DIT-MCO recently celebrated their 75th anniversary. WHN would like to honor the event with a glance back at the fascinating history of the company as well as a look at where they are headed for the next 75 years.
If you’ve ever wondered what DIT-MCO stands for, you’re not alone. The name is actually derived from its humble beginnings in 1948 when founder, George P Heller, seeing the need to supply equipment to the burgeoning drive-in theater market, formed the Drive-In Theater Manufacturing Company (fig. 1). In 1951, the name was changed to DIT-MCO as it began to branch into the production of custom transformers and coils for other electronic manufacturers.
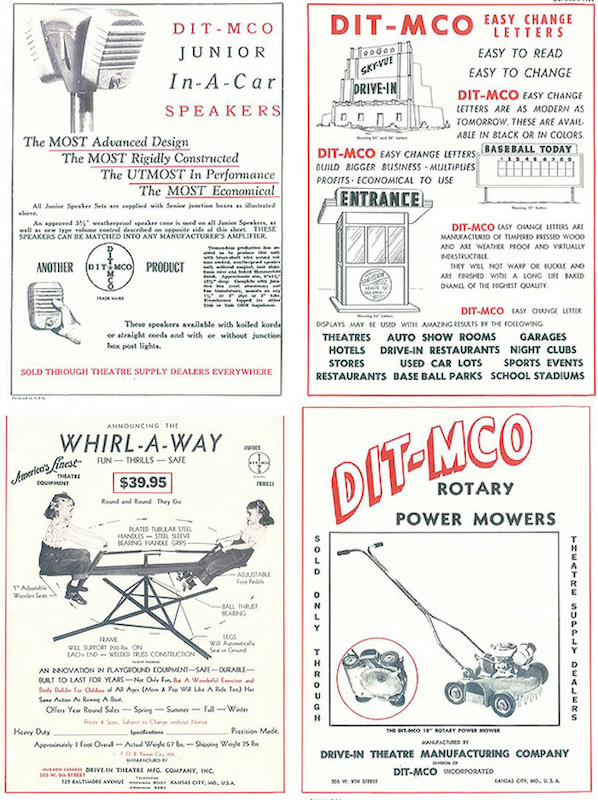
Figure 1. Part of original DIT-MCO product offering.
The forward-thinking Heller saw a plateau in the construction boon of drive-in theaters in 1953 and began to pursue other avenues to expand his business. Seeking opportunities for his Transformer Division, he called on a nearby General Motors facility that was building aviation cables. It was then that he ran into GM engineer, Warren Hannon, who had been tasked by GM to solve problems associated with testing the complicated aviation cables.
Feeling certain he could design a machine that could simultaneously measure the continuity and shorts in a bundle of insulated wires, Hannon approached Heller with the prospect that he would leave General Motors and come to work at DIT-MCO. He offered to design and build a tester to automatically test aircraft cables for shorts and opens in a given engineering specification.
Heller agreed and the original design, launched in 1952, became known as the Model 200 Universal Automatic Wiring Analyzer. The original Model 200 tested 200 circuits at the rate of approximately ten circuits per second. In 1954, DIT-MCO sold the first Model 200 to Goodyear to test electronic assemblies for one of their military electronics divisions (fig. 2). They soon approached other prospective aerospace customers.
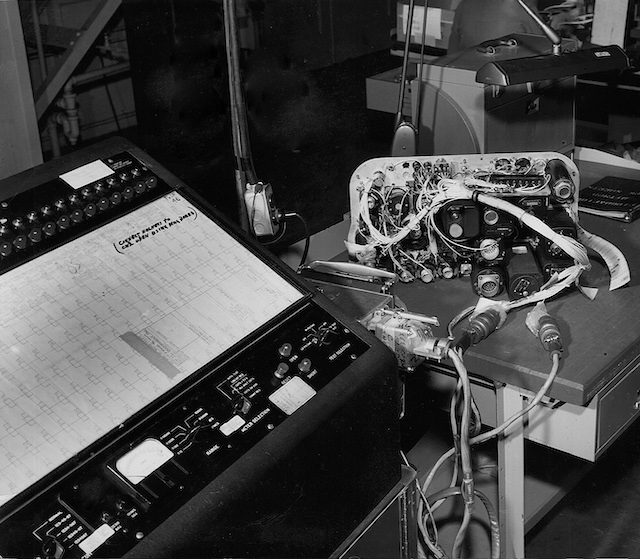
Figure 2. Model 200 testing aircraft cables.
Boeing Airplane Company in Wichita, Kansas, was building assemblies for the first U.S. jet bomber, the B-47. In 1954, Hannon convinced them to allow DIT-MCO to install the Model 200 in their plant for a demonstration to check the B-47 cables. Success in that program led to orders for the Model 200 at other Boeing locations.
The Model 200 proved a hit with the growing aerospace customer base over the next few years. In fact, it became common for the military and its suppliers to say, “This aircraft needs to be DIT-MCOed.”
Due to the success, the company decided to spin off the Drive-In Theater division to its employees in 1959. Simultaneously, the company obtained an order from the Navy for an on-board wiring analyzer known as the DIT-MCO Model 144. It used rugged waterproof construction and 44 units were delivered by the early1960’s.
Soon, engineering began on the first random access wiring analyzer. The Model 610 (fig. 3) units used punch paper tape for control and was used to test assemblies in support of the Boeing X-20 Dyna-Soar Spaceplane program, Project Mercury that put the first American in space, and the Apollo Saturn V Program that took the first humans to the moon.
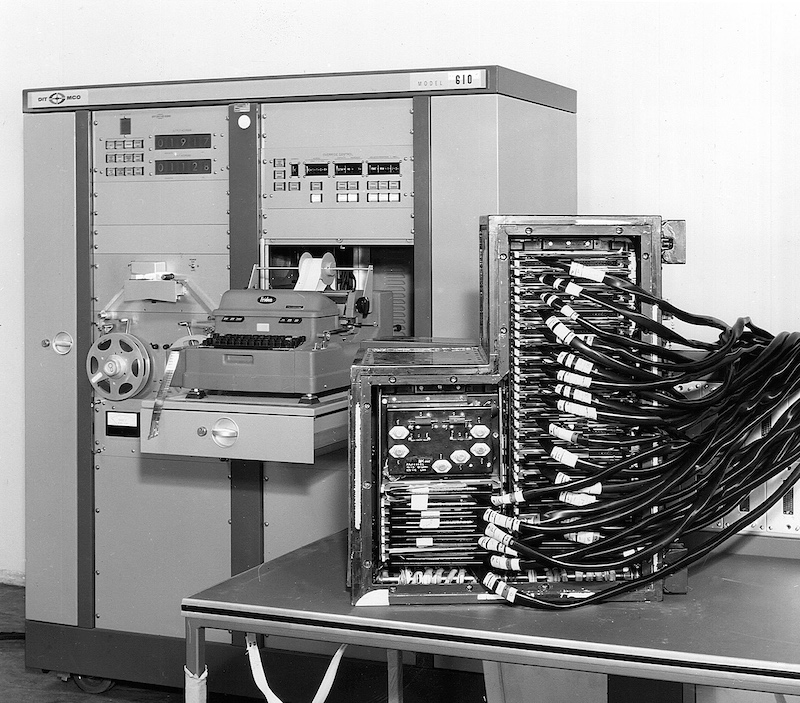
Figure 3. Model 610 testing assemblies for Boeing X-20 Spaceplane program.
The use of computers on the front end in the 1970s, along with technological advances in switch design and fault detection, greatly increased the speed of the test systems. The proliferation of integrated circuits in the 1980’s greatly reduced the size and complexity of DIT-MCO’s analyzers.
Through the years, quality improvement highlighted the need for test equipment across multiple industries. The high scrutiny once relegated to military and aerospace manufacturing now existed in the automotive, industrial, computer, telecommunication, and even appliance industries. Constant quality improvement initiatives across these industries has driven the need for enhanced testing solutions.
Today, DIT-MCO has met these challenges with a wide range of modular designs including the highly configurable model 2650 which can be cabinet mounted or distributed around an aircraft to minimize the length of test adapter cables (fig. 4).
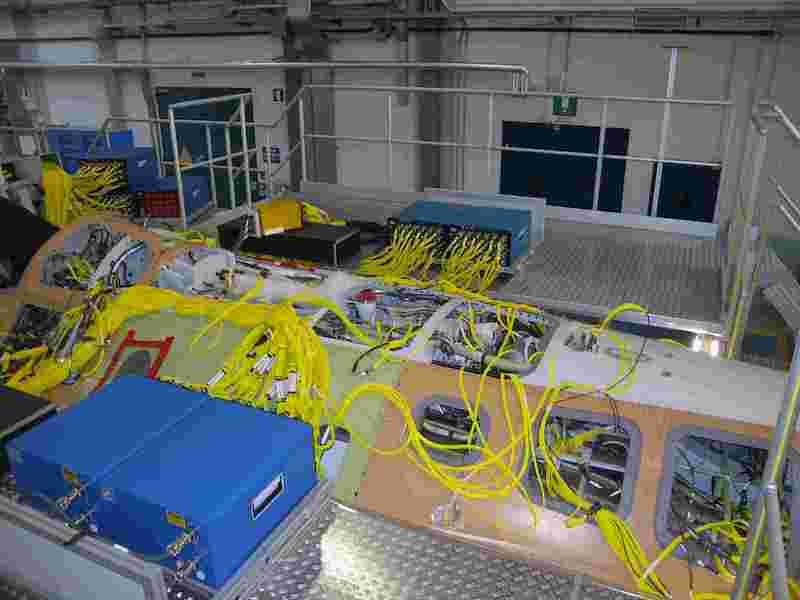
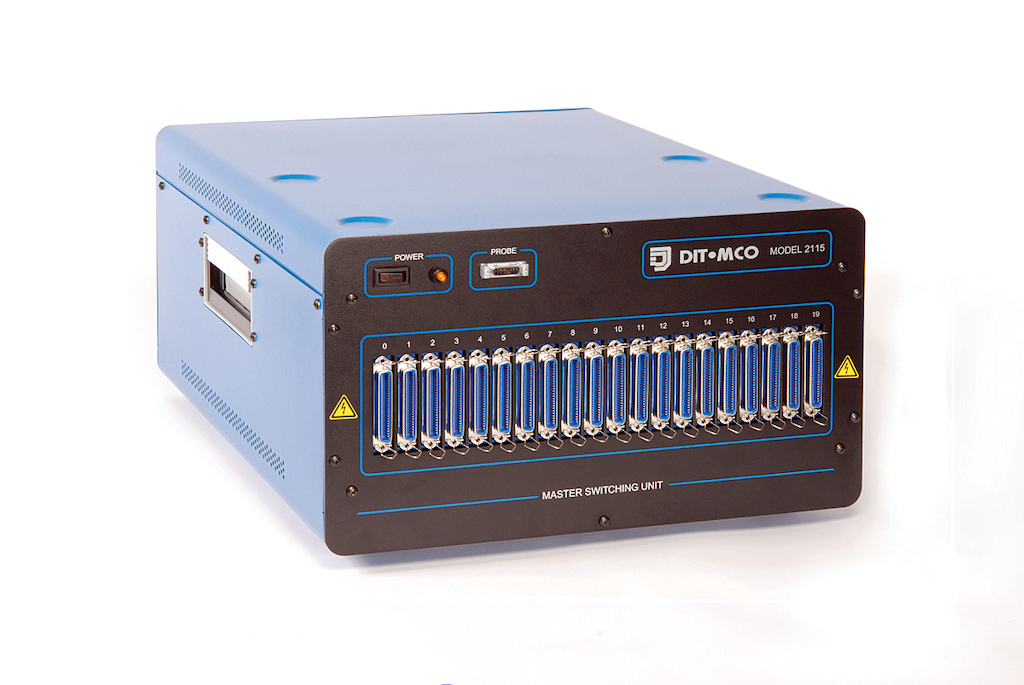
Figure 4. Model 2650s testing Leonardo M-346 Trainer)
They have also developed handheld units, field deployable units, benchtop units (fig. 5). Additionally, a high concentration on software development and interface cables has allowed the company to excel at customer specific customization.
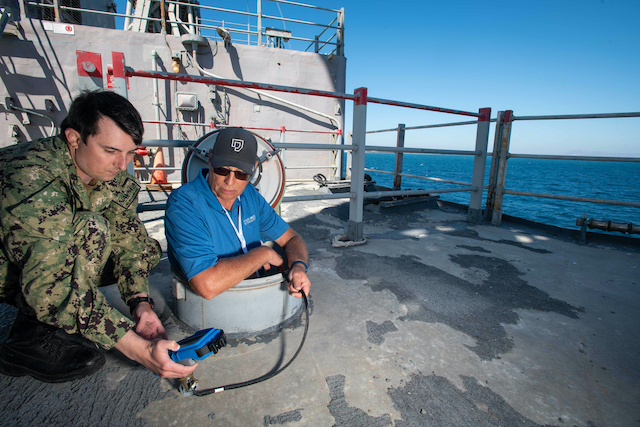
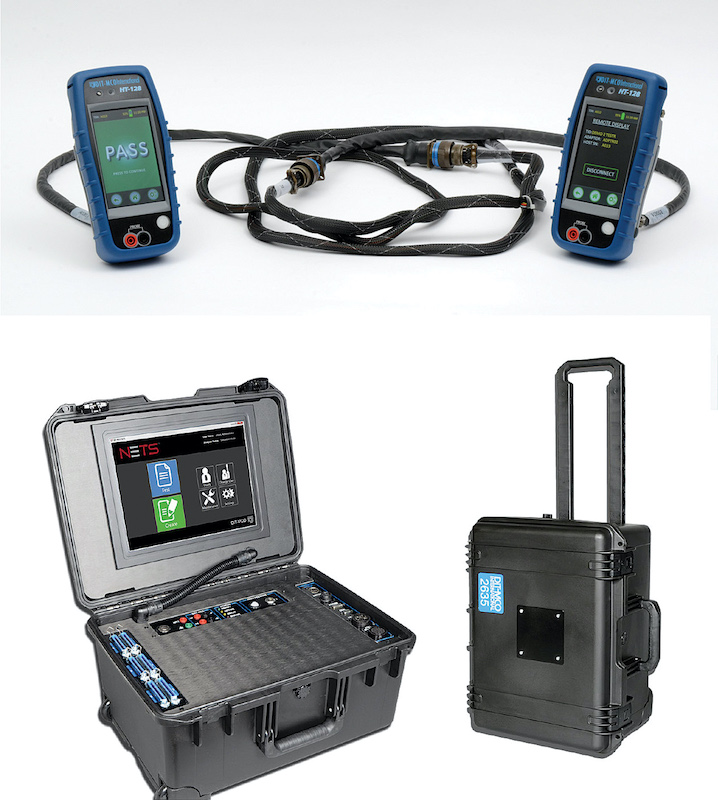
Figure 5. West Sales Manager, Marshall Pelot, demoing the HT-128 at REPTX
Into the Next 75 years
Next generation DIT-MCO hardware will continue to offer the many advantages customers have come to expect including distributed switching, Multi-Bus Architecture (MBA), Random Hookup capability, along with higher test voltages and single point control to support high-speed hipot testing.
The charge into next-gen hardware starts with their latest technology – PinMate (fig. 6). It is a guided wire insertion tool designed to aid assemblers inserting wires into electrical connectors. A miniature projector visually guides the operator by illuminating the correct cavity for pin insertion. Originally designed by Boeing Defense Group in Mesa, AZ, for their in-house wiring shop, PinMate is being commercially developed and offered to the global wiring industry under license agreement between Boeing and DIT-MCO International.
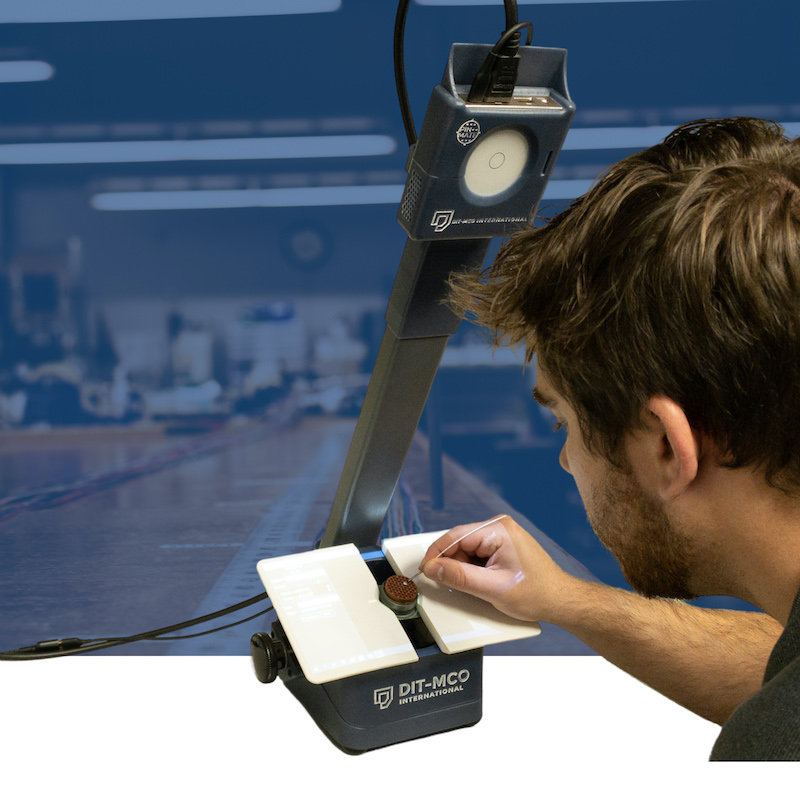
Figure 6. PinMate guided wire insertion tool.
More important in taking DIT-MCO to the next level and insuring they remain the industry leader will be the commitment to a new software infrastructure. They are going beyond just pass and fail results. Beyond checking a quality box and moving onto the next test. DIT-MCO is going to provide errors in their nature language, that anyone can read, experienced assembler or not. AI analysis will pinpoint wiring errors and generate predictive determination and preventative actions to not make the same mistake again. DIT-MCO’s software will go beyond telling you what went wrong and instead determine why it went wrong.
The new software infrastructure and top of the line test equipment and hardware will make DIT-MCO the go to total test solution partner. From the first connector being pinned, to the final point being tested, DIT-MCO offers products that provide solutions.
New Look, New Colors, New DIT-MCO
In 2022, DIT-MCO launched a new logo. This change meant more than just a brand refresher. It signaled that DIT-MCO was changing for the better. The entire brand was becoming modernized, moving to new and exciting heights in the form of technology and innovation. DIT-MCO introduced a secondary color into its brand for the first time. Remaining with the “DIT-MCO” blue, but adding green – also symbolizing something, a greener future. The new logo became a perfect visualization into the future – DIT-MCO is built on the past but focused on the future.
Going Green
DIT-MCO continues efforts to become a more sustainable and energy-efficient company. They recently installed a 200-kW solar array at their facility in Kansas City. The 200kW capacity will allow them to generate more than 51% of their power needs on an annual basis. Over 72% of the cost of the installation will be recaptured in YR 1 in the form of utility rebates, investment tax credits, and accelerated depreciation. They will realize a net savings of over $1.2m over the 30-year life of the system while offsetting nearly 6,800 metric tons of CO2.
Figure __. Solar array at facility in Kansas City.
NexGen People
DIT-MCO would not be around if it wasn’t for the employees who are advancing this company into the future. At DIT-MCO the mix of employees ranges from 50-year DIT-MCO veterans – to new hires working their way up the ladder. With recent and impending retirements of key members of DIT-MCO, they are in an exciting time, shifting into the future of talent within the company.
David Shier joined DIT-MCO in a newly created position of Chief Technology Officer in 2020. More recently, Shier was promoted to President. “I have spent more than 30 years in this industry directly competing with DIT-MCO, so I have known and respected the excellent reputation the company has maintained with its customers,” said Shier. “I’m excited for the opportunity to lead this great company as we develop new products and services that will assure DIT-MCO remains the dominant leader in the wire/harness testing industry.”
Congratulations to DIT-MCO on reaching the impressive milestone of 75 years. May this anniversary be a testament to their enduring success and a springboard to even greater achievements in the future.
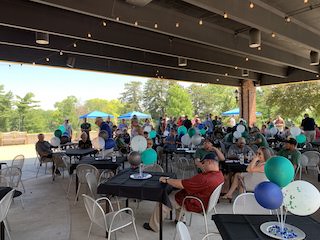
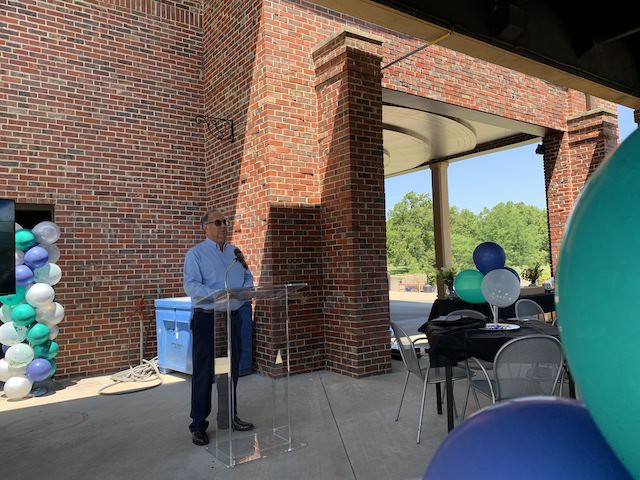