By James Dunbar, Product Marketing Manage – PCC, Phoenix Contact USA
Having problems with tinned wires coming loose in screw terminal block? Many companies and manufacturers use the practice of solder-dipping wire ends, but this can lead to loose connections. Beyond ensuring that all screws are tightened to the proper torque specification, this document shines light on why your tinned wires are coming loose.
Moving away from tinning and exploring other ways to prepare bare wire could save time and the headache of retightening connections.
Why tin wires?
Stranded copper wires are commonly connected to PCBs or other devices with a screw-style terminal block. “Tinning” is the practice in which a stripped wire is coated with a thin layer of a tin compound. However, there is the associated problem of the wire becoming loose when used with screw-style terminal blocks.
One common reason for tinning is to prevent wire strands from fraying when connecting to the termination site. For example, stranded wires can be tedious to work with when pushing into the cage of a screw-type terminal block. In this case, there is the possibility for wire strands not to be pushed all the way into the cage, which could cause a short. If the wire will be frequently installed and removed from its termination site, the wire can become increasingly difficult to work with. Tinning might appear to be a good solution.
Why does tinned wire become loose in screw terminals?
Root Cause:
The root of the problem stems from when the wire is tinned and the tin material flows into the small space in between the copper stands of the wire. This makes the copper wire and tin into a solid mass of material.
Once the wire is inserted into the terminal block, and the cage closes and clamps on to a tinned wire, the tin/wire block is compressed and can change shape. In doing so, the tin can fracture and cause wire strands to pull apart from one another, creating voids (Fig. 1). Essentially, as the wire is screwed down, it breaks apart the tin, which can start to loosen the wire. While the wire may be secure initially, normal operation can cause the wire to become loose.
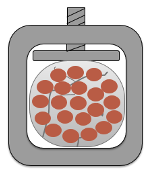
Operation and Thermal Expansion
- During operation, wires will heat up and cool down as the environment heats up and/or current flows through the wire. As the wire increases in temperature, thermal expansion can be the culprit behind loose terminations. The higher temperature in the wire and the tin material causes the metals in each of them to naturally expand and take up a larger volume. However, the material properties (coefficient of thermal expansion) cause the different metals to expand different amounts. In this case, the tin material expands more than the copper cage (Fig.2).
- As the metals cool, they shrink and take up less volume. The expansion and contraction can cause the shape of the tinned wire to change slightly, and no longer be properly clamped between the cage and pressure plate (Fig. 3).
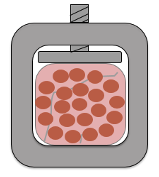
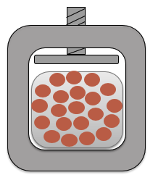
Other Common Misconceptions
Tinning wires will increase corrosion resistance.
Yes…but when the tinned wire is compressed in the terminal, the tin breaks apart, so that the connection might no longer be gas-tight. Bare wire strands will create a better, gas-tight connection, and can be a more effective way of reducing corrosion.
Tinned wires will still fit into the terminal block.
In some cases, added material will prevent the wire from fitting properly in the block. Adding tin can make the wire larger than the terminal block is rated for. This will prevent terminal from properly closing/clamping on to the wire.
Final Thoughts
All things considered, tinning wires could be the reason for loose connections in screw terminal blocks. While tinning does have benefits, there are better alternatives that could save you the headache of loose terminations. A great alternative is to use ferrules and ensure the screws are tightened to the proper specification.