Recognizing the surge in demand for high voltage wire harnesses in the heavy-duty EV industry, Bmax, a subsidiary of I-Pulse and a global leader in High Pulsed Power (HPP) technology, has strategically expanded its operations. With a 24,000 sq. ft. state-of-the-art facility in Rochester Hills, Michigan, Bmax is set to make a significant impact in the high voltage wire harness manufacturing market.
At the core of Bmax’s offering is High Pulsed Power technology.
High Pulsed power is the science and technology of accumulating energy over an extended period and releasing it in an instant, significantly increasing the power. In a pulsed power machine, low-power electrical energy from a wall outlet is stored in a bank of capacitors and then discharged as a compressed pulse of power. As the duration of the pulse decreases, the power intensifies. The result is an extremely short pulse with immense power, which can be harnessed in various ways.
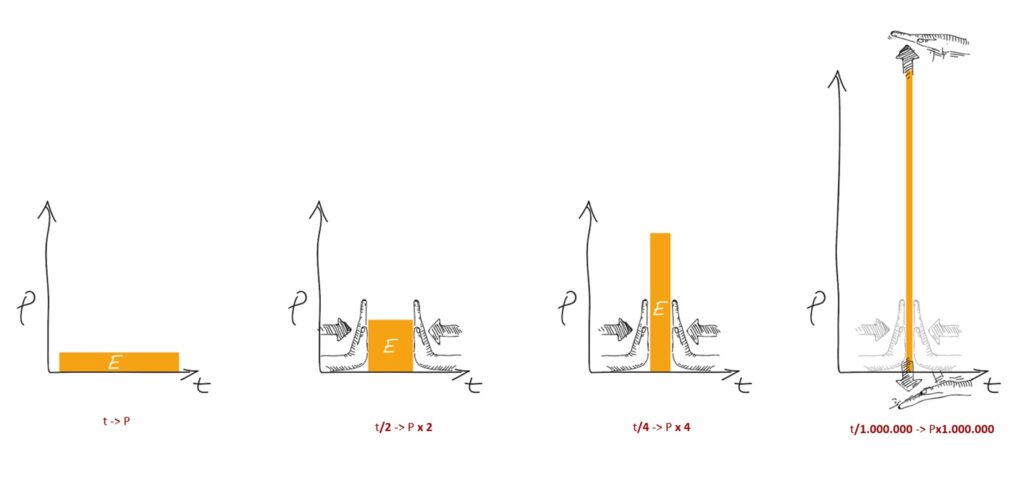
Fig.1 High Pulsed Power Principle
For over a decade, Bmax has been the world leader in manufacturing HPP (High Pulsed Power) systems for metal forming and assembly.
Bmax’s generators can convert alternating current into a pulse of current by charging a bank of capacitors and releasing the energy stored through high voltage switches. The peak of current can reach millions of amperes with a frequency of several tens of kHz.
The pulse of current directed into a coil converts the electrical signal into a magnetic pulse. Bmax utilizes this magnetic pulse to create extremely high repelling forces between the coil and the workpiece, resulting in ultra-high-speed deformation.
Cutting-Edge Magnetic Pulse Crimping Technology for High Voltage Wire Harnesses
Magnetic Pulse Crimping (MPC) is one of Bmax’s revolutionary metal forming and joining solutions.
This innovative approach utilizes High Pulsed Power (HPP) to crimp the terminal to the high voltage cable in under 100 microseconds.
MPC enables the joining of terminals onto cables with exceptionally high compression, ensuring excellent electrical and mechanical performance. During the impact, the individual strands of the wire are pushed against each other removing air gaps in the crimp area. The resulting connection has very low crimp resistance and high pull-out force.
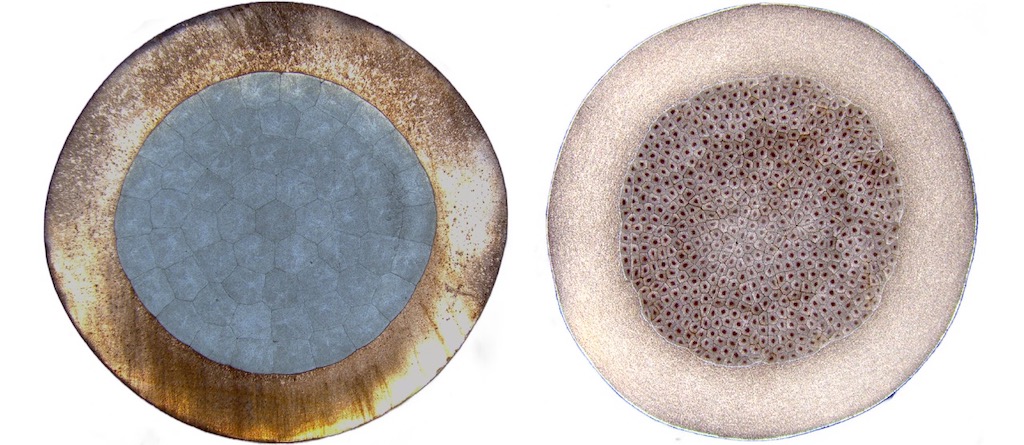
Fig. 2 Micrography, MPC samples, left: 300mm², right: 120mm²
This is crucial for maintaining the integrity of high voltage wire harnesses throughout the lifecycle of an EV. Unlike traditional crimping methods, MPC delivers a robust connection that remains consistent from initial production to the end of the vehicle’s life, due to the fact that MPC crimps do not relax after thermal cycling thus maintaining low crimp resistance levels.
Magnetic Pulse Crimping principles (MPC)
The Magnetic Pulse Crimping process (MPC) is a High Pulsed Power system based on a 4 to 6 seconds slow charge of high voltage capacitors and their rapid discharge through a coil, typically in between 1µs and 30µs.

Testing and Simulation
At Bmax, rigorous testing of wire harnesses is conducted to ensure the highest quality and performance, which include thermal cycling and salt spray, micrography, and tensile or pull force tests. Environmental testing simulates harsh conditions to verify durability, while micrography ensures optimal compaction and the elimination of air gaps to enhance electrical characteristics.
Additional testing includes: 4-wire crimp resistance measurement, hi-potential (hi-pot) testing, and dimensional checks. The crimp resistance measurement assesses the resistance level after a crimp, with Magnetic Pulse Crimping exhibiting exceptionally low resistance compared to traditional methods. The hi-pot test, performed on every wire harness assembly produced, ensures there are no nicks or breaks, serving as a critical end-of-line quality assurance measure.
Bmax also designs robust tooling and optimizes crimping results thanks to its proprietary custom Multiphysics 3D computational simulation.
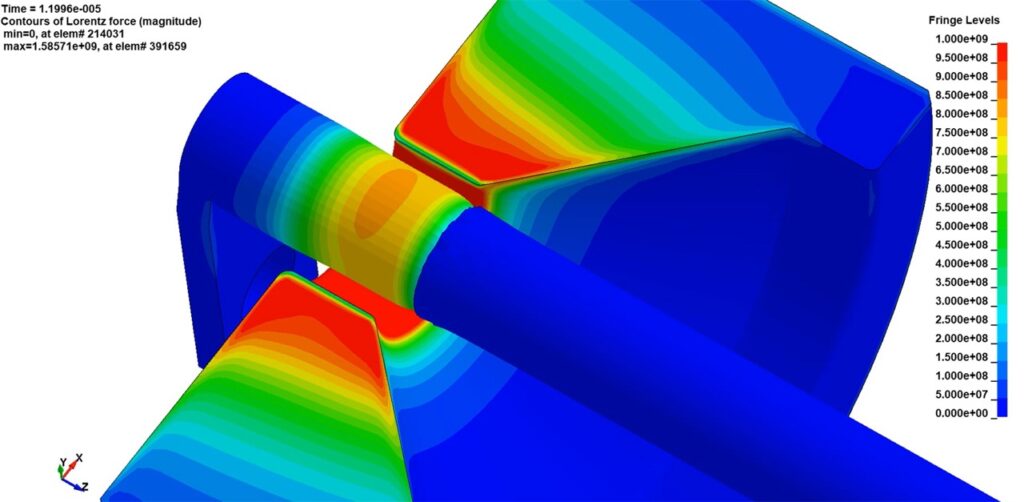
Fig. 3 Proprietary Simulation Software
Global Reach, R&D and Comprehensive Services
Bmax operates manufacturing facilities in both France and the United States, effectively serving a global customer base. Each location is equipped to provide rapid prototyping, high-volume production, testing, and exceptionally fast delivery times for wire sizes up to 300mm². Each facility is staffed by expert teams responsible for developing all products, systems, and related services. This global presence enables Bmax to offer localized support and quick response times to customers worldwide.
Bmax also maintains a dedicated research and development department, continually exploring new applications for High Pulsed Power (HPP) technology. This commitment to R&D ensures that Bmax remains at the forefront of innovation, consistently developing solutions that meet the evolving needs of the market.
Unmatched Production Capacity
One of the key advantages of Bmax’s Rochester Hills facility is its unmatched production capacity. Bmax manufactures its own systems that are used in production. As the only magnetically pulse crimping facility with multiple systems for serial production, Bmax boasts the largest volume capacity in the world. This allows the company to meet high volume demands while maintaining the highest standards of quality and consistency.
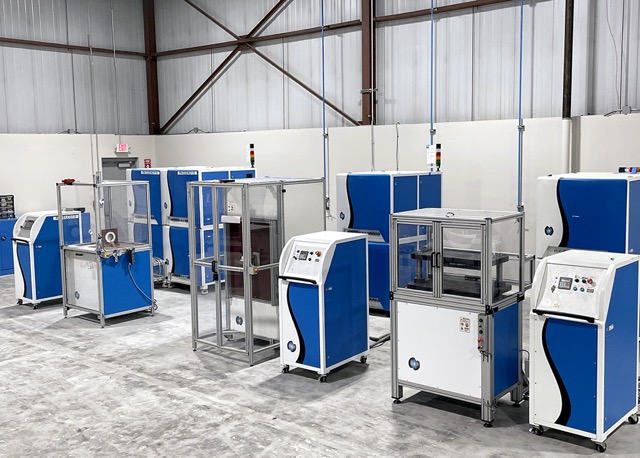
Fig. 4 Production Cells and R&D
Diverse Product Offering
Bmax’s main product is the magnetically pulse crimped high voltage wire harnesses for EVs. However, the company’s expertise extends beyond this. Bmax also offers magnetic pulse forming of sheet metal and magnetic pulse welding of dissimilar metals such as Al to Cu busbars and circular welding for HVAC. These capabilities open new avenues for product design and material selection, providing manufacturers with greater flexibility and efficiency in their production processes.
Revolutionizing Metal Joining and Shaping
Bmax’s industrial solutions, based on High Pulsed Power technology, offer a unique, efficient, and clean alternative to traditional metal joining and shaping methods. The ability to join dissimilar metals, with no heat affected zone, and create complex shapes with precision and consistency is a game-changer for industries ranging from automotive to aerospace. Bmax’s solutions enable manufacturers to produce more complex and reliable components with greater precision.
Commitment to Sustainability
At Bmax, sustainability is a core value that drives every aspect of the business. The company’s High Pulsed Power technology is inherently clean, reducing the need for harmful chemicals and minimizing waste. By offering environmentally friendly alternatives to traditional manufacturing processes, Bmax is helping to reduce the overall carbon footprint of its customers and contributing to a more sustainable future.
With its innovative magnetic pulse crimping technology, unparalleled production capacity, and commitment to research and development, Bmax is positioned to become a key player in the EV industry and beyond.
Bmax will be exhibiting at Battery Show 2024 in Detroit, booth #513.