Strain-Relief: Design Tips for Durability and Aesthetic Appeal
You reach over to plug in your phone, and you feel that spark – and not in a good “I love this product!” kind of way. The wire is broken, and yet another charging cable is about to make its way to a landfill, while you have to make a midnight run to the store to be ready for your 6 a.m. Skype conference with Japan.
For such a simple idea, strain relief designs have a huge impact on users, right or wrong. And it’s not only in consumer products where we can blame gorilla-like users; even NASA has these issues. When you need your cables to last a long time, how can you create a reliable connector? Can you do this without demolishing that beautiful aesthetic your team has worked so hard on? The following tips will get you the answers you need, and still have you out the door in time for happy hour.
Why Do Good Cables Go Bad?
Tight bends in the cable near the connector cause high stress, fatigue, and failure. The stiff connector interfaces with a very flexible cable, and the point of contact ends up taking the brunt of the movement. Every tug is concentrated on a single point.
Strain is inversely proportionate to the radius of curvature – a fancy way of saying the tighter the bend, the more risk of failure. An easy way to visualize this is to take two paper clips out of your desk drawer and straighten them (for those who want a more detailed, scientific approach, check out the work done by The Royal Institute of Technology in Sweden). With the first paperclip, try bending the wire around a pencil, straightening it, and repeating this several times. The paperclip will bend easily, and is unlikely to break. With the second paper clip, make tight bends, back and forth, and see how many times it can be bent without breaking – my personal best is five repetitions. The lesson is clear: repeated tight bends = failure.
The Solution? Strain Relief
Strain-relief on cables offers mechanical support to the cable, protecting it from tight bends and fatigue loading. But how much is enough?
Of course, you can take the strain equations from bend radii, correlate the strain with stress using the modulus of elasticity of the particular cable material, look up values for maximum stress, figure in a safety factor for material variation, and arrive at a number predicting safe bending allowance for your particular cable. But unless you gain masochistic pleasure from second-order differential equations, I recommend something simpler: the 8X rule.
For any electrical cable, multiply the overall diameter of the cable by eight, and use that as your minimum bend radius. Of course, there are exceptions for shielded cables and multi-core shields, but this basic rule is accepted by the National Electric Code, and will get you the relief you need, without adding the cable’s stress to your own.
Okay, so now we know why we need strain relief, what strain relief is, and even how tight to make the bends. Can we simplify incorporating it into the design and get a shaken-not-stirred order on the way? Yes!
Common Strain Relief Designs
Strain on electrical cables has been around as long as humans have been channeling electricity for our own devious uses, and electrical strain relief designs have been around nearly as long. Today there are several common designs, each with some pros and cons.
Metal Strain Relief
Older designs involved the use of a metal spring surrounding the cable at the cable-connector junction. Simple and effective, just make certain when incorporating the springs into your design that the bend radius will be large enough when the cable is subject to common pulling forces. One of the great things about this design is its classic look, so this makes it a great option for cables in high-end consumer designs (Fig. 1).

Plastic Designs
Much more common these days are strain relief designs made of flexible plastic. While there are theoretically an infinite number of designs, most designs fall into one of three categories: one-direction, multi-direction and solid.
- One-Direction Strain Relief
No, we are not talking about using upbeat music to relax. But properly designed, this design is something to sing about. (Almost. Well, not really. Who sings about electrical designs?)

Uni-directional designs give bend relief in one direction while remaining stiff in the other (Fig. 2). A series of plastic segments which come in contact with one another create a minimum bend radius, and are very effective in that direction. Because this design allows for strain reduction in only one axis, the applications are specific: this design is very useful in applications like mechatronics or robotics where the cable will be bending the same direction every time.
- Multi-Direction Strain Relief
As with the design above, multi-direction strain relief relies on plastic segments limiting the bend radius, protecting the vulnerable connection (Fig. 3). This design, though, allows for movement in two or more directions, alternating the connection points between segments. Because of the flexibility of the design, this is the best option for most consumer products, and is widely available.

- Solid Strain Relief
Increasingly popular for mostly aesthetic reasons, solid strain relief can be seen on everything from lightning cables to vacuum cleaner cords (Fig. 4). While it looks great, this design requires extra caution, as often the strain relief area is too stiff, and the strain is concentrated at the junction between the strain relief and the cable. The key here is to make sure that the strain relief is flexible enough to allow the cable to bend inside the strain relief area, not at the junction. Even great designers can get this wrong.
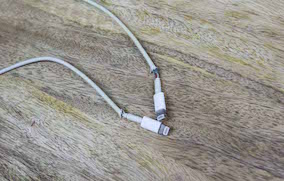
As an additional consideration, cleaning is simplest with solid designs, and so it becomes the only option for food, beverage and medical industries. Just remember to approach the design carefully.
Aesthetic Considerations
With every great design, form follows function, but follows so closely the two are nearly inseparable. Think beyond minimum bend radius and strength of materials to how this will look and feel to the person using this cable every day.
Some designs need classic industrial chic, and metal springs become an obvious choice. For others, sleek minimalism is the order, and solid strain relief wins. The multi-directional segmentation can fit with a playful, funky look (Fig. 5). Don’t be afraid to get more creative, experimenting with different sizes or even totally out-of-box designs, like the designer of the Snakables cables (full disclosure: I worked on the design of Snakables). For consumer products, this can be a chance to really stand out.

Manufacturing Considerations
Your design is almost complete. But before you put down your pencil and get ready for a chorus of “It’s Five O’clock Somewhere,” think about how your beautiful new design will be made. The options are simple: molded or slide-on.
Molded designs incorporate the strain relief directly into plug design, creating a robust unit. While this is attractive and can be very effective, it might require expensive 2-shot molding, and so is best for designs which will be produced in high quantities.
Slide-on designs are simpler, and can interface with existing plug designs (Fig. 6) . Many designs are available as off the shelf parts, and so are a great option for new products where your company is not ready to commit to custom tooling.

Additional Design Considerations
There are a few areas where you should pay more attention. Both the medical and food industries have special requirements for cleanability and materials. If your cables will go into harsh environments, you may need to use special materials, and also consider using much larger bends for extreme heat (where electrical resistance increases) or extreme cold (where brittleness increases). Each application has its own demands.
Prototyping Your New Design
All products go through iterations of design-build-test, and strain relief is no exception. Happily, most designs can easily be tested using 3D printing. For designs intended to be manufactured from an elastomer, try printing in a rubber-like material for testing. If your design is destined to be made of a rigid yet flexible plastic, you can print in a strong and flexible nylon material. Designs which will be molded can be printed in halves and glued together, while slip-on designs can be tested in nearly their final form. If you need more details, check out more articles on hardware design, as well as Fictiv’s www.fictiv.com.
What a Relief
Easy to design and vital to success, strain relief is just a matter of calculating your minimum bend and choosing the right style for your application. Make sure that the only spark felt with your product is from customers falling in love with a great design.