Polymer coated yarns are used in many industries for braiding wires and cables that need to be kept together and protected against abrasion and harsh environments. Common applications are agriculture, automotive, construction equipment, marine engines, industrial equipment, military, and locomotives. They are comprised of man-made fiber substrates that have polymeric coatings to enhance their functional properties.
Braid yarns have many advantages over rigid PVC conduits. They have more flexibility (even at low temperatures), do not retain moisture, will not trap particle matter, and dissipate heat well. Because braiding is a custom solution, it can be used on complex harnesses and will reduce the overall diameter. Increased material performance and the need for more customized solutions have made polymer coated braid yarns a good option for many harness applications,
EY Technologies is a producer of polymer coated nylon yarns. Brendan Farrell PHD, R&D Manager and Jackie Wright, General Manager discussed why these yarns have gained in popularity over legacy wire management products in recent years. They also covered some specific applications for the various levels of products they carry.
Brendan indicated that historically, braiding was done on harnesses for heavy industrial equipment and machinery, but that its use has transcended to many other applications. “I think the cost of braiding has gone down relative to other solutions, and people are seeing the value of having a custom wiring harness versus having an off-the-shelf conduit or sleeving product.” The higher performance of the materials makes braiding a superior choice, he insisted, for electric vehicles, generators, locomotives, etc.
EY Technologies has been focusing development on polymer braid yarns with increased temperature and chemical resistance. “There’s definitely been some increased awareness and inquiries over the past few years for higher temperature applications and I think there’s an opportunity to design a thermoplastic braid yarn with a working temperature up to 200 degrees C. In some cases products are being used that are designed for 900 degrees when all that is required is 175 or 200 degrees.” He also stressed that those more exotic materials are more expensive and more labor intensive to use than the polymer coated yarns.
Brendan began discussing EY Technology’s individual coated yarn offerings with what he described as the workhorse of the industry, PVC-coated nylon. “We have two variants of that. We have one that we call Regular Performance (RP) and one that we call High Performance (HP) and the difference is essentially in the flame resistance rating.” The HP coating meets UL 94 V-O (burning stops within 10 seconds on a vertical specimen; drips of particles allowed as long as they are not inflamed) and is designed to perform at slightly higher temperatures for extended periods of time.
“The next step up is our Thermoplastic Elastomer (TPE), and it has a slightly higher working temperature.” This TPE-coated polyester yarn also has great flexibility in cold temperatures. “What’s also interesting about the TPE coated polyester is that there are folks using it, particularly in Europe, to get away from the requirements that restrict the use of halogenated plastics. So they’re going up the ladder in terms of cost pretty significantly to have something that isn’t halogenated.”
Moving up the performance hierarchy is their High Performance Polyvinylidene Fluoride (PVDF) coated polyester yarn. “You can think of it as a TeflonÒ-type coating and it’s another notch up in terms of temperature performance. But you also get a lot of chemical resistance, particularly at higher temperatures where some of the PVCs may show degradation.” The PVDF coated yarn is somewhat inert in high temperature environments to things like engine oil and harsh chemicals. They also offer excellent abrasion resistance.
Jackie and Brendan were most excited to talk about the company’s deep commitment to research and development as these are the efforts that are pushing the temp and chemical resistance boundaries of coated polymer yarns even higher. “We work hand-in-hand with folks who make braiding equipment and customers who are braiders,” Brendan advised. “We can customize materials or packaging sizes. We make sure they get the right materials for their specific applications, and we are open to creating new products for them.”
These custom products might be for combinations of temperature, abrasion, or chemical resistance. They see a void where the industry is using some very expensive options that can be replaced with engineered thermoplastic products. “I just think it’s important to let folks know that we have a strong R&D department,” Jackie proclaimed. “It’s led by Brendan who is a PHD in Chemistry and I think that says a lot about us and our commitment to developing new products. Over the years, we have developed a wide range of specialty products serving virtually every phase of industry. We are an industry leader, well known for our exceptional quality and service. “
Many thanks to Brendan and Jackie for their time. Special thanks to Tonya Beaudet at EY Technologies for making this interview possible and for providing some background information. She wanted to let folks know that EY Technologies has been producing braid yarns for harness protection for 30 years and is ISO 9001:2005 certified with distributors in Europe and Australia. You can check out specific performance ranges for these products at eytechnologies.com. Meet EY Technologies at the Electrical Wire Processing Technology Expo (EWPTE), at booth 1325.
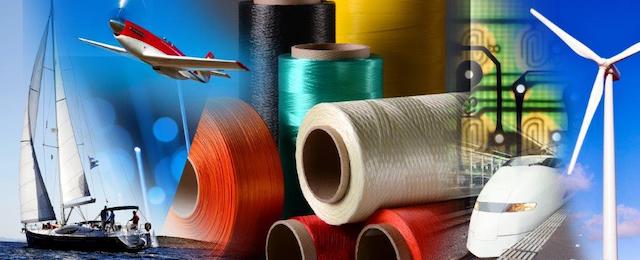