The Pursuit of Weightless Tools:
How shops are reducing occupational strain in all-day cable tie operations.
About three decades ago, automated cable tie application tools hit the manufacturing scene like a motorcycle in a bicycle race. Heads turned. Jaws dropped.
Until then, manually operated hand tools were the sole choice for manufacturers, wire harness shops and installers looking for ways to increase productivity in their bundling and securing operations. Hand tools are lightweight, portable and quite good at tensioning and cutting off cable ties.
Today’s high-volume shops have a unique problem, however, as these tasks can be repeated for hours at a time. Perpetually holding an arm out over a harness or assembly and squeezing a manual trigger leads to a greater frequency of employee injuries and the associated costs.
With the advent of the automatic cable tie tool, all the manual steps involved in applying a cable tie have been reduced to the pull of a trigger. Today, the entire process takes less than a second.
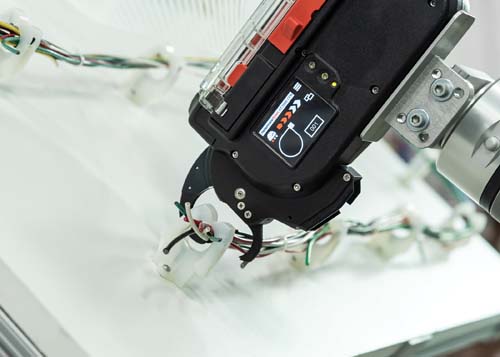
An operator assembling a six-foot wiring harness with multiple branch-outs, for example, can appreciate the impressive speed and repeatability of an automatic tool compared with a manual one. This is especially significant in applications where a single assembler applies hundreds or thousands of cable ties daily.
But just how maneuverable are these handheld machines, and can an operator comfortably use them daily without risk of developing a strain-related injury?
That pesky gravity
Just like the motorcycle versus bicycle scenario, all that power adds some heft. Depending on the tool, there may be an onboard motor or two, a cable tie feeder system as well as the necessary mechanical parts. The early automatic tools were quite heavy.
In today’s repetitive-strain-averse manufacturing culture, tool weight remains a hot topic. The most recent Bureau of Labor Statistics study found musculoskeletal disorders accounted for one-third of all worker injury and illness cases. These include tendinitis, trigger finger, shoulder and elbow injuries, and low back injuries.
“The shoulder joint is surprisingly weak,” says Jay Kapellusch, PhD, associate professor and chair of occupational science & technology at the University of Wisconsin-Milwaukee. “Anything more than 2.5 pounds becomes a problem if you have to use it repetitively, especially if you have to move the tool around a lot, which is typically the case with a cable tie tool.”
Naturally, being able to hold and maneuver the tool by hand is ideal for operations that require fastening along multiple points on an assembly. So, how can operators enjoy the benefits of an automatic cable tie tool without suffering arm fatigue or the resulting injuries?
Tool makers solve this issue in numerous ways – lighter materials, for example. Some have offloaded certain components from the tool, tethering them via cables and/or hoses to external base units that sit on the floor or are mounted to a rig. In the case of air-powered systems, there will also be a connection to an air compressor. This results in a much lighter tool for handheld operations. Of course, if mobility is important, users will want to consider how that method doesn’t allow the the tool to stray far from its base.
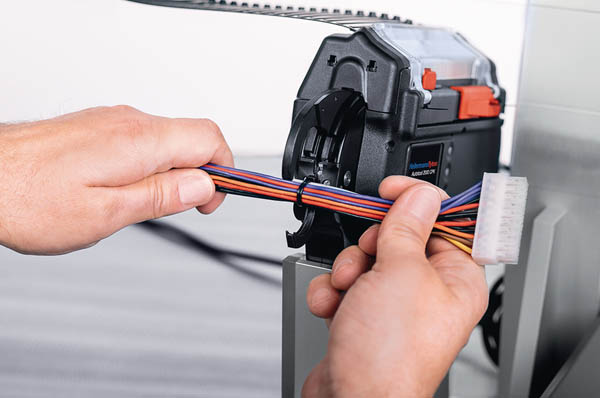
A different approach keeps all the parts on the tool. HellermannTyton borrowed from an industry standard suspension system when it developed an overhead rig that makes its 3.5-pound AT2000 CPK automatic cable tying tool virtually weightless. A “bail hook” mounted to the top of the tool connects to a “balancer.” The operator pulls the tool to the work by extending the balancer’s recoil line, and then can let go of the tool so it returns to its ready position. The suspension system installs overhead where space is typically underutilized.
Both approaches accommodate 5,000-tie reels to reduce downtime. Between the assistive technology and the ample supply of cable ties, operators can efficiently bundle wire and cables for extended periods without landing on the disabled list.
Going hands free
Sometimes, the freedom of handheld control isn’t relevant to the workflow. For operators stationed at a workbench, automatic tools adapt with a little help from another type of rig.
A bench-mount kit creates an ergonomic workstation for high-volume repetitive tasks such as applying cable ties around wire harnesses. Rather than the point-and-shoot method, the operator simply holds the bundle in place within the tool’s jaws. A dedicated foot pedal activates the tool.

With a bin full of wire harnesses beside the operator, throughput is greatly enhanced compared to attaching cable ties manually. Just as important, it’s much easier on the hands.
Many benchtop designs include an accessory to suspend the 5,000-piece cable tie reel, keeping productivity high for extended periods. And since the tool can be removed easily, users have the added flexibility to use it in a mobile workflow if necessary.
Going operator free
At the risk of sounding unsympathetic to the hardworking humans out there, automation in manufacturing continues to deliver gains in productivity and precision.
Robotic operations take fatigue completely out of the equation. Some automatic cable tie application tools are designed to fit right into the mix. They are typically affixed to a mechanical appendage, either stationary or reciprocating, with a mechanism to quickly cycle the tool as it moves across the work.
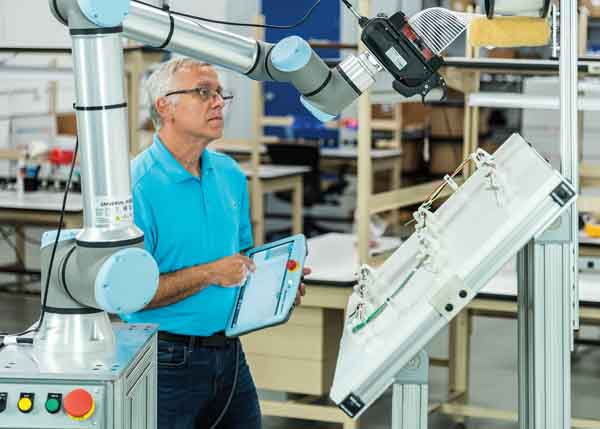
Larger manufacturing centers have found this to be an ideal addition to the workflow. It allows them to better utilize their operators in other processes.
The days of excessive operator strain injuries are becoming a thing of the past, thanks to assistive technologies taking the weight out.
About the authors
Mike Spanjar is a marketing copywriter at HellermannTyton North America. A self-professed tool geek, he writes extensively about the company’s full range of industrial cable management solutions.
Joe Roberts, HellermannTyton North America director of sales – tooling systems/OEM products, has been involved in the sales and marketing of tool systems for 18 years. He also currently resides on the board of directors for the WHMA/IPC Association.