Justificación de los ultrasonidos en la integración de barras colectoras.
Por TECH-SONIC
Las barras colectoras vienen en diferentes tamaños y formas que determinan la cantidad máxima de corriente eléctrica que un conductor puede transportar antes de deteriorarse. Las barras colectoras generalmente están hechas de cobre, latón o aluminio resistentes a la corrosión en tubos sólidos o huecos. La forma y el tamaño de una barra colectora, ya sean tiras planas, barras sólidas o varillas, permite una disipación de calor más eficiente debido a la alta relación entre el área de la superficie y el área de la sección transversal. Las barras colectoras de cobre generalmente se oxidan con el tiempo pero siguen siendo conductoras. Por eso es importante recubrir la barra colectora para protegerla contra la oxidación. Los tres propósitos principales del recubrimiento de barras colectoras son: inhibir la corrosión, aumentar la conductividad y con fines estéticos. El tamaño actual de las barras colectoras utilizadas en aplicaciones automotrices es de 35, 50 y 90 mm2. Hoy en día, un paquete de baterías tiene entre 15 y 20 barras colectoras.
Con los materiales adecuados, una barra colectora puede ayudar a la gestión térmica junto con la distribución de energía en un EV/HEV. El material conductor de una barra colectora y el tamaño de la sección transversal de la barra colectora determinarán su capacidad de transporte de corriente. Las barras colectoras laminadas generalmente consisten en conductores de cobre o aluminio que pueden o no estar revestidos con un metal conductor adicional, como plata u oro. Las barras colectoras se pueden fabricar en una variedad de formas, incluidas tiras planas, varillas sólidas y tubos huecos, con formas planas o huecas generalmente preferidas para aplicaciones de alta corriente.
Los requisitos de energía de un EV/HEV pueden variar ampliamente, siendo la mayor cantidad de energía eléctrica requerida por el inversor y el motor de accionamiento eléctrico. Un motor EV tiene una amplia gama de niveles de potencia, desde un funcionamiento de voltaje más bajo a velocidades lentas hasta un uso de mayor potencia al acelerar o subir pendientes pronunciadas. Las barras colectoras de baja inductancia pueden ayudar a lograr una transferencia de energía de baja pérdida con alta eficiencia energética desde un paquete de baterías, al minimizar las pérdidas de energía en la ruta de transmisión de energía desde el paquete de baterías de alta potencia de un vehículo eléctrico hasta el inversor y el motor de accionamiento eléctrico.
Beneficios de usar Barras colectoras
Hay muchos beneficios en el uso de barras colectoras para sistemas de cableado EV. Las barras colectoras hacen que sea mucho más fácil agregar o reubicar energía con poco o ningún tiempo de inactividad. Debido a su diseño simple, no requieren mantenimiento de rutina. Tienden a ocupar menos espacio y son más planos que los sistemas de cable tradicionales y pueden suministrar hasta un 15 % más de energía. Las barras colectoras ofrecen mucha más flexibilidad de diseño y disipan más calor que sus contrapartes trenzadas.
Una barra colectora se puede caracterizar por su resistencia y conducción, idealmente con sus contribuciones eléctricas distribuidas lo más uniformemente posible a lo largo de su longitud para evitar problemas de rendimiento. Si bien se prefieren los valores de resistencia y conducción más bajos posibles en una barra colectora para la distribución de energía EV y HEV, algunas barras colectoras para ese propósito tienen capacitancia agregada de diferentes maneras para aumentar las capacidades de transporte de carga de la estructura de distribución de energía.
A diferencia de los cables de alimentación, las barras colectoras también permiten lograr una distribución de energía con alta densidad de potencia al montar componentes activos para la conversión de energía, como semiconductores IGBT, y elementos de circuitos pasivos, como condensadores y filtros EMI para reducción de ruido, en el barras colectoras En la mayoría de los casos, los elementos del circuito se pueden incorporar a una barra colectora laminada antes de su instalación en un EV o HEV, o como parte del proceso de fabricación de la barra colectora. La incorporación de condensadores electrolíticos en barras colectoras para accionamientos de motor puede mejorar el rendimiento y, al mismo tiempo, conservar el volumen del circuito. Para ahorrar aún más espacio dentro de un EV/HEV, hay formas híbridas de barras colectoras disponibles con rutas de señal junto a los planos de potencia para interconectar sensores y unidades de control a las computadoras a bordo del vehículo y los controles del conductor.
¿Por qué hay barras colectoras en vehículos eléctricos?
Con el desarrollo del vehículo eléctrico, los fabricantes han descubierto que las barras colectoras son la solución ideal para mejorar la conducción en los vehículos eléctricos. Las barras colectoras han revolucionado el panorama de los vehículos eléctricos y se alojan dentro de interruptores, tableros de distribución y recintos de electroductos para la distribución local de energía de alta corriente.
Los siguientes son los beneficios del uso de barras colectoras en vehículos eléctricos: capacidad de agregar o reubicar energía fácilmente sin tiempo de inactividad, no requiere mantenimiento de rutina, más rápida y menos costosa para expansión o remodelación, más ecológica ya que requiere menos materiales de instalación, el conductor plano ocupa menos espacio, puede soportar hasta un 15 % más de energía que el cable, menos peso y espacio de embalaje con mucha mejor flexibilidad y una disipación de calor más eficiente que los cables trenzados.
Vehículos Eléctricos y Soldadura Ultrasónica para Barras
En los vehículos eléctricos, grandes bancos de celdas de batería se fusionan en paquetes sellados para lograr el voltaje y la corriente de funcionamiento necesarios para alimentar el motor eléctrico de un vehículo. Dos preocupaciones principales con respecto a los vehículos eléctricos son el almacenamiento de energía y el campo de prácticas. Los OEM están abordando estos problemas de dos maneras: creando baterías más grandes que permiten un mayor alcance y creando baterías más potentes que permiten una carga más rápida.
A medida que el mercado de vehículos eléctricos continúa expandiéndose, los fabricantes buscarán soluciones para mejorar los procesos tecnológicos actuales para vehículos eléctricos en lo que respecta al rendimiento de la batería, como la eficiencia, la vida útil de la batería y el tiempo de carga. Para maximizar estos factores potenciales clave, la soldadura ultrasónica jugará un papel crucial en estos avances tecnológicos. Desde la década de 1980, la industria de fabricación de arneses de cables para automóviles ha sido documentada como el mayor usuario de soldadura ultrasónica.
Tecnología de soldadura ultrasónica de TECH-SONIC para barras colectoras de soldadura
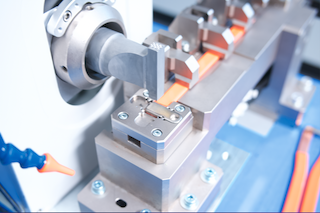
Con la implementación de barras colectoras en vehículos eléctricos, se necesita un procedimiento de unión sensible y sólido para garantizar la conductividad. La tecnología de soldadura ultrasónica es un proceso de unión probado que es ideal según lo especificado por los fabricantes de automóviles para su uso en barras colectoras y electrónica de potencia. Con la soldadura ultrasónica, los parámetros se pueden controlar y hay menos tensión en la soldadura, lo que hace que las soldaduras sean repetibles y precisas. La soldadura ultrasónica es el proceso de unión preferido para las barras colectoras.
Sin embargo, TECH-SONIC ha desarrollado un proceso de unión ultrasónico de última generación llamado “CLC” o Closed Loop Control. La soldadura ultrasónica convencional funciona con un cilindro neumático que puede tener algunas inconsistencias con la variación del aire, pero la soldadura ultrasónica de control de circuito cerrado de TECH-SONIC utiliza un servomotor eléctrico y celdas de carga junto con una soldadora ultrasónica. Esta integración permite a los usuarios controlar y monitorear la fuerza aplicada y la amplitud durante el proceso de soldadura. TECH-SONIC llama a este proceso “soldadura de varios pasos”, convirtiendo un sistema de circuito abierto en un sistema de circuito cerrado. Esta tecnología brinda un control de calidad superior con resultados de soldadura altamente repetibles, lo que genera ahorros de costos significativos. Este es el proceso de unión ideal para barras colectoras para garantizar una soldadura conductora y sólida.
Referencias: