by Saeed Mogadam – Telsonic Solutions
Ultrasonic welding of non-ferrous metals has been a proven technology for decades. However, since the early 1980’s, ultrasonic metal welding has dominated the automotive industry, with automotive wire harness manufacturers as the single largest user of the technology. Due to its efficiency and unbeatable quality, ultrasonic welding replaced mechanical crimping and resistance welding for all car brands almost immediately upon inception. The utilization of ultrasonic welding for automotive wire harnesses has seen even more rapid growth in the last decade due to the increase in electrically powered vehicles (EV). Telsonic’s innovative and industry changing torsional welding technique has in large part contributed to this rapid growth due to its unrivaled ability to address challenges such as weld size, welding in smaller areas, geometrical shapes, reaching the weld area, orientation of welding, and vibration effects on peripheral components.
Telsonic’s Torsional welding technique has overcome many of the current limitations in longitudinal welding and has created breakthrough applications that were previously considered impossible or not up to quality standards prior to last decade. Now, the technology is increasingly specified by carmakers for use in EV for weight control, battery packaging, cable to terminal connections, bus bars, battery manufacturing and power electronics. The higher power and faster charging of EV batteries requires larger battery cables with, sometimes, unconventional connectors. Telsonic’s PowerWheel® welding technology, which utilizes torsional welding, provides a solid assembly solution that satisfies the high-quality requirements in the Automotive industry.
Challenges of Longitudinal Welding with Larger Cables
There are several obstacles one needs to overcome when welding larger cables. These can include:
- The larger the weld width, the better the transfer of vibrating energy to join the cable and the connector. However, as there are limitations for the connector, there are also limitations on how large the sonotrode (vibrating tool) can be. In addition, the wider the weld width is, the more nicking of the strands can occur at the transition area of the weld. The connector’s surface area, geometrical shape, and the weld orientation will add to the challenges even further.
- The larger the cable to be terminated, the larger the generator power and welding force need to be. For cables sizes of 150 mm², we need generators with power above 10 KW and forces up to 8,000 Newton. Such high force is not sustainable for conventional welders if it is not a direct force to the weld area. Otherwise, significant bending of the sonotrode makes it impossible to create consistent weld quality between the cable and the connector.
- Conventional welders allow one orientation and thus create limitations for differently design connectors and orientation of the welding. Telsonic’s PowerWheel® allows more freedom for accessing the parts to be welded due to the orientation of tooling and vibration, creating a solution for each of these challenges. The tooling orientation of PowerWheel® allows welding on surfaces that are otherwise hard to reach with conventional welding.
- Even if none of the above challenges are present, there is always one quality criteria that can be an issue to meet. The relative movement of sonotrode, known as amplitude, is how the scrubbing/friction between the parts interface is created. (see figure 2). Conventional welding amplitude is highest at the welding transitional area. This can be an issue when welding larger cables at a pre-specified weld width and high power and force. The higher amplitude near the start of the weld nugget causes nicking of the cable’s strands due to extreme extrusion of strands (see figure 1).
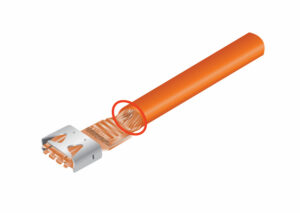
How Linear and Torsional Welding Work
Figure 2 demonstrates the basics of how longitudinal (Linear) welding works and is essential to understanding the differences between traditional longitudinal and Telsonic’s innovative PowerWheel® welding technology.
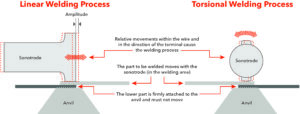
- The term ‘amplitude’ describes the extent of sonotrode’s motion – expansion and contraction.
- The amplitude correlates with the scrubbing effect at the interface of the weld seam. This movement in combination with pressure is responsible for the welding process.
Major Differences in Linear and Torsional Welding -Table 1
PowerWheel® welding technology uses an innovative concept to vibrate the sonotrode, which is excited in a torsional manner. With a scalable welding power of between 7.2 kW and 14.4 kW, the optimum welding power can be selected for each application.PowerWheel® for Cable Terminations
The torsional technology allows for welding of larger size welds, bus bars, 3D terminals, more geometrical shapes, out of reach joining areas and applications where gentle vibration is required. This has expanded the ultrasonic application spectrum significantly. Many joining applications that were previously impossible with conventional longitudinal welding are now possible.
Benefits of PowerWheel® Welding Technology
Welds can be produced up to 30% narrower and higher compared to those produced by a linear system. This can often result in considerable savings in both material and space required to position the assembly. A further benefit is that thicker terminal connections can be welded with great strength. The welding takes place in a swaying and rolling motion directly above the weld area. As a result, the maximum amplitude is always in the center of the welding area and the energy is directed and focused within the welding zone. With direct force at the welding interface and smaller amplitude in the nugget transition area, the welder can drive more energy for a larger cable because the damage to the wire strands is minimal, if at all. Due to the torsional movement of the sonotrode, there is practically no load on the surroundings of the welding zone due to the ultrasound. The torsional process is therefore particularly suitable for sensitive applications where vibrations outside the welding zone could cause damage. The slow rate of vibration propagation along the cable’s axis makes PowerWheel® more desirable for shorter cables. Often there is a concern for short cables being welded on both sides as the second weld vibration may weaken the first weld. Studies were conducted in 2011 for 50 mm² cables of 180 mm using PowerWheel® The results showed that no difference could be found on the weld strength of both ends of cable. In addition, the mechanical strength was about 30% higher than those done with the traditional longitudinal process.
Telsonic’s PowerWheel® standardized sonotrodes are optimized for copper and aluminum wires, meet the requirements of OEM’s and harness makers, as well as the USCAR 38 standard (performance specification for ultrasonically welded cable terminations). As with conventional ultrasonic welding, the PowerWheel® system can also be used to weld non-ferrous metals.
PowerWheel® Welding Advantages at a Glance:
- Maximum output of up to 8 kN with 14.4 kW
- For large cable diameters, large terminals/tubular cable lugs
- Welding of up to 160 mm2 copper / 200 mm2 aluminum wiring
- Up to 30% narrower welds
- Significantly improved wire compacting
- Excellent welding strengths
- Adjustable weld directions for universal feed
- Excellent accessibility to weld zone
Necessary Equipment
Like conventional ultrasonic welding, ultrasonic torsional welders have a generator, converter and sonotrode. In contrast to conventional systems, however, the sonotrode does not oscillate longitudinally but torsionally, which is how stress on the parts is reduced. At the same time, an ultrasonic output of up to 14.4 kW can be passed through the sonotrode. Consequently, the electrical vibrations formed by a generator in torsional processes are relayed into a PZT vibration transformer to be converted into mechanical vibrations through a piezoelectric effect. Converting linear generated vibrations into torsional movement is done by assembling the acoustic components in the SONIQTWIST® vibration head in a particular order.
The new PowerWheel® Telso®Terminal TT7 ultrasonic metal welding system is versatile and can be used for various applications, including cable assembly and battery production. Its applications include HV cables, battery terminals, 3D terminals, bus bar and cell connectors, which are welded in a wide variety of designs.
Based upon a compact and modern design, this modular system delivers a host of advantages including outstanding process control using digital technology, standard interfaces for digital networking and easy integration into automation systems. The new system also incorporates the latest version of Telsonic’s proven PowerWheel® welding technology as a standard feature, ensuring maximum reliability and optimum process control for welding metal cable with cross sections up to 200 mm2.
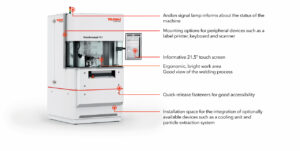
PowerWheel® TT7 for welding area
PowerWheel® Welding Technology for Terminating Stranded Wire – Actual Application Cases:
1. Small weld width without damage to fine cable strands
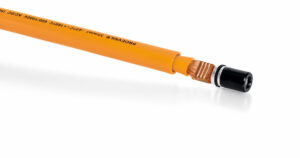
In the application shown in figure 3, a high quality 35 mm2 ProEVTM cable is welded to a Rosenberger connector, which supplies limited space for a cable of that size. ProEVTM cable was selected for this application due to its high flexibility. However, the available weld width of 10 mm as opposed to 11 mm and flexible finer strands presented some challenges. A solution that could provide a weld on a smaller space where the required weld compaction can be achieved without damages to the finer strands in the weld transition area was needed.
Solution:
The torsional PowerWheel® welding technology system was utilized to achieve a superior quality weld between the flexible ProEVTM 35 mm2 cable and the connector with 10 mm width. Tooling design and configuration had to be arranged to compensate for the limited clamping force due to the inherited connector radius. This tooling design and configuration solution allowed for sufficient welding energy to achieve a quality weld.
- Weld area is out of reach
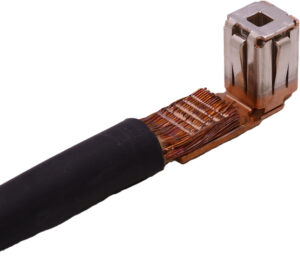
The 90° SQ4 terminal, shown in figure 4, is made of C15100 Copper alloy without plating in the weld area. This application required welding both 35 mm² and 50 mm² cables. The terminal blade width for 50 mm² was changed to 18 mm from 13 mm to accommodate a weld width of 15 mm. This also allows for 1.5 mm of clamping width on each side of the terminal when utilizing a 15 mm sonotrode. However, the connector height of about 17 mm presented a challenge for the sonotrode’s clearance in conventional longitudinal ultrasonic welding processes. It is not physically possible to design a linear sonotrode that can clear the 17 mm height and still efficiently deliver the 20 kHz. frequency required.
Solution:
The torsional PowerWheel® system was utilized to clear the connector height and achieve a superior quality weld for both 35 mm² and 50 mm2 cables with the SQ4 terminal. The sonotrode’s orientation allows for the clearance with the 90° terminal and delivers sufficient welding energy to achieve a quality weld without effecting the finer strands in the transitional area or the connector itself due to the gentler application of the vibrations.
- More examples of challenging applications (Figure 5)
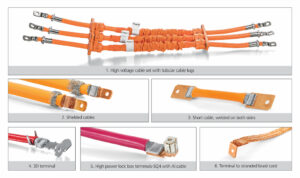
The following represent some additional applications and challenges in the ultrasonic welding of terminals on stranded wire that the Telsonic PowerWheel® system can address:
- High voltage cable set with tubular cable lugs – Welding is proven to work with PowerWheel®.
- Shielded cables – larger cables up to 200 mm² in a smaller weld area is possible when there are restrictions on surface area of the connector.
- Short cables welded on both sides – Welding both ends of a short cable by linear welding could allow the vibration for the second weld to break the first weld. Torsional welding has much less vibration affect and, therefore, it makes welding of cables as short as 4 in. possible.
- 3D terminal – PowerWheel® offers the advantage of more access to the weld area.
- High power lock box terminals with Al cable – The Royal Power Solutions terminal, SQ4, in this case is about 17 mm high. PowerWheel® is the method to access the weld area.
- Terminal two stranded braided cord – Braided wires have exceptionally fine strands which can be damaged without the gentle torsional vibration.
The innovative and rapidly growing EV market demands new, developing solutions for the challenges ahead. Torsional welding has become a significant joining process in the industry. In addition to solutions for battery cable terminations with a variety of connectors, the technology has provided welding solutions for EV weight control, battery packaging, bus bars, battery manufacturing and power electronics. The application capabilities have expanded beyond what was previously imagined. As product designers and process engineers continue to familiarize themselves with the torsional welding process and its capabilities, the technology is positioned to help propel the EV industry to even greater heights.