The adage “best laid plans often go awry” holds particular significance in the complex and dynamic world of wire harness manufacturing. Unforeseen challenges, evolving customer demands, and the intricacies of the production process require a delicate balance between control and flexibility. On the one hand, adhering to strict specifications is absolutely critical. Every process, every machine, every component needs to function in perfect sync, churning out products that meet precise specifications, on time and within budget. On the other hand, the very nature of manufacturing demands the ability to constantly evolve and adapt. Manufacturing isn’t static. The unexpected happens and production schedules need to adjust in real-time. So how do we reconcile these seemingly opposing forces? How do we maintain the control that we require for quality while embracing the flexibility that today’s wire harness manufacturing demands?
While tight control ensures consistency and efficiency, flexibility is essential for meeting customer expectations. However, customers are typically disappointed when this balancing act leads to padded estimates and uncertain delivery times. For manufacturers, there’s an additional downside: While control provides consistency, it stifles spontaneity and adaptation. Similarly, while flexibility allows for customization, it risks sacrificing efficiency and quality. Bridging the gap requires a strategic approach. Most wire harness manufacturers leverage some type of technology or advanced software solution to gain real-time visibility into operations, allowing them to make data-driven decisions and adapt to changing conditions quickly. This modern approach fosters a dynamic environment where control and flexibility coexist. This solution might seem straightforward, but in practice, it can be more complex.
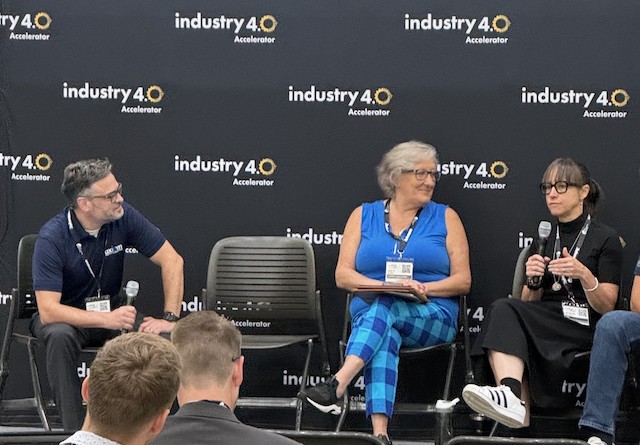
In wire harness manufacturing, a one-size-fits-all approach simply won’t cut it. Each customer’s project presents a unique puzzle full of wires with specific crimping requirements, colors, or maybe non-standard connector configurations. Each customer’s challenges are also unique, demanding a high level of adaptability from manufacturers.
Several of the most common challenges can be found in the kitting process. This step involves preparing the necessary wires, connectors, and components for assembly. The process is often manual, leading to inefficiencies and waste. Accurately calculating wire lengths is essential, as even minor discrepancies can result in scrap material. Additionally, tracking inventory becomes complex due to the nature of the cutting process, which generates waste that’s often unaccounted for. This can lead to shortages and production delays. Moreover, kitting for specific customer requirements adds another layer of complexity. Different packaging and labeling specifications for each order further increase the potential for errors.
Another common inefficiency which results in costly scrap can be found in the wire spooling process. When wire is pulled from a spool for cutting and assembly, a portion is inevitably wasted due to the cutting process. This waste, often unaccounted for, can lead to inaccurate material usage calculations. For instance, an order for ten 10-foot wires might require more than 100 feet of material due to cutting waste and scrap. This discrepancy can result in shortages and disrupt production schedules. This all underscores the manual nature of wire harness production. Unlike other industries that rely heavily on automation, wire harness assembly remains largely reliant on human labor. A single error can render an entire harness unusable. Detailed work instructions are key in mitigating human error in these situations. Operators require clear, step-by-step guidance, including visual aids, to accurately execute their tasks.
The complexities inherent in kitting, spooling, and testing processes highlight the need for a system that handles everything—a system capable of managing intricate details, minimizing human error, and adapting to the dynamic nature of the wire harness industry.
“Quantum strikes the perfect balance between control and flexibility,” says Kristin McLane, President of CIMx Software. Quantum is one of the wire harness industry’s most innovative software solutions, developed to optimize production processes and eliminate the opportunity for human error in manufacturing. McLane continues: “By automating tasks and meticulously tracking production data in real-time, Quantum provides the precision and control manufacturers need to manage inventory and reduce waste, while offering the flexibility to meet diverse customer demands.” To emphasize her point, she notes that Quantum can take a customer’s drawing from blueprint to reality by translating that schematic into actionable steps.
Despite all these benefits, digital transformation in the wire harness industry can be met with apprehension. Long-established workflows may feel comfortable and familiar, leading to a resistance to change. Concerns about the cost of implementation as well as potential disruptions to production can create a reluctance to embrace new technology. Experts counter these arguments by pointing out that the upfront investment in software like Quantum is offset by the long-term benefits like reduced waste, improved efficiency, and faster turnaround times. Furthermore, a well-implemented system is likely to minimize disruptions by streamlining communication and automating routine processes. Industry leaders overwhelmingly agree that the future of wire harness manufacturing is digital.
Manufacturers know that flexibility is more than just adapting to last-minute changes. It encompasses supporting the employees who carry out the manual steps in the processes while cultivating a culture of continuous improvement. Similarly, control is not the same as micro-management. It’s about having the foresight to anticipate potential challenges. By adopting an advanced software solution like Quantum, wire harness manufacturers can embrace a holistic approach that balances these elements and prepares them for whenever best-laid plans go awry.
About CIMx:
Patrick Vaughn is a Digital Journalist at CIMx Software. With a 28-year heritage of solving complex manufacturing challenges, CIMx built Quantum to provide flexible control for modern manufacturers. To learn more about CIMx and Quantum, visit www.cimx.com or call 513-248-7700. Reach out to the author at [email protected]