Unfortunately, reworks and returns are a reality for every wire harness assembler. Any manufacturing company should have some kind of process for handling returns authorization (RMAs). However, not all companies have well-defined, integrated workflows to guide these processes efficiently. In any given Return Merchandise Authorization (RMA) situation, there are multiple paths a product can take—from reworking a defect to issuing a refund. Ideally, you have a proven, structured process that dictates how each of these paths unfolds, minimizing delays and confusion.
More importantly, these RMA processes should be seamlessly integrated into your broader business operations. This means linking RMAs with internal purchase orders to track incoming materials, generating manufacturing rework orders to handle defects, and issuing credit memos when necessary. When these processes are properly integrated, they not only streamline rework but also reduce the impact on your company’s profitability, resource allocation, and customer relationships.
This article will review best practices for managing RMAs and reworks, focusing on how these practices can positively affect the business as a whole, from improving operational efficiency to enhancing customer satisfaction.
The True Cost of Rework
Rework introduces both direct costs—such as labor, materials, and shipping—and hidden, unplanned expenses that can significantly disrupt a contract manufacturer’s operations. Coordinating across multiple departments like sales, quality control, and production creates a heavy overhead burden, diverting resources from revenue-generating activities. Rescheduling rework into the shop floor’s capacity often leads to delayed deliveries and impacts overall production efficiency.
Frequent RMAs also pose a major risk to customer relationships, especially in contract manufacturing, where reliability and ease of service are critical. Disrupted schedules and missed deadlines can jeopardize contracts, particularly in regulated industries with strict quality audits. Over time, repeated rework incidents can damage trust, erode your reputation, and hinder future business growth.
Research conducted by Cetec ERP shows that RMAs typically account for around 3.44% of a company’s revenue, affecting 4.72% of all shipments. For a wire harness company with $10 million in annual revenue, rework could cost approximately $447,000, representing a significant financial impact to profitability.
Understanding Returns Management (RMA)
At the core of managing rework effectively is a solid returns management system. This includes four primary types of RMAs, each with its own workflow and set of transactions:
- Return (Receive & Credit): The product is returned, and the customer’s account is credited. Depending on the condition, the product may either be reworked into stock or scrapped.
- Refunds (Credit Without Receipt): In this case, the customer is issued a credit without returning the product, often used when the cost of return outweighs the value of the product.
- Repairs (Receive & Rework): The product is returned, received, and a rework order is created to track the labor and materials needed to repair it. Once completed, the reworked product is shipped back to the customer.
- Replacements (Receive & Replace): This process, often called cross-shipping, involves sending a replacement product while waiting for the defective one to be returned.
Each type of RMA requires its own workflow and decision tree, which should be designed to move products through the system as efficiently as possible. Defining these workflows in advance minimizes delays and ensures that the appropriate steps are followed.
Additionally, returns management must consider several key factors, including warranty tracking and quality control. If the product is serialized and has a warranty, it’s essential to track the warranty period and repair history. Identifying whether rework is part of a larger systemic issue is also important, as this may require corrective and preventive actions to prevent future occurrences.
Best Practices for Managing RMAs
To effectively manage rework in a wire harness manufacturing operation, companies should consider three key best practices: having a vehicle to initiate necessary and related transactions, defining workflows for each type of RMA, and efficiently and effectively collecting data for reporting and KPIs.
1. Have a Vehicle to Initiate the Necessary Transactions
The rework process should start with initiating the correct transactions for each type of RMA. Key transactions to establish include:
- RMA: This is a centralized hub that initiates and tracks RMAs. Ideally, this is linked to the original invoice or customer order for easy tracking. It provides the foundation for the workflow, and allows cross-departmental interaction for each step of the process.
- Receiving: A Purchase Order (PO) is needed to receive the returned product and bring it back into the company’s inventory system. This allows for the inventory to be accounted for and dispositioned, and maintains traceability throughout the process.
- Rework Order: Once the product is received and dispositioned, a rework order is created to schedule the necessary labor, track the material costs, and define the bill of materials (BOM) for the rework. The rework order BOM is a component of itself (called a recursive BOM) to be able to pick and use the assembly actually being reworked, in addition to other materials required. The reworked assembly is then shipped off of this rework order.
- Credit Memo: Depending on the situation, a credit memo might be issued to the customer. This could take the form of a check or an account credit, and could include both the value of the returned product plus any restocking fee.
- Non-Conformance/Corrective Action Reports (NCR/CAR): If the rework reveals a more significant issue, a corrective or preventive action should be triggered, helping to identify the root cause and ensure it doesn’t happen again.
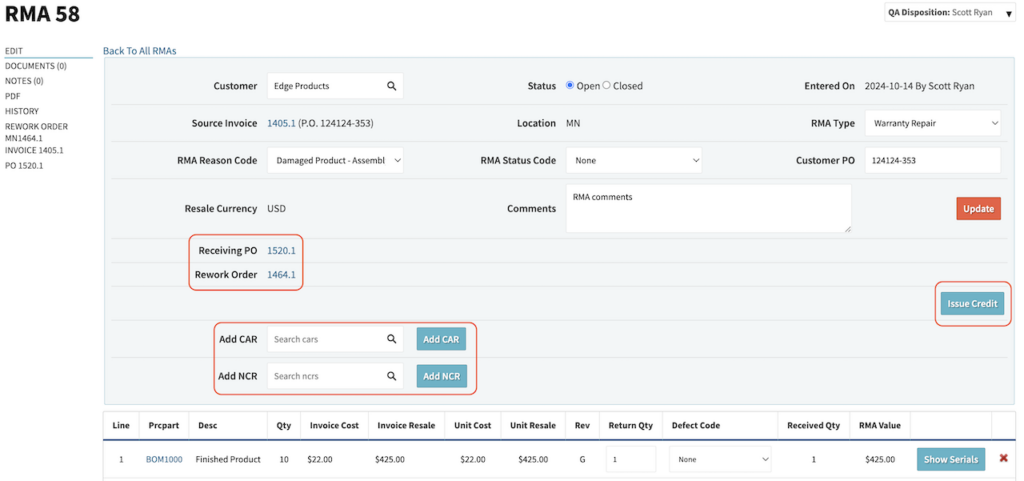
Figure 1: Sample RMA object in a standard manufacturing ERP (Cetec ERP) with each of the necessary transactions linked.
2. Define Workflows for Each Type of RMA
Every type of RMA—whether it’s a return, repair, replacement, or refund—requires its own workflow. These workflows should outline the entire process, from the time the customer initiates the return to when the product is received, repaired, and shipped back.
The key to defining these workflows is clarity and consistency. Each stage must be mapped out, ensuring that employees understand their roles and responsibilities. This reduces the chance of bottlenecks, prevents confusion, and helps streamline the rework process.
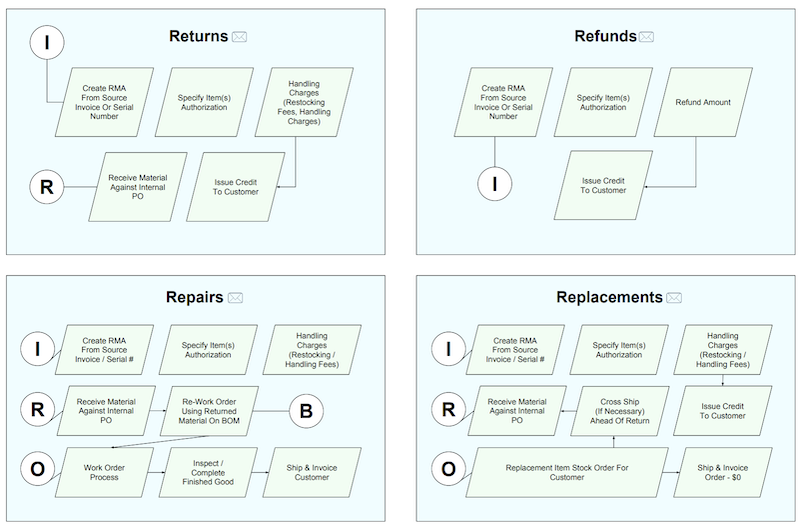
Figure 2: Sample workflows for Returns, Repairs, Refunds, and Replacements
3. Data Collection and Reporting
A robust rework management system must include data collection and reporting. At a minimum, companies should track the following data points:
- RMA Type: Identify whether it’s a return, repair, refund, replacement, warranty repair, etc.
- RMA Reason: Track the reason for the return—whether it’s due to a defect, incorrect order, or other issues.
- Defects: Record the specific defects to identify patterns.
- Turnaround Time: Measure how long the rework process takes from start to finish.
- Costs: Track the direct and indirect costs associated with the rework, including labor, materials, shipping, and overhead.
Collecting this data allows companies to perform root cause analysis, identifying recurring issues and areas where process improvements can be made. This data also helps monitor the overall health of the rework process, ensuring that rework rates remain manageable and profitability isn’t eroded.
Implementing Best Practices with a True Manufacturing ERP
Effective rework management requires more than just a set of best practices—it demands a unified, system-wide approach that integrates all aspects of the business into a single platform. A true manufacturing platform will both unify all departments and processes in a manufacturing business and have the depth of functionality to specifically navigate the niche pain points of wire harness manufacturers dealing with reworks. This level of integration ensures that information flows seamlessly between teams, streamlining communication and reducing the inefficiencies that often arise from disjointed systems.
A true manufacturing ERP system, like Cetec ERP, will be capable of incorporating all of the departments related to RMAs (program managers, quality, engineering, production, accounting) and provide the depth and niche functionality that is, ultimately, specific and unique to contract manufacturers.
With a comprehensive ERP solution, manufacturers can automate and track all key transactions related to rework, such as RMAs, rework orders, and credit memos. A centralized system enables real-time visibility, allowing managers to monitor progress and make informed decisions. It also ensures that data is consistent and accessible across the entire organization, minimizing the risk of errors and improving overall efficiency.
The right ERP system doesn’t just manage rework—it helps manufacturers identify patterns, reduce defects, and continuously improve processes through data-driven insights. By capturing detailed metrics on RMA types, defect trends, turnaround times, and costs, manufacturers can perform root cause analysis and implement corrective actions, reducing rework over time and improving product quality.
Systems like Cetec ERP empower manufacturers to integrate rework management into their core processes, reduce costs, and improve product quality—helping companies not only manage rework but also thrive in a competitive marketplace.
Conclusion
Rework is a reality of cable and wire harness assembly, but it doesn’t have to be a costly one. By adopting structured workflows, integrating rework management into the broader production process, and using data to drive continuous improvement, manufacturers can minimize the impact of rework on their profitability and reputation. The key is consistency, transparency, and a commitment to using rework as an opportunity for learning and growth, rather than a source of frustration and loss.