With over 50 years of expertise in resistance welding of non-ferrous metals, STRUNK Connect is a renowned manufacturer of customized machines.
Our competences are focused on following resistance welding technologies:
-wire compacting and splicing
-hot crimping
-terminal welding,
-welding under braze
-micro welding,
-diffusion welding of copper foils
-welding of Aluminum stranded wires into Copper sleeves/cable lugs: HC-L
-butt-welding of Aluminum busbars and Copper busbars with our innovative S2R technology.
Above mentioned technologies enable extremely reliable and high performance connections for various fields of applications:
power distribution systems, HV wire harnesses, Inverter systems, Storages / Batteries, E-traction for stators and rotors, AC/DC charging applications, sensor signal transmission and many others in various industries: e.g. Automotive, Commercial Vehicles, Marine, Aerospace, Home Appliances, etc.
Our long-term expertise enables us to support the product development through all stages of the design process: from product idea and prototyping phase till samples production and the industrialization via manufacturing and supply tailored machine and automation.
STRUNK’s solution portfolio ranges from bench top machines, semi-automated units to fully automated machines with optional process chaining.
Versatility of resistance welding: overlap welding and butt-welding (BILDER)
Aside of the known resilience with respect to surface contamination of the joining partners, resistance welding shows as well its versality as for welding of busbars following joining approaches are possible.
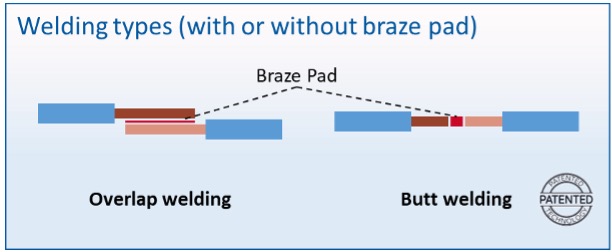
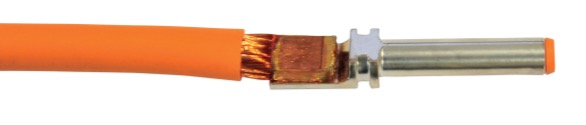
Example for overlap welding

Example for butt-welding
While overlap welding approach is quite common, butt-welding gains more importance.
The main drivers for this trend are:
– significant reduction of height of joint area
– reduction of material usage as only the functional connection area is welded
In addition to above mentioned benefits, the performance of the butt-welded joint regarding power transmission (voltage, current) and mechanical strength (e.g. pull force) is similar to overlap welding.
Depending on the material properties and coating of the joining partners, the resistance welding can be processed either without or with braze foil, which then diffuses into the joining partners during the welding process.
Welding of flex busbars: foil welding
Flex busbars, otherwise known as flexible HV connectors, are used in the field of e-mobility for power distribution. They consist of stacked individual foils with a thickness of approx. 0.1 mm to 0.5 mm in any number or of layers in the desired cross-sections and connection area. These stacks are usually welded on both ends and the flexibility depends on distance/length, number and thickness of foils.
Although the flex busbars are basically only flexible in one direction, they provide valuable benefits and can even be bended as well. This serves the purpose of reducing potential vibrations as well as facilitate assembly and disassembly of busbar systems.
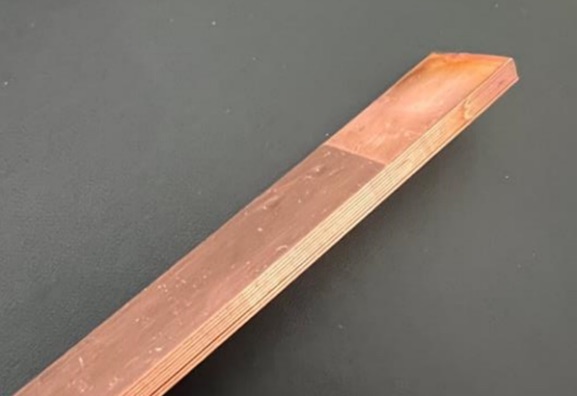
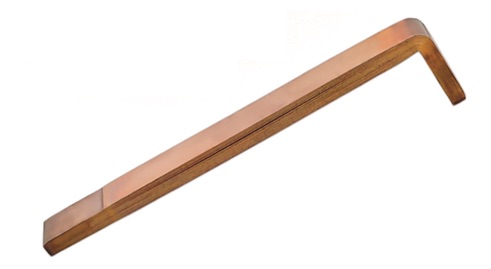
Examples of welded foils with a thickness of 0,2mm each without any oxidation
STRUNK supplies solutions to weld the ends of a stack of foils over large areas of up to 1,000 mm² without direct cooling of the components. The cycle time for the welding process itself ranges around 2 sec or less depending on welding area. Furthermore, no brazing material is needed.
Resistance welding of Aluminum and Copper: Aluminum stranded wires into HV copper contacts
Our innovative solution enables a secure and durable connection between aluminium and copper and allows in particular the joining of:
– Aluminium stranded wire connections into HV copper contacts (sleeves or cable lugs)
– Aluminum busbars to CU-Terminals or wires in S2R butt welding technology (fully scalable)
Both above mentioned joining types provide solutions that combine the best features of both worlds:
-Copper contacts and terminals: proven, mechanical reliable and high performing interfaces for HV-applications and LV-applications.
-Aluminum busbars and stranded wires: weight savings and significant material cost reduction while meeting the conductivity requirements.
NEW: Recently, we executed the welding of enameled Aluminum stranded wires into HV copper contacts successfully. This means a significant benefit of saving one complete production process step. So, removal of enamel by mechanical methods or by laser prior to the welding process is not necessary anymore.
This saves production time and reduces CAPEX: no investment in additional enamel removal machine and reduction of overall footprint.
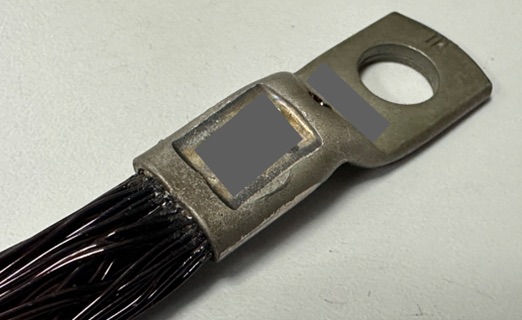
Enameled Aluminum stranded wires welded into copper cable lug.
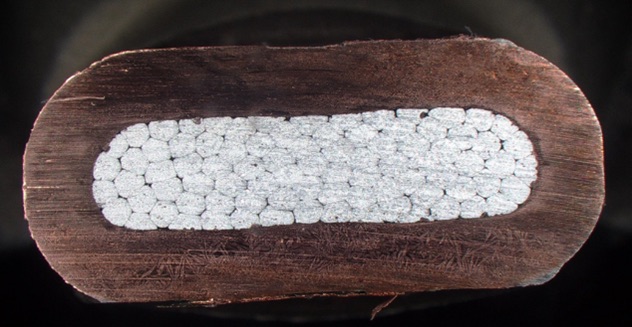
Micrograph displays that there is almost no residual enamel and excellent bonding between the Aluminum stranded wires as well as between Aluminum stranded wires and the copper sleeve.
This enables excellent long-term stability with high pull forces and minimum resistance.
Summary
Although resistance welding is a mature technology with a wide variety of applications, there is room for innovation and progress. Especially the increasing requirements towards reliability and safety of connections in HV applications and the overall increasing trend of electrification drive more and more attention to resistance welding as an efficient technology to meet these requirements.
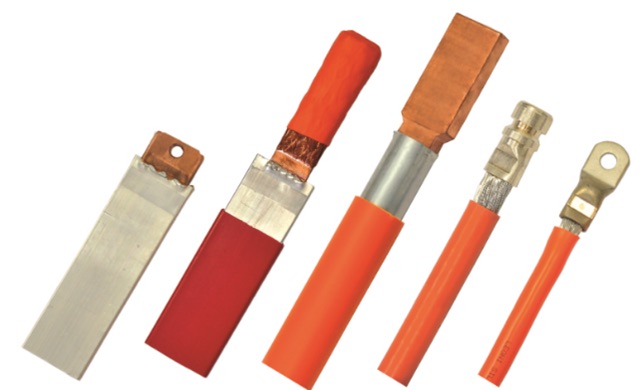
In addition, our Aluminum-Copper resistance welding solutions pave the way for new HV applications in different type of vehicles: passenger cars, commercial trucks, airborn applications, and even marine applications.