Usually when we think about cables and movement, we think about cables inside a train, plane or some other vehicle traveling at various speeds. But what about when the cables themselves do the moving? Motion is what igus is all about. igus is a German manufacturer and distributor of linear guides, cable carriers, continuous-flex cables and both plain and spherical polymer bearings. Worldwide, they employ just under 3,000 with 430 of those working out of their 189,000 sq. ft. Rhode Island facility. Many of the flex or dynamic cables that igus makes go in their self-lubricating plastic guides and carriers. Because they have achieved such proficiency in dynamic cable assemblies in their own products through the years, that business has become a strong, stand-alone product line.
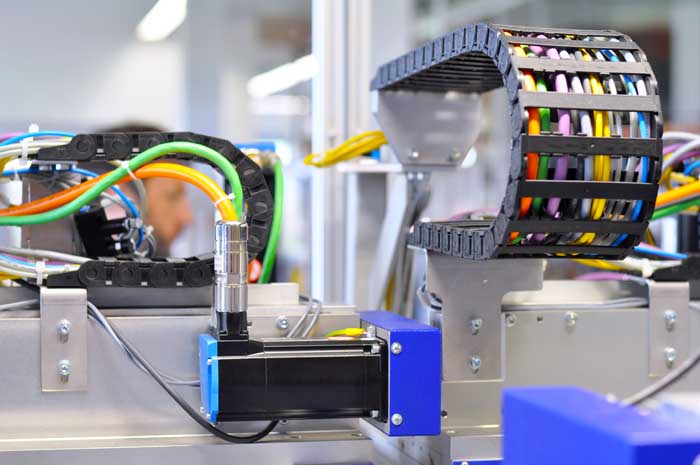
Wiring Harness News recently spoke with Joe Ciringione. Joe is the igus Division Manager for Energy Chain Systems (ECS), which includes their e-chainÒ cable carriers, cables, cable assemblies and connectors. Joe spoke about the specific guidelines for manufacturing their chainflexÒ dynamic cables, as well as some salient points about the igus business model.
Joe dug right into what makes their dynamic chainflex cables unique by discussing the selection of jacket materials. “Most static cables use rubber jackets like neoprene that have great high and low temperature resistance, but you can wear through them quickly.” igus has done extensive research into the way cable jacket materials wear on the crossbars inside their e-chain and have found that certain polyvinyl-chloride and polyurethane blends that are abrasion and UV resistant work best. Likewise, core insulation materials must be made from similar abrasion resistant materials to achieve peak efficiency in multi-axis movement.
The actual strand design of the cable itself is also very important. Joe mentioned it’s actually not super-fine like many may think. “It’s not the smallest, finest stranding you can get because that actually does not have a good tensile strength, so over time, and over longer travel distances, it’s not as good as fine to medium stranding,” he explained.
The way the conductors are wrapped inside of the cable is also unique in two ways. “First, we braid or bundle it around a strain relieving, high tensile-strength fiber core. That helps to prevent the conductors from kinking as you bend the cable.” igus also designs the cable with a very tight or high pitch, meaning the number of times it wraps around the core over a meter distance is relatively high. “Think of a telephone cord or something like that,” Joe described. “The tighter (higher) the pitch, the easier it will flex and bend. Whereas if with a longer pitch, it’s almost like a coat hanger and will have a tendency to break over time as it bends.” He added that cables with a comparatively lower pitch are inexpensive to manufacture because they are produced very quickly compared to higher pitch cables.
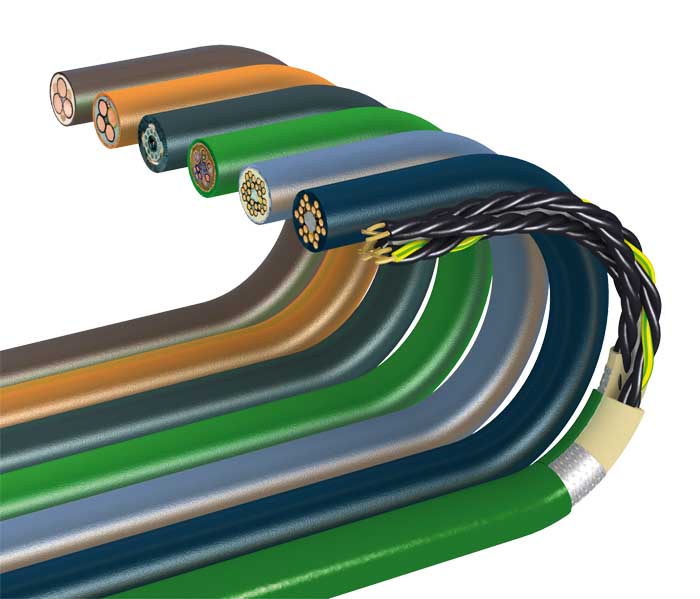
Joe then mentioned the unique inner jacket in their chainflex cable. “We don’t use any textile wraps between the outer jacket and the inner conductors. Static cables use a cloth-like wrap. We actually use a powder-like talc instead of a wrap because we found that in dynamic applications, textile wraps tend to bunch up inside the cable and cause failures.”
The conversation turned to the special shielding used in dynamic cables at igus. “Most standard shielded cables use a longer braiding compared to the much tighter braiding we use. The longer weave braids work great as an effective shielding for electrical properties, but they don’t perform well mechanically when you bend them,” Joe instructed. “Tighter braids use more copper and are more expensive to produce, but they provide a much higher quality shield for dynamic applications.” He pointed out that this optimized braid angle prevents the shield strands from breaking over the linear axis and increases overall torsional stability. igus shields have an optical coverage of about 90%.
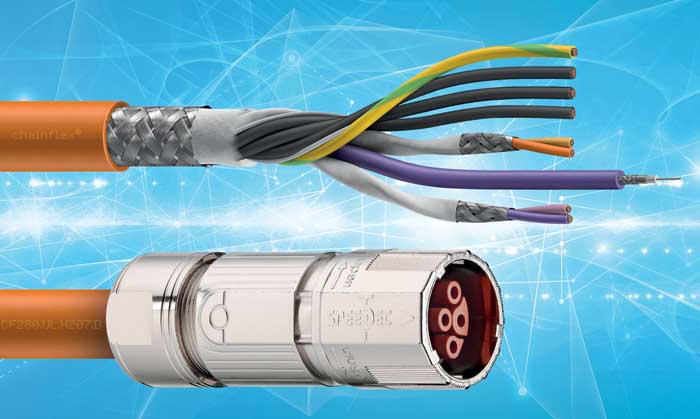
These exacting details mean igus cables are rated for up to 10,000,000 cycles of flexing and rolling. With proper installation in an igus e-chain, they can achieve an operational travel range of up to 1,312 ft. Cables are available that are oil and bio-oil resistant, flame retardant and hydrolysis and microbe-resistant, which are critical features in many applications. The cables also have a very small bend radius compared to other cables which means they will not need as much space for operation.
Because of the years of field experience, coupled with rigorous in-house testing, igus has no qualms about standing behind their products. “We actually offer a three-year flex life guarantee, and nobody else in the industry does that. That’s because we do the testing and we are confident that these cables will work, and we get almost zero returns.” Joe mentioned they can tweak these design parameters to address specific needs and they also produce less expensive cables for less stringent dynamic applications.
We then began to focus on the typical igus customer. “Our ideal customer would be a manufacturer of automated machinery. That’s a pretty broad term as automation equipment extends across many industries,” Joe cited. igus has customers in the entertainment, food and beverage, construction machinery and energy sectors. You will find their products on amusement rides, stadium roofs, at busy seaports and on oil platforms. Basically, anywhere there is movement, igus products are in action.
Another aspect of their business is with motor control cables. igus stocks motor cables for the top five brands of motors. “You can call us and say, ‘I have a certain Allen Bradley motor,’ and we will have the part number for that in our system.” The cables will come complete with the OEM connectors and are also available in catalog form on the igus website.
There are situations where igus builds static cables. Although it’s a much smaller part of their business, they end up building a sizable amount. “There are some that run into pretty high volumes,” Joe outlined. “They usually have a lower dollar value as they don’t use the more expensive cable, and we do them in situations where we are already providing a customer with a dynamic cable and we don’t want them to have to look for another partner.” He noted they use virtually the same tooling for these assemblies as they do for chainflex.
igus realizes that as automation is on the rise, many contract manufacturers of traditional static cables get requests for dynamic cables from their customers. “When that happens, they often pick out a cable that doesn’t work very well in that application because those companies don’t have the experience putting wire through a cable carrier like ours,” Joe stated. In order to provide the best outcome, igus is happy to work seamlessly with the harness manufacturers for the best solution. “Actually, there are a lot of harness houses that buy our e-chain along with our chainflex cable and do the work themselves,” he detailed.
As far as connectors, igus uses a lot of TE’s Intercontec plug & play type connectors for power, signal, and data connections. “It’s all customer specified, but those are the common connectors for automation,” Joe revealed. They also use a fair amount of RJ connectors for data communication and MIL-SPEC circular connectors.
In a world quickly ramping for automation, igus seems well poised for growth. “There are exciting new developments in technology to address some of the global challenges that we are facing that will use our products like robots that can disinfect a hospital room to prevent the spread of viruses, and ship to shore cranes that can offload container ships faster at seaports to reduce their backlog and help improve the speed of the supply chain.”
Anywhere there is moving energy, there will be a need for high quality cables that last.