Crimping is a fundamental aspect of wiring harness production, but achieving the perfect crimp involves more than just pressing a wire into a terminal. Recently, I had the chance to sit down with Mark Ondo, Senior Manager of Engineering, Application Tooling at TE Connectivity, to discuss best practices for crimping. Mark brought a wealth of knowledge and practical advice to our conversation—insights that will resonate with anyone involved in wiring harness manufacturing.
When I asked Mark about the key elements of crimp quality, he laid out five critical factors to consider. “Whenever I think about crimp quality, you have to start with the inputs,” he said. “What are all the things that have to come together to make that crimp?” From wires to terminals, tooling, and equipment, every component must be correct and in optimal condition. Mark was quick to emphasize the importance of inspecting these inputs: “If you have a banged-up reel of terminals, you’re going to get bad results. It’s the old garbage-in, garbage-out analogy.”
For those in the industry, TE’s Ocean Applicator and their newly released T5+ Terminator are well-known tools. Mark highlighted their reliability but also stressed the importance of maintenance: “Even with the best tooling, like our Ocean Applicator, if your tooling is in bad condition, you’re not going to get the best results.” This is why regular inspection of crimpers, anvils, and other touch tooling is crucial.
After establishing the importance of inputs, Mark moved on to requirements. Manufacturers like TE provide detailed application specifications for their terminals that cover parameters like crimp height, bell mouth, wire brush, and cutoff tab length. “Understanding these requirements and their tolerances is critical,” Mark explained. “You want to aim for the center of those tolerances to account for natural process variations.” He described a process capability test, a service TE offers, to ensure tooling produces consistent, within-spec crimps.
“Centering the process is key,” Mark said. “For example, if your crimp height is 1mm with a tolerance of ±0.2mm, you want to get as close to 1mm as possible.” He elaborated on how TE calculates process capability indices by running 30-piece samples and analyzing the data. This ensures the tooling can consistently produce high-quality crimps.
Mark then turned to the execution phase of crimping. Whether it’s a manual or automatic process, consistency is the goal. “If it’s manual, you need to carefully position the wire each time,” he said. “With automatic machines, like leadmakers, adjusting speed can help achieve consistent results. Running at full speed might introduce variability in wire positioning, so sometimes slowing down is better.”
Another cornerstone of crimping is process monitoring. Mark introduced TE’s newly launched CQM Lite, a simplified version of their flagship CQMII. This tool analyzes crimp force to determine quality in real-time. “It’s an invaluable resource for catching issues early,” he said. “Visual inspections also play a role, especially in manual processes. Anomalies often present themselves in obvious ways.” Other manufacturers provide similar crimp quality monitoring equipment.
I asked Mark about troubleshooting crimping issues, and his advice was straightforward: “Start back at the beginning. If something’s not working, check your terminals, wires, and tooling conditions. Many issues stem from bent terminals or snagged reels.” He also emphasized the importance of maintaining the correct setup. “Begin with a crimp height that’s too high and adjust downward. This avoids damaging tooling and ensures accuracy.”
Maintenance, as Mark pointed out, is often overlooked. “Lubricating the ram on the applicator and checking tooling conditions regularly is essential,” he informed. While some users ask how many crimps a tool can perform, Mark cautioned that it varies by application. “You need to visually inspect for wear and replace tooling as needed,” he advised.
Toward the end of our conversation, I asked Mark about diagnostic tools for crimp quality. “Crimp height is the primary indicator,” he said. “If your crimp height is correct, other metrics like pull force should follow suit. However, pull testing and cross-section analysis are also valuable for identifying issues.”
We delved into wire variability and its impact on crimping. “Wires from different manufacturers can have subtle differences in diameter and insulation properties,” Mark explained. “Even wires from the same manufacturer can vary based on insulation color. These differences can affect pull force and crimp force, so spot checks are important when changing reels or wire batches.”
Mark’s insights extended to the practicalities of process adjustments. “Whenever you change terminals or wire batches, retrain your crimp quality monitor,” he recommended. “Even small changes can affect the process, and retraining ensures consistent results.”
Incorporating the latest tools and technologies into your process can make a significant difference. TE’s CQM Lite, for example, simplifies crimp quality monitoring with a user-friendly interface and reliable analysis methods. For high-volume applications, their Ocean Applicator and T5+ Terminator offer precision and durability, reducing variability and maximizing efficiency. Mark also noted that these tools are designed with user feedback in mind, emphasizing simplicity and reliability for operators of all skill levels.
Figures 1 and 2 illustrate TE’s Ocean Applicator and T5+ Terminator, respectively. The Ocean Applicator is known for its industry-leading performance, while the T5+ Terminator is a benchtop solution designed for simplicity and reliability. These tools embody TE’s commitment to delivering solutions that enhance crimping processes. Operators have reported significant improvements in setup times and consistency after adopting these tools, showcasing their value on the production floor.
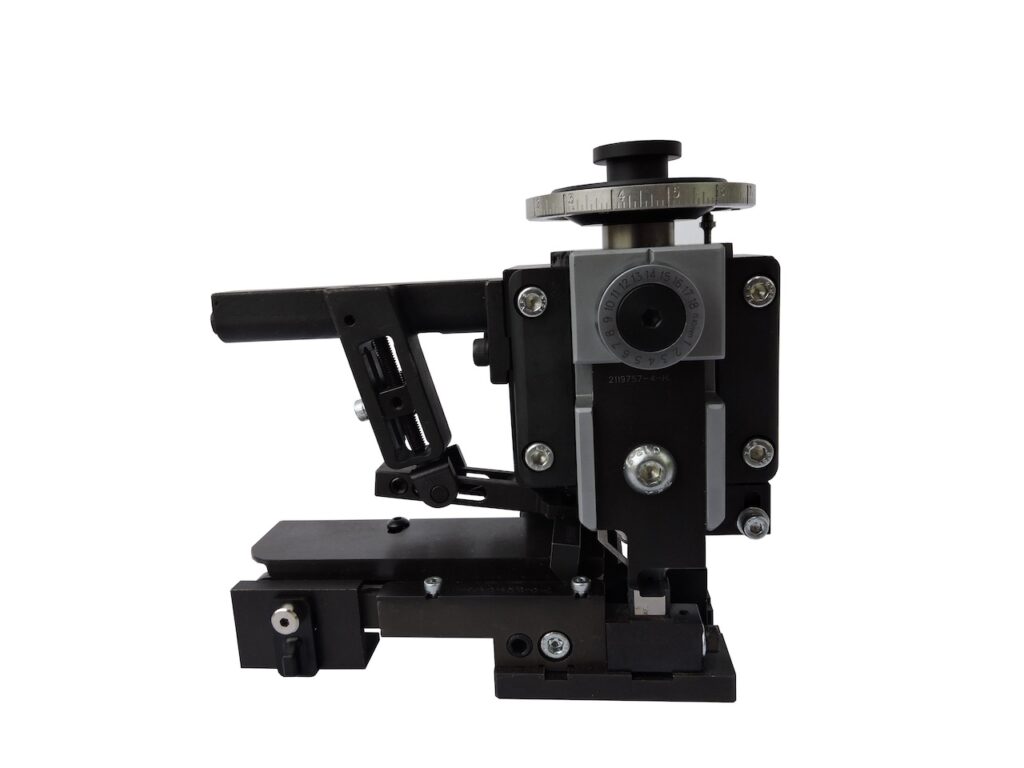
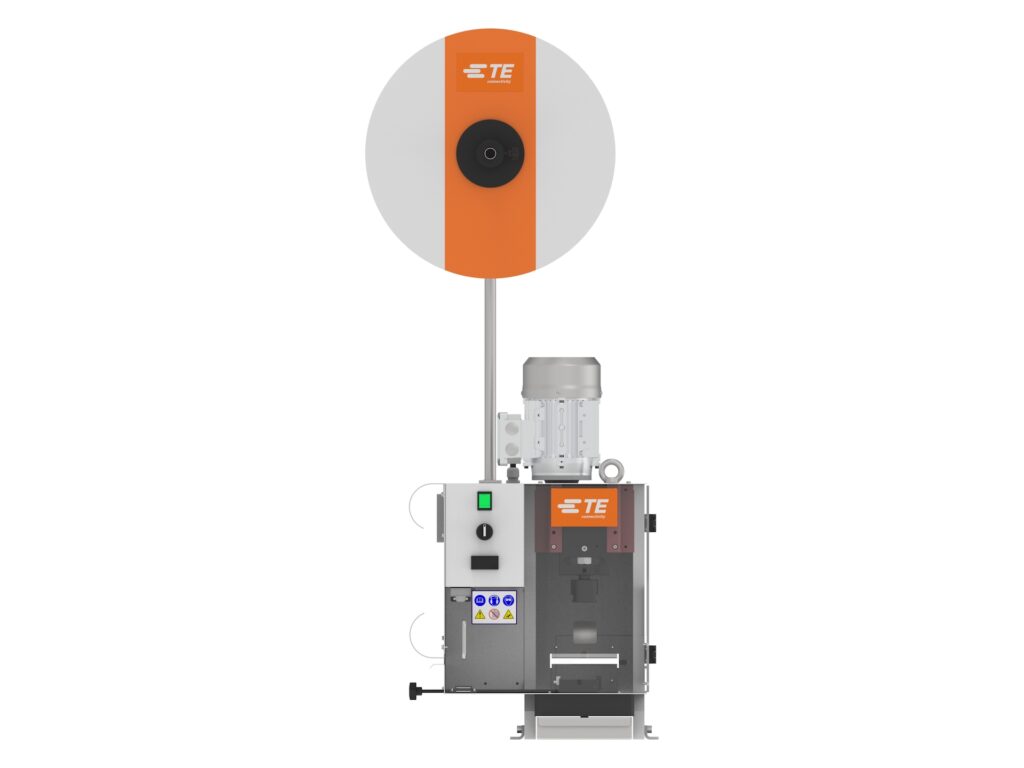
Additionally, Mark shared insights into how TE supports its customers through training and process validation. “We often provide on-site training to ensure operators fully understand how to use our equipment,” he said. “This includes running process capability tests and offering ongoing support to troubleshoot any challenges that arise.” He emphasized that investing in operator training, be it through TE, or some other entity, can significantly improve outcomes, especially in high-stakes production environments.
As we wrapped up, Mark shared a final piece of advice: “Crimping isn’t just about having the right tools—it’s about understanding your process, monitoring it, and making adjustments when needed. That’s how you ensure consistent, high-quality results.” He also highlighted the importance of fostering a culture of continuous improvement. “Even when things are running smoothly, there’s always room to optimize and adapt as new technologies and methods emerge.”
For wiring harness professionals, these insights from TE Connectivity offer a roadmap to mastering crimping. With a focus on inputs, requirements, execution, monitoring, and maintenance—and with the right tools and training—achieving the perfect crimp is well within reach.