Muchas pruebas pueden juzgar la integridad de una conexión engarzada. Las pruebas de altura de engarzado miden la altura de un terminal engarzado y pueden revelar cosas como engarzado insuficiente o excesivo, desalineación de cables e inconsistencias generales en el proceso de engarzado. Las pruebas de tracción de cables revelan muchas de las mismas cosas que las pruebas de altura de engarce y también pueden revelar una selección inadecuada del calibre del cable o incompatibilidad de materiales. Por supuesto, una gran cantidad de pruebas eléctricas pueden revelar la integridad de la señal y la energía.
Pero si realmente desea profundizar para ver exactamente qué sucede dentro del engarzado, un análisis de la sección transversal del engarzado o micrografía es probablemente el más completo. Implica cortar el área del rizado y analizar la sección transversal con un microscopio con varios aumentos para ver los huecos, contar las hebras, verificar la simetría y tomar otras medidas para determinar la aceptabilidad del rizado.
Rob Boyd, jefe de desarrollo de productos de Schleuniger, habló sobre cómo la prueba ha ganado popularidad y cómo eso ha requerido un proceso simplificado. Rob comenzó señalando que los sistemas de micrografía existen desde hace mucho tiempo. “Empresas como Schleuniger (ahora Komax) solían fabricar productos de mesa grande con múltiples estaciones. El operador tuvo que colocar los terminales en epoxi, luego cortarlos y grabarlos con ácido”.
Luego, estas muestras deberán pulirse con un disco de lijado de grano fino para suavizar los bordes ásperos creados durante el corte. Señaló que el laborioso proceso inicial se utilizaba generalmente para determinar los parámetros de validación de engarzado cada vez que se diseñaba un nuevo terminal. Ayudaría a los fabricantes de nuevos terminales a establecer las alturas de engarzado óptimas en función de una sección transversal determinada. El trazado y medición manual de las geometrías internas eran tediosos y consumían mucho tiempo.
Rob analizó varios inconvenientes de las primeras pruebas. Además del aspecto tedioso de la encapsulación con epoxi, la preparación ácida tenía sus peligros. “Es una solución peligrosa que requirió una formación especial. Los operadores tuvieron que usar EPI y trabajar en un ambiente ventilado. Además, había que alejar la muestra del microscopio porque los vapores dañan el lente”. Otro inconveniente, señaló, fue que el ácido seguía corroyendo el material después del análisis. “Entonces, si tuvieras que regresar y volver a analizar la muestra en una fecha posterior, se degradará aún más.
No fue hasta que la prueba se hizo más popular que los fabricantes del equipo se volvieron más agresivos para simplificar el proceso. Rob indicó que fue un fabricante de automóviles en particular el que encabezó el cambio. “VW realmente impulsó el uso de sistemas de micrografía cuando exigieron a los fabricantes que tomaran una microsección con cada configuración. Los proveedores de arneses aumentaron significativamente la cantidad de microsecciones por día y, por lo tanto, necesitaban sistemas más rápidos. Mientras que antes lo hacían tal vez una o dos veces, o incluso algunas veces por semana, ahora lo hacían 20, 30 o 40 veces al día”. Por lo tanto, señaló, la mayoría de las empresas, incluida Schleuniger, ahora tienen sistemas más pequeños y menos complicados que son mucho más rápidos y minimizan la necesidad de grabado ácido.
Rob describió la evolución con más detalle. Para empezar, se acabaron los arduos pasos para encapsular la muestra en epoxi. Los avances en el corte de muestras han eliminado la necesidad de pulir. “Los sistemas antiguos utilizaban un sencillo disco de corte de fibra de vidrio, como los que se pueden encontrar en una herramienta Dremel. Estos no dan un corte limpio, por lo que es necesario pulirlos. El proceso es lento y los discos de corte se rompen fácilmente”, explicó.
Rob notó que las hojas de metal duro de alta calidad cortan limpiamente y, en la mayoría de los casos, eliminan la necesidad de un paso de pulido. “Para materiales como el aluminio, es posible que necesites una hoja con dientes más grandes y más separados. Para materiales más duros, usaría una hoja con dientes más pequeños y más juntos. Las hojas de metal cuestan más pero durarán mucho más y proporcionarán un resultado mucho mejor”.
Los avances en la tinción con pH equilibrado también han ayudado a eliminar de la ecuación las soluciones ácidas dañinas. “La tinción con las nuevas soluciones es un proceso electrolítico. Es bastante rápido y sencillo para la mayoría de las aplicaciones. La mayoría de las soluciones tienen un valor de pH de siete, que es el mismo que el del agua, por lo que es mucho más segura para el operador. Estas soluciones proporcionan un buen contraste entre el conductor y el terminal para la visualización”. Añadió que también es posible teñir la muestra bajo el microscopio sin grabar la lente.
Otro beneficio de las soluciones electrolíticas es que no degradan la muestra con el tiempo. “Puedes sacar una muestra después de que haya existido durante aproximadamente una semana y seguirá teniendo el mismo aspecto y dándote básicamente la misma imagen”, dijo. Esto es particularmente útil si se le pide que regrese y extraiga muestras de configuraciones anteriores.
Rob señaló que en algunos casos, como con el acero o el aluminio, es posible que necesite una solución ligeramente más ácida para obtener una imagen clara, pero que aún son menos dañinas que las antiguas fórmulas de grabado ácido.
Los avances en software también han simplificado el proceso. “Con los sistemas antiguos había que trazar el contorno del engarzado. También había que trazar el interior y realizar todas las medidas del trazado manualmente. Ahora tenemos un software que puede capturar automáticamente las dimensiones exteriores e interiores y realizar todas las mediciones en segundos”, describió. Teniendo en cuenta la cantidad de mediciones y combinaciones de cables/terminales, Rob reiteró que todo el proceso debe ser rápido y simple.
No todas las situaciones requieren el mismo nivel de detalle y Rob insiste en que los usuarios deberían poder seleccionar lo que se mide en el flujo de trabajo de medición. También mencionó que hay casos raros en los que las mediciones deben aplicarse manualmente, especialmente en casos donde el terminal y los conductores tienen un tono muy similar. Añadió que una buena fuente de iluminación puede ayudar a mitigar este efecto.
Una característica importante que Rob destacó como primordial al seleccionar un sistema es el paso del zoom sobre la marcha para la lente. “A medida que se acerca o aleja el zoom en terminales más pequeñas o más grandes, es muy importante que su sistema de lentes tenga una configuración de calibración para cada paso de zoom. Otros sistemas tienen zoom ajustable, pero con nuestro sistema, sientes un pequeño freno en cada paso del zoom. Es muy fácil estar un poco fuera de lugar si no tienes eso”.
Rob detalló además que en el 97% de los casos el paso de pulido se puede eliminar y se puede manejar con un equipo integrado compacto similar a su SawInspect System 6 (figura 1). En el SS6, la muestra se carga en el soporte en línea con la hoja de sierra. Después del corte, puede mover la muestra sobre rieles deslizantes desde la cuchilla hasta el microscopio, girándola 90° para permitir una vista perfecta de la sección transversal. Después de una ligera aplicación del colorante electrolítico, el software se hace cargo de medir y analizar la muestra.
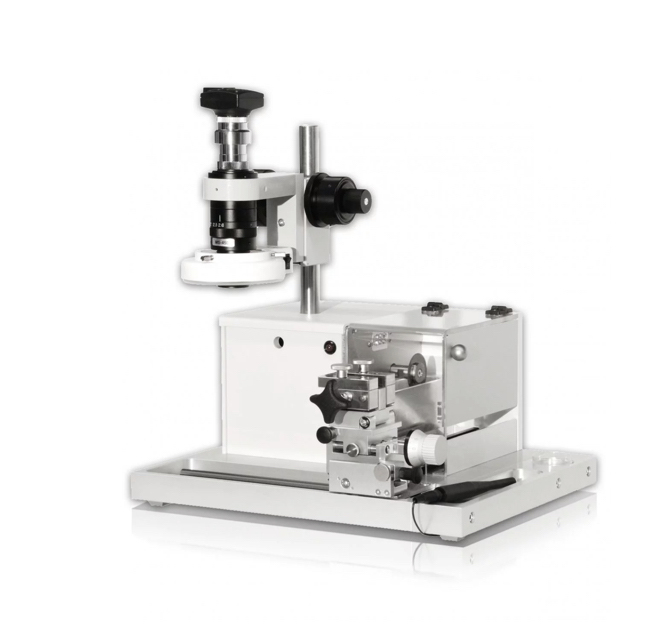
Para los clientes que necesitan fabricar grandes cantidades de materiales que requieren pulido, Rob señaló que Schleuniger y otros también ofrecen estos sistemas. “Komax” tiene la línea de equipos automatizados MICROLAB donde se carga la muestra y automáticamente la lleva a través de la sierra, el sistema de pulido, el proceso de lijado y luego al microscopio para su análisis (figura 2). Por tanto, todo el proceso está más o menos automatizado”.
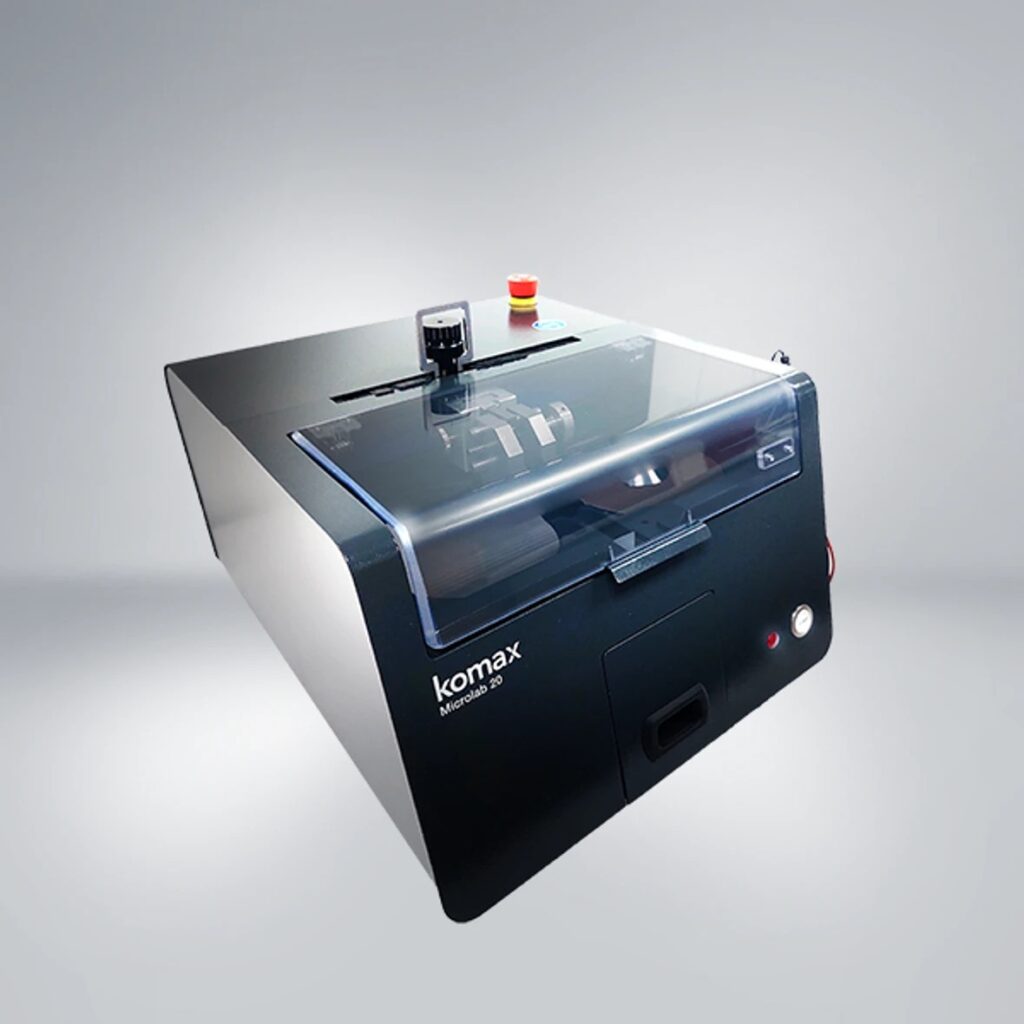
La capacidad de mirar dentro del engarce es muy esclarecedora y Rob mencionó que revela algunas cosas interesantes sobre las especificaciones del fabricante. “Los fabricantes de terminales están intentando utilizar el mismo cuerpo estampado y la misma forma de matriz para tantos terminales y cables como puedan. Por ejemplo, hay una terminal de registro de mantenimiento que se adapta a un rango de cables de calibre 20 a 14. Sin embargo, si miras el calibre 20 debajo de la micrografía, hay algo de espacio extra allí y está realmente abarrotado en la parte inferior. Los calibres 18 y 16 se ven muy bien, pero el 14 apenas mantiene juntas las alas engarzadas. No significa que no debas juntarlos, pero es útil saber exactamente qué está pasando allí”. Señaló que los estándares automotrices son mucho más estrictos y realmente buscan una bonita simetría en forma de “B” en el engarce.
Rob enfatizó que aunque el análisis micrográfico lo lleva al interior del engarce para juzgar su integridad, debe usarse junto con otras pruebas en una evaluación de calidad total. “La altura del engarce le indica si está engarzando según las especificaciones del fabricante. La prueba de tracción le indica cosas como la selección adecuada de los cables, pero cada prueba le indicará algo diferente”. Con mayores presiones sobre la calidad y la trazabilidad, la evaluación de la calidad total es definitivamente parte del panorama de la fabricación.
Muchas gracias a Rob Boyd por ayudarnos a compilar este informe. Si desea obtener más información sobre los sistemas específicos de Schleuniger o Komax, consulte Garantía de calidad o Herramientas de calidad en sus respectivos sitios web.