In-Depth Look at Ultrasonic Wire Splicing
By Saeed Mogadam
In the age of electromobility and its fast-paced development, ultrasonic wire splicing continues to be up to all challenges presented by automotive industry. Through continuous development and expanding capabilities, it remains the best joining technology available today. Ultrasonic welding is a widely recognized and accepted joining process known best for its reliability, the most common applications being splicing and termination of wires to connectors (Figure 1) and is utilized in many industries – from transportation to aeronautical engineering and appliances.
Figure 1. Linear welds, copper, aluminum, combination.
Typically, applications are found in pre-fabrication, in the production of cable harnesses on the assembly board, and in the solidification of individual stranded wires. It has even become possible to link modern wire splicing systems directly to users’ manufacturing execution systems (MES), thereby increasing process reliability and making quality assurance easier. The service life of a car, which faces harsh environmental conditions such as constant vibration and extreme temperatures, depends on fault-free connections. In cases like this, ultrasonic connections offer both technical and financial benefits, including low electrical resistance, cost-effectiveness, and excellent corrosion protection.
Welding systems have also become very flexible over time. For example, copper-to-copper and copper-to-aluminum combinations in a variety of cross-sections can be welded with the same machine. There are also appropriate tools for twisted cables or multi-conductor cables with shorter stripped cable jackets (Figure 2).
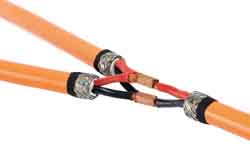
The automotive wire harness manufacturing industry has traditionally been the single largest user of ultrasonic wire spicing since the late 1980’s. An average wire harnesses contains 180 splices, and that number grows with each model year. OEMs are adding more electronic features to cars which require more splices. The splices and wire terminations together make up a long and complex heavy harness that controls the entire electrical system throughout the vehicle.
Wire splicing has always been a major focus in the manufacturing of wire harnesses due to the inherent labor intensity in wire processing. Splicing has provided a partial solution, but many splices are required. Mechanical connection (crimping) was the first method introduced for wire splicing, and it still has applications today. In some cases, the joints are dipped in solder to improve the crimped connection.
In the early 1970’s companies started to utilize resistance welding to join wires together. This process involves fusion (melting) of the material created by resistance to electrical current through electrodes.
In the late 70’s German wire harness manufacturers started to investigate the feasibility of using ultrasonic metal welding for splicing stranded wires. Soon after, American manufacturers adopted this largely unknown technology. Companies like Delphi Packard (APTIV), Yazaki, United Technologies (Lear) and Siemens spearheaded efforts to perfect this process because of the advantages it offered.
- Low temperature process does not affect material properties
- Pure metallurgical bond for many non-ferrous materials
- Ability to weld dissimilar materials
- No consumable materials such as splice clips or solder
- Environmentally friendly process
- Consistent weld quality, mechanical and electrical properties
- Fast cycle time
- Operator safety with no fumes or chemicals such as lead
The Process
There are two types of ultrasonic welding methods for metal and plastic. Linear welding is the more common technique used by all equipment manufacturers and a standard for the splicing of the wires (Figure 3). Torsional welding, developed by Telsonic, came into the picture over a decade ago. The torsional welding technique can be used for most common applications in linear welding. However, because of its unique capabilities, it has certain advantages in terms of the application’s geometrical shape and its gentle process that leads to a wider spectrum of applications in the market. In fact, this technology is sometimes found to be the only solution for electric car battery manufacturers and in the termination of high-voltage cables (Figure 4). Other examples where torsional ultrasonic welding proves to be the superior method are bus bars, 3D terminals and integrated gate bipolar transistors (IGBT).
Figure 3. Linear Welding Figure 4. Tortional Welding
How it Works
Ultrasonic Wire Splicing
The wires are stacked between the vibrating/oscillating tool (sonotrode) and the anvil block. They are confined in a pre-determined space before the static force is applied through the anvil. As oscillation ensues, the metal surfaces heat up, plasticize, and the strands are bonded together by inter-mingling at the molecular level (Figure 5.6).
Figure 5. (left) The vibration and motion involving ultrasonic linear welding of metal.
Figure 6. (right) Illustration of the splicing process.
The result is a continuous weld with a finely grained structure similar to the structure of cold-worked metals. The entire process is very rapid, with welds typically completed in a fraction of a second. Most common splicing machines used today are operated at 20KHz frequency mechanical vibration. The vibration under the force dissipates any contaminants and starts the cold friction welding until the splice is completed. The temperature rise of the welded material is less than 30% due to the friction force at the welding interface. Therefore, there is no hardening of the wire material which makes the wire strands brittle in the weld transition area. This is one of the many advantages over resistance welding which involves melting of the material to make the splice nugget.
Basic Welding Parameters and Variables
Wire splicing with ultrasonics has also proved to be a high-quality and safe in practice. Because the welding parameters can be adjusted and monitored as appropriate for the application in question, this is also possible in Industry 4.0 environments now.
Welding Parameters:
In addition to the condition of the welding tools and dimensions that are always predetermined, there are four welding parameters that need to be set up. These parameters are normally predetermined by a default given by the machine controller to begin the qualification of the weld quality.
- Width of the weld: Set up by the machine
- Weld energy: The fixed number of watt-seconds to be delivered to complete the weld
- Amplitude: The oscillation that can be adjusted up to 100% capability of the sonotrode
- Force-pressure setting: To set the welding force
Quality Variables:
In order to control the process for the best quality when welding with fixed energy, the following variables are measured and are compared to the upper and lower allowed limits determined by the machine or the user.
- Weld time (duration of welding)
- Compaction height before ultrasonic is started
- Final weld height
- Power consumed
Stable Production and Data Integrity
There are other features that increase production reliability for wire splicing (all the following features are available on Telsonic machines). All splice data should be stored by the machine and preferably backed up on a local network for quality analysis and customer audits. The panel PC should be fitted with an uninterruptible power supply (UPS) as a standard. This provides protection against voltage drops. The data for the last splice completed is saved even in the event of a power failure and the PC is shut down in an orderly fashion. This safeguards the data integrity of both the Microsoft Windows operating system and the system software (TelsoSplice® in the case of Telsonic machines). The splicing unit pneumatics are also monitored. An automatic under-pressure detection function warns the operator if the pressure is too low and stops production until the fault has been rectified, thereby avoiding the expense of rejects. Moreover, the wire splicing systems support numerous options to help increase production ergonomics and operator convenience. For example, the multi-conductor splice kit streamlines material handling during the welding process for an operator, thus reducing reject parts. There is a bad part cutter to destroy incorrect splices, preventing them from ever being passed as a good part. The optional capability to interface with a shrink oven is a practical consideration for using the correct shrinking parameters per splice which ultimately is a great improvement from the traditional heat guns that have the potential of sealing splices incorrectly. This adds to production reliability, because faults of this nature would otherwise not be detected until the final check stage.
Ultrasonic metal welding is a crucial process for all aspects of wire harness assemblies due to its ability to provide a reliable bond to meet all low and high current carrying characteristics. Therefore, certain standards and specifications have been prepared by individual companies. USCAR 45 for Ultrasonic Wire Splicing is one example, as well as other specs that can be applied to most industrial products in the market.
About Telsonic
The Swiss Telsonic Group has been offering its industrial ultrasonic solutions through representation in Europe, America, and Asia since 1966. Constant innovations help to ensure that, in many applications, Telsonic has established a lead over competitors that offers added value to customers. With over 250 highly qualified staff, the owner-managed company specializes in plastic and metal welding, cleaning, and sieving for customers in fields such as automotive, packaging, and medical technology. Visit www.telsonic.comfor more info.