Justification for Ultrasonics in Busbar Integration.
By TECH-SONIC
Busbars come in different sizes and shapes that determine the maximum amount of electric current a conductor can carry before deteriorating. Busbars are usually made from corrosion-resistant copper, brass, or aluminum in solid or hollow tubes. The shape and size of a busbar, whether flat strips, solid bars, or rods, allows for more efficient heat dissipation due to high surface area to cross sectional area ratio. Copper busbars usually oxidize over time but remain conductive. That is why coating the busbar is important to protect against oxidation. The three main purposes of coating busbars are: to inhibit corrosions, increase conductivity, and for cosmetic purposes. The current size of busbars used in automotive applications are 35, 50, and 90mm2. Today a battery pack has about 15-20 busbars.
With the proper materials, a busbar can assist thermal management along with power distribution in an EV/HEV. A busbar’s conductor material and the cross-sectional size of the busbar will determine its current-carrying capacity. Laminated busbars typically consist of copper or aluminum conductors which may or may not be plated with an additional conductive metal, such as silver or gold. Busbars can be fabricated in a variety of shapes, including flat strips, solid rods, and hollow tubes, with flat or hollow forms generally preferred for high-current applications.
The energy requirements of an EV/HEV can vary widely, with the largest amounts of electrical energy required by the inverter and electric drive motor. An EV motor has a wide range of power levels, from lower-voltage operation at slow speeds to higher-power use when accelerating or climbing steep grades. Low-inductance busbars can help achieve low-loss transfer of energy with high energy efficiency from a battery pack, by minimizing energy losses in the power transmission path from an EV’s high-power battery pack to the inverter and electric drive motor.
Benefits of using Busbars
There are many benefits in using busbars for EV wiring systems. Busbars make it much easier to add or relocate power with little or no downtime. Because of their simple design, they require no routine maintenance. They tend to take up less space and pack flatter than traditional cable systems and can supply up to 15% more power. Busbars offer much more design flexibility and dissipate more heat than their stranded counterparts.
A busbar can be characterized by its resistance and conduction, ideally with its electrical contributions distributed as evenly as possible across its length to avoid performance issues. While the lowest possible resistance and conduction values are to be preferred in a busbar for EV and HEV power distribution, some busbars for that purpose have capacitance added in different ways to increase the charge-carrying capabilities of the power-distribution structure.
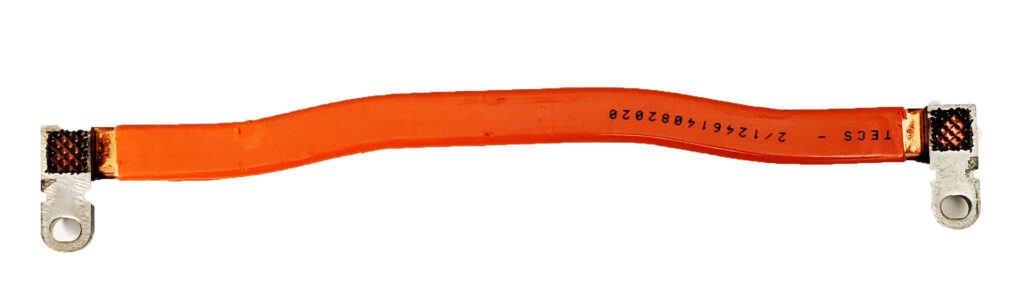
In contrast to power cables, busbars also make it possible to achieve power distribution with high power density, by mounting active components for power conversion, such as IGBT semiconductors, and passive circuit elements, such as capacitors and EMI filters for noise reduction, on the busbars. In most cases, circuit elements can be incorporated onto a laminated busbar prior to its installation in an EV or HEV, or as part of the busbar’s manufacturing process. Incorporating electrolytic capacitors into busbars for motor drives can improve performance while also conserving circuit volume. For further savings of space within an EV/HEV, hybrid forms of busbars are available with signal paths alongside the power planes for interconnecting sensors and control units to on-board vehicle computers and driver controls.
Why Busbars in Electric Vehicles?
With the development of the electric vehicle, manufacturers have found that busbars are the ideal solution to improve conduction in EVs. Busbars have revolutionized the EV landscape and are housed inside switchgears, panel boards, and busway enclosures for local high current power distribution.
The following are benefits of using busbars in EVs: ability to add or relocate power easily without any down time, requires no routine maintenance, faster and less costly for expansion or remodeling, more environmentally friendly as it requires fewer installation materials, flat conductor takes up less space, can support up to 15% more power than cable, less weight and packaging space with much better flexibility, and more efficient heat dissipation than stranded cables.
Electric Vehicles and Ultrasonic Welding for Busbar
In EVs, large banks of battery cells are fused in sealed packs to achieve the required operating voltage and current to power a vehicle’s electric motor. Two main concerns regarding EVs are power storage and driving range. OEM’s are addressing these issues in two ways: creating larger batteries that allow for greater range and creating more powerful batteries that allow for faster charging.
As the market for electric vehicles continues to expand, manufacturers will seek solutions to improve current technological processes for electric vehicles when it comes to battery performance such as efficiency, battery lifespan, and charging time. To maximize these key potential factors, ultrasonic welding will play a crucial part in these technological breakthroughs. Since the 1980s, the automotive wire harness manufacturing industry has been documented as the largest user of ultrasonic welding.
TECH-SONIC’S Ultrasonic Welding Technology for Welding Busbar
With the implementation of busbars in EVs, a sensitive and solid joining procedure is needed to ensure conductivity. Ultrasonic welding technology is a proven joining process that is ideal as specified by carmakers for use in busbars and power electronics. With ultrasonic welding, parameters can be controlled and there is less stress on the weld which makes the welds repeatable and precise. Ultrasonic welding is the preferred joining process for busbars.
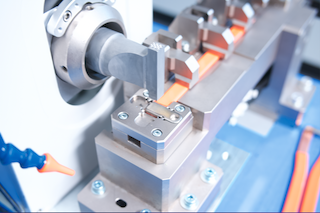
However, TECH-SONIC has developed a state of the art ultrasonic joining process called “CLC” or Closed Loop Control. Conventional ultrasonic welding operates on a pneumatic cylinder which can have some inconsistencies with the air variation, but TECH-SONIC’s Closed Loop Control ultrasonic welding uses an electric servo motor and load cells in conjunction with an ultrasonic welder. This integration allows users to control and monitor the applied force and amplitude during the weld process. TECH-SONIC calls this process “multi-step welding”, turning a once open loop system into a closed loop system. This technology provides superior quality control with highly repeatable welding results, creating significant cost savings. This is the ideal joining process for busbars to ensure a conductive and solid weld.
References: