3D printing technology offers several opportunities for the wire harness industry. WHN interviewed David Tucker, Director of Additive Manufacturing at MasterGraphics. David is certainly well credentialed in the industry having worked for ten years in the digital manufacturing realm. Before that, he spent time in traditional manufacturing in the automotive industry. He has worked with companies making equipment and parts as well as for those looking to create a business model around additive manufacturing.
David has worked many projects in our industry and sees the technology fitting into four categories. “The first is the electrical connector and these are typically done in low-volume applications on DLP printers. They are area-based printers with liquids that have really fine details associated with them,” he began. These printers use a photo polymer resin liquid that can cure under a light source. David referenced a particular automotive need where a trailer tow connector cap was needed. It was a low volume application requiring USCAR2 validation to guarantee its integrity against extreme elements. Using carbon digital light synthesis, they were able to reduce the cycle time by 50%. It met all the performance requirements previously met by traditional injection molded pieces.
The second major category of applications for 3D printing David discussed is the creation of custom jigs and fixtures for harness production. “That’s actually a huge application in the production of wire looms, and I’ve seen companies like Aptive and Yazaki make extensive use of powder bed fusion printers for these fixtures.” David explained that this 3-D printing technique can produce a vast array of geometrically complex products using a heat source, usually a laser, to diffuse metal or polymer particles layer by layer to form a complete part.
The third category where David sees extensive use of 3-D printing, especially in the electric vehicle space, is where they’re integrating high-voltage and low-voltage systems inside an EV. They often need special wire routing guides to route and separate these wires.
The fourth area where David sees the greatest potential for 3-D printing in the automotive electrical interconnect system is with digital hybrid components. He described these as perhaps an enclosure that might incorporate multiple functions in one assembly. “This would be where you had, for example, a fluid motor that has an electrical connector on the side. I’ve also seen, especially in autonomous vehicle arena, where people are using 3-D printing to create enclosures that can package up electronics in a nice formfitting way. And that’s very interesting because it’s digital hybrid thinking in component design.
These new tech-heavy components make a strong case for additive manufacturing, especially in the design and prototype phase. “Things are being created that were never there before and it requires disruptive versus incremental innovation,” David said. “With the use of LiDAR in autonomous vehicles, there is a need for sensor cleaning where the washer fluid is heated and used in very specific cleansing mechanisms. You are integrating those in electrical systems inside the vehicle and packaging them, which naturally brings up the need for 3-D printing.”
Rapid prototyping, the ability to create complex geometries, cost savings and design freedom are all strong reasons that make a business case for 3-D printing. But as David points out, there are limitations. “I think a lot of 3D equipment manufacturers want to trick the user into thinking that additive manufacturing is limitless in scale, but there is a limit. It depends on the part, the size and the application, but realistically it’s around 3000. At that point you should really be thinking about other methods.”
The discussion then touched on making that transition to higher production methods like injection molding or stamping. David advised that the original 3D design should take this eventual transition into account. He used Tesla’s gigacastings as an example. “[Tesla] validated a digital manufacturing process material that they used inside a low-volume casting process to make sure it correlated to the high-volume casting process so they could guarantee the same results. It’s the same case study whether you’re talking about a massive casting or a little connector.”
This was a good point for David to discuss the two major categories of 3-D printers and provided some detail. The first category he spoke about was FDM (Fused Deposition Modeling and FFF (Fused Filament Fabrication. “This is where you have a heated nozzle extruding a material are it’s mostly what people have in their head when they think about 3D printing. You have a point, and that point is moving in an X and Y axis to create layers to build the part,” he explained.
David then pivoted to SLA (Stereolithography) and DLP (Digital Light Processing). “These are area-based printers that use liquid resins that have really fine details associated with them.” The liquid resin is hardened (polymerized) layer by layer using a light source (UV laser in SLA or UV projector in DLP). The object is built upside down in a reservoir of resin, with each layer being cured by light to form the final 3D object. “FDM/FFF parts can be grainy and have a fair amount of surface friction. But the SLA/DLP processes are pretty smooth by comparison,” he detailed.
As far as cost, David indicated 3D capability can be acquired inexpensively. He did admit that some of the more sophisticated area-based printers using polymer infused metals can be upwards of $40,000. “Those aren’t cheap by any means,” he clarified. “But these days you can buy a really good desktop printer for about $1,200. There’s a company called Bambu that makes a great low cost 3-D printer. There’s another company called Prusa that makes another really solid one, and it’s around 600 bucks.”
Most David’s experience in this field is automotive, so clearly that was the focus of the examples he spoke about. But he was quick to point out that the same innovations are going on in the medical and aerospace arenas. He reiterated that the creation of jigs and fixtures are the low-lying fruit for harness manufacturers.
3D Printing at Harness Producsr, Heltronics
Daniel Helder, Owner of Heltronics, a harness producer in central PA, talked about the use of 3D printing in his business. “It all goes back to my previous employer where we built sockets for relays. We used 3D printing to get production started for our customer. Now, at Heltronics, we use it for a lot of fixtures and some prototyping,” Daniel began. “We have done a lot of fixtures like a simple one that is bulletproof in cutting wire leads to the proper length every time. We just made a little block with a trench, and then cut the wire off at the end with a flush cut. It takes about 15 minutes for us to design and build something like that. We send it to the 3-D printer, and an hour later check in make sure it works and maybe make some adjustments.”
This ability to design and produce things quickly as also given Heltronics, an edge, when it comes to value-add business. “We have a customer that makes protective hood for arc flashes needed for operating high voltage breakers and other high-voltage electronics. Usually those environments are very hot, so they came to us with a design for a fan unit with a switch,” Daniel explained. The company was looking at $15,000 in tooling cost. “I suggested a better investment would be to use 3D printing. I’d done it before, and I knew we might need to switch up some material and designs. We have been continuously building that product and there haven’t been any returnsHeltronics.”
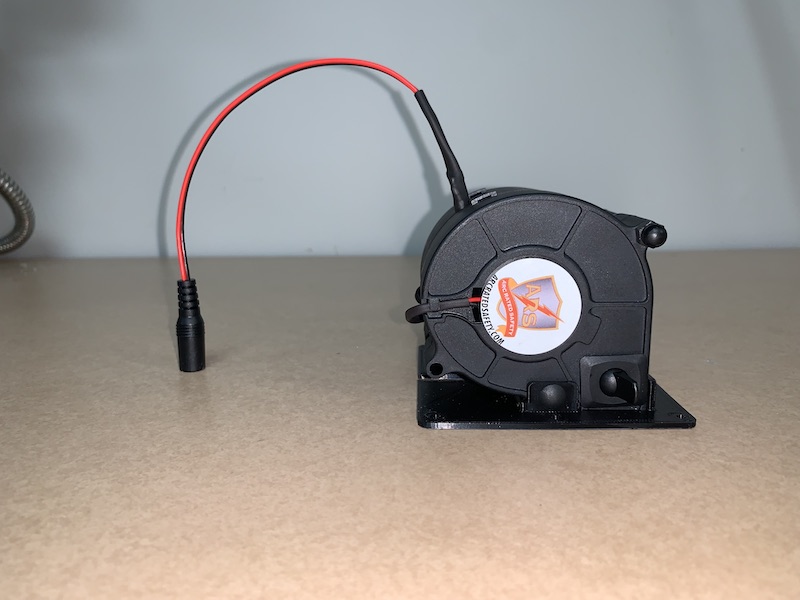
What Daniel likes about making products for his customers, or jigs and fixtures for his business is that he can choose materials that are biodegradable or recyclable. “If you’re doing a lot of prototypes or fixtures, there isn’t big environmental impact,” he advised.
Daniel sometimes makes custom add-ons for their existing wire processing equipment with his 3D printer. “We have a Komax lead maker and we had a problem with the cutoffs flying everywhere and collecting in a big pile. We built something that resembles a rain gutter where the material falls right in and gets funneled into a collector.” In yet another application, Daniel has built L-shaped spacers they have drilled to a table to separate wires before they start assembly.
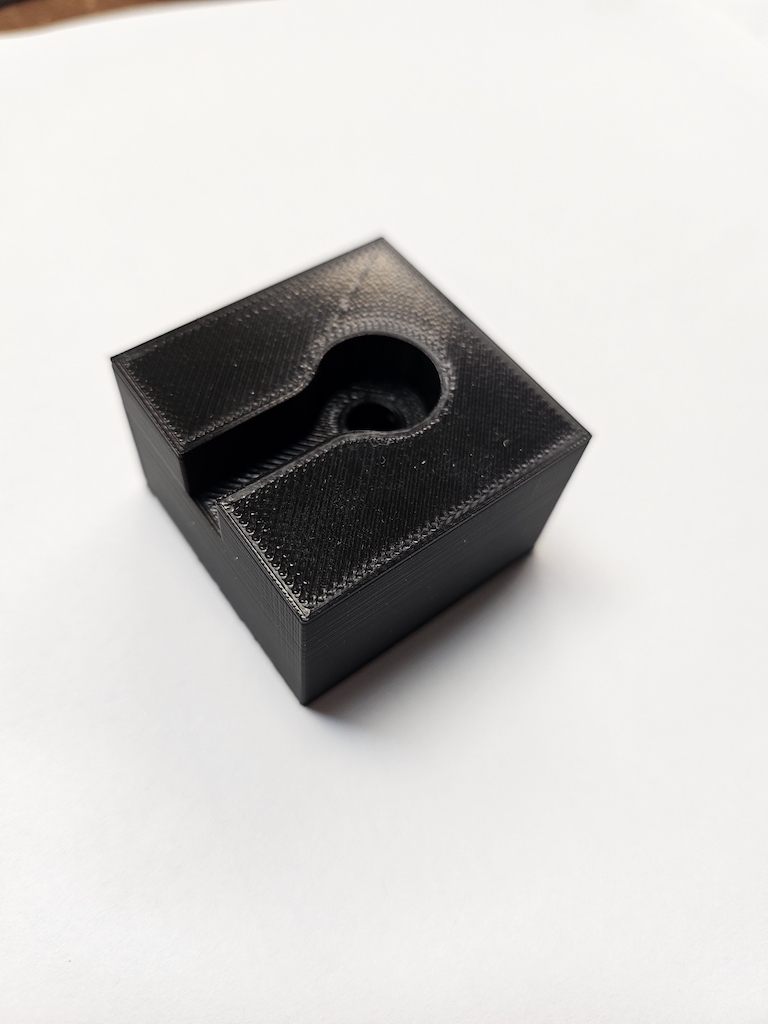
Daniel reiterated David’s assertion that you can get into 3D printing fairly inexpensively. He mentioned the equipment has come a long way in the past 10 years. Previous equipment required a fair knowledge of CAD but he indicated the newer equipment has greatly streamlined the design process.
*