By Paul Johnston – Siemens
Unpacking motivations of customers gets to underlying needs. Let’s look for insights, perspective, and lessons from how Electric and Autonomous Vehicle OEM’s electrical systems designers do their work. It is an expanding market segment.
Acronyms: ROFL not really – RFLP definitely
Designers who devise a transportation architecture refer to models of system requirements to ensure they are fulfilled. Reviewing, performing simulations and testing the integration of different subsystems are a series of complicated tasks. These are fraught with difficulties and finding time to optimize a design is hard.
Systems models possess different levels of fidelity and maturity. They are developed independently in various technical languages and may not interlace well. Also, models are often locked in applications that only a few specialists understand, lacking parameters and attributes coworkers can comprehend. Fundamental software or signal/ network architecture choices are made early by a few design engineers. These decisions impact the wiring content downstream.
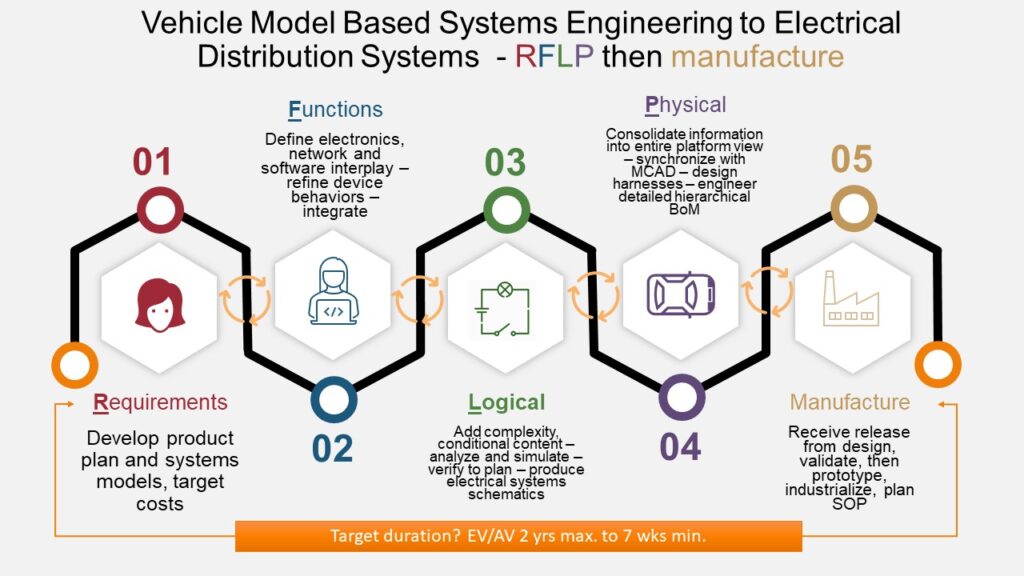
Figure 1: Manufacturing a harness preceded by an often lengthy design process – in EV/AV with aggressive/ambitious timelines.
RFLP is an acronym which summarizes vehicles design projects. It refers to Requirements, Functions, Logical and Physical phases, in that order. ROFL is an acronym for “Rolls on Floor Laughing” a reaction of EV/AV design engineers when asked to squeeze another key project into their “slammed” schedule.
Architecture abstractions – device definition – early pre-wiring designs.
Many OEM’s, deploy in their electrical design methods a Device Transmittal (DT) repository or Interface Control Documentation (ICD) system to characterize devices governing electrical interconnect. Stored descriptions of physical manifestations of equipment and their logical attributions (signal assignments to device pins for example) are refined and negotiated between team members. This dataset is useful, if and only when it is controlled with respect to allowed changes. Overall data quality outcomes depend on a collaborative effort where most people contributing to device definitions are largely oblivious of the detail of the wiring and harness design process.
A set of subsystem schematics is almost always developed as documents of record for this logical phase of electrical design. These schematics consist principally of functional connectivity expressed as nets/signals. If DT/ICD repositories are used these schematics derive significant contribution from them.
Systems, network and pre-wiring architecture increasingly follows a zonal compartmentalization in vehicles. Zonal architecture lessens the cost and space needed for electrical and electronics content by reducing and consolidating Electronic Control Units (ECU’s).
Platform level design and generating wiring a modern solution.
Siemens colleagues and I steer EV customers towards creating a digital twin of design as a whole vehicle overview. Zonal architecture, logical systems, device characterization and the variability of the finished product are integrated into a meta-design “the platform” to which is added topological information. Physical wiring can be generated when functional and systems inputs are mature. Subsequent wiring design schematics should be seen as an output of the platform design – obtained querying the wiring of the entire vehicle with all its variants. Interconnect auto-generated with software tools primed with business rules (for network wiring, splice positions and so on) greatly accelerates the speed to develop verified interconnect data. It is the only way many EV designers can fit their work in the greatly compressed cycles expected of them.
Choice although good, complicates.
As wiring is defined, the requirements’ optionality is applied. The prerequisites, end user options and clustering of the variability is often termed “complexity.” In combining optional features into buildable assemblies, techniques that constrain proliferation of variations, yet retain control of the BoM content exist. One philosophy uses a 150% or composite design which can decomposed to derived harnesses. KSK – Kundenspezifischer Kabelbaum in German – is an alternative way of handling many customer-specific variations (fig 2). KSK’s goal is to eliminate redundancy and waste, for example isolating common circuitry and defining modules for additions as “children” or “overlays.”

Figure 2: Same Harness design, different buildable harnesses based on optionality
If harnesses’ options are numerous, one can expect nuances and frequent changes. Mistakes in assigning tags to show variability of components and errors processing logical relationships are hard to detect reliably.
End user alternatives impacting vehicle electrical features can easily encompass thousands, or millions of potential combinations. That’s beyond an engineers’ ability to comprehend. Trying to judge where it makes sense to give away circuitry, or where to reduce proliferation of child parts using spreadsheets increases the likelihood of errors. Engineers without sophisticated generative computer applications will struggle to produce work products and CAD outputs of acceptable quality in the time available.
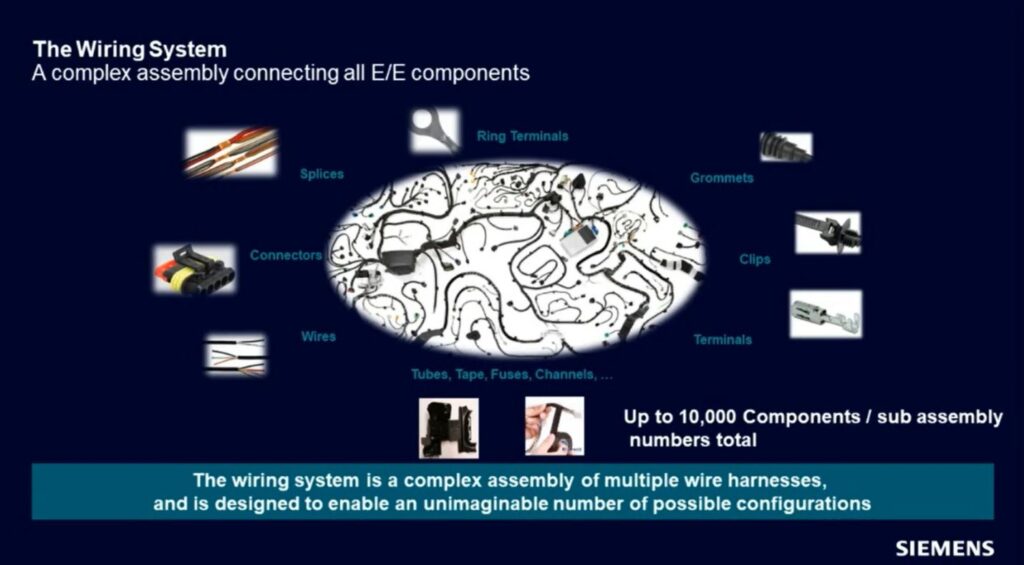
Figure 3: Getting more complicated as time goes on
Omitting wires which should have been assembled into a child harness of the meta-design is a major risk. The consequences of installing a harness which does not support what’s in the vehicle are dire for both OEM and Harness Maker.
Designers package wiring in 3D models and” partition” which is a term used to include decisions about inline interconnections linking harnesses families. Managing routing of bundles, rightsizing and choosing inline pair connector systems are tasks assigned to experienced engineers. Good judgment about capacity for routing more signals (consequently bigger bundles) in the later life of the platform saves time and expense. Exchanging data with electrical design models affords an opportunity to validate. Sub-optimal/incorrect decisions here, inadvertently concealed during later validations, may re-emerge as mis-builds in production. Teamwork between mechanical and electrical designers is crucial.
Each individual harness part number needs a BoM with precise calculations providing dimensioning and quantification. This is essential to model the cost, time and processes of manufacture. Many validations (e.g., appropriate connector accessories) take place to prevent manufacturability issues. Without versatile and efficient software tools at this stage, it is easy to fall into repetitious manual data creation and endless checking.
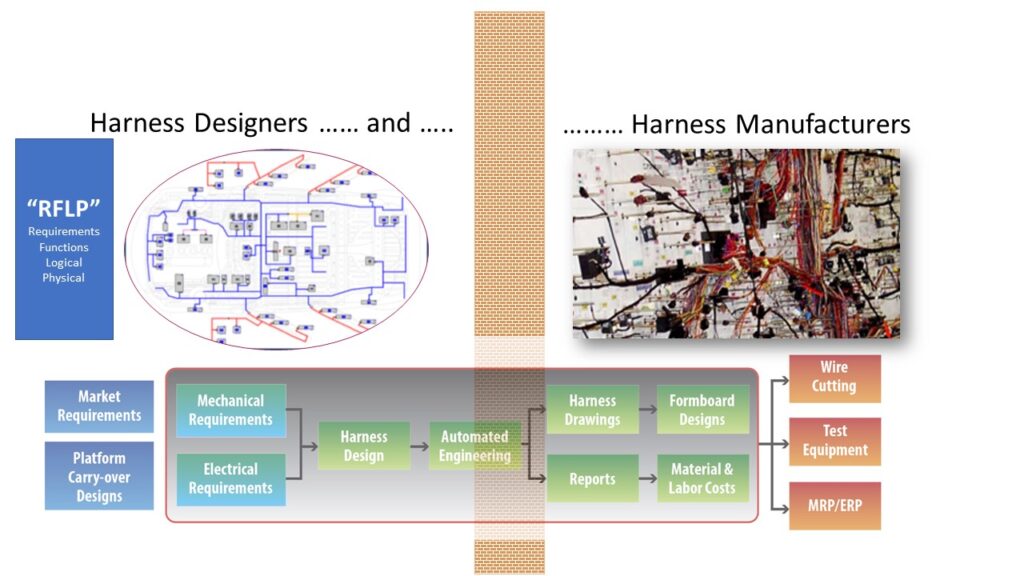
Figure 4: in the middle ground is commercial opportunity. Any chance for a feedback loop in these processes?
Most studies in this area agree design changes account for over 90% of work. Feedback loops informed by software applications serve a valuable purpose. They referene the design artifacts in the previous stage of the life cycle, along with the drawings, diagrams and checklists, to trace the continuity of requirements.
Handing off correct design data to the next phase helps because late changes are expensive. Effectively communicating changes between design and manufacturing, shown in figure 4 as a brick wall, is particularly valuable.
Electrical Designers Culture and Practices in EV/AV Companies.
An electrical engineering manager with EV Company Faraday Future, Ulrike Hoff, authored material six years ago which she presented at conferences. Her ideas succinctly capture the challenges faced by new OEM entrants. Ms. Hoff works now in a mining/industrial vehicle company on a different type of electric powered platform. Her observations still hold true today for EV/AV ventures (figure 5).
Electrical design in transportation, as well as other electrical engineering fields, is expressed in CAD outputs and delivered by software automation tools. Herein lies the first challenge – EV/AV companies truly can be starting with a software solution unhitched to a design process or a well-defined product development workflow.
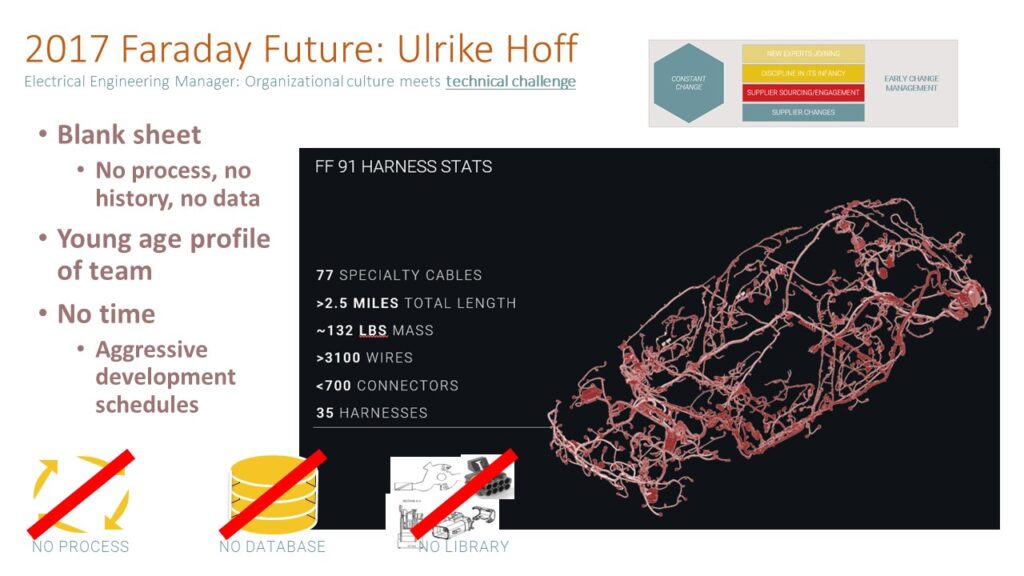
Figure 5: Organizational Culture meets Technical Challenge
Engineers are very talented, yet can lack real-world experience. They may also lack the luxury of time necessary for creating any of these data sets from scratch. Working in an environment of best practice decisions, where the development of methods and standard, or writing new specifications is something they must do. It can be an invigorating but also an exhausting experience. It is frequently the inspiration of working a mission with ecologically more responsible technologies which makes it worthwhile for many designers.
“Culture eats strategy for breakfast” – Peter Drucker, management author & theorist
When engineers start with a “blank” sheet, they participate in forming an organizational culture which is exciting and intense. In a vibrant atmosphere, there are ups and downs for staff. Expansion can be followed quickly by contraction in the size of a team because of short-term funding difficulties. Turnover/attrition rate can be high in terms of people voluntarily separating too. Staff can be lost to other EV/AV positions, cashing in on the scarcity value of their design knowledge. Many startup companies expect 60+ hours a week and staff choose sometimes to leave for a personal/professional life balance.
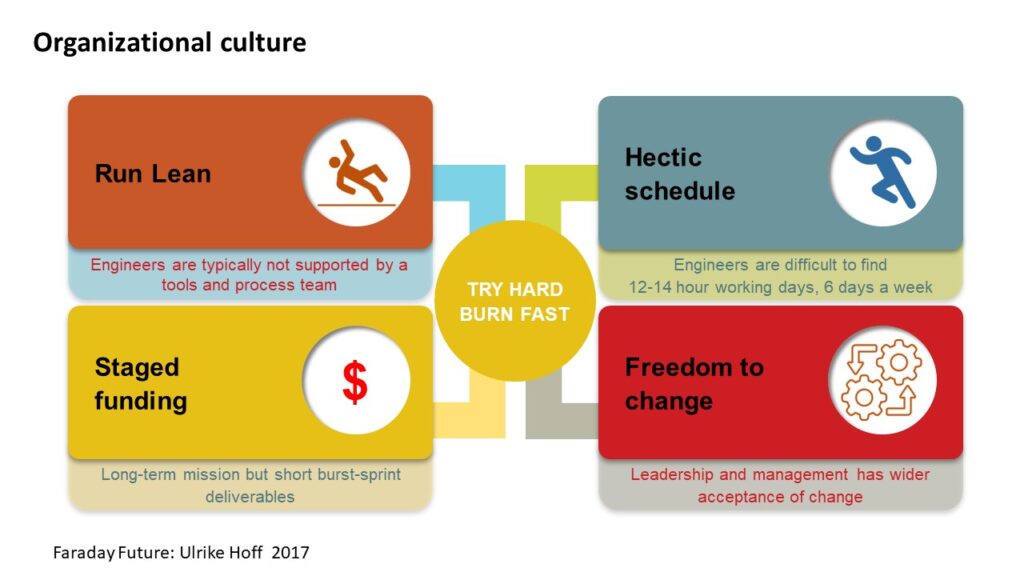
Figure 6: Attributes of an EV company in startup phase
Design instability meets manufacturing solidity.
These companies are sometimes so “lean” that one defection of an engineer to a competitor can throw the entire project into turmoil. Designers may be inexperienced at what a manufacturable harness looks like! Here lurks an opportunity for a manufacturing partner to provide a lot of value. Helping your OEM’s staff traverse that learning experience will hold down their costs and avoid quality problems – potentially leading to loyal repeat business.
The design engineers can be the most focused, brilliant and hardworking people you have ever met. The risk in running lean, however, is there may be insufficient people to complete the work given the project hours remaining. Wiring Harness Manufacturing partners have know-how which can help them avoid crises in timing. Moving out of a “build to print” arrangement into more of a “collaboration” role in the latter stages of design, while assisting them with early validation, will help OEM customers a lot. It presents an opportunity to be helpful in part selection, like the correct terminals or other cavity parts to be used. A myriad of other assistances with manufacturability preparedness are possible. Supply chain expertise and industrialization experience are at a premium in new OEM’s.
Manufacturing Partnership
The harness manufacturing process is still stubbornly resistant to many forms of automation. Still, more harnesses translates into more revenue. If your company is smart, efficient and has a sound pricing strategy, performance and profit will go in the right direction.
The solitary axiom of “make money for every mile of wire unspooled and manufactured into a harnesses,” isn’t enough. Your OEM customers are looking to reduce the practical minimum length of harnesses along with the number of the wires. Helping them to right size weight and number of circuits is a service they will appreciate and pay for.
Find the new business opportunities
EV/AV startup companies realize large suppliers can’t support their R&D phase without risking profitably. A smaller wire harness manufacturer might submit an elevated quote factoring in setup costs, tooling and factoring in low volume. An OEM’s alternative might be to set up their own wiring harness shop. A company awash with IPO money might indeed see in-house harness manufacture as viable. For a company living on venture capital funding for products yet to come to market prior to seeking another round of funding, insourcing is unthinkable. Recruiting and spending on space and machinery to make a few dozen wiring harnesses a month is wasteful.
EV/AV OEM’s thus typically lean towards containing costs by accepting whatever design assistance a manufacturing partner can offer. ‘Open to anything’ – from help with component library definitions to component recommendations, assistance in CAD drafting of release drawings and developing the release BoM can be on the table. Every aspect of the design for manufacturing workflow the manufacturing partner can help with is in scope to contribute to the win-win of having a trusted partner.
About The Author
Paul Johnston is a Portfolio Development Executive in metro Detroit, Michigan. He works with Siemens DISW’s Capital and Capital Essentials Electrical Design solutions customers who get value out of software automation from architectural studies and model-based systems engineering all the way through to manufacturing with digital continuity.