Last November, WHN covered some of the intricacies of high-voltage wire preparation with Martin Rosten, Global Sales and Field Service Director at TE Connectivity. It’s well worth having a look if you missed it. In this issue, we are fortunate to have another expert from TE Connectivity to discuss developments in support of EV manufacturing in the automotive and commercial vehicle arenas. We were happy to speak with Dr. Nengquan (Nick) Liu, CTO of the Applications Tooling Business Unit at TE Connectivity. He provided details on some of the solutions TE is developing to help meet the challenges the industry is facing.
The first big development Nick wanted to talk about was their recent strides developing processing equipment for flat flexible cable (FFC) and flat printed cable (FPC). Examples are shown in figures 1 and 2 respectively.
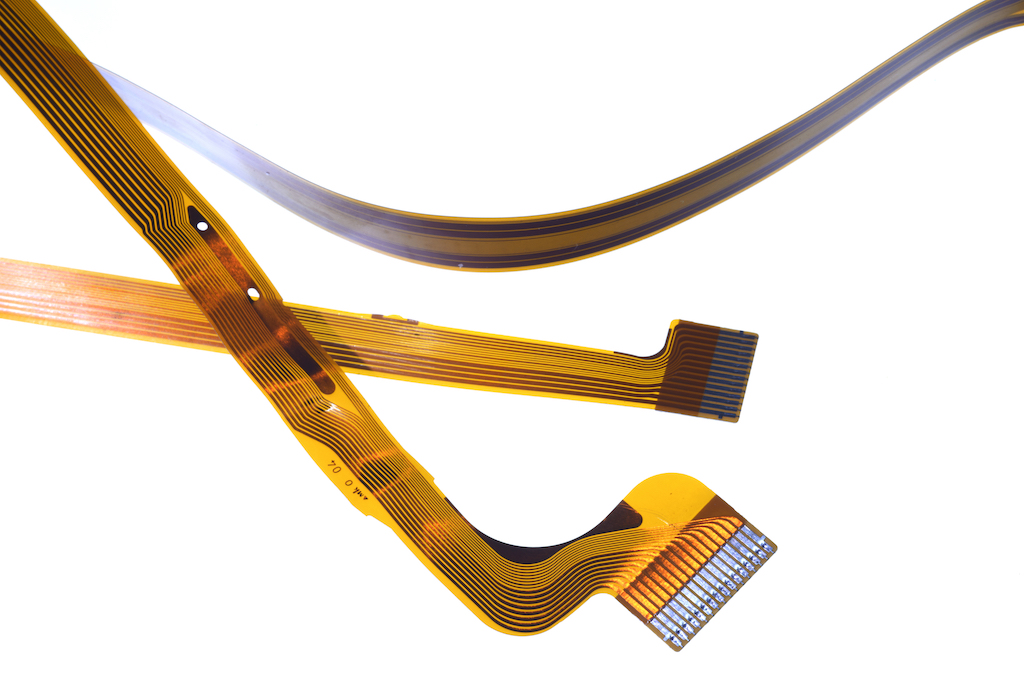
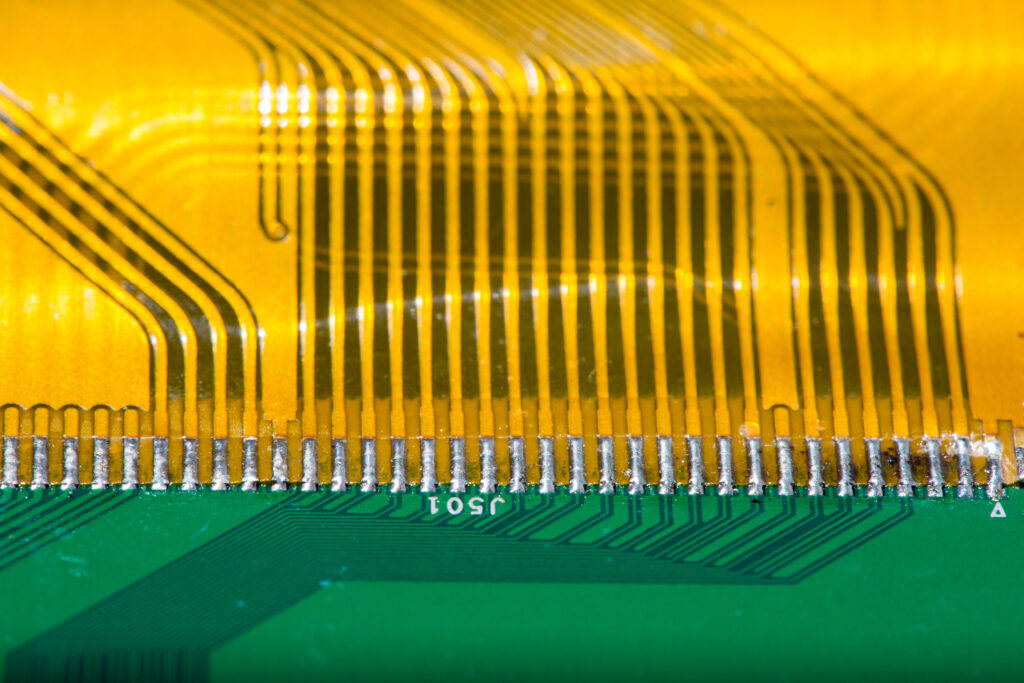
FFC and FPC technologies have been around for some time. It’s light weight, low profile and flexibility make it ideal for battery cell production. These conductors dissipate heat more easily, so they can carry more power with a smaller and lighter overall footprint. As volumes for EVs ramp up, so will the need for automation, as these materials make their way into mainstream production. The need for speed, validation and consistency in processing them has become paramount.
Nick maintains companies like Tesla and other EV manufacturers have really propelled the use of these conductors. “I think they totally disrupted the traditional wire harness and how it is assembled. The introduction of FFC/FPC is a definite cost advantage and it’s also easier to manage from a manufacturing standpoint once you have the proper tooling,” he explained.
TE currently has a semiautomatic machine for terminating FFC (FFC Termination Machine Mark II). This machine has provided the template for automation in processing FFC/FPC. They are on the cusp of launching automated processing equipment for these architectures to support the automotive industry. “We started in development a few months ago and quickly came up with a prototype machine. We tested it with a potential customer. They liked it and we continued to develop the machine at faster speeds,” he detailed.
Their new Semiautomatic Machine for both FFC and FPC, will be available very soon, will crimp up to 100mm, has a cycle time of three crimps per second and has on-board crimp force and crimp height monitoring. Vision Alignment locates the foil at the first crimp, and the ‘Re-crimping’ function allows the machine to do a re-crimp if a batch of foil is missing one terminal. This feature greatly reduces waste.
A companion machine is completing testing now and will be available sometime in Q4 of 2023. It will have the ability to terminate FFC/FPC cables to 300mm. This capability will allow the equipment to handle the more robust interconnect systems of commercial EVs.
Nick was also eager to talk about another advancement in wire processing he and his team have been busy developing. In partnership with an outside ultrasonic technology company, TE is introducing its own ultrasonic weld equipment. The new machine can accommodate Cu and Al cable is sizes up to 95 mm². Its poka-yoke design ensures fail-safe terminations with full monitoring and validation throughout the entire process.
We spent the remainder of our time discussing the importance of crimp integrity in high-voltage systems. He shared the illustration in figure 2 to drive the point home.
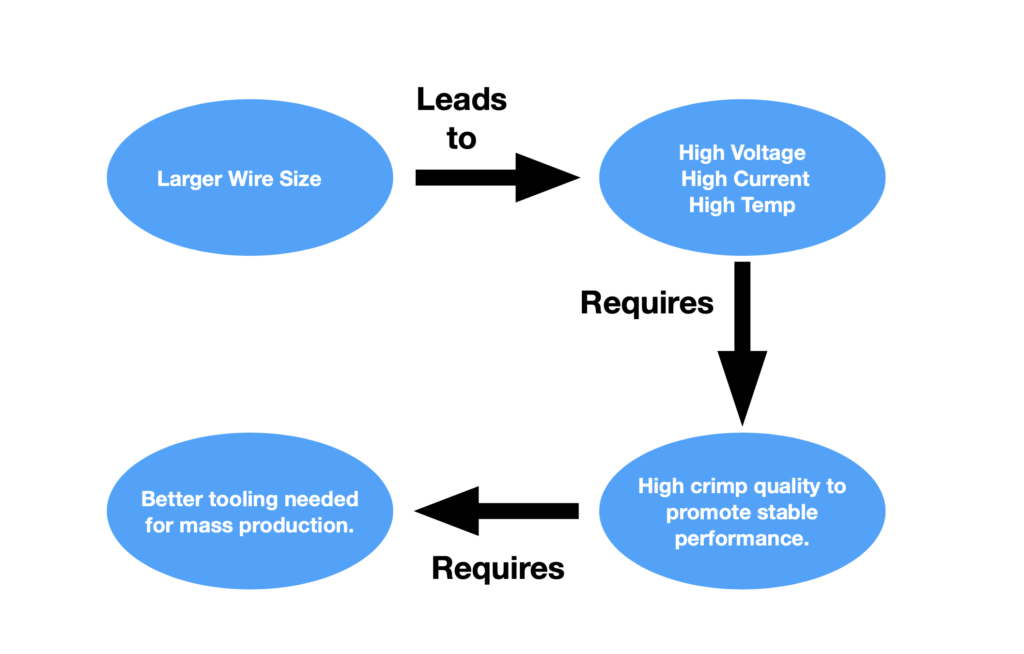
Figure 3. Crimp Tooling Criticality in EV Production – © 2020 TE Connectivity
“When considering the crimp tooling for EVs, you have larger wire to handle the higher voltage, currency and temperature profiles. It definitely requires high crimp quality to support stable manufacturing because the environment has changed from traditional low-voltage to high-voltage for automotive EVs, and even higher in commercial vehicles. As the industry ramps EV production better crimping tools are needed.,” he explained.
Nick concluded stressing TE’s ability to innovate with things like FFC/FPC and ultrasonic technology. He highlighted the company’s desire to be a ‘total solutions’ provider. “We are working very closely with our suppliers and our customers to validate the equipment in development very quickly. Sometimes you make assumptions, and those assumptions turn out to be true, other times not. As volumes increase, however, you have to do things at a much higher rate with more consistency,” Nick advised. “But we have done quite a bit of concept design review together with our customers and I think the result has been very effective.”