By Jimmy Fortuna-Peak, Robert Technologies
Selecting the correct expeditionary (high-reliability) power cable connector can be a daunting task. There are numerous factors to consider when choosing a connector that will work well in rugged environments, withstand the elements, and provide reliable connectivity. With over three decades of experience producing expeditionary connectors, RTI is here to provide you with the information you need for your next project. Here are 17 considerations when selecting an expeditionary cable connector.
- Compatibility
Compatibility is critical when selecting an expeditionary power cable connector. It is vital to ensure that the connector is compatible with the cables and devices in operation with it. A mismatched connector can cause signal loss, data corruption, power loss, overheating, and even damage to the devices. Therefore, it is important to choose connectors compatible with a range of cables commonly used in the field, such as coaxial and power cables.
- Durability
Durability is another critical factor to consider when selecting an expeditionary cable connector. The connectors must withstand harsh environmental conditions such as extreme temperatures, moisture, dust, and vibration. They must also withstand frequent handling, disconnection, and reconnection without compromising performance.
Therefore, it is important to choose connectors made from high-quality materials, such as stainless steel or aluminum, that can withstand harsh environmental conditions and resist corrosion. Power connectors with ruggedized features, such as over-molded shells and strain relief, can also enhance durability and reduce the risk of damage from physical handling.
- Performance
Performance is another critical factor to consider when selecting an expeditionary cable connector. The connectors must be able to deliver the necessary level of performance for the intended application in terms of data transmission rate, signal quality, power delivery, and other factors. Poor performance can result in data corruption, signal loss, and power disruptions, leading to downtime and reduced efficiency.
Therefore, it is integral to choose connectors designed to meet or exceed industry standards for performance, such as MIL-STDs. Connectors with high signal integrity, low insertion loss, and low crosstalk can ensure reliable data transmission and signal quality. Connectors with high power handling capabilities can ensure stable and efficient power delivery.
- Size and Weight
Size and weight are also important considerations when selecting an expeditionary cable connector. The connector must be compact and lightweight enough to transport and deploy in the field. A connector that is too large or heavy can add unnecessary bulk and weight to the system, making it difficult to transport and deploy. Therefore, you should consider choosing power connectors designed to be lightweight and compact without sacrificing performance or durability.
- Environmental Conditions
Environmental conditions play a significant role in selecting an expeditionary cable connector. The connector must withstand the specific environmental conditions it will be exposed to in the field, such as extreme temperatures, moisture, dust, and vibration.
For example, connectors used in desert environments may need to be able to withstand extreme heat and sandstorms, while connectors used in arctic environments may need to be able to withstand extreme cold and ice. Therefore, it is important to choose connectors designed to meet the specific environmental conditions they will encounter in the field.
- Ease of Use
Ease of use is also something you should consider when selecting an expeditionary cable connector. The connector must be easy to install, connect, and disconnect, even in harsh environmental conditions. Power connectors that are difficult to use or require specialized tools or training can add unnecessary complexity and delay to the system. Therefore, it is wise to choose connectors designed to be easy to use and require minimal training or specialized tools.
- Cost
Cost is also an important consideration. The connector must be cost-effective and fit within the budget of the system. Multiple options present themselves for connectors with similar specifications and performance characteristics but with varying costs. Choosing an expensive connector can put a strain on the budget, while choosing a connector that is too cheap may sacrifice performance, reliability, or durability.
Therefore, it is vital to consider cost alongside other factors when selecting an expeditionary cable connector to ensure you receive the best value for your money without sacrificing quality. Additionally, cost considerations may also include factors such as the availability of spare parts and the cost of repair or replacement in case of damage or failure in the field.
8. Signal Integrity
Signal integrity is critical in many applications, including those involving high-speed data transmission or sensitive analog signals. It refers to the quality of the signal as it travels through the connector and cable and can be affected by factors such as impedance mismatch, signal attenuation, and electromagnetic interference (EMI). To ensure high signal integrity, look for connectors with low insertion loss and crosstalk, high shielding effectiveness, and impedance matching capabilities.
9. Power Connector Type
There are many different types of power connectors available for use in expeditionary applications, such as circular, rectangular, coaxial, and fiber optic connectors. The type of connector you choose will depend on factors such as the type of cable you are using, the frequency and power of the signal, and the environmental conditions of the application. Consider factors such as connector mating cycles, insertion and extraction forces, and contact resistance when selecting the appropriate connector type.
10. Power Connector Materials
The materials used to make a connector can impact its durability, performance, and cost. Common materials used in connector construction include metals such as stainless steel, aluminum, and brass, as well as plastics and composites. Consider factors such as corrosion resistance, thermal conductivity, and weight when selecting the appropriate materials for your application.
11. Contact Plating
The plating on a connector’s contacts can impact its performance and reliability. Common plating materials include gold, silver, nickel, and tin. Applications that require high signal integrity and low contact resistance implement gold plating, while high-frequency applications use silver. Nickel and tin plating are more cost-effective and offer good corrosion resistance.
12. Voltage and Current Ratings
The voltage and current ratings of a connector will determine the maximum voltage and current that it can handle without degrading or failing. Ensure that the connector you choose has sufficient voltage and current ratings for your application to prevent overheating, arcing, and other hazards.
13. EMI Shielding
Electromagnetic interference (EMI) can be a significant issue in many applications, particularly those involving high-speed data transmission or sensitive electronics. Look for connectors with effective EMI shielding, such as conductive coatings or gaskets, to reduce the impact of EMI on your system.
14. IP Rating
Ingress Protection (IP) ratings indicate the level of protection provided by a connector against dust and water ingress. The rating consists of two numbers, with the first indicating the degree of protection against solid objects and the second indicating the degree of protection against liquids. Consider the environmental conditions of your application and choose a connector with an appropriate IP rating to ensure reliable operation.
15. Contact Density
The contact density of a connector refers to the number of contacts accommodated within a given connector size. Higher contact density can allow for greater functionality in a smaller space but can also make the connector harder to work with. Consider the tradeoffs between contact density and ease of use when selecting a connector.
16. Mating Mechanism
The mating mechanism of a connector refers to how it is connected and disconnected. Common mating mechanisms include threaded, bayonet, and push-pull mechanisms. Consider factors such as ease of use, mating force, and security when selecting a mating mechanism for your connector.
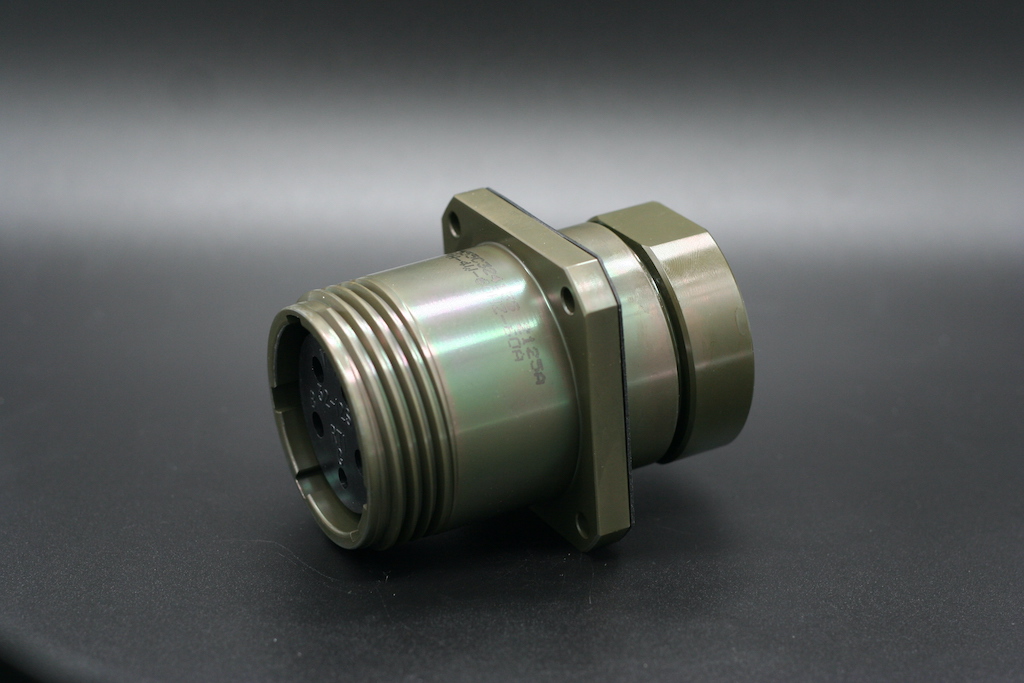
17. Certifications and Standards
Certifications and standards need to be kept in mind when choosing an expeditionary cable connector because they ensure the connector meets performance and safety requirements. Agencies, military organizations, or other regulatory bodies require these regulations and certifications before considering them.
For example, MIL-STD (Military Standard) certifications are common recognitions in the military and defense industry, and military operations require them on many occasions. These standards ensure the tests run on the connectors meet specific performance and safety requirements, such as resistance to vibration, shock, and extreme temperatures. If you want to learn more about RTI’s MIL-grade connectors, you can read about them here.
Similarly, industry standards such as the National Electrical Manufacturers Association (NEMA) and International Electrotechnical Commission (IEC) provide guidelines and requirements for connectors used in various applications, including hazardous environments or medical equipment. Compliance with these standards ensures that the connector is suitable for its intended use and can perform reliably in the specified conditions.
Conclusion
There are many reasons and aspects you should consider when selecting your next cable connector, and this guide provides you with a checklist of information you should know. RTI offers thousands of expeditionary power connector models that allow you to find the perfect match for you. When you invest in us, you invest in a positive future for your project.