Altering Design Parameters to Strip Fluoropolymer Cable Jackets
By Dick Chen, Aerospace Wire & Cable
As all we know, it can be quite difficult to strip fluoropolymer cable. It has excellent insulative properties for many applications, but its slippery nature makes it a challenge to process.
Generally speaking, you need to purchase an expensive, specially designed and very expensive piece of equipment to do the job without damaging the insulation (Fig 1). It’s an even bigger challenge in long-run and second-end terminations in an aircraft or in the field, such as a fire alarm system. It is time consuming and mistakes will be costly.
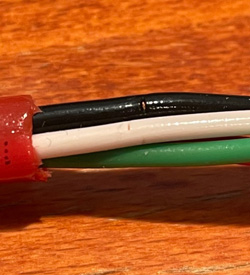
Most people don’t realize that producers of wire and cable can control some of the parameters in the manufacturing process to meet the needs of specific customer applications, thus reducing the effects of these stripping challenges. Sadly, not all manufacturers are willing to work with customers to produce these custom solutions.
As a fluoropolymer cable manufacturer, Aerospace Wire & Cable has long carved out a niche in the industry with their willingness to produce custom extrusion solutions to meet specific industry and customer needs. If, for example, the customer can specify the maximum force required to pull the jacket off at a certain length (four inches long with maximum one lb. of force), they can do their best to produce a more suitable product.
Here are some of the engineering procedures they can tweak to improve the stripping characteristics of fluoropolymer cable jackets.
- Design the extrusion die and tip to get Draw Ratio Balance and Draw Down Ratio*. Typical draw ratios for Fluoropolymer are 50-150 with special techniques is >150. Draw Ratio Balance** shall always keep as 1.
- Set up proper extrusion parameters for process temperature, extrusion speed, cooling distance etc. depending on different Fluoropolymer.
- Select suitable Fluoropolymer for easy strip. For example, Harlar is easier to strip than FEP.
- Add high temperature ripcords or tapes to facilitate an easier strip. (Fig 2, 3)
- Design the cable configurations to facilitate an easy strip. They do this by offering a different lay for the wire pairs, or by using a different type of cable to enhance roundness.
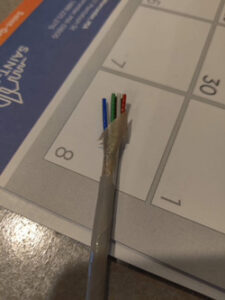
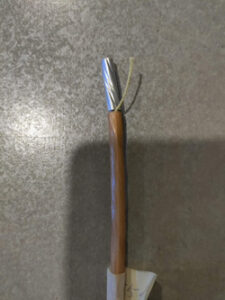
There are many considerations to design a cable for different purposes. Some end users want the jacket to be loose, others want it to be tight. If a fluoropolymer has been selected for the jacket material, ease of the stripping process will be one of the main parameters for a qualified engineer to consider.
* Draw Down Ratio in a tubular die is defined as the ratio of the cross-sectional area of the annular die opening to the cross-sectional area of the finished insulation. In the case of wire, it’s the ratio of the cross-sectional area of the extruded plastic melt to the cross sectional area of the plastic in its final product form, be it a tube, hose or insulation on a core, such as a wire or cable. It is the
extent to which the plastic has been reduced in size to make the part. A larger DDR enables faster production rates, while a lower DDR facilitates more precise control of the product dimensions. A low draw down ratio process is more stable than a high one.
**Draw Ratio Balance describes the balance between the rate the outside
of the cone draws down, and the rate the inside of the cone draws down.
Most products made by drawing a plastic melt are smaller in cross sectional
area than the tooling gap.
About AEROSPACE Wire & Cable
AEROSPACE is a privately owned manufacturer of high temperature, custom designed wire & cable. They can design and manufacture cables to precise specifications. the manufacturing and engineering team has over 40 years combined experience in cable design and production. And can tailor your cables to fit your specific application.
AEROSPACE Wire & Cable provides specialty products for aerospace, communications, computers, automotive, steel & paper mills, petrochemical plants, public utilities, nuclear power plants, mining and defense. Their selection of premium materials allows for reduced diameters with superior electrical performance or data transmission at a wide temperature range. Check them out at www.aerospacewire.com, or call them directly at 800-395-0200.