Hand tools have been a cornerstone product at TE Connectivity since the company’s inception in 1941 when they were known as Aircraft & Marine Products (later AMP). There has been a lot of development in the tooling and applications over the years, yet some things have remained constant.
WHN recently had a discussion with Mandar Deshpande, Global Product Manager of TE Connectivity. Much of the conversation centered on TE’s portable hand tools, but we did explore the tool selection roadmap that manufacturers tend to follow as they move into higher volume production. Mandar covered aspects of crimp technology of interest to everyone from the novice to the seasoned pro.
WHN: Can you describe your role, and give us an overview of TE’s crimp tool platforms?
Mandar: My responsibility is for what we call the portable tools. Hand tools are a part of it, and I will explain that and how we move from one level of automation to the next. When we talk about portable tools, we mean hand tools, along with their battery, pneumatic, and hydraulic tool counterparts. These are mainly used in aerospace/defense, rail, marine, mining equipment and commercial transportation like caterpillar.
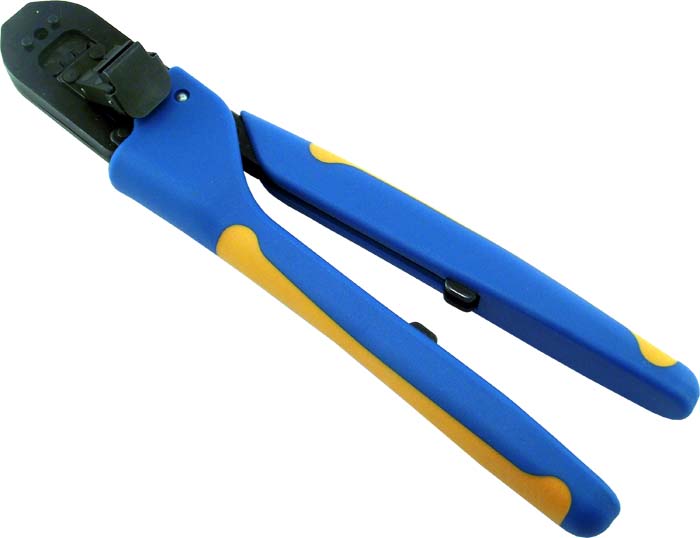
If the frequency of crimping is very low, customers prefer hand tools. What we see, however, is that among workers, there can be a variance in terms of hand strength and dexterity. This can be an issue, especially for larger crimps. What customers are looking for is, instead of replacing a person with automation, they would rather replace the hand tools with a power assisted version so they can just squeeze the button and do it.
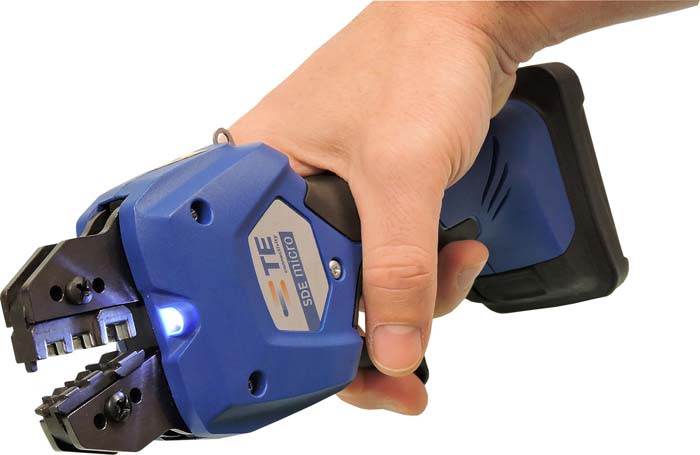
That gives you two things. First it is giving you better ergonomics in that you don’t have to squeeze the tool every time. It also increases speed. On average, the battery tool gives you more productivity than hand tools and then pneumatic tools will give you even better productivity. You can step through those things when it comes to the volumes in the markets just described.
WHN: Can you talk about the features that make hand tools such a viable and repeatable technology?
Mandar: There are two features that have always been with the tools that, I would say, are poorly understood. When you look at applicator/terminator combinations, there are so many different adjustments. When it comes to hand tools, they are perfect every time. And the way we ensure this is with two things. First is the ratchet which makes sure the handle is completely closed before it can open, thus verifying the crimp is complete. The other feature is the bottoming dies. What that does is stop the travel to prevent over-crimping. So, each time, we get an exact execution of the crimp. That is the strong point for hand tools.
WHN: What are the proper calibration intervals for portable crimp tools?
Mandar: We get that question often from customers. I will talk about two things. First, each and every tool comes with an instruction sheet, and those instruction sheets have a repair and maintenance section specific to that tool. There you will find a recommended timeframe and cycle count for recalibration. Those instructions may say something like 5,000 cycles or six months for example. Normally, if a customer is using tools day in and day out, they have a pretty good idea of cycle count, so they go by that metric. But when they do not use the tools regularly, it is better to go by time duration. So that establishes the maintenance schedule.
Also, in the same instruction sheet you have the gauging information. In most cases, you have go/no-go gauges to make sure your tool is still in prime condition. That is something we recommend customers do.
Some customers will make a group of samples for crimp height or crimp depth tests to verify calibration. Others will go beyond that and do a cross-sectional test where they cut the crimped area in half and see what is going on inside the crimp microscopically. But most of the time, the tools are being maintained according to the maintenance schedule in the instruction sheet.
WHN: I know you deal mostly with TE’s portable tools, but can you describe how customers move into more automated crimping solutions?
Mandar: As mentioned, for prototypes, repairs and low volumes, people use portable tools. But when they are going into higher production, they look at the requirements…is it 500, 1,000, 5,000 crimps per hour? From there, you might move into applicators and terminators. That is a semi-automatic solution. Semi-automatic means you are preparing a wire in one station and crimping in another. So, you have a wire prep machine cut and strip the wire, and then you have the applicator/terminator for crimping.
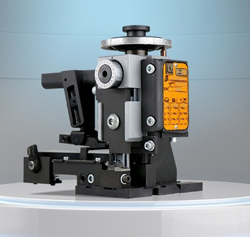
If you have much more than that you could go to a fully-automatic solution. In the case of a fully-automatic machine, which TE also offers, you have a wire reel and a terminal reel coming in and the machine is making the complete assembly.
WHN: Going back to the portable tools, are the crimp dies interchangeable from hand tools to battery and pneumatic?
Mandar: Absolutely. That’s the modularity that we strive for. If we design a die for a specific terminal and wire combination, you should be able to use it in any if the portable tools. As you get into applicator/terminator tooling, you have a feeding mechanism to align the terminals, as well as many other adjustments. Then you have adjustments for the applicator tooling. It’s a combination of many things going on, so that’s why the dies are not interchangeable from the portable tools.
WHN: How do customers select the right tool/die combination?
Mandar: We focus on the terminal and what the crimping specifications are for that terminal to get the best performance. So, we would ask which terminal and wire you are using, and based on that combination, we will offer you the correct tool and die combination. That information is all available on the TE website, or you can speak with a TE representative.
WHN: What else should folks consider when selecting tooling options?
Mandar: We talked about tool selection where there is a terminal and a wire being crimped. But there is also an application. Think about the case of aerospace, defense or marine for example. You need to have that exacting specification because failure is basically not an option. For those kinds of things, we provide our Premium Tools or Certified Tools. On the other hand, when we are repairing a refrigerator or an air conditioner or some relatively simple equipment, we suggest Commercial Tools which offer a more cost-effective solution while still providing good quality crimps.
WHN: What other things should folks consider when looking at a range of tools, or a manufacturer?
Mandar: I’ve described a broad range of tooling like non-automated hand tools, through semi-automatic (applicator/terminator) all the way up to fully automated solutions. But the most critical portion in all of this is service and training. All this equipment can get very complex depending upon what terminals are being applied to what application. And so training and service becomes a very critical piece, and that is our fourth pillar. And customers only appreciate it when they stumble upon it or they get stuck. What we at TE are trying to do is reach out to stress that when you are making a decision to buy tooling, think about service repair and training, because it is critical to your success.
At TE, we have four service centers across the world: North America, Europe, Japan, and China. Customers can send tools back and get them repaired, recalibrated, reconditioned and have them returned quickly. Also, for applicator/terminator tooling, we have field service engineers who are geographically located across the world, and can actually go in and do those repairs, help with installation or do the calibration.
For large customers, who might have hundreds of tools, instead of sending them all in every six months or one year, it might be wise to have a tooling applications engineer visit them. He or she basically works there for two or three days to calibrate and certify the tools and also assist with installation of new equipment.
WHN: I see there are a lot of training materials and resources available directly from the TE website. What sort of training options do you folks offer?
Mandar: Actually, there are many. It could be an on-sight training where we go and visit the customers location. The customer can alternatively visit our facility for training. It could also be online or virtual. Those are the three areas we focus on. And we can focus on basic training like how to make a crimp, how to recognize a good crimp from a bad one, and how to measure it.
For the person who is a little more experienced, we can ‘train the trainer’ so that person can train others within their company. We can also do certifications on those trainers going forward so they are current with all the technology and all the new advancement in tooling.
WHN: Thanks so much Mandar. Is there anything else you would like readers to know?
Mandar: Yes! TE’s vision is to create a safer, more sustainable, productive and connected future with our customers. Our entire strategy, whether it is for the connectivity portion or the sensors, is to follow that methodology. And application tooling is there to absolutely make sure that happens. For hand tools, we stress ergonomics and quality. And what I mean by quality is repeatedly getting a good crimp to exacting specifications. Those are the combinations we commit to give the customer every time.
Many thanks to Mandar for taking the time to speak with us. If you would like more information on TE’s portable or application tooling, please refer to www.TE.com.