In any electrical system, particularly those involving wire harnesses and cable assemblies, ensuring the integrity and safety of the connections is critical. Continuity testing and HiPot (High Potential) testing are essential processes that help verify that electrical circuits function properly and meet safety standards. Without these tests, there’s a risk of malfunction or, worse, electrical hazards such as short circuits, fires, or equipment damage.
Continuity Testing
Continuity testing ensures that the electrical current can flow unobstructed from one end of a wire to another. It verifies that each wire in a harness is correctly connected and that there are no open circuits or incorrect connections. This is crucial for avoiding failures in the field, where faulty connections could lead to costly repairs or dangerous situations.
HiPot Testing
HiPot testing, on the other hand, applies a high voltage to the wire harness or cable assembly to confirm the insulation quality and verify that there are no shorts between conductors or to ground. It’s particularly vital for ensuring that the harness can handle its expected operational voltage without risking an insulation breakdown.
Simple vs. Complex Harness Testing
The testing process for wire harnesses varies significantly based on the complexity of the system:
– Simple Harnesses: For smaller or less complex harnesses, such as those used in consumer electronics, the primary concern is ensuring continuity. These harnesses typically have fewer wires, lower voltage requirements, and fewer interconnections, so the testing process is relatively straightforward. A basic continuity tester or handheld tool may suffice.
– Complex Harnesses: In contrast, harnesses for industrial, aerospace, transportation, or medical applications are much more complex. These systems often involve hundreds or even thousands of wires, numerous connectors, and must operate in harsh or highly regulated environments. For these applications, both continuity and HiPot testing are mandatory. More sophisticated testing equipment is required to ensure reliability, meet safety standards, and perform in extreme conditions.
Key Players in the Harness Testing Equipment Market
Several companies offer solutions for wire harness and cable assembly testing. Below is an overview of some of the key manufacturers and their offerings, highlighting the most suitable applications for each.
1. Cirris Systems (A Komax Group Company)
Cirris Inc is known for its user-friendly and versatile electrical cable and wire harness testers. Their product line includes both basic and advanced test systems, catering to a wide range of applications and industries.
– Product Highlights: Cirris offers off the shelf and tailored testing solutions for any size of project, big or small. Off the shelf and easy to use testers like the Easy-Touch Pro, which supports continuity, HiPot, and resistance testing. Their modular systems, both in hardware and software, make it easy to scale testing capabilities as needed.
– Applications: Cirris’ benchtop testers are ideal for small to mid-size cable assemblies and wire harnesses, making them a good choice for contract manufacturers dealing with a mix of simple and moderately complex harnesses. Their larger rack mounted systems further expand their scale and capabilities into very large applications up to 100,000 test points. Their products are commonly used in industries like Aerospace, Defense, Space, Electronics, Medical Devices, and Automotive. Their machines can also be integrated to control semi and fully automated machines where electrical testing is desired.
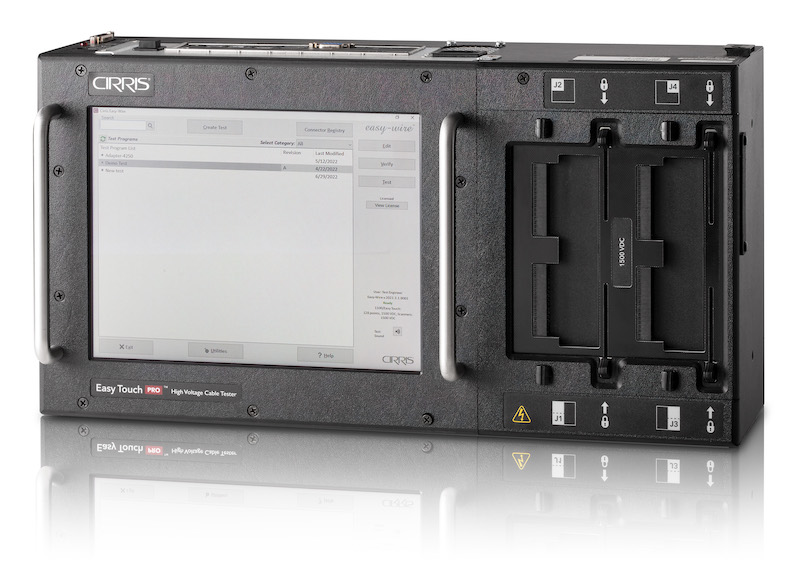
2. DIT-MCO
DIT-MCO is a leader in the high-end, complex wire harness testing market, especially for industries with demanding reliability requirements like aerospace..
– Product Highlights: DIT-MCO’s offerings, such as the **Model 2650**, are capable of testing extremely large and intricate wire harnesses with thousands of connections. These systems provide multi-point testing and are equipped for both continuity and high-voltage HiPot tests.
– Applications: DIT-MCO systems are widely used in aerospace, defense, and transportation, where the complexity of wire harnesses demands sophisticated testing capabilities. Their equipment is designed to handle high-stakes environments like military aircraft, space systems, and large-scale industrial machinery.
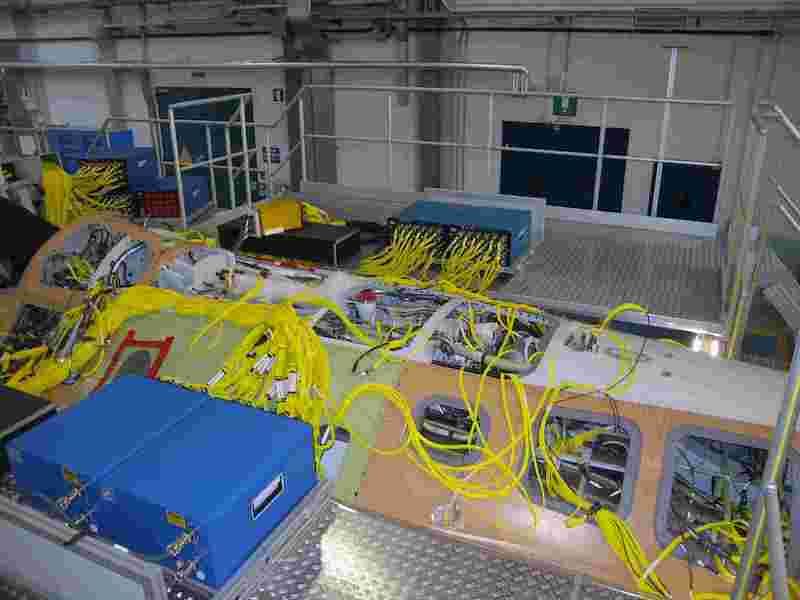
3. Dynalab Test Systems
Dynalab Test Systems offers wire harness testers with features including advanced testing capabilities for various industries, customizable testing options, and intuitive software interfaces, with a focus on cost-effectiveness and user-friendliness.
– Product Highlights: Dynalab Test Systems offers a suite of testers for low voltage continuity tests, supporting projects from 64 to over 32,000 test points, as well as Hipot applications. The NX Testers are suitable for diverse component testing and validation, featuring LED-guided solutions and various accessory interfaces.
– Applications: Dynalab Test Systems supports various custom low volume wire harness applications to major high volume automotive production lines. Dynalab Testers’ are suitable for automotive, appliance, military, aerospace, and industrial wire harness applications.
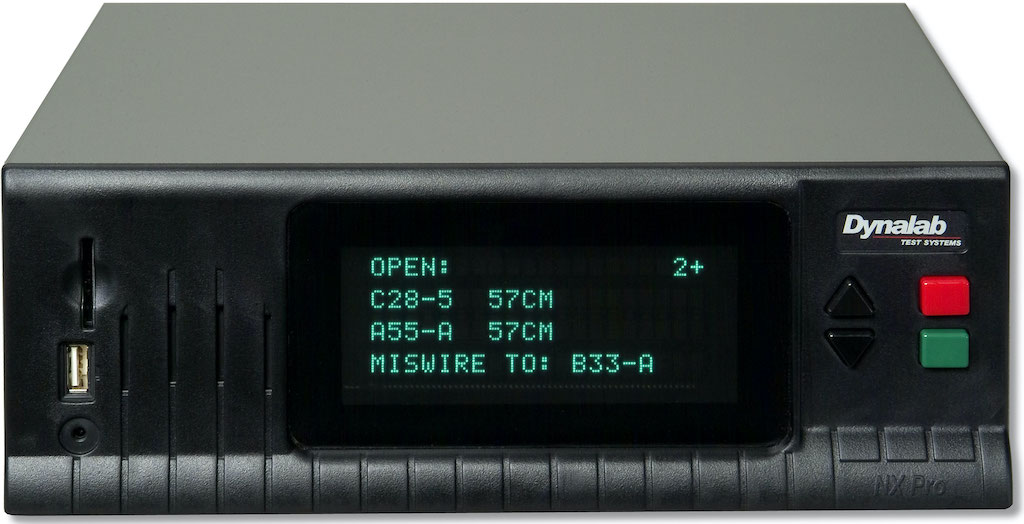
4. CAMI Research
CAMI Research specializes in low-to-mid complexity cable testers for low- and high-voltage systems and accessories for cable, wire harness and backplane test management.
– Product Highlights: CAMI’s CableEyeÒ multi-conductor wiring analyzers and guided assembly systems are customizable and scalable. Systems are PC-based interface, which provides extensive data logging and reporting capabilities. They perform, display, and document diagnostic tests and Pass/Fail checks for electrical properties such as continuity, resistance, miswires, and intermittent faults.
– Applications: CAMI Research’s products are well-suited for aerospace, automotive, defense, medical, robotics, telecom and other sectors, particularly when manufacturers need detailed reporting and traceability features. Users can improve productivity, product quality, and documentation with a rapid return on investment.
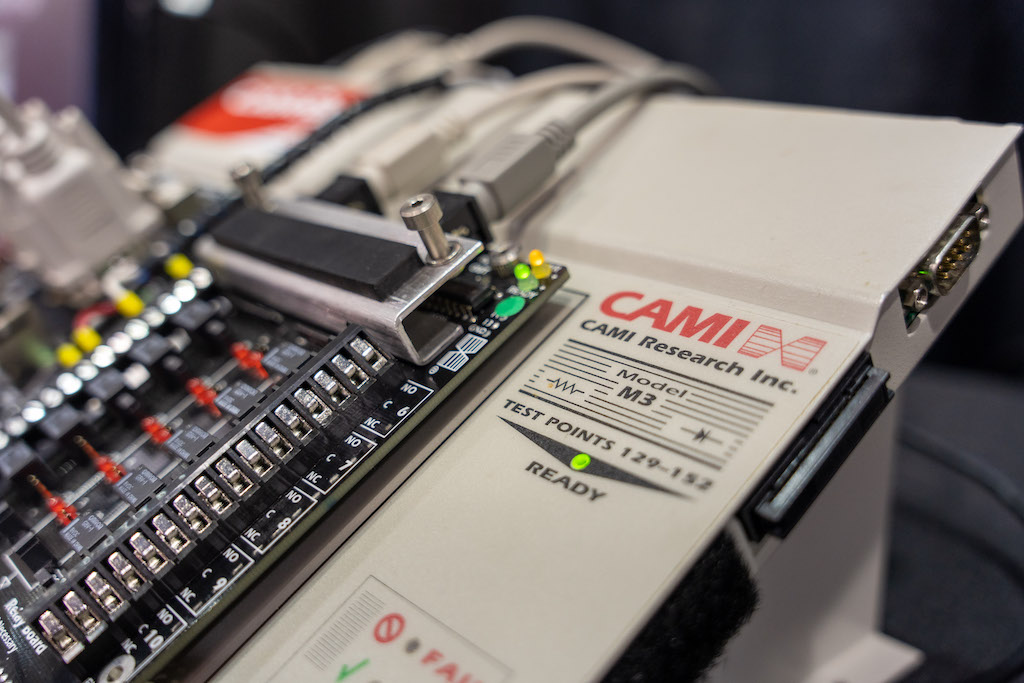
5. MK Test Systems
MK Test Systems is a leading provider of automatic electrical testing equipment designed to meet the demands of high-performance industries such as aerospace, rail, defense, and industrial sectors.
• Product Highlights: MK Test Systems offers fully automated test solutions for both continuity and HiPot testing, along with insulation resistance testing. The MKAT 3000 series is particularly well-regarded for its ability to test large and complex assemblies, offering modular configurations to adapt to various production environments.
• Applications: MK Test Systems’ equipment is ideal for large-scale production environments where efficiency, speed, and accuracy are crucial. Their systems are widely used in high-stakes industries like aerospace, transportation, and defense, where stringent testing and precise documentation are mandatory. Additionally, MK Test provides specialized software for enhanced test reporting and traceability, critical for industries requiring strict regulatory compliance.
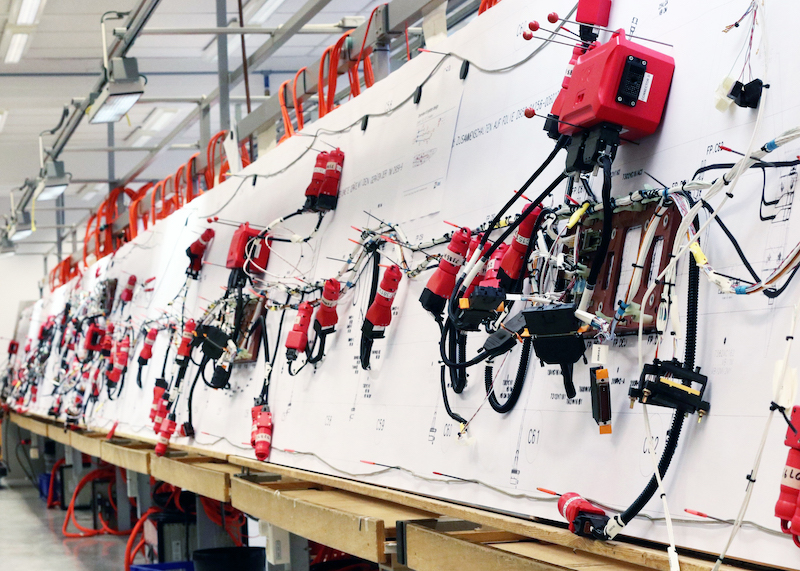
Other Notable Manufacturers
In addition to these key players, several other companies provide specialized wire harness and cable assembly testing equipment:
– **Weetech**: Known for offering high-voltage testing systems, Weetech products are ideal for industries requiring rigorous HiPot testing, such as automotive and industrial power systems.
– **Kahnetics**: Specializes in automated test systems, catering to manufacturers needing fully automated solutions to handle large volumes of testing for complex assemblies.
– **ATE Solutions**: Offers a range of automated testing solutions, focusing on large-scale production environments where speed and efficiency are essential.
Choosing the Right Test Equipment
Selecting the proper test equipment for wire harness and cable assemblies depends on a variety of factors, including the complexity of the harness, the industry standards, and the required testing processes. Here are a few key considerations:
1. Harness Complexity: For simple harnesses, basic continuity testers may be sufficient. However, for complex assemblies, a system capable of multi-point testing, HiPot verification, and advanced fault diagnostics is essential.
2. Industry Standards: Different industries have specific safety and performance standards. For example, aerospace and medical applications may require higher levels of testing, including extensive HiPot and insulation resistance tests, to ensure compliance with strict regulatory guidelines.
3. Production Volume: Manufacturers producing large volumes of cable assemblies will benefit from automated or semi-automated testing systems that can handle repetitive tasks efficiently while ensuring high accuracy.
4. Customization and Scalability: The ability to scale testing equipment to meet the growing needs of a manufacturing process is also important. Companies that offer modular or upgradable systems, like Cirris or Dynalab, provide flexibility that can be cost-effective in the long run.
5. Data Reporting and Traceability: In industries like medical devices or aerospace, traceability and detailed reporting are critical. Testing systems with advanced software features, such as those from CAMI or Dynalab, can log test results and ensure compliance with regulatory documentation requirements.
Conclusion
Continuity and HiPot testing are critical to ensuring the safety, reliability, and performance of wire harnesses and cable assemblies, especially as systems become more complex. Manufacturers need to carefully consider the demands of their specific industry and production needs when selecting test equipment. Proper equipment selection is crucial not only for ensuring product quality but also for maintaining safety and regulatory compliance, especially in high-stakes environments like aerospace, defense, and medical applications.