or not. The insulation should be securely in place, and the bare wire should be firmly held in the connector. If there are any signs of a defect or poor contact, which inspection needs to be done. Further inspection may include the following:
- Core Crimp Height This can be affected by both the press shut height and the regulating head index setting. Under crimping can result in low compression which in turn can result in high resistance and low pull force. Over crimping can also produce negative effects on pull test results and pre-mature wear on tooling. The majority of Mecal Applicators come equipped with our Fine Adjustment Regulating Head. Where the crimp height is easily adjusted with .01mm resolution per click.
- Pull-Force A low pull-force can result from many factors including under / over crimping, under insertion of the wire or a bad strip of wire that may be missing conductor strands.
- Crimp Height vs. Pull Force – We have conducted several in depth studies to find the “optimum” pull force or tear out value, both for customers and ourselves. When you are crimping the terminal onto the wire, you are compressing the wire to a total area something smaller than the total area of all the lose wire strands combined. We call this the compression ratio. Some think tighter is better. But it’s like holding a bunch of cooked noodles in your hand – not tight enough and some may slip out…too tight and you can squeeze them to the point where they come apart in your hand. So, as you are reducing your crimp height, little by little, you can watch the pull force value increase, but only to a certain point. Then the pull force will start to decrease, and it will continue to decrease as you go lower on the crimp height. Mecal’s standard for compression ratio is 17% to 24%.
- Terminal Bend A terminal that bends too much during the crimping process will impact the insertion of the terminal into a connector. This can be solved with an adjustable terminal support or a rear depressor. Both are used in many applicators to control the bend.
- Cut-off Tab A cut-off tab that is exceeding max tolerance can be caused by the terminal alignment front to back or the lower cut-off group being out of location. It is up to whoever is maintaining the applicator to decide which needs adjusted based on what other elements of the crimp look like. In some cases, both the slide and lower tooling group could need adjustment.
- Centrality Maintaining proper crimp centrality can help ensure the best possible crimp results as well as even tool wear. Usually, cross section analysis is required to verify centrality. This is on Mecal applicators, adjusted with the simple turn of an adjustment screw as shown in the applicator manual.
- Burr The presence of a burr in the crimp area can be signs of tool damage, over-crimping, or bad terminal alignment. In some cases, a burr is almost impossible to eliminate due to the terminal material and / or plating. In these cases, we would recommend using terminal lubricant. Per Mecal Crimp specifications, a burr is still within tolerance when the material extrusion is less than the thickness of the terminal. This will still allow inserting the terminal into housings and minimizes the risk of cutting through heat shrink.
Inspecting your crimps is easy with a digital inspection scope. The Suba-Scope is the ideal choice for wire harness manufacturers because of the easy-to-use interface, autofocus ability, high resolution, and plug-n-play simplicity. We’ve found that it increases efficiency in inspection processes, whether in your Quality Assurance department or on the production floor when troubleshooting. Mecal By Starn is Proud to be the North America Distributor of Suba Digital Inspection Scopes
An Ounce of Prevention is worth a Pound of Cure
Conducting maintenance on your applicators while they are still operable helps ensure consistency and longevity. Start with setting up a systematic inspection process that is based on your production cycles and production volumes. This will minimize any failure before its occurrence or before it turns into a major fault. Regularly conducting various inspections, tests, and replacements of parts and components before they fail or become too worn—that is, before a break or breakdown occurs is an essential practice. It not only increases the reliability of the equipment, but it also reduces the likelihood of lengthy, expensive breakdowns and downtime. With a thorough preventative maintenance process, it is also easier to detect unhealthy levels of wear on parts, as problems can be addressed before they become more serious.
Here are (4) things to check in your Preventative Maintenance:
1) Grease the ram, roller pin, cam, as well as inside of the cast body should be lightly coated with white lithium grease. The main ram and down inside the cast body are the most important areas to grease and maintain a light coat of grease throughout production. You can remove the ram from the body but be sure to leave the red safety collar, provided with each applicator, on the ram when re-inserting it into the body.
- We recommend greasing the critical components listed above before production, or every 100,000 cycles.
2) Clear the applicator of debris after production is completed for the shift.
- Do not use Air as it can blow debris further into critical places.
3) Inspect your applicator if there were any incidents (misfeed, double feeds, or terminals stuck to the crimp tools). Remove the applicator from the press, and the ram from the applicator body inspect and evaluate to ensure no damage has occurred to crimp tools. Replace any necessary damaged parts, re-align the tooling if necessary, utilizing plastic paper to ensure crimp plates and anvils do not meet each other.
4) When re-aligning crimp tools, use the Mylar paper to ensure that the upper crimp tools do not crash with the anvils.
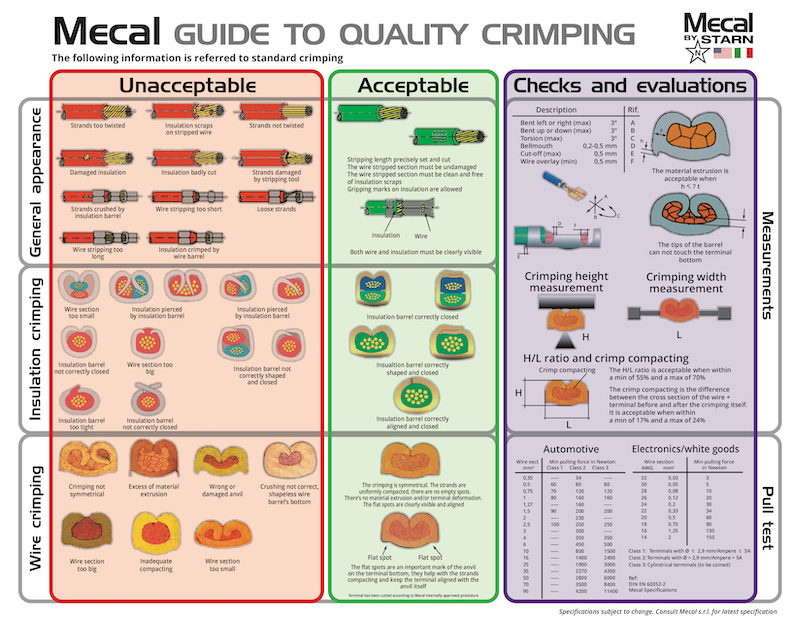
Mecal By Starn provides a Free Applicator Training Course. This course is designed to identify the root cause and corrective actions for crimp errors, along with preventive and predictive maintenance processes of Applicators.
This article was written by Samuel Myers, Business Development Manager, Jared Callahan, Senior Technician, and Ben Babcock, Design Engineer. It was influenced and inspired by the late John Belovarac. Mecal by Starn provides wire harness crimping solutions by providing products that support higher levels of system reliability, improved efficiency, and long-term savings. Mecal By Starn serves customers in consumer electronics, automotive, energy and industrial, aerospace and defense, telecommunications, healthcare, appliance, and transportation markets.